Two radio communication options safeguard processes and reliability
Contact us

Whenever Mindelheim is mentioned, the industrial sector generally understands this to mean a large machine manufacturer. But Mindelheim has also been known for high-quality plastics processing and it is the home of the first fully industrially produced plastic gilders.
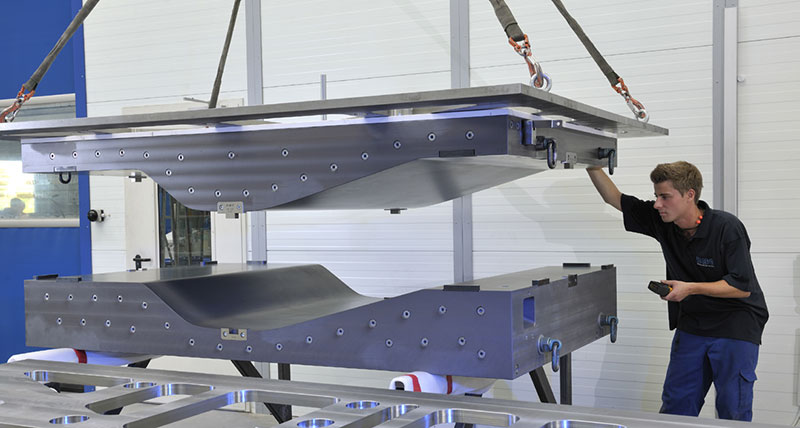
Founded in 1960, the company was bought by its current owner in 1999 and has been called BBG GmbH & Co. KG since 2001. In this time, its customers have included well-known manufacturers in Europe, Asia and America, buying tools, machines and entire installations with the specialist expertise of the Mindelheim-based company. More and more orders from satisfied customers ensure the company’s continuous growth. The tool manufacture and design departments alone currently have around 25 employees. The team eventually moved into new buildings, not least to provide more space for production and create better working conditions.
However, there were often unforeseen issues in the process sequence when measuring on large machining centres: an unwelcome surprise resulting in false measurements and unplanned machine stoppages. The cause of this turned out to be the crane system’s radio remote control, which continually and uncontrollably switched between frequencies with its co-called frequency hopping feature, sending stronger interfering signals via the radio channel reserved for the radio measuring sensor. If the radio measuring sensor is active at the time, the interfering signal can affect machine control and malfunction.
An error in the final stages can have bitter costly consequences.
Years of positive experience with m&h touch probes meant that BBG didn’t want to go without this tried and tested tool. “We have been using them for a long time and have never had any problems with them,” explains Michael Späth, Head of Milling and Production Planning at BBG. The company did not receive the troubleshooting support it expected from the crane manufacturer, so it switched to m&h. “They took our issue seriously immediately and worked with us to find a solution,” adds Michael Späth.
m&h is a pioneer in terms of touch probes with radio data transmission and brought the first touch probe of its kind to market a number of years ago.
These devices are now used worldwide, principally on five-axis machines or large machining centres. m&h radio touch probes on the 433 MHz band still set the benchmark on the market. Their wide range and fast, secure signal transmission ensure a high degree of process reliability. Over the years, the probes’ radio technology has been further and further developed and modern technologies and new electronics have been integrated. Now, for example, m&h radio receivers have permanent channel scanning, which monitors all available radio channels for interfering signals and gives machine operators recommendations of the channels without significant interfering signals. This has the advantage of the user being able to systematically design his/her radio architecture with fixed channels during operation. The permanent channel scanning by the m&h receiver also avoids radio channels which continue to emit significant interfering signals from other systems. Furthermore, this system redundantly transmits entire signal protocols multiple times, which enables clear ordering of the signals. This makes the system one of the fastest and most secure on the market. The new electronics modules in the probes use a lot less energy than previously, which is clear to see in the markedly increased service life of their batteries. In addition, all m&h touch probes take standard batteries.
However, the frequency band around 432 MHz, which m&h has used exclusively up to now, is not reserved for industry all over the world as it is in Germany. In other countries, other transmit in this band or it is entirely reserved for the military, as is the case in Japan, in important market for tool setters. As a result, m&h were required to find an alternative for the long term. It was important for development at m&h to also ensure that the signals were clearly identified in another system and always transmitted to the control unit consistently quickly. This is the requirement for process reliability and consistent accuracy of measuring results.
As many customers also wish to use the reserved industry frequency band in the future, it was clear that this technology will remain standard at m&h. For all cases where local conditions require an alternative solution, the new industry frequency band around 2.4 GHz was selected, which is already widely used for industry applications. Thanks to new technologies, m&h was able to create secure connections in this frequency band. With AFS (Automatic Frequency Select) technology, the frequency ranges of this radio band are continually scanned and partial frequencies are automatically selected, which are free of interfering signals. This not only ensures the system’s own transmission will be fast and trouble-free, but also prevents interference from WLAN or Bluetooth systems or other radio sources. The frequency spread method means that the touch probe sends its signals redundantly and with higher signal density, similar to the proven m&h technology on previous systems. This reliably provides the fastest possible signal transmission with the shortest possible delays and ensures consistent measuring accuracy. This also avoids the otherwise recurrent frequency hopping with unpredictable transmission times, like the time-consuming switching between occupied radio channels.
m&h spontaneously offered BBG the opportunity to be one of the pilot customers for this technology and test a pilot series model of the new 2.4 GHz technology, which it gladly accepted. “The service provided by m&h really took our issue seriously and they were very committed. They really got things moving. Their approach was really solution-oriented,” enthuses Michael Späth. The probe initially installed on a machine provisionally worked perfectly from the outset.
The second machine was then soon converted to the new 2.4 GHz m&h technology. “We haven’t had a single false measurement since the conversion,” enthuses Michael Späth about the restored process reliability. BBG can now get back to setting up, probing and adjusting with the touch probes and measuring standard geometries. The touch probes are an indispensable tool for high accuracy, process reliability and efficiency in mechanical production. “That’s extremely important to us. We generally work in a batch size of one and have the machines working for 60-70 hours or more,” explains Späth of the high value of process reliability in measuring. “An error in the final stages can have bitter and costly consequences,” stresses Späth.