Portability and support drives quality in forklift manufacturing
Portable measuring arm technology improves processes and capabilities for leading global forklift manufacturer.
Contact us

The Hyster-Yale site in Craigavon in Northern Ireland is responsible for a wide range of direct component production and assembly activities, including the need to assess multiple families of parts, with a percentage received from external suppliers.
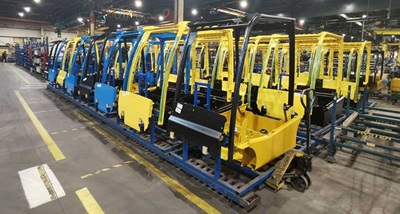
The quality department acquired its first advanced metrology tool in 1994 when it invested in a DEA CMM unit, which was subsequently upgraded to one of Hexagon’s GLOBAL CMMs in 2005. Since then the department’s needs have developed, with the capacity to move around the large Craigavon site to better support their variety of internal customers demanding a more portable inspection solution. This was particularly necessary as the quality team began to add fixture inspection to their portfolio of duties – fixtures are in a set position and cannot be moved to the quality areas.
John and his team’s first foray into portable measuring arm technology involved purchasing a system from one of Hexagon’s competitors, but this solution didn’t live up to expectations, with the very high cost of ownership cited as a particular reason to move on to a better solution.
Processes that used to take 8 hours to complete with manual methods are now completed in as little as 40 minutes.The department’s previous experience with the GLOBAL machine from Hexagon meant there was already an established familiarity with Hexagon’s PC-DMIS software solution within the team at Craigavon. After a visit to the Hexagon Precision Centre in Milton Keynes for a hands-on demonstration and the opportunity to put Hexagon’s latest solutions through their paces, John’s team were convinced by the performance of the Absolute Arm 7-Axis and RS5 Laser Scanner.
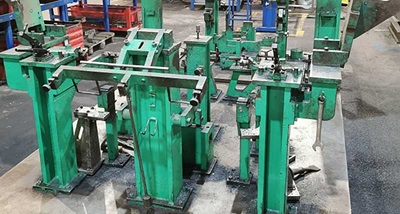
The introduction of laser scanning with the Absolute Arm has also been beneficial from a cost saving perspective. Processes that used to take 8 hours to complete with manual methods are now completed in as little as 40 minutes, including programming.
John estimates that the new portable measuring arm system is split about 70/30 between time in the quality room checking manufactured and acquired components and moving around the facility – on the assembly lines for fixtures, in the weld shops, at the cylinder plant or in the product development area. The latter is where reverse engineering work at Hyster-Yale is carried out, specifically for the development of tubes and hoses and brackets.
One area in particular that scanning with the Absolute Arm has allowed for an increase in activity and an improvement of outcomes has been with the measurement of the fixtures that are manufactured onsite. The arm has really enhanced the team’s capabilities in this regard, and the data collected is often now used for preventative maintenance purposes.
John and his team are also currently involved in piloting new products. With the Absolute Arm they’re able to measure directly within pilot areas, checking for clearance and fits – this is much more efficient than previously.
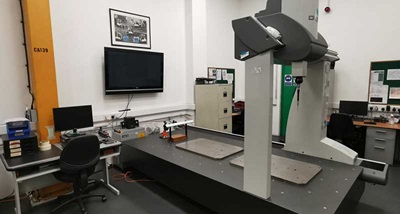
According to John the ability to develop the team’s skills by continuing to work with PC-DMIS was a big driver for their decision to invest in Absolute Arm technology, as was the quality of the scanner – the team found they were able to very quickly collect clean and usable data with the RS5 Laser Scanner.
Also important was Hexagon’s support network. John said that local Hexagon representative Paul O’Neill was an invaluable resource as they made the decision, as well as immediately afterwards during the training transition and since then until the present. His expert knowledge of the hardware and of PC-DMIS programming was available whenever needed and the team appreciated his patience during their learning period.