Control de fabricación activo
Contacto

La medición de piezas aún sujetas en la máquina
crea seguridad del proceso, también en células de
fabricación automatizadas. El especialista en
plásticos y en construcción de moldes FKT ahorra
así mecanizados ulteriores y estabiliza el ciclo de
fabricación.
La innovación tecnológica, los ciclos de fabricación fiables, así como la precisión y puntualidad, son los factores de éxito de la construcción alemana de moldes frente a la competencia mundial. Esto también se reconoció en FKT - Triptis (en la región de Turingia).
Allí se desarrollan moldes y herramientas para fundición
inyectada, fundición a presión, así como herramientas de
extrusión para componentes metálicos y no metálicos.
En la mayoría de los casos se trata de moldes de varios
componentes, para hasta tres componentes. Además de
la tecnología de moldeo por inyección en montaje, en la
empresa FKT también se domina el proceso Laser Cusing
y la llamada Tecnología MuCell.
En Lasercusing materiales metálicos se forman capa por capa similar al „Rapid-Prototyping“ y se funden uno con otro por medio del láser. Esta técnica permite introducir contornos interiores moldeados libremente, los cuales no pueden fabricarse de otra forma. Estos contornos interiores se utilizan en moldes de fundición inyectada y moldes de fundición a presión, como canales de temperado próximos al contorno, lo que también permite ciclos de fabricación rápidos en grandes volúmenes de inyección.
En la técnica MuCell el plástico se espuma físicamente en el molde. Aquí, con temperatura y presión se logra un espumado controlado, el cual no sería posible con agentes esponjantes. Así pueden elaborarse piezas interiores livianas y con baja deformación, que se combinan por lo general con otros plásticos o grupos constructivos para obtener las propiedades de superficie deseadas.
Los productos de los moldes de FKT se utilizan ante todo
en la industria automotriz, la industria electrónica y la
técnica de comunicaciones, así como en la construcción
de equipos eléctricos / maquinaria. En estos campos
aumentan continuamente las exigencias para el fundido
por inyección de varios componentes. Del mismo modo
se solicitan cada vez más combinaciones de plásticos
blandos y duros de un sólo molde. Igualmente la llamada
fundición de inyección en montaje se utiliza cada vez más.
En ello piezas móviles como por ejemplo laminillas se
inyectan directamente en el cuerpo de soporte. Así es
comprensible por que la técnica LaserCusing se necesita
frecuentemente para los canales de refrigeración correspondientes.
Al mismo tiempo los moldes de varios componentes
colocan altas exigencias a la precisión de las partes
de molde individuales en las respectivas cavidades.
Esto comenzó en aquel entonces con la fabricación de electrodos en la empresa FKT, en una celda de fabricación automatizada. Esto también fue el punto de partida de la medición controlada por programa con m&h en la máquina. El centro de mecanizado de Röders en la celda de fabricación está equipado con palpadores de medición de m&h y el software Röders Inspect, basado en el software m&h - Form Inspect.
Pronto se equiparon otros centros de mecanizado con los
palpadores y el software m&h. Mientras tanto se trabaja con 6 licencias del software m&h Form Inspect en 10
centros de mecanizado de diferentes fabricantes y
tamaños, desde Röders pasando por DMG hasta Makino.
En lugar de desmontar y medir en una máquina de medición, y luego volver a sujetar, ahora con el palpador de medición se mide directamente en la sujeción en la máquina herramienta. En un ordenador en el taller se representan los datos CAD de la pieza como modelo plano. Con clics del ratón, o con los datos ya especificados en el dibujo, pueden determinarse aleatoriamente puntos y contornos a los cuales se asigna con clic de ratón una función de medición. El software 3D Form Inspect calcula automáticamente los desplazamientos necesarios del palpador de medición y escribe en el programa de fondo un programa de medición para la máquina en que debe medirse. Allí el programa se llama como programa de mecanizado normal. La máquina cambia el palpador de medición, y un calibrado breve generado también de forma automática registra el offset térmico actual de los ejes de la máquina. Los valores de corrección así determinados se tienen en cuenta en la evaluación de los datos de medición. Por medio de este proceso, patentado por m&h, se obtienen en cualquier momento resultados de medición repetibles y fiables que corresponden con los de la máquina de medición. Los resultados se hacen visibles en el ordenador y pueden imprimirse como protocolo en diferentes formatos, o transmitirse como registro de datos. Todo el ciclo toma solamente unos pocos minutos. Entonces el operador reconoce de un vistazo si sus piezas mantienen o no las tolerancias. En caso de duda, puede inmediatamente y en la misma sujeción repasarse.
Las voces críticas en un comienzo de algunos operadores a los cuales se exigió la medición adicional en la máquina cambiaron de forma rápida. „Ahora cada uno puede controlar y protocolizar por si mismo que su pieza es correcta“, relata el Asistente de Innovación Maik Spangenberg. „Se puede medir y confirmar en el lugar, en un tiempo breve, puntos y superficies importantes“. En todas partes el uso del software se describe como sencillo y la introducción transcurrió sin problemas. Entre tanto, la medición con Form Inspect de m&h es natural en toda fábrica y se ha convertido en un alivio para el trabajo diario. „Esto nos ofrece seguridad en toda la empresa“ resalta Klaus Dietsch.
Respondiendo a los minutos de medición en la máquina,
Klaus Dietsch aclara su experiencia: „Más importante que
el tiempo de mecanizado de la pieza es la seguridad y
estabilidad de la producción“, aclara él. „Cuando esto no
es así, el trabajo ulterior es varias veces mayor y significa
ante todo mucho tiempo perdido“, indicando las consecuencias.
Siempre que una pieza debe tomarse de nuevo,
está acompañado de pérdida de tiempo y de precisión.
Muchas veces debe fabricarse de nuevo. Ahora en la
empresa FKT se omiten en gran parte estos trabajos
ulteriores. Por cierto, aunque Klaus Dietsch no puede o no desea
expresar en números la ganancia por medio de la medición
en la máquina, es indiscutible que es una ganancia clara
para el ciclo de fabricación. Por último, ahora se ve previamente
que las piezas cumplen la precisión exigida y después
sirven. Estos son aspectos importantes, no solamente en
cavidades múltiples, aletas y moldes de varios componentes.
Los moldes cada vez son de un diseño más complejo y tienen
planos de estanqueidad en todas las tres dimensiones del
espacio. Estos se fresan hoy día a „Medida cero“, lo cual
frecuentemente sólo es posible por medio de la medición
antes de la operación de acabado. Cuando antes debía
fabricarse de nuevo, siempre se desordenaba el cronograma
para otros productos. „El mecanizado ulterior ha descendido
claramente“, confirma Klaus Dietsch, „y nosotros tenemos
una estabilización considerable en el ciclo“. Finalmente,
además de la calidad y longevidad del producto, la puntualidad
es también un criterio importante para los clientes.
La innovación tecnológica, los ciclos de fabricación fiables, así como la precisión y puntualidad, son los factores de éxito de la construcción alemana de moldes frente a la competencia mundial. Esto también se reconoció en FKT - Triptis (en la región de Turingia).
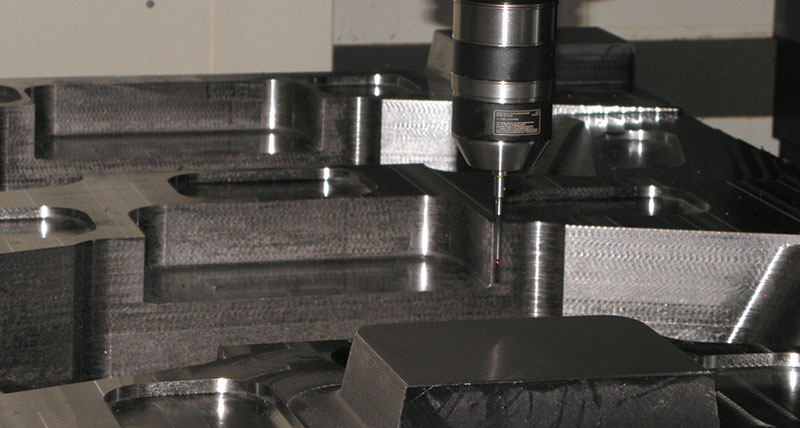
En Lasercusing materiales metálicos se forman capa por capa similar al „Rapid-Prototyping“ y se funden uno con otro por medio del láser. Esta técnica permite introducir contornos interiores moldeados libremente, los cuales no pueden fabricarse de otra forma. Estos contornos interiores se utilizan en moldes de fundición inyectada y moldes de fundición a presión, como canales de temperado próximos al contorno, lo que también permite ciclos de fabricación rápidos en grandes volúmenes de inyección.
En la técnica MuCell el plástico se espuma físicamente en el molde. Aquí, con temperatura y presión se logra un espumado controlado, el cual no sería posible con agentes esponjantes. Así pueden elaborarse piezas interiores livianas y con baja deformación, que se combinan por lo general con otros plásticos o grupos constructivos para obtener las propiedades de superficie deseadas.
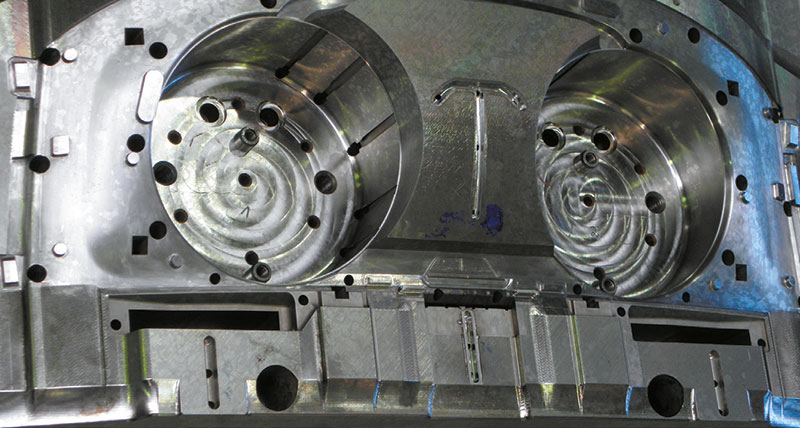
Esto comenzó en aquel entonces con la fabricación de electrodos en la empresa FKT, en una celda de fabricación automatizada. Esto también fue el punto de partida de la medición controlada por programa con m&h en la máquina. El centro de mecanizado de Röders en la celda de fabricación está equipado con palpadores de medición de m&h y el software Röders Inspect, basado en el software m&h - Form Inspect.
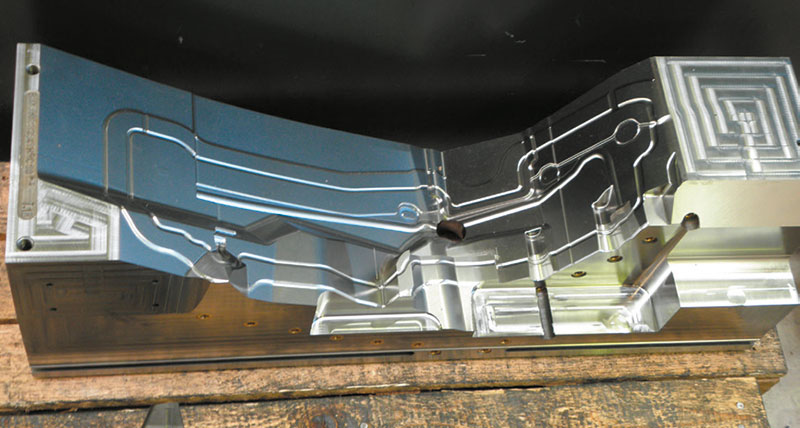
En lugar de desmontar y medir en una máquina de medición, y luego volver a sujetar, ahora con el palpador de medición se mide directamente en la sujeción en la máquina herramienta. En un ordenador en el taller se representan los datos CAD de la pieza como modelo plano. Con clics del ratón, o con los datos ya especificados en el dibujo, pueden determinarse aleatoriamente puntos y contornos a los cuales se asigna con clic de ratón una función de medición. El software 3D Form Inspect calcula automáticamente los desplazamientos necesarios del palpador de medición y escribe en el programa de fondo un programa de medición para la máquina en que debe medirse. Allí el programa se llama como programa de mecanizado normal. La máquina cambia el palpador de medición, y un calibrado breve generado también de forma automática registra el offset térmico actual de los ejes de la máquina. Los valores de corrección así determinados se tienen en cuenta en la evaluación de los datos de medición. Por medio de este proceso, patentado por m&h, se obtienen en cualquier momento resultados de medición repetibles y fiables que corresponden con los de la máquina de medición. Los resultados se hacen visibles en el ordenador y pueden imprimirse como protocolo en diferentes formatos, o transmitirse como registro de datos. Todo el ciclo toma solamente unos pocos minutos. Entonces el operador reconoce de un vistazo si sus piezas mantienen o no las tolerancias. En caso de duda, puede inmediatamente y en la misma sujeción repasarse.
"Realmente puede afirmarse: esta inversión ha valido la pena"
Las voces críticas en un comienzo de algunos operadores a los cuales se exigió la medición adicional en la máquina cambiaron de forma rápida. „Ahora cada uno puede controlar y protocolizar por si mismo que su pieza es correcta“, relata el Asistente de Innovación Maik Spangenberg. „Se puede medir y confirmar en el lugar, en un tiempo breve, puntos y superficies importantes“. En todas partes el uso del software se describe como sencillo y la introducción transcurrió sin problemas. Entre tanto, la medición con Form Inspect de m&h es natural en toda fábrica y se ha convertido en un alivio para el trabajo diario. „Esto nos ofrece seguridad en toda la empresa“ resalta Klaus Dietsch.
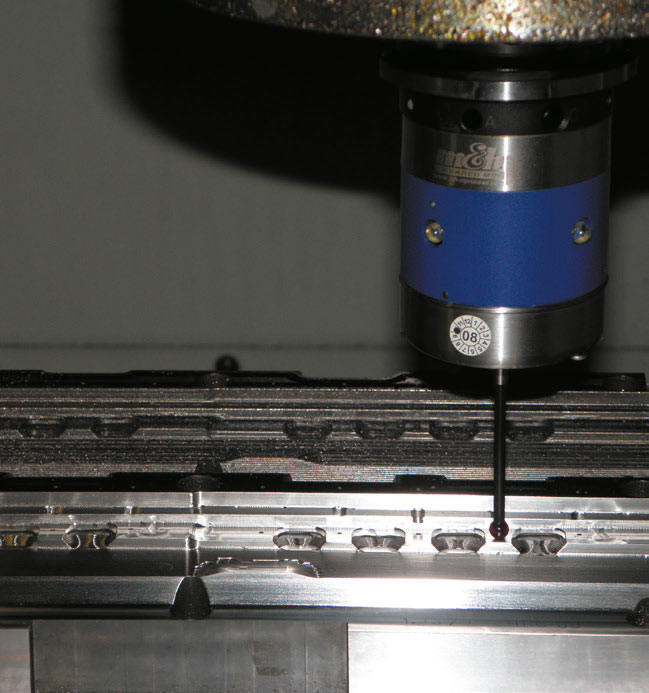