Les composants mobiles rendent la fabrication et le contrôle entièrement autonomes
Une combinaison unique de systèmes de mesure Hexagon est associée avec des technologies AGV et robotiques pour montrer la voie d’une fabrication réellement autonome à grande échelle
Contact
Système autonome UniFix | Absolute Tracker + 3DArena
Reflétant l’urgence de mettre en œuvre des approches de fabrication plus efficaces et pilotables dans l’aéronautique, le projet de recherche UniFix a réuni des partenaires innovants dans l’industrie et la recherche aéronautiques pour définir un plus haut niveau avec un système de fabrication et de contrôle ingénieux. Le projet réunit Hexagon, Stäubli WFT, FFT Production Systems et l’institut de recherche Fraunhofer IFAM.
Le concept UniFix repose sur un support de composant flexible qui véhicule de façon indépendante différents grands éléments entre des stations de traitement. Dans le cadre de ce processus, un flux électronique de toutes les données de composant et de traitement est créé, permettant de réutiliser les données de mesure sur toutes les stations en aval et fournissant un meilleur suivi des défauts. Les longs processus de mesure sont dissociés des stations de fabrication, qui réalisent uniquement des référencements rapides. Avec un
tel système, les composants n’ont plus besoin d’être installés et assemblés pendant les passages entre les stations, ce qui rend le processus bien plus efficace.
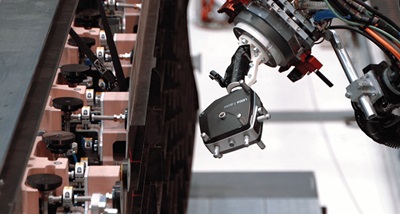
Sur ce véhicule est montée une fixation personnalisable, conçue pour monter différents types de grands composants. Une conception spéciale permet de transporter les éléments sans déformer la fixation mobile.
Chaque processus cible sur la chaîne de fabrication est sélectionné et défini de manière intuitive avec une interface tablette personnalisée. Celle-ci est connectée à un système de gestion de données centralisé qui génère des ordres et gère tout le processus en surveillant les indicateurs de performance clé définis.

La position réelle de chaque moulage est alors vérifiée par le système photogrammétrique dynamique multi-caméra 3DArena, qui enregistre simultanément chaque partie de la grande fixation. En la comparant avec le dessin CAO, il fournit des données de réglage en temps réel pour garantir un positionnement précis des éléments de fixation, avec l’affichage en direct de paramètres d’ajustement dans le logiciel, qui est superposé sur le modèle CAO. La capacité de référencement dynamique du système 3DArena permet de suivre facilement la position de la fixation à travers le processus d’ajustement. La position de chaque élément de fixation est ajustée avec précision.

Après cet ajustement, le composant à traiter est monté sur la fixation. Après la mise en place et le calage pour le transport, le véhicule automatisé déplace le composant monté jusqu’à la prochaine station de production, le processus de référencement géométrique et d’inspection.
Une fois que ce système arrive à la station d’inspection et de référencement, la fixation mobile est initialement référencée par un système laser tracker Hexagon de haute performance, à savoir le Leica Absolute Tracker AT960. Celui-ci peut effectuer des mesures sur des rétroréflecteurs montés sur la fixation, permettant un référencement de haute précision au niveau de la station d’inspection.

Après le référencement initial, le processus de mesure démarre. Le composant est capturé comme nuage de points 3D dans toutes les zones d’intérêt, là aussi avec le laser tracker AT960. À ce stade du processus, le laser tracker est associé à un scanner laser 3D Leica T-Scan 5 monté sur un robot, qui est capable de se déplacer autour de la pièce sur sa propre plateforme AGV séparée.
Avec ces données d’inspection, le processus de fabrication peut identifier des caractéristiques clés et définir des paramètres comme les trajectoires d’usinage pour l’ajustement du bord extérieur du plan horizontal d’un avion ou la position des perçages sur les éoliennes.
Après l’inspection, la fixation mobile se déplace jusqu’à la station d’usinage. C’est la fin du cycle UniFix, l’AGV est libéré pour effectuer le prochain ordre de transport pendant l’usinage.

« On peut en conclure que l’utilisation de l’AGV pour transporter la fixation réduit considérablement le nombre d’opérations de manutention », explique Christoph Brillinger, chef de projet UniFix à l’institut Fraunhofer IFAM, à Stade. Le concept UniFix permet au système d’usinage de se focaliser sur sa finalité initiale, à savoir réaliser des usinages de haute qualité.

« La flexibilité de ce processus contribue aussi à harmoniser les temps de cycle et à réduire les délais d’exécution. La capture efficace des données réalisée par le système de gestion centralisée favorise également l’identification précoce de défauts de fabrication, en réduisant ainsi le rebut », ajoute Christoph Brillinger.
Grâce à ce projet de recherche innovant, de nouveaux standards de productivité ont été définis pour les systèmes d’usinage.
Le projet UniFix est une collaboration entre un groupe d’organisations leaders dans le domaine de la recherche et du développement manufacturiers. Stäubli est un fournisseur mondial de solutions mécatroniques, dont la division WFT réalise des véhicules guidés automatisés (AGV) conçus pour les charges les plus lourdes sans sacrifier la manœuvrabilité. FFT Production Systems est un fournisseur mondial leader de systèmes de fabrication innovants, flexibles et très complexes, spécialisé dans le développement, la conception, l’implémentation et traitant des projets dans le monde entier avec des clients du secteur de la construction automobile, de l’aérospatiale et d’autres industries. Fraunhofer IFAM est l’un des instituts de recherche indépendants les plus importants en Europe dans les domaines « Technologies d’assemblage adhésive et Surfaces » et « Formage et Matériaux fonctionnels ». Sur le site de Stade, le département R&D se concentre sur les technologies d’automatisation, de numérisation et de fabrication afin de fournir aux clients des solutions sur mesure fiables, axées sur l’application. Hexagon apporte un ensemble de matériel et de logiciels de mesure avancés, idéal pour relever, traiter et analyser les détails.