A globalised measuring solution
Ford - Germany
Contact us
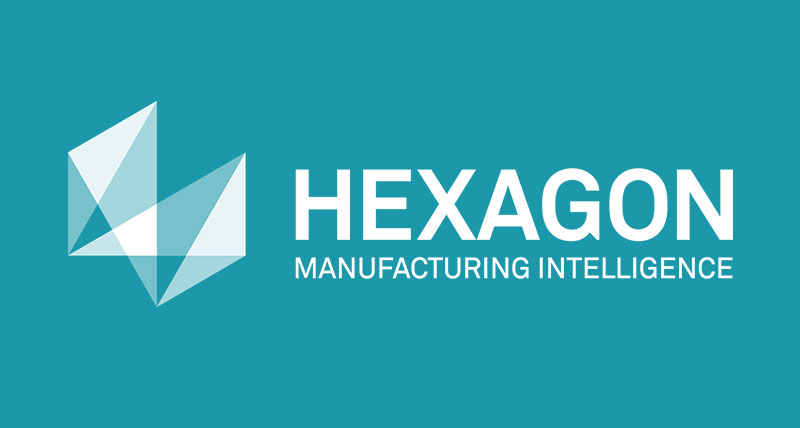
Retrofitting is gaining more and more importance in coordinate metrology. Without a doubt – retrofitting prolongs the service lives of existing systems and is more cost effective than acquiring new equipment. In order to be able to fulfil this aim competently and effectively, Hexagon Metrology has established a retrofit team in each of its sales companies.
The team concentrates its activities on the upgrading of electronic components and software – and not just of products made by Hexagon Metrology. Installation of the PC-DMIS metrology software system results in immediate improvements, for example the integration of CAD data and offline programming for more productivity.
Impressive presentation
Ford also profits from the advantages offered by PC-DMIS. The Cologne carmakers were tipped off about this package in 2009 by their colleagues in the USA, who had been running Hexagon Metrology software for some years. The use of the same technology, processes and tooling is seen as a big plus at all Ford plants worldwide. The acquisition of PC-DMIS therefore offers even more. Especially as the existing metrology software was no longer satisfactory and the search for alternatives had already begun. This new metrology software would allow them to write high-quality programs without having to invest a great deal of time.The Hexagon Metrology software was installed first in the toolmaking shop and the pilot plant. At the same time, an analysis of the manufacturing process was performed in the pilot plant to identify where problems could occur and the measuring programs were written for the assembly groups. This lead was followed by body and toolmaking shops in other plants in Europe – each time just before the start of production of a new model.
Writing the measuring programs
The process for writing the measuring programs is as follows: the test plan is drawn up and agreed in „measuring point meetings“ at which the points to be measured are determined. The plan is passed to the offline programmers in the pilot plant. They import the data into PC-DMIS and implement them in an executable measuring program. The offline measuring program is then sent to the online machine, then trialed and edited.The integration of the interfaces is an important step here, otherwise the processes will not run smoothly. In a model series with three bodyshell types – 4-door, 5-door and estate – there can be 70 to 80 programs, which are not only programmed online, but also require reporting routines.
When the first assemblies arrive, the programs are tested and fine-tuned in try-out. Numerous updates take place over the course of amendments and reapprovals as well as the integration of additional measured points. The last step at this stage is then to hand over the programs and the reports to the manufacturing works. However, the project is still not complete: Ford staff test the programs on site to see that they all run properly.
Significant advantages
One glance at the requirements profile alone proves the value of PC-DMIS. The use of the software delivers a significant advantage online as well as offline – no interface problems between the two shops, no more programs to convert. In addition, the users have the same user-interface and can work on the same files and send them between one another. PC-DMIS also makes sending files by e-mail from the pilot plant to the other plants much easier. The files are considerably smaller. The previous system did not allow sending files by e-mail.Time savings arise from considerably faster programming. An important point, when you consider programs are becoming more complex, through the presence of holes for example. These holes are often provided in bodyshell parts to allow functional components to be attached at a later stage – for example airbags. With new technology coming along all the time, there are more and more holes to measure. „Shorter times between new models demand that programs are written quicker. If only one software package is in use, all staff become familiar with it and it makes deputising for a colleague much less of a problem,“ says Frank Herr, Business Field Manager Software at Hexagon Metrology Germany. The applications in the pilot plant are now covered with the same software package, whereas previously parts production and assembly used different software. A further important advantage is the solid stability of PC-DMIS – system crashes are a thing of the past. In addition, the systen can handle larger amounts of data and move the parts quicker than before.