Aktive fertigungskontrolle
Kontakt

Technologische Innovation, verlässliche Fertigungsabläufe, sowie Genauigkeit und Termintreue sind die Erfolgsfaktoren für den deutschen Formenbau im weltweiten Wettbewerb. Das hat man auch bei FKT im thüringischen Triptis erkannt. Dort entwickelt man Formen und Werkzeuge für Spritzguss, Druckguss sowie Umspritzwerkzeuge für metallische und nichtmetallische Komponenten.
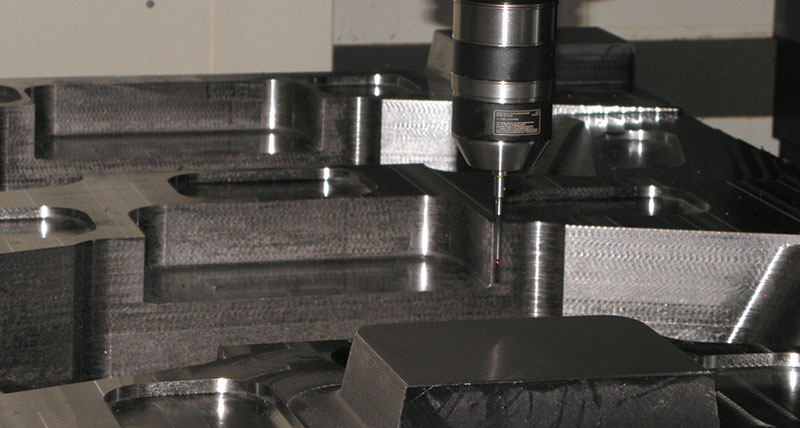
Beim Lasercusing werden metallische Werkstoffe ähnlich dem „Rapid-Prototyping“ schichtweise aufgebaut und durch den Laser miteinander verschmolzen. Diese Technik erlaubt frei geformte Innenkonturen einzubringen, die anders nicht zu fertigen sind. Diese Innenkoturen werden in Spritz- und Druckgussformen als kontur-nahe Temperierkanäle genutzt, was auch bei großen Spritzvolumen schnelle Fertigungszyklen erlaubt.
Bei der MuCell-Technik wird der Kunstsoff in der Form physikalisch geschäumt. Hierbei wird mit Temperatur und Druck ein kontrolliertes Schäumen erreicht, was mit Treibmitteln so nicht möglich wäre. So können leichte und verzugsarme Innenteile erzeugt werden, die in der Regel dann mit weiteren Kunststoffen oder Baugruppen kombiniert werden, um die gewünschten Oberflächeneigenschaften zu erhalten.
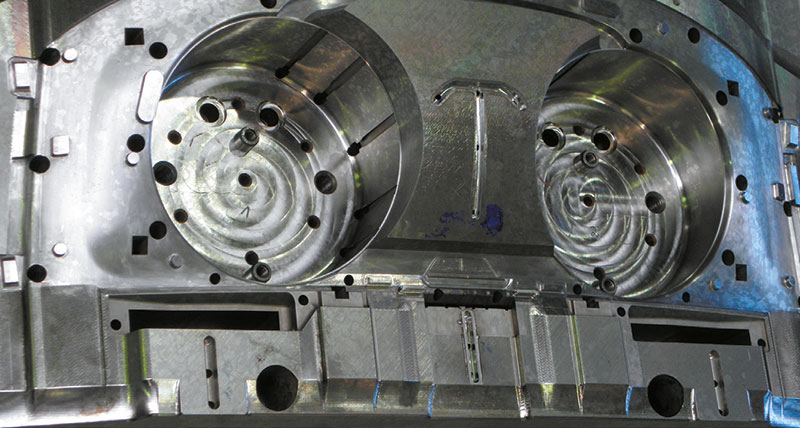
Dies begann damals bei der Fertigung von Elektroden, die man bei FKT in einer automatisierten Fertigungszelle herstellt. Sie war auch der Ausgangspunkt des programmgesteuerten Messens mit m&h in der Maschine. Das Bearbeitungszentrum von Röders in der Fertigungszelle ist mit Messtastern von m&h und der Röders Inspect Software ausgestattet, die auf der m&h Software Form Inspect basiert.
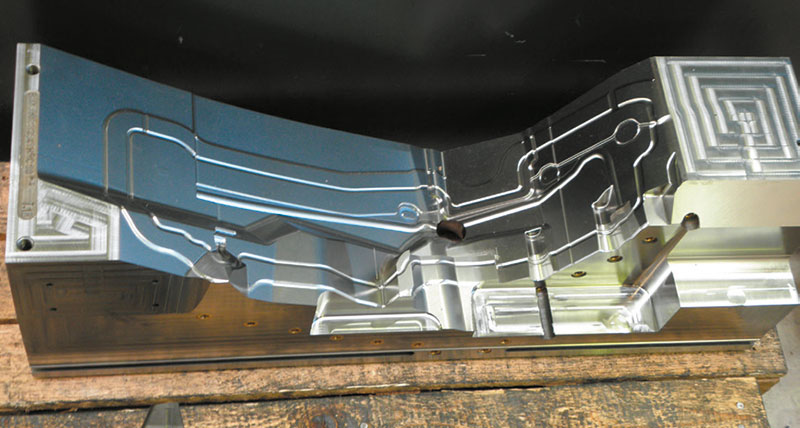
Statt abzurüsten und auf einer Messmaschine zu messen und dann wieder aufzuspannen, wird nun mit dem Messtaster direkt in der Aufspannung in der Werkzeugmaschine gemessen. Auf einem Com-puter in der Werkstatt werden die CAD-Daten des Werkstückes als Flächenmodell dargestellt. Mit Mausklicks oder in der Zeichnung bereits festgelegten Daten können beliebige Punkte und Konturen bestimmt werden, denen man per Mausklick eine Messfunktion zuordnet. Die Software 3D Form Inspect berechnet automatisch die notwendigen Verfahrwege der Messtaster und schreibt im Programmhintergrund ein Messprogramm für die jeweilige Maschine, auf der gemessen werden soll. Dort wird das Programm als normales Bearbeitungsprogramm aufgerufen. Die Maschine wechselt den Messtaster ein und eine ebenfalls automatisch generierte Kurzkalibrierung erfasst den aktuellen thermischen Versatz der Maschinenachsen. Die so ermittelten Korrekturwerte werden bei der Auswertung der Messdaten eingerechnet. Durch dieses für m&h patentierte Verfahren ergeben sich jederzeit wiederholbare und verlässliche Messergebnisse, die denen auf der Messmaschine entsprechen. Die Ergebnisse werden dann auf dem Computer sichtbar gemacht und können als Protokoll in verschiedenen Formaten ausgedruckt oder als Datensatz weitergegeben werden. Der gesamte Ablauf nimmt nur wenige Minuten in Anspruch. Dann erkennen die Bediener auf einen Blick, ob Ihre Werkstücke toleranzhaltig sind oder nicht. Im Zweifelsfall kann sofort und in gleicher Spannung maschinell nachgearbeitet werden.
"Man kann wirklich sagen: Diese Investition hat sich gelohnt."
Anfänglich kritische Stimmen der Maschinenbediener, denen
nun zusätzlich das Messen auf der Maschine abverlangt
wurde, kehrten sich sehr schnell ins Gegenteil. „Jetzt kann
jeder selbst kontrollieren und protokollieren, dass sein
Werkstück stimmt“, schildert der Innovations-assistent
Maik Spangenberg. „Man kann kurz mal wichtige Punkte und
Flächen im Raum vermessen und bestätigen.“ Das Handling
der Software wird allenthalben als einfach beschrieben
und die Einführung verlief problemlos. Zwischenzeitlich ist
das Messen mit Form Inspect von m&h für jeden im Betrieb
selbstverständlich und tägliche Arbeitserleichterung
geworden. „Das gibt uns Sicherheit im ganzen Betrieb“
betont Klaus Dietsch.
Angesprochen auf die Minuten des Messens auf der Maschine
macht Klaus Dietsch seine Erfahrung deutlich: „Wichtiger
als die Stückfertigungszeit ist die Sicherheit und die Stabilität
der Produktion“, erläutert er. „Wenn es nicht stimmt, ist
später der Aufwand um ein Vielfaches höher und bedeutet
vor allem viel verlorene Zeit“, zeigt er die Konsequenzen auf.
Immer wenn ein Teil noch einmal aufgenommen werden
muss, geht dies mit Zeitverlust und Einbußen in der Genauigkeit
einher. Oftmals muss komplett neu gefertigt werden.
Diese Nacharbeiten erspart man sich nun im Hause FKT
zu großen Teilen. Zwar kann, oder will, Klaus Dietsch den
Gewinn durch das Messen auf der Maschine nicht in Zahlen
ausdrücken, dass es aber ein klarer Gewinn für den Fertigungsdurchlauf
ist, bleibt unbestritten. Schließlich sieht man nun schon vorher, dass die Teile in der geforderten
Genauigkeit sind und nachher passen. Das sind wichtige
Aspekte nicht nur bei Mehrfachkavitäten, Schiebern und
Mehrkomponentenformen. Die Formen sind zunehmend
komplexer gestaltet und haben Dichtebenen in allen drei
Dimensionen des Raums. Diese werden heute auf Nullmaß
fertig gefräst, was oft nur durch messen vor dem Schlichten
zu gewährleisten ist. Wenn man früher neu fertigen musste,
hat das ja immer auch den Zeitplan für andere Produkte
durcheinander gebracht. „Die Nacharbeit ist deutlich rückläufig“,
bestätigt Klaus Dietsch, „und wir haben eine wesentliche
Beruhigung im Durchlauf.“ Schlussendlich ist neben der
Produktqualität und Langlebigkeit auch die Termintreue ein
wichtiges Kriterium für die Kunden.