Componentes móveis tornam a inspeção e a produção totalmente autônomos
Uma combinação exclusiva de sistemas de medição da Hexagon com tecnologia AGV e robótica para uma produção realmente autônoma em grande escala
Contato
Linha de fluxo autônoma UniFix | Absolute Tracker + 3DArena
Impulsionado pela necessidade urgente da indústria aeroespacial de estabelecer abordagens de produção mais eficientes e controláveis, o projeto de pesquisa UniFix reuniu parceiros inovadores da indústria e pesquisa no setor aeroespacial para definir padrões mais altos com uma configuração inovadora de produção e inspeção de linha de fluxo. O projeto é uma colaboração entre a Hexagon, Stäubli WFT, FFT Production Systems e instituto de pesquisa Fraunhofer IFAM.
O conceito UniFix trata de uma transportadora flexível de componentes que faz independentemente os ciclos de diferentes componentes de grande porte utilizando várias estações de processamento. Nesse processo, cria-se um fluxo eletrônico de todos os componentes e dados relevantes do processo, permitindo que os dados de medição sejam reutilizados em todas as estações subsequentes, além de fornecer um melhor rastreamento de defeitos. Os processos de medição demorados são terceirizados das estações de produção, que realizam apenas tarefas de referência rápida. Com esse sistema, os componentes não precisam mais ser configurados e montados nas transições entre as estações, aumentando significativamente a eficiência do processo.
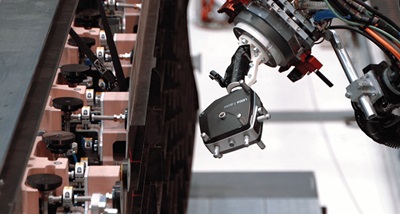
Sobre esse veículo é montado um dispositivo de fixação personalizável projetado para acomodar vários tipos de componentes de grande porte. O design especial permite a realização de um transporte sem deformação até o dispositivo de fixação.
A seleção e definição de cada processo desejado na linha de produção é realizada de maneira intuitiva por meio de uma interface personalizada de tablet, conectada a um sistema central de gerenciamento de dados de processo que gera pedidos e gerencia toda a linha de fluxo monitorando os principais indicadores de desempenho definidos.

A posição real de cada moldagem é verificada pelo sistema 3DArena de fotogrametria dinâmica com várias câmeras da Hexagon, que tem capacidade de registrar simultaneamente todas as peças do dispositivo de grande porte. Na comparação com o desenho CAD, ele apresenta dados de ajuste em tempo real para garantir o posicionamento preciso dos elementos do dispositivo, com parâmetros de ajuste exibidos em tempo real no software, sobrepostos ao modelo CAD. A capacidade de referência dinâmica do sistema 3DArena significa que a posição do dispositivo pode ser rastreada facilmente durante todo o processo de ajuste, pois a posição de cada elemento individual do dispositivo é ajustada com precisão.
Após esse ajuste, o componente a ser trabalhado é montado no dispositivo de fixação. Depois de posicionado e protegido para o transporte, o veículo automatizado move o componente montado para a próxima etapa de produção definida: o processo de inspeção e referência geométrica.
Quando o sistema chega à estação de inspeção e referência, o dispositivo de fixação móvel é inicialmente referenciado por um dos principais sistemas de rastreador a laser da Hexagon, o Leica Absolute Tracker AT960. Esse processo pode medir retrorrefletores montados no dispositivo, permitindo uma referência altamente precisa na estação de inspeção.
Com o referenciamento inicial concluído, inicia-se o processo de medição. O componente é capturado como uma nuvem de pontos 3D em todas as áreas de interesse, usando novamente o rastreador a laser AT960. Nessa etapa do processo, o rastreador a laser é emparelhado com um scanner a laser 3D Leica T-Scan 5 montado no braço do robô, que é capaz de mover a peça em sua própria plataforma de AGV.
Com esses dados de inspeção, o processo de produção pode identificar os principais recursos e definir informações como a localização das trajetórias de usinagem para o corte da borda externa de uma cauda de aeronave ou a posição das perfurações nas pás de turbinas eólicas.
Após a inspeção, o dispositivo de fixação móvel segue para a estação de usinagem, que marca o fim da linha de fluxo do UniFix, liberando o AGV para prosseguir para o próximo pedido de transporte no processo de usinagem.
Graças à abordagem UniFix, o referenciamento do sistema de usinagem consiste em um número bastante reduzido de pontos a serem medidos, oferecendo um benefício significativo de produtividade no processo de usinagem. Assim, o conceito de calibração em várias etapas necessário para a linha de fluxo do UniFix agora é totalmente implementado.
“Conclui-se que a utilização do AGV para o transporte do dispositivo de fixação reduz drasticamente o número de operações de manuseio”, explica Christoph Brillinger, líder do projeto UniFix Fraunhofer IFAM, em Stade. Com o conceito UniFix, o sistema de usinagem pode se concentrar em sua finalidade original: operações de usinagem de alta qualidade.
“A flexibilidade do conceito de processo também pode ser usada para harmonizar os tempos de ciclo e reduzir o prazo de entrega. A capacidade de captura de dados consistente do sistema de gerenciamento de dados com processamento central também simplifica a identificação precoce de defeitos de fabricação, reduzindo o desperdício de peças”, acrescenta Christoph Brillinger.
Graças a esse projeto de pesquisa inovador, foi possível estabelecer novos padrões na produtividade dos sistemas de usinagem.
O projeto UniFix é uma colaboração entre um grupo de organizações líderes na área de pesquisa e desenvolvimento de manufatura. A Stäubli é uma fornecedora global de soluções mecatrônicas, e sua divisão Stäubli WFT desenvolve AGVs (veículos autoguiados) projetados para as cargas mais pesadas sem sacrificar a manobrabilidade. A FFT Production Systems é uma fornecedora líder global de sistemas de fabricação inovadores, flexíveis e altamente complexos, sendo especializada no desenvolvimento, design, implementação e execução de projetos em todo o mundo com clientes nos setores automotivo, aeroespacial e outros. O Fraunhofer IFAM é um dos institutos de pesquisa independentes mais importantes da Europa nas áreas de "Tecnologia de colagem adesiva e superfícies" e de "Materiais de modelagem e funcionais". Na região de Stade, a tecnologia de automação, digitalização e produção são o foco do trabalho de P&D, tendo o objetivo de fornecer aos clientes soluções personalizadas, confiáveis e orientadas para a aplicação. A Hexagon contribui com uma série de softwares e hardwares avançados de medição, ideais para a captura, o processamento e a análise detalhados.