Let's do a quick calibration
Contact us

The contract manufacturer SHW Bearbeitungstechnik GmbH has equipped its machining and turning/milling machines with radio-wave touch probes by m&h and regularly calibrates the machine tables with it. That provides accuracy, and the probes save set-up times and allow for an accelerated and secure production of mostly large and complex cast parts.
The contract manufacturer SHW Bearbeitungstechnik GmbH confirms that measuring with the probe significantly accelerated not only the set-up times. In addition, the check measurements between the processing steps and regular calibrations accelerate the production process as a whole and ensure process reliability. There, the increased productivity with higher accuracy is highly welcome. But one thing at a time: The SHW Bearbeitungstechnik GmbH was founded in the year 2005 from the former SHW and has been successfully working since then as a machining service provider, not only for the SHW Werkzeugmaschi-nen GmbH (SHW WM), but also for many other customers from the fields of mechanical engineering, plant engineering and in the large engines sector. Turning, milling and grinding of medium and large workpieces is offered, mostly from various cast iron or steel types. As with any contract manufacturer, the workpiece sizes vary greatly. SHW Bearbeitungstechnik processes workpieces from an edge length of about 500 mm up to 18 m in length and up to a weight of 20 tons. Generally, complex shapes with high accuracy are required.
The machine park includes both large machining centers and turning-milling machines from SHW WM as well as from other manufacturers. Five SHW WM machines are equipped with m&h probes which have wireless data transmission. This is necessary to transmit the signals of the probe quickly and reliably over large distances within the machining areas of the machines to the control. “We frequently use the probes to find the zero points and to probe the workpieces,” explains Roland Ziegler, Managing Director of SHW Bearbeitungstechnik GmbH. “But very often we use the probe also to check clearances and for length measurement, before and during the machining. This saves a lot of time and prevents errors. We also need no longer length measuring devices.” An advantage not to be underestimated, if you take into account that the workpieces at SHW Bearbeitungstechnik can be up to 18 m in length.
This is also a reason that probe data transmission is done by radio and not, as is usual in small machining centres, with infrared technology. Infra-red technology has a limited range and requires a direct optical transmission path between transmitter and receiver. This can not be reliably guaranteed with these workpiece sizes. This is why m&h marketed the then first functionally reliable probe with radio transmission many years ago. These devices have become firmly established with many machining companies and have proven themselves with highest operational reliability in daily use in the workshops. These good experiences with m&h probes are also confirmed by SHW Werkzeugmaschinen GmbH, which generally have been equipping their machines with m&h probes for many years if customers order a machine with a probe. Many customers have reported good experiences over the years, which not least can be seen in repeat orders of the machines, specifically those with m&h probes. “The handling is easy and the devices are just great,” Roland Ziegler also confirms his good operational experience.
Because we produce individual parts and small series, the probes are used very often by us - and that since many years without any problems.Right from the beginning, m&h used the protected industrial radio band at 433 MHz with 64 selectable channels in its radio wave touch probes. Constantly improving electronics ensure high transmission and reception performance in order to provide secure data transmission and to prevent unnecessary machine downtimes even under extreme conditions. Even measuring within the workpieces is possible with this powerful technology. The security of signal transmission is the most important control variable for accuracy and reliability on the machines to avoid unscheduled stoppages or even damage. Especially with large workpieces or the tilting of multiple-axis heads, shading of the direct signal line can occur, which, however has no effect if a powerful wireless technology, such as the m&h, is used.
The receiver mounted on the outside of the machine housing has an antenna that protrudes into the machining area of the machine and is in turn connected to the control unit via a single cable. The roughly cigar-sized receiver contains all necessary electronics and the so-called interfaces to the machine control. It monitors all radio channels for external signals during the entire duty cycle of the machine and recommends a channel for the installer or operator to use. This can be selected by a simple touch of a button. Channels on which it receives significant exterior signals are blocked automatically to prevent malfunctions. The selected channel is shown at all times so that the customer can select which channels to use when production is being done with multiple machines. This individual channel selection on the wireless receiver by the user also ensures that multiple machines in a hall do not interfere with each other and that false signals are excluded. Thus, radio-controlled crane paths can also do no harm. With LEDs and a digital display, the receiver keeps the operator informed about the state of the touch probe and the signal quality. It monitors the signal strength to request a battery replacement at an early stage in case of doubt. “Because we produce individual parts and small series, the probes are used very often by us – and that since many years without any problems,” says Roland Ziegler.
To meet the stringent accuracy requirements for the versatile turn-milling machines, Roland Ziegler has created his own strategy. Before mounting a new workpiece for turning or milling on the machine table, which is designed as a turntable, a calibration ring is clamped quickly and the exact centre of the turntable is determined. Only then the workpiece is aligned and clamped. In the way, the thermal displacement of the machine is recorded and the zero point and the centre of rotation are calibrated based on the current state of the machine table. In this way, the processing takes place with the best possible basic accuracy. “Meanwhile, measuring with probes has become an integral part of our production,” explains Roland Ziegler. “This provides accuracy and reliability in our machining. The costs of the probe easily pay for themselves. We measure more and more and the next step must be measuring whole shapes and contours while still in the machine,” says Roland Ziegler about his views on his future projects.
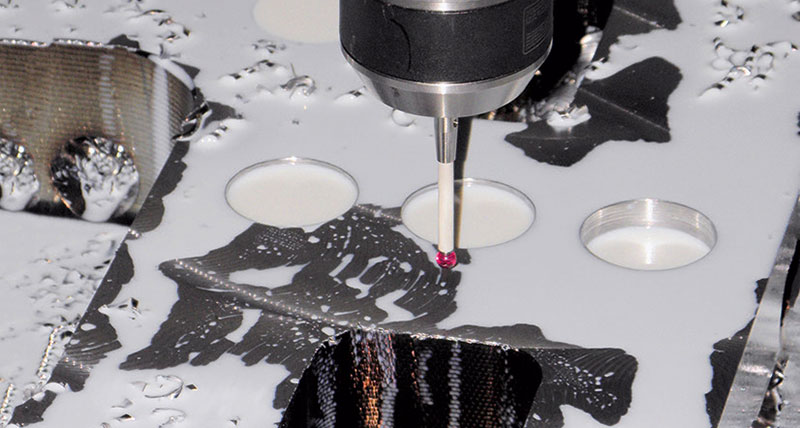
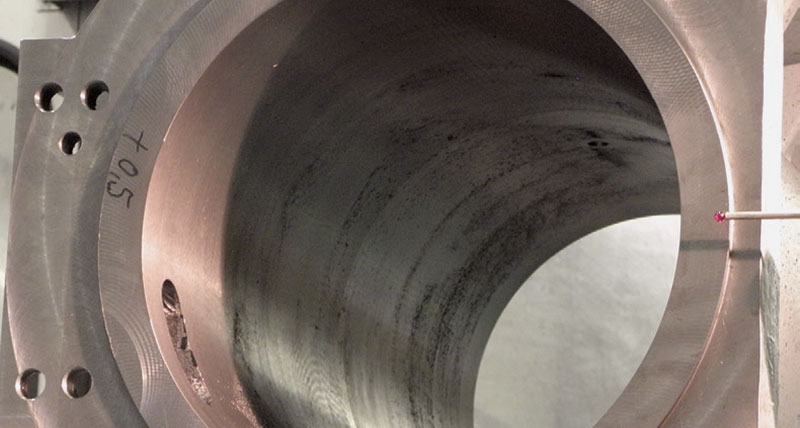
This is also a reason that probe data transmission is done by radio and not, as is usual in small machining centres, with infrared technology. Infra-red technology has a limited range and requires a direct optical transmission path between transmitter and receiver. This can not be reliably guaranteed with these workpiece sizes. This is why m&h marketed the then first functionally reliable probe with radio transmission many years ago. These devices have become firmly established with many machining companies and have proven themselves with highest operational reliability in daily use in the workshops. These good experiences with m&h probes are also confirmed by SHW Werkzeugmaschinen GmbH, which generally have been equipping their machines with m&h probes for many years if customers order a machine with a probe. Many customers have reported good experiences over the years, which not least can be seen in repeat orders of the machines, specifically those with m&h probes. “The handling is easy and the devices are just great,” Roland Ziegler also confirms his good operational experience.
Because we produce individual parts and small series, the probes are used very often by us - and that since many years without any problems.Right from the beginning, m&h used the protected industrial radio band at 433 MHz with 64 selectable channels in its radio wave touch probes. Constantly improving electronics ensure high transmission and reception performance in order to provide secure data transmission and to prevent unnecessary machine downtimes even under extreme conditions. Even measuring within the workpieces is possible with this powerful technology. The security of signal transmission is the most important control variable for accuracy and reliability on the machines to avoid unscheduled stoppages or even damage. Especially with large workpieces or the tilting of multiple-axis heads, shading of the direct signal line can occur, which, however has no effect if a powerful wireless technology, such as the m&h, is used.
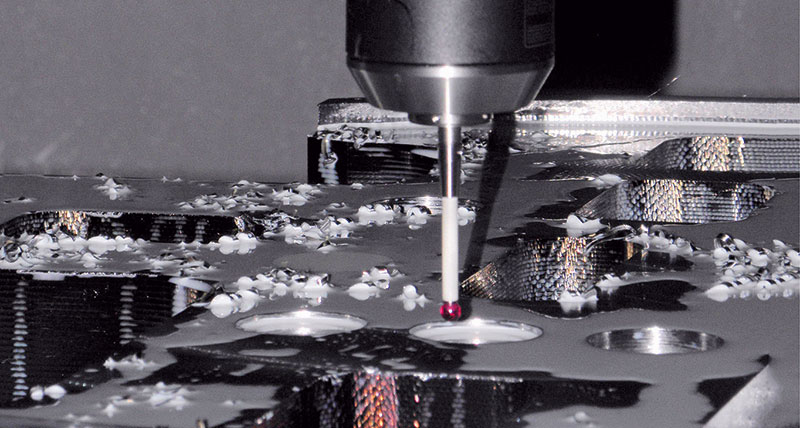
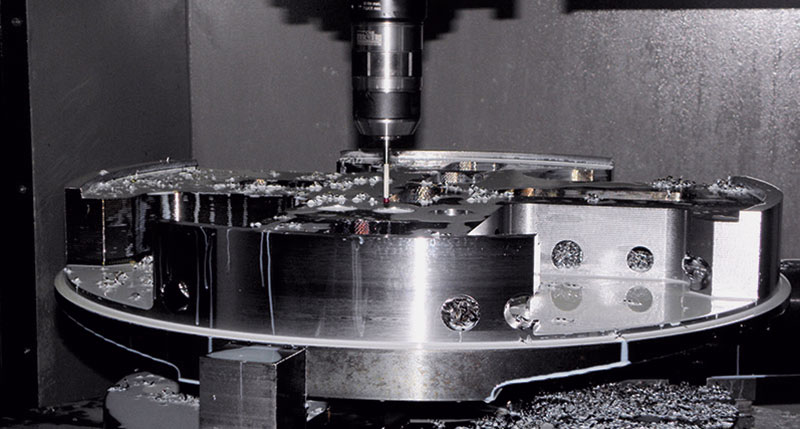