High accuracy combined with flexible applications
Contact us
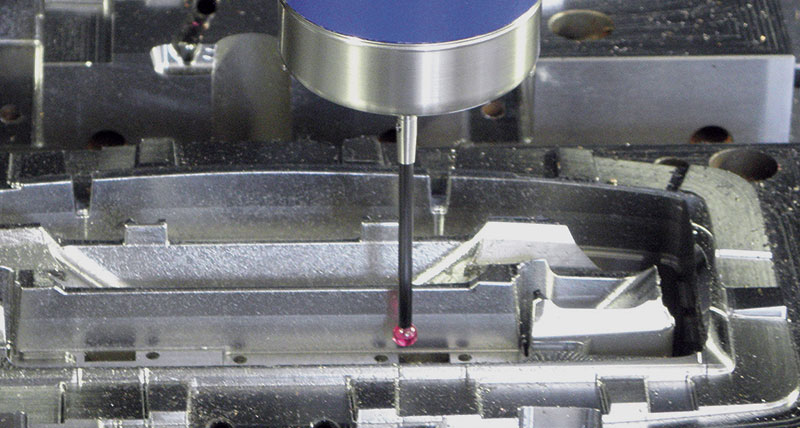
At Jochum, a mould manufacturer, tool length measurements and blade fracture checks are performed on a removable Tool Setter by m&h, even in unmanned shifts. The Tool Setter communicates with the control via the same infrared receiver as the probe.

For 25 years now, Volker Jochum has manufactured injection moulds of various kinds in his own company. These are, however, mostly highly complex and with many mechanical components, such as core pulls and slides. “Initially it was very difficult for us because we had to take on order for forms that no one else wanted,” Volker Jochum tells his story. “In hindsight this was very lucky, because we are now set up for complex things while simple shapes are often manufactured in Asia nowadays.”
Today, 32 employees manufacture single- and multicomponent injection moulds in ranging in size from 0.5 - 2 tons up to 3.5 tonnes of weight and dimensions of up to 1,200 x 1,000 x 600 mm. The client industries are wide-ranging, and include the automotive and construction industry, medical technology, electrical and electronics and even the furniture industry. With the new construction in 2012, there is now more space for precise work, for the now 11 CNC-controlled machining centres and for the increasing automation.
The tool designs are generally made in-house or at design offices which have been cooperating in a close and friendly way for a long time. This is an important factor for Jochum, since it is important to him that low maintenance and longevity are already taken into consideration as design principles in the construction of injection moulds. Experience has shown that the construction already significantly determines costs and efficiency of an injection mould as well as the smooth running of the process in the injection machine.
The entire team of mould construction evidently puts great emphasis on precision and clean work. “Many people are surprised that we have no spotting press,” Volker Jochum reports with a smile. “But everything just fits the way we make it.” The frequent use of the probe on the machines has a significant share in this. These are probes by m&h with infra-red data transmission. They have proven themselves in everyday use over many years. The employees praise their reliability and easy handling with the m&h equipment.
Therefore, when ordering machines, care has been taken for some time now to ensure the probes come from m&h.
Not least because the employees requested it, the 35.70 Tool Setter by m&h was purchased several months ago. In contrast to normal measuring cells or other Tool Setters, the m&h device is equipped with an infrared data transmission that communicates via the same receiver with the control as the m&h probe of the machine. This keeps investment costs low and simplifies the work. The special feature of this Tool Setter, however, is the possibility to simply remove it manually from its mounting surface. Just as quickly it can be put back manually in its place, where it is guided back to its place by a magnet and led by prisms with a precision of just a few microns. Because the magnet is located in the bottom of the Tool Setter, the low mounting plate in the machining area remains free from chips, so time-consuming cleaning is not needed.
The measuring cells, the Tool Setter and the probes by m&h have been working properly from the outset.When the 35.70 Tool Setter was developed by m&h, much thought was given to designing the unit to be as flexible as the customers have long been demanding. While other devices by the competition limit themselves to no longer requiring cables in the machining area, here the whole device was designed to be removable. That means there is no interference contour on the work table any more when changing workpieces or with large workpieces that need to be processed on the outside. This creates space in the machining area, and the set-up can be done faster. There are also no longer expensive collisions in which the Tool Setters can be seriously damaged. If the Tool Setter is then needed, it can be inserted again “in the blink of an eye” thanks to its clever design. “We do a brief calibration when we put the Tool Setter back in, but even when we don’t, the accuracy is within a few microns,” the Jochum staff report. “For us it is simply: quick calibration, measure and do the fitting.”
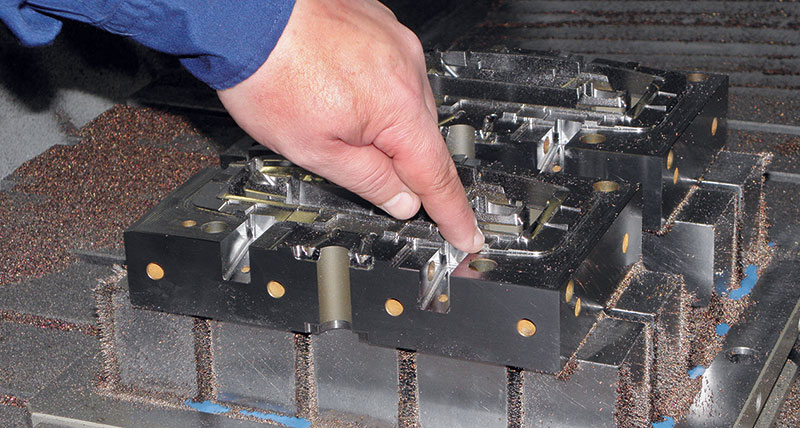
Not only does the m&h Tool Setter use the same receiver as the probe; it can also remain in the machining area when measurements are made with the probe. This fact is very much appreciated at Jochum. It ensures process reliability even during the so-called ghost shift when the machine continues working without any operator. The Tool Setter is usually left in the machining area on the one machine that carries out the long-running programs at Jochum’s during the night. After the individual work processes, the blades of the critical tools are then checked for presence at the Tool Setter. This ensures that no consequential damage can occur in case of tool breakage or that expensive rejects are produced. Especially with milling cutters, cutter heads and drills, it can happen once in a while that a blade fails prematurely. As with all m&h products, the 35.70 Tool Setter is sturdily built and created to withstand the adverse conditions in the machine tool with permanent bombardment of flying chips and frequent, sustained coolant showers. The infra-red diodes of the Tool Setter by m&h are located behind tempered glass; this prevents interference from vapours and coolant, which would greatly reduce the transmission performance.
The infrared transmission of signals between receiver and Tool Setter or probe is based on the m&h HDR (High Data Rate) technology which has been tried and tested for years. This ensures no other light sources or other signals can interfere with communication.
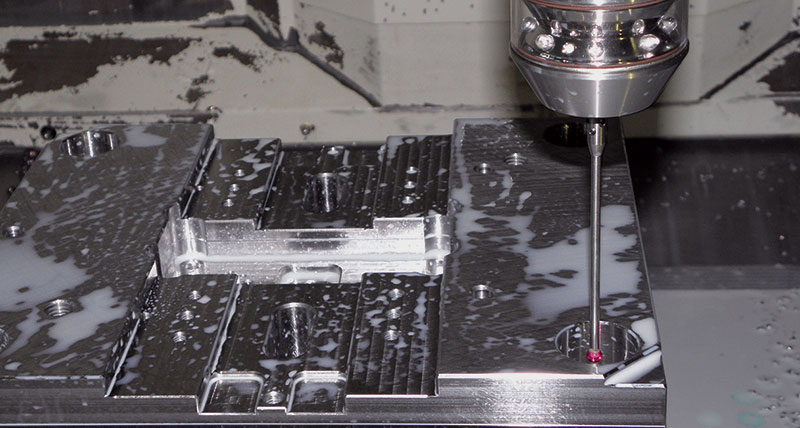
At Jochum, every tool is measured at the m&h Tool Setter when it is picked up by the machine. “And all this in a more accurate way than for laser tool setters by other manufacturers. We have checked this several times,” emphasize the employees. In general, everybody at Jochum is quite satisfied with the products and the service of m&h with its short response times. “The measuring cells, the Tool Setter and the probes by m&h have been working properly from the outset” Volker Jochum also confirms. “And if something is defective, we make a call and a replacement is there the next day.” The easy handling of all devices by m&h and the use of normal batteries which are available at any time are also praised.

For 25 years now, Volker Jochum has manufactured injection moulds of various kinds in his own company. These are, however, mostly highly complex and with many mechanical components, such as core pulls and slides. “Initially it was very difficult for us because we had to take on order for forms that no one else wanted,” Volker Jochum tells his story. “In hindsight this was very lucky, because we are now set up for complex things while simple shapes are often manufactured in Asia nowadays.”
Today, 32 employees manufacture single- and multicomponent injection moulds in ranging in size from 0.5 - 2 tons up to 3.5 tonnes of weight and dimensions of up to 1,200 x 1,000 x 600 mm. The client industries are wide-ranging, and include the automotive and construction industry, medical technology, electrical and electronics and even the furniture industry. With the new construction in 2012, there is now more space for precise work, for the now 11 CNC-controlled machining centres and for the increasing automation.
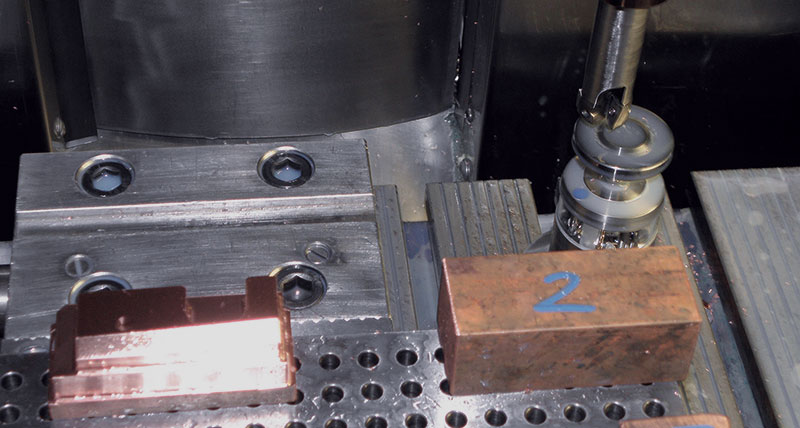
The entire team of mould construction evidently puts great emphasis on precision and clean work. “Many people are surprised that we have no spotting press,” Volker Jochum reports with a smile. “But everything just fits the way we make it.” The frequent use of the probe on the machines has a significant share in this. These are probes by m&h with infra-red data transmission. They have proven themselves in everyday use over many years. The employees praise their reliability and easy handling with the m&h equipment.
Therefore, when ordering machines, care has been taken for some time now to ensure the probes come from m&h.

The measuring cells, the Tool Setter and the probes by m&h have been working properly from the outset.When the 35.70 Tool Setter was developed by m&h, much thought was given to designing the unit to be as flexible as the customers have long been demanding. While other devices by the competition limit themselves to no longer requiring cables in the machining area, here the whole device was designed to be removable. That means there is no interference contour on the work table any more when changing workpieces or with large workpieces that need to be processed on the outside. This creates space in the machining area, and the set-up can be done faster. There are also no longer expensive collisions in which the Tool Setters can be seriously damaged. If the Tool Setter is then needed, it can be inserted again “in the blink of an eye” thanks to its clever design. “We do a brief calibration when we put the Tool Setter back in, but even when we don’t, the accuracy is within a few microns,” the Jochum staff report. “For us it is simply: quick calibration, measure and do the fitting.”
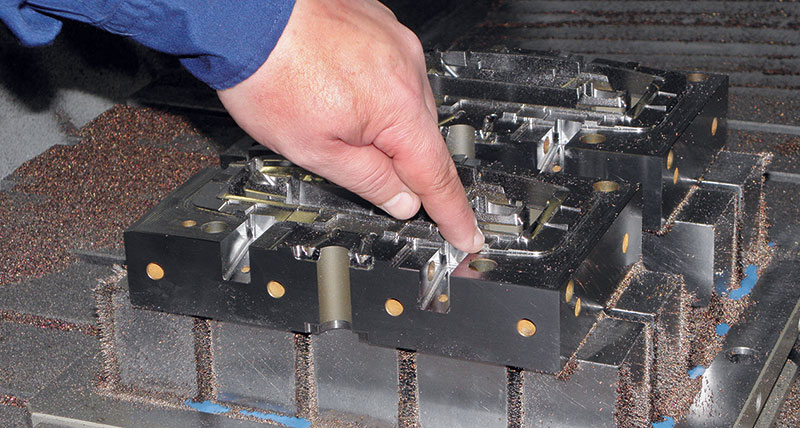
Not only does the m&h Tool Setter use the same receiver as the probe; it can also remain in the machining area when measurements are made with the probe. This fact is very much appreciated at Jochum. It ensures process reliability even during the so-called ghost shift when the machine continues working without any operator. The Tool Setter is usually left in the machining area on the one machine that carries out the long-running programs at Jochum’s during the night. After the individual work processes, the blades of the critical tools are then checked for presence at the Tool Setter. This ensures that no consequential damage can occur in case of tool breakage or that expensive rejects are produced. Especially with milling cutters, cutter heads and drills, it can happen once in a while that a blade fails prematurely. As with all m&h products, the 35.70 Tool Setter is sturdily built and created to withstand the adverse conditions in the machine tool with permanent bombardment of flying chips and frequent, sustained coolant showers. The infra-red diodes of the Tool Setter by m&h are located behind tempered glass; this prevents interference from vapours and coolant, which would greatly reduce the transmission performance.
The infrared transmission of signals between receiver and Tool Setter or probe is based on the m&h HDR (High Data Rate) technology which has been tried and tested for years. This ensures no other light sources or other signals can interfere with communication.
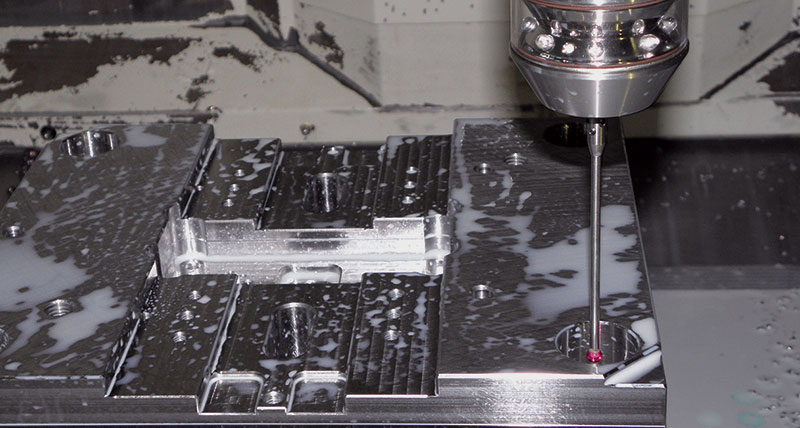
At Jochum, every tool is measured at the m&h Tool Setter when it is picked up by the machine. “And all this in a more accurate way than for laser tool setters by other manufacturers. We have checked this several times,” emphasize the employees. In general, everybody at Jochum is quite satisfied with the products and the service of m&h with its short response times. “The measuring cells, the Tool Setter and the probes by m&h have been working properly from the outset” Volker Jochum also confirms. “And if something is defective, we make a call and a replacement is there the next day.” The easy handling of all devices by m&h and the use of normal batteries which are available at any time are also praised.