Mobile Bauteile für vollständig autonome Inspektions- und Fertigungsprozesse
Eine einzigartige Kombination aus Hexagon-Messsystemen mit fahrerlosen Transportsystemen (AGV) und Robotertechnologie weist den Weg in die Zukunft einer wirklich autonomen Fertigung großer Bauteile
Kontakt
Autonome Fließfertigung UniFix | Absolute Tracker + 3DArena
Getrieben vom dringenden Bedarf der Luft- und Raumfahrtindustrie, effizientere und besser steuerbare Produktionsverfahren zu schaffen, schlossen sich im Forschungsprojekt UniFix innovative Partner aus Industrie und Forschung im Luft- und Raumfahrtsektor zusammen, um mit einem intelligenten Fließprozess für die Inspektion und Fertigung neue Maßstäbe zu setzen. Das Projekt ist eine Zusammenarbeit zwischen Hexagon, Stäubli WFT, FFT Produktionssysteme und dem Fraunhofer IFAM.
Das UniFix-Konzept beruht auf einem flexiblem Bauteilträger, der unterschiedliche Großbauteile autonom durch mehrere Prozessstationen taktet. Dabei wird ein elektronischer Fluss aller relevanten Bauteil- und Prozessdaten realisiert, der eine Wiederverwendung von Messdaten in allen nachfolgenden Stationen sowie eine bessere Rückverfolgung von Fehlern erlaubt. Zeitaufwändige Messungen werden aus den Fertigungsstationen ausgelagert, die nur noch Schnellreferenzierungen ausführen. Zudem entfallen bei einem derartigen System die Ein- und Ausrüstvorgänge der Bauteile bei den Übergängen zwischen den Stationen. Das steigert die Prozesseffizienz deutlich.
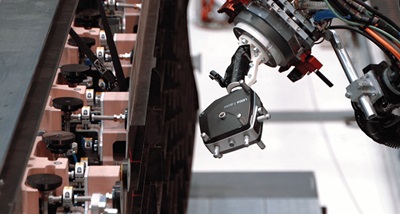
Auf diesem Fahrzeug ist eine individuell anpassbare Haltevorrichtung montiert, die unterschiedliche große Bauteiltypen aufnehmen kann. Ein spezielles Design ermöglicht einen Transport ohne Verformungen der mobilen Haltevorrichtung.
Jeder Zielprozess in der Fertigungslinie lässt sich intuitiv über eine maßgeschneiderte Tablet-Bedienoberfläche auswählen und definieren. Diese ist mit einem zentralen Prozessdaten-Managementsystem verbunden, das Arbeitsaufträge erstellt und den gesamten Fließprozess verwaltet, in dem es definierte Leistungskennzahlen überwacht.

Die tatsächliche Position jedes Formteils wird dann mithilfe des dynamischen Mehrkamera-Photogrammetriesystems 3DArena von Hexagon überprüft, das jedes Teil der großen Vorrichtung gleichzeitig erfasst. Durch den Vergleich mit der CAD-Zeichnung liefert es Einstelldaten in Echtzeit und gewährleistet damit die korrekte Positionierung der Vorrichtungselemente. Dabei werden die Einstellparameter live in der Software über das CAD-Modell gelegt. Da das 3DArena-System über eine dynamische Referenzierungsfunktion verfügt, lässt sich die Position der Vorrichtung während der Feinjustierung jedes einzelnen Vorrichtungselements einfach verfolgen.

Im Anschluss an diese Justierung wird das zu bearbeitende Bauteil auf der Haltevorrichtung befestigt. Ist das Bauteil in der Vorrichtung positioniert und fixiert, transportiert das AGV das befestigte Bauteil zum nächsten definierten Fertigungsschritt – der geometrischen Referenzierung und Inspektion.
Bei seiner Ankunft an der Inspektions- und Referenzierungsstation, wird die mobile Vorrichtung zunächst von Hexagons Flaggschiff-Laser-Tracker-System, dem Leica Absolute Tracker AT960, referenziert. Die Messungen mithilfe der an der Vorrichtung angebrachten Retroreflektoren gewährleisten die hochpräzise Referenzierung in der Inspektionsstation.

Mithilfe dieser Inspektionsdaten identifiziert der Produktionsprozess Schlüsselmerkmale und definiert Parameter, wie beispielsweise die Lage von Bearbeitungsbahnen für den Beschnitt der Außenkanten eines Flugzeugleitwerks oder die Position von Bohrungen an den Rotorblättern einer Windkraftanlage.
Nach der Inspektion bewegt sich die Haltevorrichtung zur nächsten Bearbeitungsstation. Damit ist der Endpunkt des UniFix-Fließprozesses erreicht. Ab hier kann das freigegebene AGV die nächste Transportaufgabe im Bearbeitungsprozess in Angriff nehmen.

„Es hat sich gezeigt, dass sich dank des Einsatzes eines AGV für den Transport der Vorrichtung die Anzahl der Bedienoperation erheblich reduziert“, erklärt Christoph Brillinger, Projektleiter UniFix bei Fraunhofer IFAM in Stade. Dank des UniFix-Konzepts konzentriert sich das Bearbeitungssystem auf seine eigentliche Aufgabe: das Ausführen hochqualitativer Bearbeitungsoperationen.

Dieses innovative Forschungsprojekt setzt neue Maßstäbe hinsichtlich der Produktivität von Bearbeitungssystemen.
Im Rahmen des UniFix-Projekts arbeitet eine Gruppe führender Organisationen aus dem Bereich Forschung und Entwicklung in der Fertigung zusammen. Stäubli ist ein weltweit tätiger Anbieter von Mechatroniklösungen. Der Geschäftszweig Stäubli WFT fertigt fahrerlose Transportsysteme (AGV) für besonders große Nutzlasten mit ausgezeichneter Manövrierbarkeit. FFT Produktionssysteme ist ein führender internationaler Anbieter innovativer, flexibler und hochkomplexer Produktionssysteme, der sich auf die Entwicklung, Konstruktion sowie die Implementierung und Durchführung von Kundenprojekten im Automobilbau, in der Luft- und Raumfahrt und anderen Branchen im internationalen Rahmen spezialisiert. Das Fraunhofer IFAM ist eine der europaweit bedeutendsten unabhängigen Forschungseinrichtungen auf den Gebieten „Klebtechnik und Oberflächen“sowie „Formgebung und Funktionswerkstoffe“. Am Standort in Stade stehen Automatisierung, Digitalisierung und Produktionstechnik im Fokus der Forschungs- und Entwicklungsarbeit. Ziel ist es, Kunden maßgeschneiderte, zuverlässige und anwendungsorientierte Lösungen anzubieten. Hexagon liefert eine Reihe fortgeschrittener Messtechnik und Messsoftware, die sich ideal für die Erfassung, Verarbeitung und Analyse der detailreichen Daten eignet.