Active production control
Contact us

Measuring the workpieces while they are still being clamped on the machine ensures process reliability even in automatic manufacturing cells. In this way, the mould construction and plastics specialist FKT saves reworking and thus smooths the production flow.
Technological innovation, reliable production processes as well as accuracy and adherence to schedules are major success factors in German mould construction and on the global market. This fact was recognized by FKT in Triptis, Thuringia (Germany). There they develop moulds and tools for injection moulding, pressure casting and overmoulding for metallic and non-metallic components.
These are usually multi-component moulds for up to three components. In addition to assembly injection technology, FKT are also experts with the LaserCusing process and with so-called MuCell technology.
In LaserCusing, metallic materials are constructed layer by layer, as they are for “Rapid Prototyping”, and fused with each other by the laser. This technology allows introducing freely moulded inner contours which cannot be manufactured any other way. These inner contours are used as close-to-contour tempering channels in injection and pressure-casting moulds, which allows short production cycles even with large injection volumes.
When using MuCell technology, the plastic is physically foamed within the mould. This permits controlled foaming by means of temperature and pressure which would not be possible with propellants. In this way, light-weight and low-torsion inner parts can be produced, which, as a rule, are then combined with further plastics or components in order to achieve the desired surface properties.
The resulting products made with FKT moulds are primarily used in the automotive industry, the electronics industry and communication technology as well as in electric appliances/ machine construction. In these industries, the demands for multi-component injection moulding are constantly increasing. Combinations of soft and hard plastics from one mould are also increasingly in demand. In addition, the so-called assembly injection is used more and more often. In this procedure, movable parts such as lamellae are injected directly into the carrier. It is therefore clear that the LaserCusing technology is often needed in order to provide the necessary cooling channels. At the same time, multi-component moulds place especially high demands on the accuracy of the individual moulded parts in the respective cavities.
This began in the past with the production of electrodes, which, at FKT, are produced in an automated manufacturing cell. This was the point of departure for software-controlled measuring using m&h devices within the machine. The Röders machining centre in the manufacturing cell is provided with measuring probes by m&h and Röders Inspect Software, which is based on the m&h software Form Inspect.
Soon after, further machining centres were equipped with probes and software by m&h. FKT is currently using up to six m&h Form Inspect software licenses in ten machining centres of differing size by different manufacturers, such as Röders, DMG and Makino.
Instead of unclamping the workpiece, measuring it with a measuring machine and then clamping it again, it is now measured directly while still in the machine tool‘s clamping setup. The CAD data of the workpiece is displayed as a surface model on a computer in the workshop. By mouse clicks or using data already defined in the drawing, any point or contour can be selected which is then assigned a measuring function by a mouse click. The 3-D Form Inspect software automatically calculates the necessary traverse paths of the measuring probes and, in the program background, creates measuring software for the machine in which the measuring is to take place. There the software is started like any standard machining program. The machine automatically positions the measuring probe and the current thermal displacement of the machine axes is measured with a quick calibration. The correction values thus determined are taken into account when the measuring data is evaluated. This procedure, which is patented by m&h, yields reliable measuring results which can be reproduced at any time and correspond to those of the measuring machine. The results are then displayed on the computer and can be printed out in different formats as a log or transmitted as a data set. The whole procedure only takes a few minutes. Then the operators can see at one glance if their workpieces are within the tolerance or not. In case of doubt, reworking can be done immediately and in the same clamping setup.
The initial critical response by the machine operators who were now required to carry out the measuring at the machine quickly turned into the opposite. „Now everyone can check and record that their workpiece is within the tolerance“, innovation assistant Maik Spangenberg reports. „It is possible to quickly measure and confirm important points and surfaces in the space.“ Handling the software is generally described as simple, and its introduction was carried out smoothly. By now, measuring with Form Inspect by m&h has become commonplace and an everyday means of reducing the workload. „This gives us security within the whole company“, Klaus Dietsch stressed.
When asked about the time needed for measuring on the machine, Klaus Dietsch explained his experiences: „The security and stability of production is more important than the production time per workpiece“, he explained. „If the results are outside the tolerance, the effort ends up being several times higher, which most of all means losing a lot of time“, he said, referring to the consequences. Whenever a workpiece has to be clamped again, the result is loss of time as well as reduced accuracy. The workpiece often has to be produced again from scratch. This reworking effort can largely be saved now at FKT. Even though Klaus Dietsch is not able or willing to express the gains achieved by measuring on the machine in numbers, it remains undisputed that it is a significant improvement for the production flow. It is, after all, now possible to know in advance that the parts meet the required accuracy and will subsequently fit. These are important aspects not only for multiple cavities, sliders and multi-component moulds. These shapes are increasingly complex and have sealing levels in all three spatial dimensions. Nowadays, the milling is completed to measure zero, which often can only be ensured by measuring before finishing. When a part had to be produced again from scratch, this always upset the schedule for other products. „Reworking has been significantly reduced“, Klaus Dietsch confirms, „and we also have a considerably smoother production flow. “ After all, besides product quality and longevity, adherence to schedules is also an important criterion for the customers.
Technological innovation, reliable production processes as well as accuracy and adherence to schedules are major success factors in German mould construction and on the global market. This fact was recognized by FKT in Triptis, Thuringia (Germany). There they develop moulds and tools for injection moulding, pressure casting and overmoulding for metallic and non-metallic components.
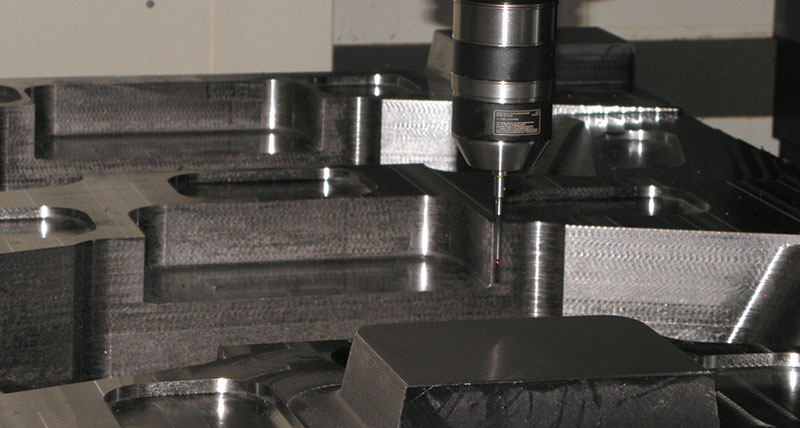
In LaserCusing, metallic materials are constructed layer by layer, as they are for “Rapid Prototyping”, and fused with each other by the laser. This technology allows introducing freely moulded inner contours which cannot be manufactured any other way. These inner contours are used as close-to-contour tempering channels in injection and pressure-casting moulds, which allows short production cycles even with large injection volumes.
When using MuCell technology, the plastic is physically foamed within the mould. This permits controlled foaming by means of temperature and pressure which would not be possible with propellants. In this way, light-weight and low-torsion inner parts can be produced, which, as a rule, are then combined with further plastics or components in order to achieve the desired surface properties.
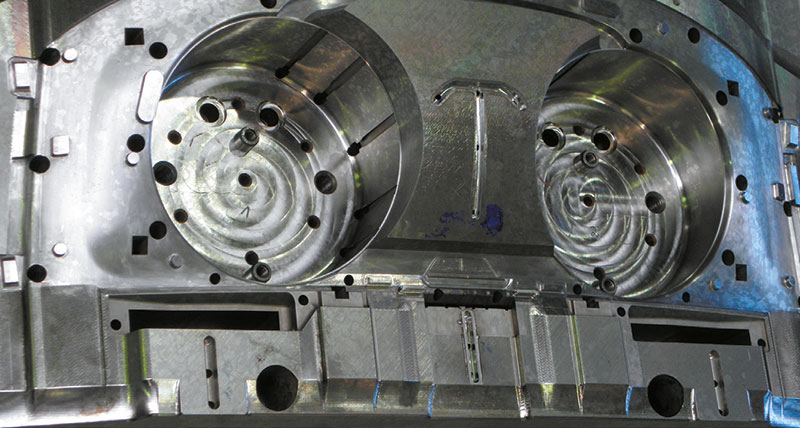
This began in the past with the production of electrodes, which, at FKT, are produced in an automated manufacturing cell. This was the point of departure for software-controlled measuring using m&h devices within the machine. The Röders machining centre in the manufacturing cell is provided with measuring probes by m&h and Röders Inspect Software, which is based on the m&h software Form Inspect.
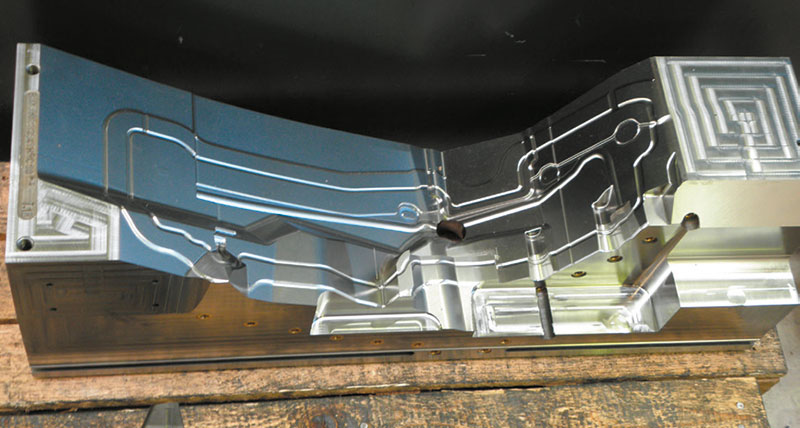
Instead of unclamping the workpiece, measuring it with a measuring machine and then clamping it again, it is now measured directly while still in the machine tool‘s clamping setup. The CAD data of the workpiece is displayed as a surface model on a computer in the workshop. By mouse clicks or using data already defined in the drawing, any point or contour can be selected which is then assigned a measuring function by a mouse click. The 3-D Form Inspect software automatically calculates the necessary traverse paths of the measuring probes and, in the program background, creates measuring software for the machine in which the measuring is to take place. There the software is started like any standard machining program. The machine automatically positions the measuring probe and the current thermal displacement of the machine axes is measured with a quick calibration. The correction values thus determined are taken into account when the measuring data is evaluated. This procedure, which is patented by m&h, yields reliable measuring results which can be reproduced at any time and correspond to those of the measuring machine. The results are then displayed on the computer and can be printed out in different formats as a log or transmitted as a data set. The whole procedure only takes a few minutes. Then the operators can see at one glance if their workpieces are within the tolerance or not. In case of doubt, reworking can be done immediately and in the same clamping setup.
"It can be truly said: this investment has paid off."
The initial critical response by the machine operators who were now required to carry out the measuring at the machine quickly turned into the opposite. „Now everyone can check and record that their workpiece is within the tolerance“, innovation assistant Maik Spangenberg reports. „It is possible to quickly measure and confirm important points and surfaces in the space.“ Handling the software is generally described as simple, and its introduction was carried out smoothly. By now, measuring with Form Inspect by m&h has become commonplace and an everyday means of reducing the workload. „This gives us security within the whole company“, Klaus Dietsch stressed.
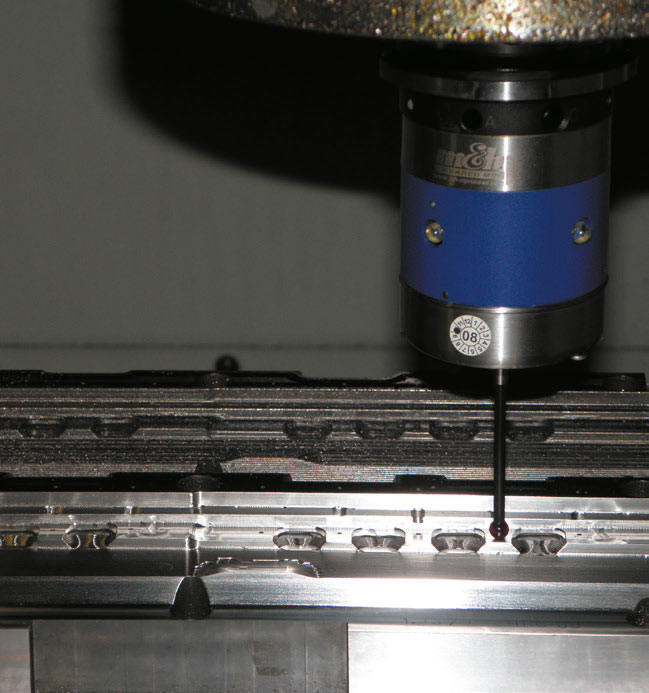