Zwei Alternativen sichern Prozess und Genauigkeit
Kontakt

Wer von Mindelheim spricht, meint im industriellen Sektor oft einen großen Maschinenbauer. Aber Mindelheim steht seit vielen Jahren auch für hochwertige Kunststoffverarbeitung, ist es doch die Heimat der ersten voll industriell gefertigten Kunststoff-Segelflugzeuge.
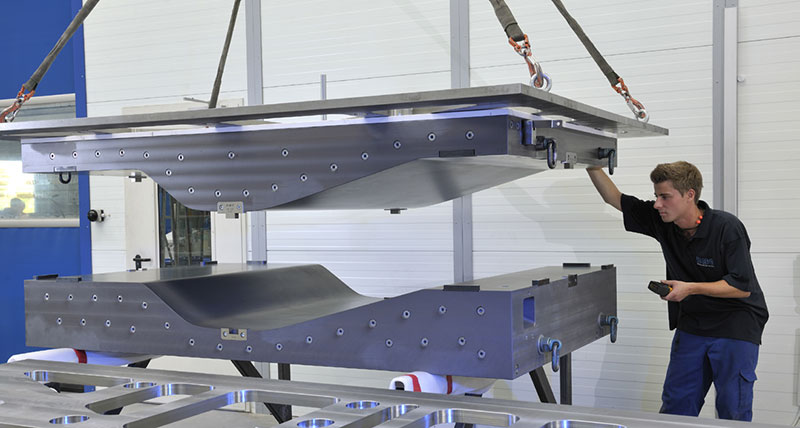
Die 1960 gegründete Firma wurde 1999 vom heutigen Inhaber übernommen und trägt seit 2001 den heutigen Namen BBG GmbH & Co. KG. Zwischenzeitlich zählt man namhafte Hersteller in Europa, Asien und Amerika zu den Kunden für Werkzeuge, Maschinen, ganze Anlagen mit dem spezialisierten Know-How aus Mindelheim. Immer weitere Aufträge zufriedener Kunden sorgen für stetiges Wachstum der Gesellschaft. Allein der Werkzeugbau mit eigener Konstruktion zählt heute ca. 25 Mitarbeiter. Mit Freude zog man schließlich in neue Betriebsgebäude, nicht zuletzt um der Fertigung mehr Platz und bessere Arbeitsbedingungen zu gönnen.
Allerdings kam es bald zu ungeahnten Problemen im Prozess-ablauf beim Messen auf den großen Bearbeitungszentren, eine unliebsame Überraschung, mit der niemand gerechnet hatte. Fehlmessungen und ungeplanter Maschinenstillstand waren die Folge. Als Ursache stellte sich schließlich die Funk-Fernsteuerung der Krananlage heraus, die mit ihrem sogenannten Frequenz-Hopping andauernd und unkontrollierbar durch Frequenzen springt und dabei auch starke Störsignale in die eigentlich für den Funkmesstaster reservierten Funkkanäle schickt. Ist der Funkmesstaster in diesem Moment aktiv, kann das Störsignal zur Maschinensteuerung durchschlagen und zur Fehlfunktion führen.
Ein Fehler am Schluss kann da bittere und teure Folgen haben
Aufgrund jahrelanger guter Erfahrung mit den Messtastern von m&h wollte BBG auf das bewährte Hilfsmittel nicht verzichten. „Die hatten wir ja schon lange im Einsatz und haben noch nie Probleme damit gehabt“, schildert Michael Späth, Bereichsleiter Fräserei und Arbeitsvorbereitung bei BBG seine damalige Situation. Vom Kranhersteller kam nicht die erwartete Unterstützung zur Lösung des Problems. Also wandte man sich an m&h. „Die haben unser Problem sofort ernst genommen und mit uns nach Abhilfe gesucht“, erzählt Michael Späth.
Schließlich ist m&h der Pionier bei Messtastern mit Funk-
Datenübertragung und hat vor Jahren den ersten derartigen
Messtaster überhaupt auf den Markt gebracht.
Mittlerweile
sind diese Geräte weltweit, vornehmlich auf Fünfachs-
Maschinen oder großen Bearbeitungszentren, im Einsatz.
Die m&h Funkmesstaster im Frequenzbereich des 433
MHz-Bandes setzen nach wie vor den Benchmark im Markt.
Vor allem mit großer Reichweite und schneller, sicherer
Signalübertragung sorgen Sie für hohe Prozesssicherheit. Im
Laufe der Jahre wurde die Funktechnik dieser Taster immer
weiter fortentwickelt und moderne Technologien sowie neue
Elektronik integriert. Heute beinhalten die Funkempfänger
von m&h beispielsweise einen permanenten Kanalscan, der
alle verfügbaren Funkkanäle auf Störsignale hin überwacht
und den Maschinenbedienern die Kanäle empfiehlt, die
ohne signifikante Störsignale sind. Das hat den Vorteil, dass
der Anwender seine Funkarchitektur im Betrieb mit fest
vergebenen Kanälen planvoll gestalten kann, ohne andere
Anwendungen im Betrieb zu stören. Andererseits führt
die permanente Kanalüberwachung des m&h Empfängers
dazu, dass Funkkanäle gemieden werden, die immer wieder
signifikante Störsignale von anderen Systemen aufweisen.
Außerdem werden bei diesem System immer ganze
Signalprotokolle mehrfach redundant übertragen, was eine
eindeutige Zuordnung der Signale ermöglicht. Das macht
dieses System zu einem der Sichersten und Schnellsten auf
dem Markt. Die neuen Elektronikmodule in den Tastern weisen
einen deutlich geringeren Energieverbrauch auf als früher,
was sich in außerordentlich langer Lebensdauer der Batterien
bemerkbar macht. Zudem sind in allen m&h Messtastern
handelsübliche Standardbatterien im Einsatz.
Allerdings ist das Frequenzband um 432 MHz, das m&h
bislang ausschließlich genutzt hat, nicht überall auf der Welt
so für die Industrie geschützt, wie es hier in Deutschland der
Fall ist. In anderen Ländern funken andere Anwendungen in
diesem Band oder es ist gar dem dortigen Militär vorbehalten; so zum Beispiel in Japan, einem wichtigen Markt im Bereich Werkzeugmaschinen. Schon deshalb war m&h auf längere Sicht gezwungen, für seine dortigen Kunden eine Alternative zu finden. Der Entwicklung im Hause m&h war es wichtig, auch bei einem alternativen System sicherzustellen, dass die Signale eindeutig identifiziert werden und immer gleichbleibend schnell an die Steuerung weitergeleitet werden. Das ist schließlich die Voraussetzung für Prozesssicherheit und gleichbleibende Genauigkeit der Messergebnisse.
Weil viele Kunden auch in Zukunft das geschützte Industrie-
funkband nutzen wollen, war klar, dass diese Technologie weiter Standard bei m&h bleibt. Für alle Fälle, in denen die örtlichen Gegebenheiten eine Alternativlösung notwendig machen, hat man sich für das neue Industriefrequenzband um 2.4 GHz entschieden, das vielfach bereits für Industrieanwendungen verwendet wird. Dank neuer Technologien ist es m&h gelungen, auch in diesem Frequenzband sichere Verhältnisse zu schaffen. Mit der automatischen Frequenzauswahl AFS (Automatic Frequency Select) werden die Frequenzbereiche dieses Funkbandes permanent gescannt und automatisch Teilfrequenzen gewählt, die frei von Störsignalen sind. Das sichert nicht nur die schnelle und störungsfreie eigene Übertragung, sondern verhindert auch Störungen mit und von WLAN- oder Bluetooth Systemen oder anderen Funkquellen. Durch das Frequenzspreizverfahren sendet der Messtaster dann seine Signale vielfach redundant und mit hoher Signaldichte, ähnlich der bewährten m&h Technologie bei den bisherigen Systemen. Das sichert zuverlässig schnellste Signalübertragung mit kürzest möglichen Delay-Zeiten und stellt gleichbleibende Messgenauigkeit sicher. Das sonst übliche Frequenz-Hopping mit unkalkulierbaren Übertragungszeiten wird ebenso vermieden, wie das zeitraubende Hüpfen entlang belegter Funkkanäle.
Im Fall BBG hat m&h kurzentschlossen angeboten, BBG als
einen der Pilotkunden für diese Technik mit einem Null-Serienmodell der neuen 2.4GHz-Technologie zu Testzwecken auszurüsten, was man hier gerne angenommen hat. „Der Service von m&h hat unsere Probleme wirklich ernst genommen und sich sehr engagiert. Die haben echt was bewegt. Das war wirklich lösungsorientiert“, freut sich Michael Späth. Der zunächst provisorisch an einer Maschine installierte Taster funktionierte auf Anhieb ohne Störungen.
Also wurde auch die zweite Maschine schon bald auf die neue 2.4 GHz-Technologie von m&h umgerüstet. „Seit der Umrüstung hatten wir keine einzige Fehlmessung mehr“,
freut sich Michael Späth über die wiedergewonnene Prozess-
sicherheit. Nun kann BBG wieder wie gewohnt mit den
Messtastern rüsten, antasten, ausrichten sowie Regelgeo-metrien messen. Die Messtaster sind eine unverzichtbare Arbeitshilfe für hohe Genauigkeit ebenso, wie für die Prozesssicherheit und Wirtschaftlichkeit der mechanischen Fertigung. „Das ist für uns sehr wichtig. Schließlich arbeiten wir in aller Regel in der Losgröße eins und auch gut und gerne mal mit 60 bis 70 Stunden oder mehr Bearbeitungszeit auf den Maschinen“, erläutert Späth den hohen Stellenwert der Prozesssicherheit beim Messen.