WLS400M helps deliver high level quality for the new Honda Civic
Honda - UK
Contact us

For Honda of the UK Manufacturing Ltd, customer satisfaction is everything. Precision measurement is employed at every stage of the manufacturing process to ensure that everything from the engine to the fit and finish of the body is as good as it can be.
During the development phase of the award winning new Honda Civic, the Complex Analysis Team for High Accuracy Body (CAT HAB) used the Cognitens system to help the maturation process of crucial parts such as door assemblies and tail gates. These critical areas affect both the aesthetics and the functionality of the vehicle. If a boot doesn’t shut properly or the gap between the door and main body doesn’t look right – customers aren’t happy and neither is Honda. This quest for accuracy is combined with a strict production deadline that must be hit in order to meet business objectives. Therefore the measurement strategy in the development phase must combine high accuracy with speed and efficiency.
The CAT HAB team sits as a quality function in the Weld Division but brings together people from Paint, Assembly Frame and Product Engineering to pool experience and focus on complex issues that cut across departments. By using the Cognitens White Light scanning system from Hexagon Metrology the team were able to focus on specific areas and speed up root cause analysis of any imperfections in the development phase. The objective being to optimise fit and finish before mass production starts – and for customers to receive cars that meet the quality standard they expect from Honda.
The process begins with receiving the drawings from Japan and defining some critical parameters – then the first trial builds of the car are critiqued on a company basis. Focus areas are identified and the Cognitens WLS400M is used to verify child parts of sub-assemblies (stage measurement) as well as critical areas such as tail gates. The CAT HAB team leaders scan parts using Cognitens at different stages of the build process. For example a tail gate can be scanned when it arrives from Weld and before and after Paint, Assembly Frame and other departments. The tail gate scans can then be overlaid on each other to show where any changes have occurred and whether they sit outside agreed parameters.
The Cognitens WLS400 sensor works by projecting a random pattern on the object and triggering simultaneous capture of the area of interest by its cameras. It scans an area half a metre square and measures full surfaces, features and edges that are not possible for other systems. The data is grabbed in milliseconds, enabling working in a shop floor environment with vibrations and different light conditions so nothing can affect the measurement. An easily understandable colour map and features data is produced as a summary.
At HUM in Swindon, once a fixture has been mapped, measurements that used to take 1.5 hours using a combination of manual methods and other portable arms can now be carried out in 15 minutes. Root cause analysis can now often be carried out in one shift when previously it would several days to even identify the issue.
The CAT HAB Manager explains “Using Cognitens takes the ambiguity out of measurement and it speeds up our root cause analysis process. We’re working to tolerances of + or – 0.5mm on finished panels and that is after they have been assembled, pressed and welded. We’re now able to take more data, more accurately and more quickly enabling us to achieve the excellence we strive for in the timeframe allowed.” In terms of stage measurement – the process of scanning individual child parts of an assembly – this equated to being able to make five iterations of measurements when in the past – only one would have been possible.
The culture at HUM is very much one of sharing information face to face with PowerPoint presentations. The “colour mapping” provided by Cognitens’ proprietary CoreView software has enabled clear communication between the CAT HAB team and managers and directors in other parts of the business. It is far easier to demonstrate an area needs adjustment (in blue for under or red for over) or is within tolerance (in green) visually rather than having to explain a series of numbers to those who might not be familiar with them. Cognitens colour maps and reports have become respected documents within HUM and contribute to effective knowledge transfer and decision making. Although the CoreView is an interactive report system, it is a compressed file so reports are small enough to email.
Some of HUM’s major suppliers run the Cognitens system and software – it provides a very good basis for dealing with queries. A part might be provided to HUM within specification but then change during a process at the plant. Solutions can be found quickly by sharing this information on Cognitens reports and working together to make the adjustment.
HUM has found aftersales support from Hexagon Metrology to be excellent. When maintenance has been required it has been carried out under warranty with no quibbles. HUM is developing a close relationship with their Hexagon contact and are interested in pursuing new product development and possible automatic measurement applications using the WLS400A version of the system.
The CAT HAB Manager concludes “The Cognitens system has been used almost every day since we acquired it. It is now fully ingrained in our processes and an integral part of development and production at Honda. There has been a clear return on investment. “If we were without it – we’d worry.”
During the development phase of the award winning new Honda Civic, the Complex Analysis Team for High Accuracy Body (CAT HAB) used the Cognitens system to help the maturation process of crucial parts such as door assemblies and tail gates. These critical areas affect both the aesthetics and the functionality of the vehicle. If a boot doesn’t shut properly or the gap between the door and main body doesn’t look right – customers aren’t happy and neither is Honda. This quest for accuracy is combined with a strict production deadline that must be hit in order to meet business objectives. Therefore the measurement strategy in the development phase must combine high accuracy with speed and efficiency.
The need for speed (and accuracy)
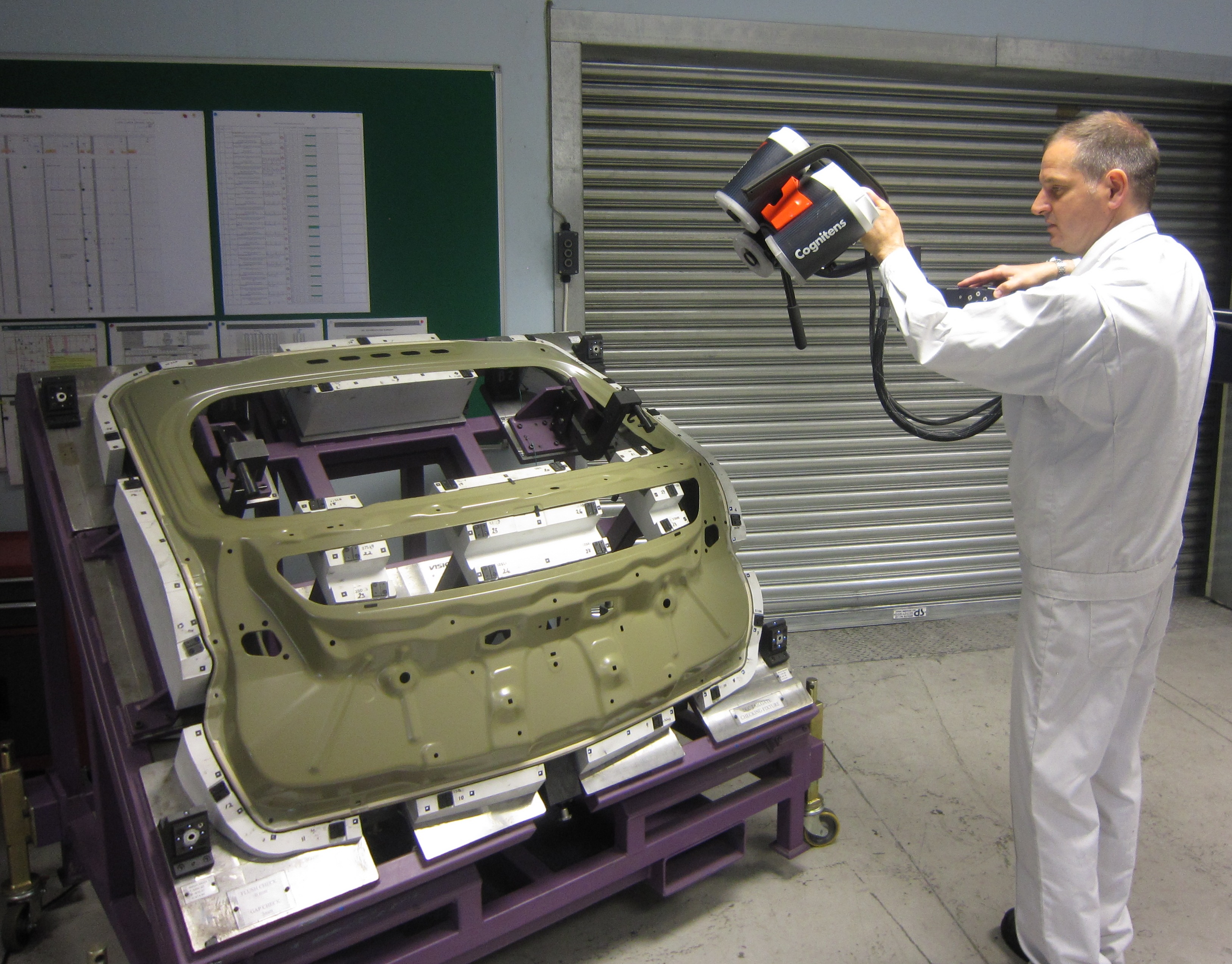
The process begins with receiving the drawings from Japan and defining some critical parameters – then the first trial builds of the car are critiqued on a company basis. Focus areas are identified and the Cognitens WLS400M is used to verify child parts of sub-assemblies (stage measurement) as well as critical areas such as tail gates. The CAT HAB team leaders scan parts using Cognitens at different stages of the build process. For example a tail gate can be scanned when it arrives from Weld and before and after Paint, Assembly Frame and other departments. The tail gate scans can then be overlaid on each other to show where any changes have occurred and whether they sit outside agreed parameters.
The Cognitens WLS400 sensor works by projecting a random pattern on the object and triggering simultaneous capture of the area of interest by its cameras. It scans an area half a metre square and measures full surfaces, features and edges that are not possible for other systems. The data is grabbed in milliseconds, enabling working in a shop floor environment with vibrations and different light conditions so nothing can affect the measurement. An easily understandable colour map and features data is produced as a summary.
At HUM in Swindon, once a fixture has been mapped, measurements that used to take 1.5 hours using a combination of manual methods and other portable arms can now be carried out in 15 minutes. Root cause analysis can now often be carried out in one shift when previously it would several days to even identify the issue.
The CAT HAB Manager explains “Using Cognitens takes the ambiguity out of measurement and it speeds up our root cause analysis process. We’re working to tolerances of + or – 0.5mm on finished panels and that is after they have been assembled, pressed and welded. We’re now able to take more data, more accurately and more quickly enabling us to achieve the excellence we strive for in the timeframe allowed.” In terms of stage measurement – the process of scanning individual child parts of an assembly – this equated to being able to make five iterations of measurements when in the past – only one would have been possible.
Talking the same language
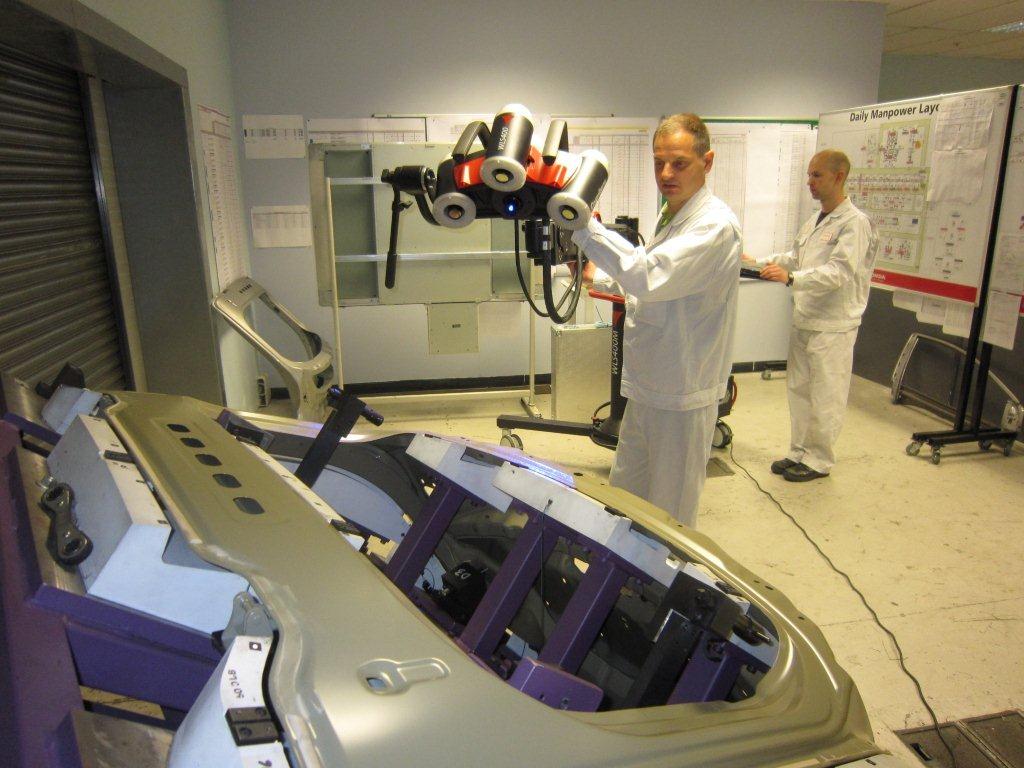
Some of HUM’s major suppliers run the Cognitens system and software – it provides a very good basis for dealing with queries. A part might be provided to HUM within specification but then change during a process at the plant. Solutions can be found quickly by sharing this information on Cognitens reports and working together to make the adjustment.
Embedded in the process
There are four main users of the Cognitens system in the CAT HAB team at Swindon. All of these engineers received five days of training from Hexagon Metrology. The training was carried out onsite and contained real life worked examples from the new Civic development process. Within a working week the operators were up and running and solving problems that helped the business. The ambition is to have a further six people trained on the system soon. The Cognitens has also been deployed in production when small design adjustments to parts have been required and on new product development using the WLS400’s reverse engineering features for die design and duplication.HUM has found aftersales support from Hexagon Metrology to be excellent. When maintenance has been required it has been carried out under warranty with no quibbles. HUM is developing a close relationship with their Hexagon contact and are interested in pursuing new product development and possible automatic measurement applications using the WLS400A version of the system.
The CAT HAB Manager concludes “The Cognitens system has been used almost every day since we acquired it. It is now fully ingrained in our processes and an integral part of development and production at Honda. There has been a clear return on investment. “If we were without it – we’d worry.”