High-quality innenmeisterbock inspection for Audi e-tron
An Absolute Arm with laser scanner allows Audi Brussels to perform innenmeisterbock inspection more efficiently, reliably and quickly than ever
Contact us

The varied and eventful history of Audi Brussels extends back to 1948 and has witnessed a number of major milestones in the field of car manufacturing. Since 2018 the plant is synonymous with e-mobility, as production site of the Audi e-tron and e-tron Sportback, the brand’s first full-electric SUV range.
This plant’s location in the Belgian capital makes Audi the only major car manufacturer with a production location in the heart of Europe. Close to important European institutions, the Brussels C02-neutral site offers ideal conditions for the production of the e-tron. Audi’s success factors in Brussels are the highly qualified and experienced workforce, easy access to highways and rail transport, and good relations with the institutions based in the city. Audi Brussels is actively involved in dialogue with international, national and regional authorities to shape and discuss the future of mobility.
Audi is betting on the future of sustainable mobility and aims to sell about a million electric cars a year by the middle of the coming decade. That would reduce the CO2 footprint of their fleet by 30 percent over the entire lifecycle by 2025 and lead to complete CO2 neutrality by at the latest 2050. But Audi’s objectives are also to be “the most progressive premium brand with the best customer experience and to be the brand with the greatest appeal, fascinating customer-relevant innovations and breath-taking design.”
Quality assurance at AUDI AG focuses above all on the general client experience – customers should be able to experience quality with all their senses. This may concern even very small matters, such as the need for fittings between the different components to be in complete harmony. Quality is very important to Audi buyers. This was the case ten years ago and has only increased since. At AUDI AG, guaranteeing quality happens across all departments, starting with the purchase of car components. Therefore, a good relationship with suppliers is important for developing new processes that can improve quality in the long run.
“In our quality department, we bring the parts of the car, along with the concept of mounting them, to a quality standard where they are ready for series production”, explains Dries Daniels, Audi e-tron Brussels Coordinator Innenmeisterbock. “We work in close cooperation with our suppliers who deliver samples already considered to be build-quality. The quality department verifies this, asks for changes to increase stability, and we offer feedback to the suppliers on how their parts are working in coordination with the parts of other suppliers. We define shared working points and assign responsibilities to solve the issues we find.”
The Belgian plant, as well as the majority of the other Volkswagen-group factories in world, has been a user of Hexagon products for many decades. The Brussels quality department uses a DEA Bravo, DEA Taifun (oldest system but still functioning), an old ROMER portable measuring arm with an HP-L laser scanner and, most recently acquired, a current generation Absolute Arm with a flagship blue-light laser scanner.
“We are working in an enclosed space, both in jobs in the innenmeisterbock and in tasks where we analyse finished customer cars”, explains Daniels. “We want the checks to be as good as possible right at the beginning, and we want them to have as little influence on the final results as possible. The parts we are checking should be like a natural build-up – as close as what we are going to get in series but controlled to be able to ensure that what we do here is also relevant for our series.”
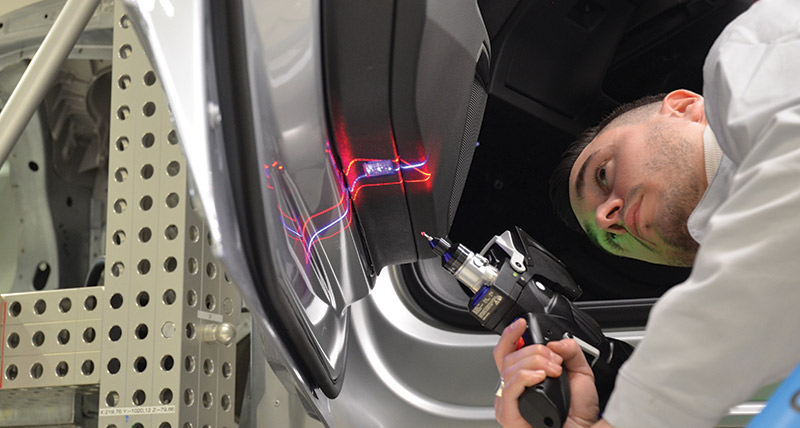
“The Absolute Arm allows us not only to inspect the whole inner car, but can also easily scan high-gloss black surfaces. And modern cars have quite a lot of them! Using a spray for example was not an option as it’s not the most pleasant working environment for our team.”
At the moment a few members of the team have trained to be expert users for both portable measuring arms. They quickly noticed how the new Absolute Arm is easy to use and no more switches close to the grip are necessary.
“It’s now more intuitive to work with the laser scanner”, says Daniels. “The large scan width was a real bonus – the quicker you can scan, the better! The small screen indicates which modes you are working in and gives you the option to quickly switch between different profiles without the need to run back to the laptop. All those improvements are real advantages and represent a considerable gaining of time.”
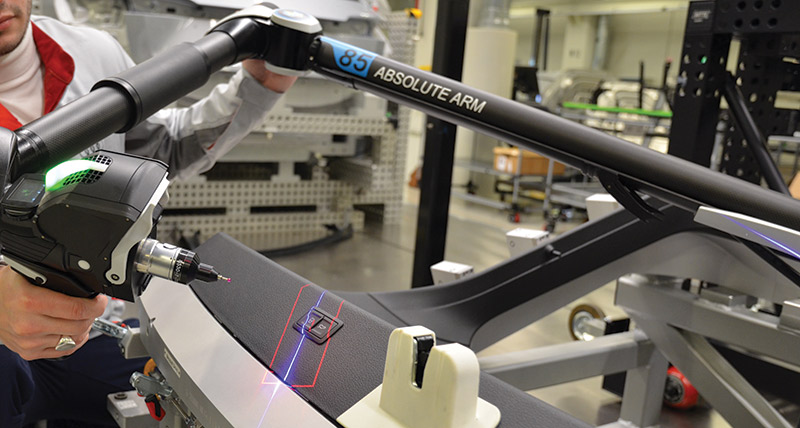
“We were able benefit from the excellent existing cooperation with Hexagon Belgium”, adds Thomas Marteau, Head of Department Meisterbock. “They offered us the test time we needed before the acquisition. This working relationship is very important for us.”
The replacement of the old CMM will be the next step for the quality team in Brussels. “The spare parts are slowly becoming an issue”, says Marteau. “We always need to look to the most recent technologies, especially for series measurement. Inline or at-line inspection are definitely on the agenda. Looking for the right accuracy, independent of any environment or circumstances is on our wish list. We are dreaming of a turnkey solution that everybody can use.”