Increased precision and speed in dimensional checks of L’Oréal bottles and capsules
The multisensor machine OPTIV M 3.2.2 equipped with pallet mode not only offers precise and automated dimensional measurements of L’Oréal caps and bottles, but also makes it possible to develop real packaging expertise on other analysis criteria such as deformation and bottle verticality
Contact us
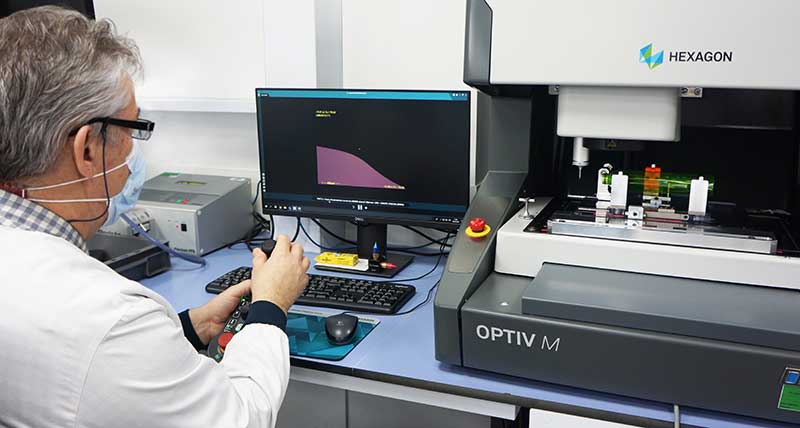
Founded in France in 1909, the L’Oréal Group is the world leader in the cosmetics industry. Dedicated to the beauty business, the Group has 88 000 employees worldwide. L’Oréal relies on its excellence in research and innovation and its 4100 researchers to meet all the world’s beauty aspirations. L’Oréal has made ambitious commitments to sustainable development by 2030, involving its entire ecosystem for a more inclusive and sustainable society.
With more than 10 000 employees at 44 production sites in charge of 36 international brands, L’Oréal France accounts for more than a quarter of the Group’s global production. The 240 people at the Rambouillet production site, near Paris, are responsible for the production of nearly 300 million units per year of haircare and skincare products such as shampoo, conditioner and shower products, including those for the Elsève and DOP brands.
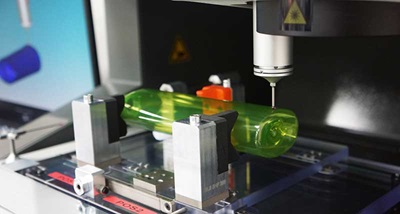
“My role consists, among other things, of ensuring that the design choices and the packaging equipment are appropriate. To do this, on the basis of the product definition, a formalised risk analysis is used to assess the impact of packaging developments on industrial equipment. We must therefore ensure the organisation, monitoring and support of the tests by synthesising the results that will make it possible to validate or reject the technical choice”, explains Mr Debreuille.
In other words, two quality systems coexist at L’Oréal: design quality (packaging) and conformity quality (production). Mr Debreuille navigates between the two. In design, he contributes to the product definition and industrial feasibility (testing) that he builds and carries out with the centralised Packaging and technical teams, making it possible or not to approve the new packaging item.
“We used to carry out dimensional measurements using manual tools, including electronic callipers. However, some measurements were very complex to carry out, especially those inside a capsule and even on a bottle,” recalls Mr Debreuille.
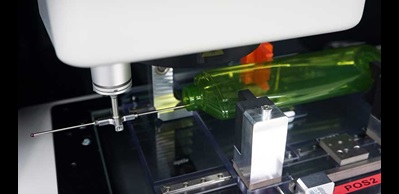
L’Oréal uses PC-DMIS CAD++ software coupled with the Inspect operator interface with pallet option and HERO analysis report software, all from Hexagon. “I have already been able to design around 20 PC-DMIS programs and train three laboratory technicians on the machine in analysis. I am discovering new possibilities every day and can be reassured to see our level of packaging expertise grow even more in the coming months,” concludes Mr Debreuille.
Partnership with Opus Solutions Techniques
Created by a group of experts in metrology, Opus Solutions Techniques specialises in the design of dimensional control solutions. Aware that making production more reliable is a major challenge for industrialists, Opus approaches work with skills that have been forged over time, but also with an attentive eye to changes and developments in manufacturing processes. Based near Lyon, Opus is a partner of Hexagon and actively participated in the automation project for L’Oréal. https://opus-st.com/
Some of the products covered in this case study have since been discontinued. Please visit [Multisensor and optical CMMs] and [PC-DMIS] for details of our current options in this product category.