Proving a technology leader’s seal of machine quality
Hexagon’s ETALON LASERTRACER NG confirms precision and proof of manufactured quality over the entire working area of a machine tool

F. Zimmermann GmbH chose Hexagon’s ETALON LASERTRACER NG for acceptance testing and quality verification to confirm the outstanding accuracy of their newly manufactured milling machines and machining centres. The system provides its customers with documented proof of precision over the entire working area of a machine, delivers large time savings during the verification measurement and can be used for regular condition monitoring, leading to greater maintenance efficiency.
From Neuhausen auf den Fildern in Germany, Zimmermann is a technology leader known for its high-performance portal milling machines and horizontal machining centres. The company specialises in serving customers from the aerospace and automotive industries and is acutely focused on ensuring its machines deliver the exceptional quality, accuracy and surface finish of the end product its customers expect.
The purchase process of a machine tool usually ends with proof of manufactured quality on-site at a customer’s manufacturing facility during the acceptance process. The purchase is completed only after the customer is convinced that the required quality is achieved. In most cases, this is done by manufacturing a special test part. If the subsequent measurement of this part demonstrates that all necessary tolerances have been met, the machine acceptance is considered successful.
However, this test process does not cover the entire machining area of the machine, which means deviations at other points would not be discovered.
Since Zimmermann promises excellent results over the entire machining area, they decided to go further than strictly necessary in their machine acceptance testing, choosing Hexagon’s ETALON LASERTRACER NG-system to prove quality over the total machining volume.
Testing the individual axes is costly and takes time, meaning environmental conditions can influence machine verification. “Sometimes we measure the machines at night to have the most constant possible temperature conditions in the hall for the duration of the measurement,” explains Steffen Nüssle, Sales Director Export, Zimmermann.
Adding another complication to the task, rotary axes cannot be measured and inspected with conventional alignment systems, which means a separate measuring device must be used for this measurement, adding extra time and cost to the process.
In contrast to conventional systems, the LASERTRACER NG uses a patented measuring technology that captures mechanical inaccuracies of the linear, rotary and swivel axes together, thus ensuring unsurpassed accuracy in much less time.
From Neuhausen auf den Fildern in Germany, Zimmermann is a technology leader known for its high-performance portal milling machines and horizontal machining centres. The company specialises in serving customers from the aerospace and automotive industries and is acutely focused on ensuring its machines deliver the exceptional quality, accuracy and surface finish of the end product its customers expect.
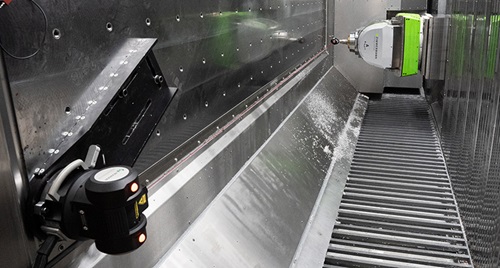
However, this test process does not cover the entire machining area of the machine, which means deviations at other points would not be discovered.
Since Zimmermann promises excellent results over the entire machining area, they decided to go further than strictly necessary in their machine acceptance testing, choosing Hexagon’s ETALON LASERTRACER NG-system to prove quality over the total machining volume.

Adding another complication to the task, rotary axes cannot be measured and inspected with conventional alignment systems, which means a separate measuring device must be used for this measurement, adding extra time and cost to the process.
In contrast to conventional systems, the LASERTRACER NG uses a patented measuring technology that captures mechanical inaccuracies of the linear, rotary and swivel axes together, thus ensuring unsurpassed accuracy in much less time.
“Hexagon’s system detects early deviations before consequences arise, allowing more efficient maintenance planning.”
Steffen Nüssle
Sales Director Export
F. Zimmermann GmbH
Simple set up and fast, accurate measurement
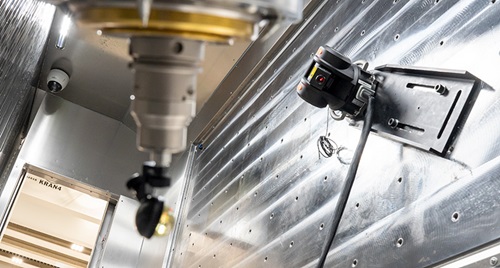
The device tracks the travel path of the machine throughout its entire working volume via the tool centre point, delivering highly accurate measured values, from which Hexagon software packages calculate and analyse machine deviations to within fractions of a micrometre.
Measurements are taken in the fully assembled machine and not only recorded separately for individual axes. This way, consequential errors – for example, from set-up mistakes – can be excluded. Between the measuring steps, the device is manually repositioned.
With this system, the complete measurement of a machine requires only a fraction of the time needed when using comparable systems. “Hexagon’s solution has led to great time savings and is the system’s biggest advantage for us,” says Nüssle. “Once the LASERTRACER NG is set up, a few button presses, and hand movements are enough to complete the measurement. It’s that easy.”
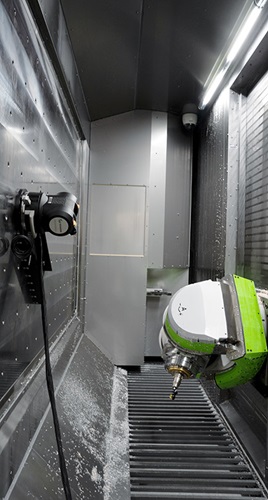
Proof over a machine’s lifetime
After commissioning a machine, it is necessary to periodically make sure it continues to meet the required tolerances.The validity of certified measurements using metrology software like PC-DMIS on the machine tool, which several Zimmermann customers use, requires proof that the machine meets the required tolerances – evidence that the LASERTRACER NG-system can provide.
Especially when manufacturing large, cost-intensive components, as used in the aerospace industry, it is essential to ensure that the machine is in perfect condition. Otherwise, errors caused by the machine can lead to costly rework or scrap.
Whatever the requirement – at regular intervals or before the production of cost-intensive parts – LASERTRACER NG makes it easy to check whether machines function as specified or whether maintenance is necessary.
“Large companies, in particular, with cost-intensive components would like to know if, when and where machine deviations are imminent. Predictive maintenance is becoming increasingly important in this regard,” explains Nüssle. “Hexagon’s system detects early deviations before consequences arise, allowing more efficient maintenance planning.” Spontaneous failures can be a thing of the past.
It’s a bonus that thanks to its ease of use, customer personnel can operate the system on-site without needing a service technician’s support. “And because the system requires much less time than similar systems, it’s easy to show the customer again and again how well our machines work, across the entire working area, even after many hours of operation,” says Nüssle.
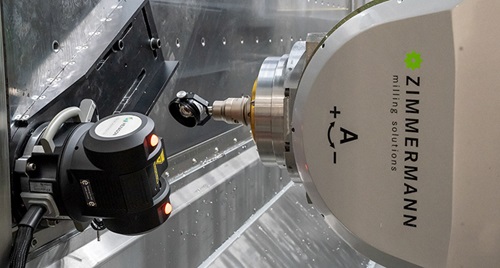
Advantages
- Easy check of the current condition of machine tools
- A system for determining all axis component deviations and axis orientations
- Minimal time compared to conventional measuring equipment (test standards or conventional laser interferometers)
- Secure and automatic generation of correction data to the control (Conventional or volumetric)
- Flexible use on machines of different sizes and types
“Hexagon’s solution has led to great time savings… Once the LASERTRACER NG is set up, a few button presses, and hand movements are enough to complete the measurement. It’s that easy.”
Steffen Nüssle
Sales Director Export
F. Zimmermann GmbH