Simufact Welding
Special weld structure software for virtual tests and process design for the optimisation of assemblies
Welding Process Simulation Software
Robustly simulate complex multi-station fixturing and assembly of complex assemblies with hundreds of joints. Perform a “virtual tryout” before the first part is fabricated.
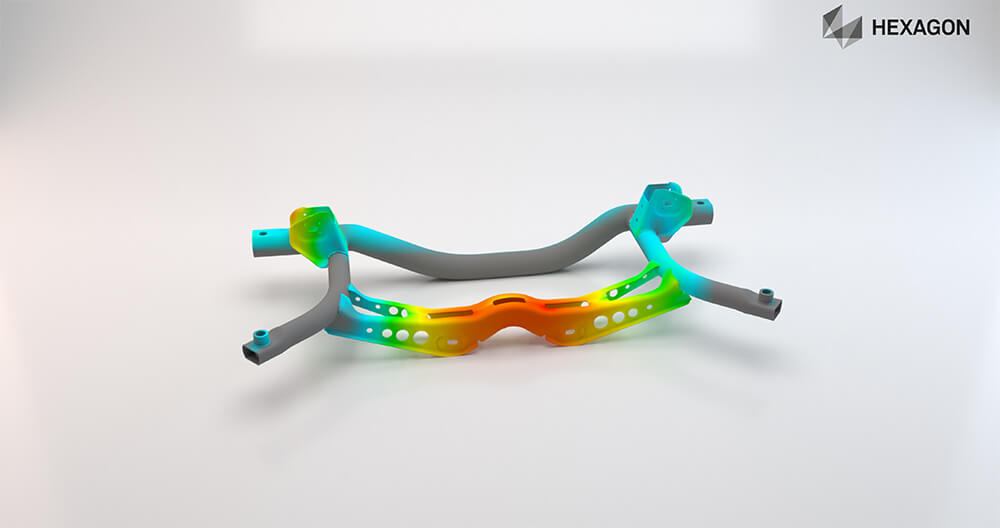
Software solution for welding processes without CAE expert knowledge
Simufact Welding is used to model and optimise a variety of thermal joining processes, taking into account the welding sequence and fixture.
One of the biggest challenges in welding is the thermal deformations or residual stresses of the entire assembly that occur after a non-optimised welding and clamping process. As a result, subsequent assembly processes cannot be easily performed because the geometry of the sub-assembly is out of tolerance. With Simufact Welding, the welding process and parameters can be optimised to achieve the desired product quality.
Exactly the right welding process you need
With the Arc Welding module common arc welding processes are simulated. Residual Stress, strain and distortion as caused by the welding process are predicted. This enables an improved quality and dimensional control.
Simufact Welding allows to evaluate the impact of vaious parameters, like: weld sequence, arc welding process parameters and fixturing strategy.
Multiple weld robots can be configured. Weld fillets are modelled very easily using the internal fillet generator.
Simufact Weldiing makes use of a comprehensive material database that can be extended by the user.

Laser- and Electron Beam Welding processes are simulated to predict the local distribution of residual stress, strain and distortion.
Simufact Welding takes into account the specifics of a Laser or Electron Beam heat source. This complements the extensive capabilities that are offered for simulating arc welding processes and enables an accurate prediction of any physical Laser and Beam welding process.

With Simufact Welding, Resistance Spot Welding processes are simulated with a high accuracy. The impact of multiple parameters like spot sequence, welding process parameters (force, current, time) and fixturing/clamping strategy on the weld structure is predicted.
The flexible configuration of the simulation in different modes (thermomechanical, mechanical with electrode movement and simplified) enables a fast simulation for complex assemblies.

Simufact Welding enables the quick and efficient setup of robust laser metal deposition (DED) models in order to calculate and evaluate for stress, strain, distortion, thermal history, and hot spots during manufacturing and post processing.
Common robot programming such as the G-Code can be utilized - This allows users to simply import existing tool paths instead of defining weld paths manually.

Brazing is a thermal process that applies hot soldering material to join parts. The Simufact Welding Brazing module takes care of the specifics of this process: the heat input for example is limited to the soldering material only - the soldering material itself is modelled by fillets.
Brazing simulations can be defined using both conventional and beam heat sources, or a combination of them.

Virtual Clamping enables to predict the exact geometry for parts and assembled structures. Simufact Welding simulates the behavior of parts as they are clamped and welded in their designated (for example: vehicle) coordinates - This dramatically reduces the need for prototypes or tryouts.
Stress relieving reduces residual stresses in the assembly after welding. Usually the application of this heat treatment method involves controlled heating of the assembly, a certain holding period at elevated temperature as well as controlled cooling - The simulation enables virtual tryout to achieve the best possible heat treatment process

Features in Simufact Welding
Your benefits with Simufact Welding

Design and optimise your welding process:
- Determine the optimal weld sequence and parameters, as well as clamping and unclamping concepts, to minimise thermal distortions and residual stresses and ensure a robust welding process.
- Identify and eliminate potential welding defects, such as hot cracks.
- Investigate material behavior during welding, such as phase transformation.

Simplicity – No CAE expert knowledge required as the software solution is designed to be user-friendly, intuitive and process-oriented.

Sustainability – Save material, time and money by replacing expensive and time-consuming physical tests with virtual tests.
Flyers & Brochures
Case Studies
Related Articles
White Paper
Reducing costs through virtual simulation
Flyer
EV Battery Enclosure Manufacturing
You may be interested in...
Suite
Virtual Manufacturing
Product
Simufact Forming
Division
Manufacturing Intelligence division
Magazine