Mobile components make inspection and production fully autonomous
A unique combination of Hexagon measurement systems comes together with AGV and robotic technology to show the way forward to a future of truly autonomous large-scale production
Contact us
UniFix autonomous flow line | Absolute Tracker + 3DArena
Driven by the urgent need of the aerospace industry to establish more efficient and steerable production approaches, the UniFix research project has brought together innovative partners from industry and research in the aerospace sector to set higher standards with an ingenious flow line inspection and production setup. The project is a collaboration between Hexagon, Stäubli WFT, FFT Production Systems and the Fraunhofer IFAM research institute.
The UniFix concept is that of a flexible component carrier that independently cycles different large components through several processing stations. In this process, an electronic flow of all relevant component and process data is created, enabling the reuse of measurement data in all subsequent stations as well as delivering better defect tracking. Time-consuming measurement processes are outsourced from the production stations, which only perform quick referencing tasks. With such a system, components no longer need to be set up and assembled during transitions between stations, significantly increasing the efficiency of the process.
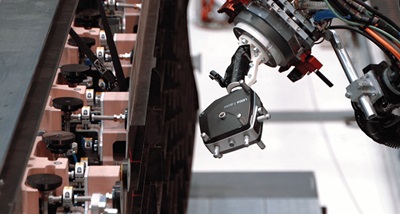
Upon this vehicle is mounted a customisable holding fixture designed to accommodate several types of large component. A special design enables a transport without deformation to the mobile holding fixture.
The selection and definition of each target process in the production line is intuitively performed through a custom tablet interface. This is connected to a central process data management system that generates orders and manages the entire flow line by monitoring defined key performance indicators.

The actual position of each moulding is then checked by Hexagon’s 3DArena dynamic multi-camera photogrammetry system, which can record every part of the large fixture simultaneously. By comparing against the CAD drawing, it provides real-time adjustment data to ensure accurate positioning of the fixture elements, with adjustment parameters displayed live in the software, overlaid on the CAD model. The dynamic referencing capacity of the 3DArena system means the position of the fixture can be easily tracked throughout the adjustment process as the position of each individual fixture element is fine tuned.

Following this adjustment, the component to be worked on is mounted on the holding fixture. Once placed and secured before transport, the automated vehicle moves the mounted component onto the next defined production step – the process of geometrical referencing and inspection.
Once the system arrives at the inspection and referencing station, the mobile holding fixture is initially referenced by one of Hexagon’s flagship laser tracker systems, the Leica Absolute Tracker AT960. This can measure to retro reflectors mounted on the fixture, allowing for highly accurate referencing within the inspection station.

With this inspection data, the production process can identify key features and define things such as the location of machining trajectories for the trimming of the outer edge of an aerospace tail plane or position of drillings on wind turbine blades.
Following inspection, the mobile holding fixture moves on to the machining station. This marks the end of the UniFix flow line, with the AGV freed to pursue the next transport order during the machining process.

“It can be concluded that the utilisation of the AGV for transporting the holding fixture reduces the number of handling operations drastically,” explains Christoph Brillinger, UniFix project leader Fraunhofer IFAM in Stade. Due to the UniFix concept, the machining system can focus on its original purpose, namely high-quality machining operations.

Thanks to this innovative research project, new standards have been set in the productivity of machining systems.
The UniFix project is a collaboration between a group of leading organisations in the field of manufacturing research and development. Stäubli is a global mechatronics solution provider, whose Stäubli WFT arm creates automated guided vehicles (AGVs) that are designed for the heaviest loads without sacrificing manoeuvrability. FFT Production Systems are a leading global supplier of innovative, flexible and highly complex manufacturing systems, specialising in development, design and implementation and running projects worldwide with customers in automotive, aerospace and other sectors. Fraunhofer IFAM is one of the most important independent research institutes in Europe in the fields of “Adhesive Bonding Technology and Surfaces” and “Shaping and Functional Materials”. At the Stade location, automation, digitalization and production technology are the focus of R&D work with the aim of providing customers with tailored reliable and application-oriented solutions. Hexagon brings to the table a range of advanced measurement hardware and software, ideal for capturing, processing and analysing the high detail.