Controllo attivo della produzione
Contattateci

La misurazione dei pezzi quando questi sono
ancora serrati sulla macchina garantisce la
sicurezza di processo, anche nelle celle di
produzione automatiche. Con un tale metodo
l‘azienda FKT, specializzata nella realizzazione
di stampi e lavorazione di materie plastiche,
non deve eseguire lavori di rifinitura e può
così semplificare il processo di produzione
Innovazione tecnologica, processi di produzione affidabili, così come precisione e puntualità nelle consegne sono i fattori che contribuiscono al successo delle aziende tedesche specializzate nella realizzazione di stampi nel confronto con la concorrenza internazionale. Un tale successo va riconosciuto anche all‘azienda FKT con sede a Triptis nella regione della Turingia.
Qui si sviluppano stampi e utensili per lo stampaggio ad
iniezione, la pressofusione, così come utensili per il rivestimento
mediante stampaggio ad iniezione per componenti
metallici e non metallici. Nella maggior parte dei casi si
tratta di stampi per multicomponenti, fino ad un numero di
3. Accanto alla tecnologia dello stampaggio a iniezione per
l‘assemblaggio, FKT è specializzata anche nel processo
Laser Cusing e nella cosiddetta tecnologia MuCell.
Nel LaserCusing, processo simile alla „prototipazione rapida“, i materiali metallici vengono fusi a strati mediante laser. Questa tecnica consente di realizzare contorni interni da modellare liberamente non realizzabili in altro modo. Questi contorni vengono utilizzati nello stampaggio ad iniezione e pressofusione come canali di termoregolazione e sono posizionati molto vicino al contorno stampo, permettendo così un‘esecuzione rapida dei cicli di lavorazione anche in presenza di grandi volumi.
Con la tecnica MuCell il materiale plastico viene schiumato fisicamente nello stampo. Per mezzo della temperatura e della pressione si ottiene una schiuma controllata, altrimenti non ottenibile per mezzo dei normali agenti schiumogeni. Grazie a tale tecnica possono essere realizzate parti interne leggere e con poche deformazioni, in combinazione con altri materiali plastici o componenti per ottenere le caratteristiche di superficie desiderate.
I prodotti finiti, realizzati con gli stampi prodotti da FKT,
vengono poi impiegati per la maggior parte nell‘industria
automobilistica, elettronica e nella tecnica delle comunicazioni,
come anche nell‘industria meccanica e nella costruzione
di apparecchi elettrici. In questi settori aumentano in
modo esponenziale le richieste per lo stampaggio a iniezione
di multicomponenti. Allo stesso modo si moltiplicano le
richieste di stampi in cui è possibile combinare materie
plastiche morbide e dure. Anche il cosiddetto stampaggio
a iniezione di assemblaggio trova un impiego sempre più
frequente. Grazie a tale processo, parti mobili, come ad
esempio lamelle, possono essere stampate a iniezione
direttamente nel corpo portante. È dunque comprensibile
che la tecnica LaserCusing sia spesso utilizzata per
garantire la presenza di canali di raffreddamento adeguati.
Contemporaneamente, gli stampi per multicomponenti in
particolare soddisfano requisiti oltremodo elevati per
quanto riguarda la precisione delle singole parti dello
stampo nelle rispettive cavità.
Tutto è cominciato quando FKT ha avviato la produzione di elettrodi e ha utilizzato una cella di produzione automatizzata. Tale cella è stata anche il punto di partenza nella misurazione controllata da programma m&h nella macchina. Il centro di lavoro di Röders nella cella di produzione è dotato di tastatori m&h e del software Inspect Röders, che si basa sul software Form Inspect m&h.
Ben presto altri centri di lavoro sono stati dotati di tastatori
e software m&h. Nel frattempo si lavora con 6 licenze
software Form Inspect m&h per 10 centri di lavoro di
differenti produttori e dimensioni da Röders a DMG fino
a Makino.
Invece di disattrezzare per poi misurare su una macchina di misura e alla fine della misurazione eseguire di nuovo il serraggio, si procede ora alla misurazione con il tastatore direttamente nel serraggio della macchina utensile. Su un computer presente nell‘officina vengono rappresentati i dati CAD del pezzo come modello di superficie. Cliccando con il mouse o nei dati fissati già nel disegno si possono definire punti e contorni a piacere a cui viene assegnata una funzione di misura per mezzo del clic del mouse. Il software 3 D Form Inspect calcola automaticamente i necessari percorsi di traslazione dei tastatori e scrive nel programma in background un programma di misura per la rispettiva macchina, su cui deve essere eseguita la misurazione. Tale programma viene richiamato come normale programma di lavorazione. La macchina scambia il tastatore e una calibrazione breve, anche questa automatica, rileva lo spostamento termico attuale degli assi di macchina. I valori di correzione così acquisiti vengono inclusi nella valutazione dei dati di misurazione. Grazie a questo procedimento brevettato per m&h, si ottengono in ogni momento risultati di misurazione ripetibili e affidabili che corrispondono a quelli che si possono ottenere con la macchina di misura. I risultati vengono poi visualizzati sul computer e possono essere stampati come protocollo in diversi formati oppure trasmessi come record di dati. Tutto il processo richiede solo pochi minuti. A questo punto l‘operatore riconosce subito se i pezzi sono entro le tolleranze ammesse oppure no. In caso di dubbio può eseguire subito a macchina i lavori di rifinitura nello stesso serraggio.
Le critiche iniziali degli operatori di macchina, a cui tocca ora anche il compito di misurare sulla macchina, si sono rapidamente trasformate in una valutazione positiva. „Ognuno è ora in grado di controllare e protocollare personalmente se il proprio pezzo è in ordine“, afferma l‘assistente addetto all‘innovazione Maik Spangenberg. „Si possono misurare e confermare velocemente punti e superfici importanti nello spazio“. L‘uso del software viene descritto da tutti come semplice e la sua introduzione è avvenuta senza problemi. Nel frattempo la misurazione con Form Inspect di m&h è diventata per tutti in azienda una cosa ovvia e una semplificazione del lavoro quotidiano. „Ci offre sicurezza in tutto il processo di produzione“ sottolinea Klaus Dietsch.
Alla domanda sulla durata in minuti della misurazione sulla
macchina Klaus Dietsch osserva a partire dalla sua esperienza:
„Più importante del tempo di produzione del pezzo è
la sicurezza e la stabilità della produzione“.
E poi trae le conseguenze: „Se il risultato non è preciso,
il dispendio di energie che ne consegue è molto più grande e ciò comporta soprattutto una grande perdita di tempo“.
Sempre quando un pezzo deve essere di nuovo inserito nel
processo di produzione, si è confrontati con una perdita di
tempo e di precisione. Spesso il pezzo deve essere prodotto
completamente da nuovo. Con la nuova tecnologia l‘azienda
FKT non deve quasi più eseguire questi lavori di rifinitura.
Klaus Dietsch non è in grado o non vuole descrivere in
cifre il guadagno che ne deriva per l‘azienda se si esegue la
misurazione direttamente sulla macchina, ma comunque
resta indiscusso che un tale procedimento sia un chiaro
guadagno per il processo di produzione. Dopo tutto si può
vedere già per tempo che i pezzi rispettano la precisione
richiesta e quindi sono adatti al ciclo di lavorazione. Questi
sono aspetti importanti non solo per le multicavità, le guide
scorrevoli e gli stampi per multicomponenti. Gli stampi
hanno una forma sempre più complessa e piani di tenuta
in tutte e tre le dimensioni spaziali. Tali stampi vengono
prodotti tramite fresatura a dimensione zero, che spesso è
garantita solo dalla misurazione prima della finitura.
Quando una volta si doveva produrre da nuovo, si correva
sempre il rischio di non rispettare i tempi di produzione degli
altri prodotti. „Il lavoro di rifinitura è chiaramente diminuito“,
conferma Klaus Dietsch, „ e il processo di produzione
avviene con meno interruzioni e disturbi“. D‘altronde
accanto alla qualità del prodotto e alla sua durata,
un altro importante criterio per i clienti è la puntualità
nelle consegne.
Innovazione tecnologica, processi di produzione affidabili, così come precisione e puntualità nelle consegne sono i fattori che contribuiscono al successo delle aziende tedesche specializzate nella realizzazione di stampi nel confronto con la concorrenza internazionale. Un tale successo va riconosciuto anche all‘azienda FKT con sede a Triptis nella regione della Turingia.
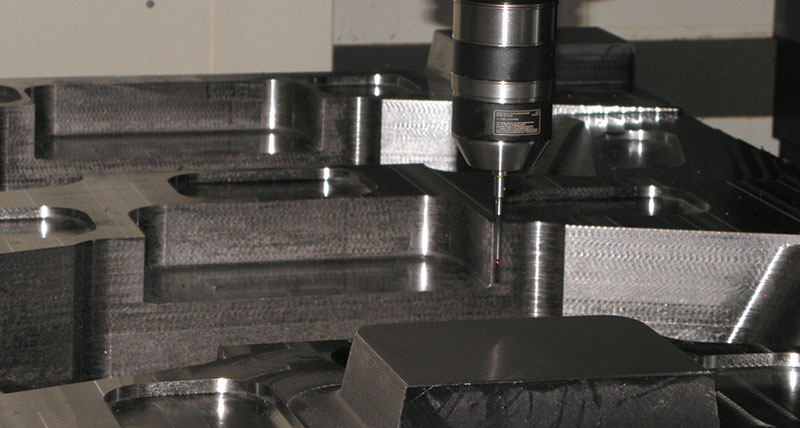
Nel LaserCusing, processo simile alla „prototipazione rapida“, i materiali metallici vengono fusi a strati mediante laser. Questa tecnica consente di realizzare contorni interni da modellare liberamente non realizzabili in altro modo. Questi contorni vengono utilizzati nello stampaggio ad iniezione e pressofusione come canali di termoregolazione e sono posizionati molto vicino al contorno stampo, permettendo così un‘esecuzione rapida dei cicli di lavorazione anche in presenza di grandi volumi.
Con la tecnica MuCell il materiale plastico viene schiumato fisicamente nello stampo. Per mezzo della temperatura e della pressione si ottiene una schiuma controllata, altrimenti non ottenibile per mezzo dei normali agenti schiumogeni. Grazie a tale tecnica possono essere realizzate parti interne leggere e con poche deformazioni, in combinazione con altri materiali plastici o componenti per ottenere le caratteristiche di superficie desiderate.
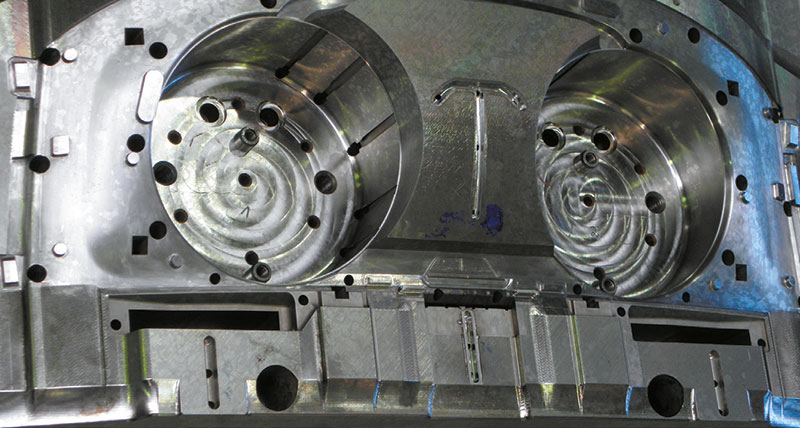
Tutto è cominciato quando FKT ha avviato la produzione di elettrodi e ha utilizzato una cella di produzione automatizzata. Tale cella è stata anche il punto di partenza nella misurazione controllata da programma m&h nella macchina. Il centro di lavoro di Röders nella cella di produzione è dotato di tastatori m&h e del software Inspect Röders, che si basa sul software Form Inspect m&h.
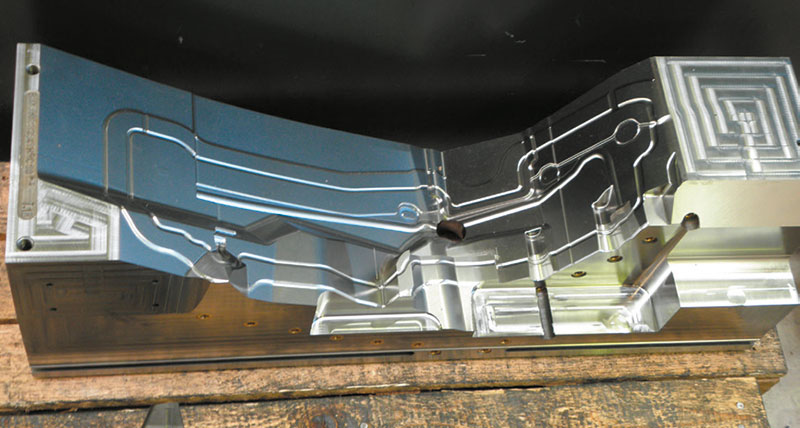
Invece di disattrezzare per poi misurare su una macchina di misura e alla fine della misurazione eseguire di nuovo il serraggio, si procede ora alla misurazione con il tastatore direttamente nel serraggio della macchina utensile. Su un computer presente nell‘officina vengono rappresentati i dati CAD del pezzo come modello di superficie. Cliccando con il mouse o nei dati fissati già nel disegno si possono definire punti e contorni a piacere a cui viene assegnata una funzione di misura per mezzo del clic del mouse. Il software 3 D Form Inspect calcola automaticamente i necessari percorsi di traslazione dei tastatori e scrive nel programma in background un programma di misura per la rispettiva macchina, su cui deve essere eseguita la misurazione. Tale programma viene richiamato come normale programma di lavorazione. La macchina scambia il tastatore e una calibrazione breve, anche questa automatica, rileva lo spostamento termico attuale degli assi di macchina. I valori di correzione così acquisiti vengono inclusi nella valutazione dei dati di misurazione. Grazie a questo procedimento brevettato per m&h, si ottengono in ogni momento risultati di misurazione ripetibili e affidabili che corrispondono a quelli che si possono ottenere con la macchina di misura. I risultati vengono poi visualizzati sul computer e possono essere stampati come protocollo in diversi formati oppure trasmessi come record di dati. Tutto il processo richiede solo pochi minuti. A questo punto l‘operatore riconosce subito se i pezzi sono entro le tolleranze ammesse oppure no. In caso di dubbio può eseguire subito a macchina i lavori di rifinitura nello stesso serraggio.
"Si può veramente affermare: è valsa la pena fare questo investimento."
Le critiche iniziali degli operatori di macchina, a cui tocca ora anche il compito di misurare sulla macchina, si sono rapidamente trasformate in una valutazione positiva. „Ognuno è ora in grado di controllare e protocollare personalmente se il proprio pezzo è in ordine“, afferma l‘assistente addetto all‘innovazione Maik Spangenberg. „Si possono misurare e confermare velocemente punti e superfici importanti nello spazio“. L‘uso del software viene descritto da tutti come semplice e la sua introduzione è avvenuta senza problemi. Nel frattempo la misurazione con Form Inspect di m&h è diventata per tutti in azienda una cosa ovvia e una semplificazione del lavoro quotidiano. „Ci offre sicurezza in tutto il processo di produzione“ sottolinea Klaus Dietsch.
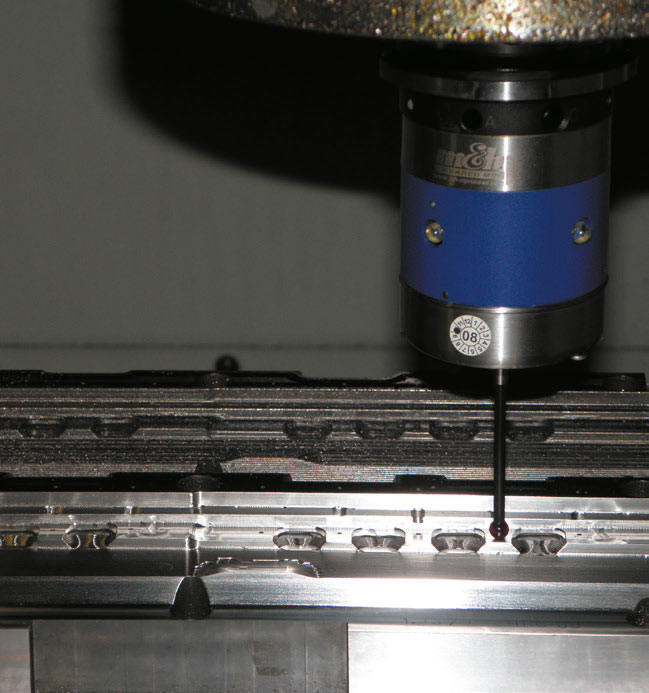