I componenti mobili rendono la verifica e la produzione completamente autonome
Una combinazione unica di sistemi di misura di Hexagon si affianca alla tecnologia AGV e robotica per realizzare la produzione su larga scala veramente autonoma del futuro
Contattateci
La produzione a flusso continuo autonoma UniFix | Absolute Tracker + 3DArena
Spinto dall’urgente necessità del settore aerospaziale di stabilire strategie di produzione più efficienti e flessibili, il progetto di ricerca UniFix ha coinvolto partner innovativi dell’industria e della ricerca nel settore aerospaziale per definire standard più elevati grazie a un innovativo sistema di verifica e produzione a flusso continuo. Il progetto è frutto della collaborazione tra Hexagon, Stäubli WFT, FFT Production Systems e l’istituto di ricerca Fraunhofer IFAM.
Il sistema UniFix prevede una piattaforma flessibile di trasporto dei componenti, che consente di gestire in modo indipendente diversi elementi di grandi dimensioni attraverso varie stazioni di lavorazione. Questo processo crea un flusso elettronico di tutti i dati rilevanti dei componenti e del processo, che consente di riutilizzare i dati di misura in tutte le stazioni successive e di ottenere una migliore tracciabilità dei difetti. I processi di misura che richiedono molto tempo sono esternalizzati dalle stazioni di produzione, che eseguono solo compiti di referenziazione rapida. Grazie a questo sistema i componenti non devono più essere impostati e assemblati durante le fasi di movimentazione da una stazione all’altra, aumentando in modo significativo l’efficienza del processo.
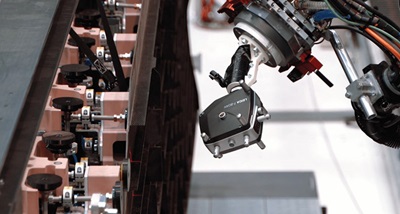
Su questo veicolo è montata un’attrezzatura di fissaggio regolabile, progettata per accogliere diversi tipi di componenti di grandi dimensioni. Un design particolare consente un trasporto senza problemi dell’attrezzatura di fissaggio mobile.
La selezione e la definizione di ogni processo specifico della linea di produzione avviene in modo intuitivo attraverso un’interfaccia personalizzata su tablet. Questa è collegata a un sistema centrale di gestione dei dati di processo che comanda e controlla l’intero flusso continuo monitorando gli indicatori chiave di prestazione definiti.
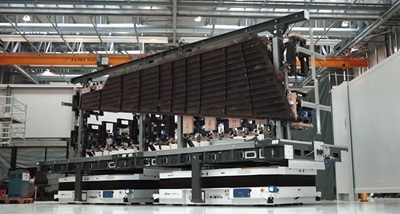
dei supporti, che fornisce i dati di regolazione per l’attrezzatura di fissaggio a regolazione automatica. Dopo il posizionamento, il mantenimento della forma è garantito da supporti bilanciati con precisione.
La posizione effettiva di ogni stampo è poi controllata dal sistema di fotogrammetria dinamica multicamera 3DArena di Hexagon, che può monitorare simultaneamente ogni parte della grande attrezzatura di fissaggio. Grazie al confronto con il disegno CAD, fornisce dati di regolazione in tempo reale per garantire un posizionamento preciso degli elementi dell’attrezzatura di fissaggio, con i parametri di regolazione visualizzati in tempo reale nel software, sovrapposti al modello CAD. La capacità di referenziazione dinamica del sistema 3DArena consente di seguire facilmente la posizione dell’attrezzatura di fissaggio durante l’intero processo di regolazione mentre si mette a punto la posizione di ogni singolo elemento della suddetta attrezzatura
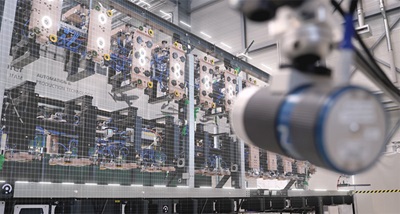
Una volta che il sistema arriva alla stazione di verifica e referenziazione, l’attrezzatura mobile di fissaggio è referenziata dal Leica Absolute Tracker AT960, uno dei sistemi laser tracker di punta di Hexagon. La misura può essere effettuata su retroriflettori montati sull’attrezzatura di fissaggio, consentendo un riferimento estremamente preciso all’interno della stazione di verifica.
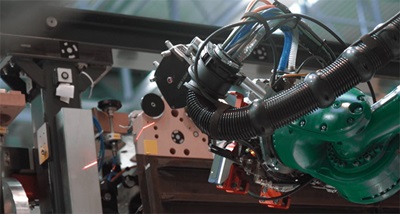
5 montato su un braccio del robot, in grado di muoversi intorno al pezzo su una piattaforma AGV separata.
Con questi dati di verifica, il processo di produzione può identificare elementi chiave e definire aspetti quali la posizione delle traiettorie di lavorazione per la rifilatura del bordo esterno di un piano di coda di un velivolo o la posizione dei fori sulle pale delle turbine eoliche.
Dopo la verifica, l’attrezzatura mobile di fissaggio passa alla stazione di lavorazione. In questo modo si conclude il flusso continuo di UniFix e l’AGV è libero di proseguire con l’ordine di trasporto successivo durante il processo di lavorazione.
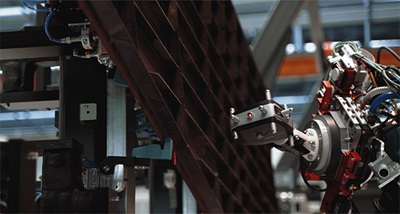
“Si può concludere che l’utilizzo dell’AGV per il trasporto dell’attrezzatura di fissaggio riduce drasticamente il numero di operazioni di movimentazione”, spiega Christoph Brillinger, responsabile del progetto UniFix del Fraunhofer IFAM di Stade. Grazie alla soluzione UniFix, il sistema di lavorazione può concentrarsi sul suo scopo originale, ovvero operazioni di lavorazione di alta qualità.
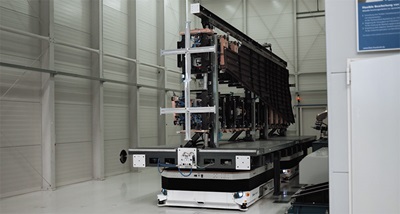
“La flessibilità del processo può essere sfruttata anche per armonizzare i tempi di ciclo e ridurre i tempi di consegna. La capacità di acquisizione dati coerente del sistema di gestione dati elaborato a livello centrale semplifica anche l’identificazione precoce dei difetti di produzione, portando a una riduzione dei pezzi di scarto”, aggiunge Christoph Brillinger.
Grazie a questo innovativo progetto di ricerca, sono stati fissati nuovi standard nella produttività dei sistemi di lavorazione.
Il progetto UniFix è una collaborazione tra un gruppo di organizzazioni leader nel campo della ricerca e dello sviluppo della produzione. Stäubli è un fornitore globale di soluzioni meccatroniche, che con la sua unità Stäubli WFT crea veicoli a guida automatica (AGV) progettati per i carichi più pesanti senza sacrificare la manovrabilità. FFT Production Systems è un fornitore leader a livello mondiale di sistemi di produzione innovativi, flessibili e altamente complessi, specializzato nello sviluppo, nella progettazione e nella realizzazione di progetti in tutto il mondo con clienti del settore automobilistico, aerospaziale e di altri settori. Fraunhofer IFAM è uno dei più importanti istituti di ricerca indipendenti in Europa nei campi della “Tecnologia di incollaggio e superfici” e dei “Materiali funzionali e di modellazione”. Presso la sede di Stade, l’automazione, la digitalizzazione e le tecnologie di produzione sono al centro del lavoro di ricerca e sviluppo, con l’obiettivo di fornire ai clienti soluzioni affidabili e orientate alle applicazioni. Hexagon mette a disposizione una gamma di hardware e software di misura avanzati, ideali per acquisire, elaborare e analizzare ogni dettaglio.