Contrôle de production activé
Contact

Mesurer les pièces usinées alors qu‘elles sont encore
dans leur dispositif de serrage sur la machine assure
une sécurité du processus, y compris dans les cellules
de production automatiques. FKT, le spécialiste des
matériaux synthétiques et moulages permet ainsi
d‘éviter un post-usinage et assure un déroulement
de production plus posé.
Technologie innovante, déroulement fiable de la production ainsi que précision et respect des délais apportent le succès dans le moulage „made in Germany“ au sein de la concurrence mondiale. C‘est ce qui fait la réputation de FKT à Triptis située dans la région de La Thüringe.
On y développe des moules et des outils pour le moulage par
injection et par pression ainsi que des outils de gainage pour
composants métalliques et non métalliques. Dans la plupart
des cas, il s‘agit de moules composites pouvant contenir
jusqu‘à 3 composants. Outre la technologie de moulage par
injection, FKT maîtrise également le procédé de LaserCusing
et la technologie appelée MuCell.
Le Lasercusing signifie que des matériaux en métal, un peu comme le „Rapid-Prototyping“, sont posés par couches successives fondues ensemble par laser. Cette technique permet d‘introduire des contours internes aux formes libres qu‘il est impossible de réaliser autrement. On utilise ces contours internes dans des moulages par injection et par pression comme canaux de climatisation semblables au contour, ce qui permet d‘atteindre des cycles de production rapides, y compris pour de gros volumes d‘injection.
Avec la technique MuCell, le plastique est moussé physiquement en forme. La température et la pression permettent de contrôler le moussage, ce qui serait difficile à réaliser ainsi avec des produits moussants. Cela permet de fabriquer des pièces internes légères et stables, généralement combinées par la suite à d‘autres plastiques ou sous-groupes dans l‘objectif de conserver les propriétés de surface souhaitées.
Les produits ensuite réalisés à partir de ces moulages FKT
sont particulièrement prisés dans l‘industrie automobile et
électronique ainsi que les techniques de communication,
comme dans la construction de machines et d‘appareils
électriques. Dans ces domaines, la demande en moulages
composites par injection est de plus en plus exigeante. De
même que les combinés de plastiques mous et durs en un
seul moulage sont de plus en plus demandés. Le moulage
par injection (montage) est lui aussi de plus en plus utilisé.
Les composants mobiles, tels les lamelles par exemple, sont
directement injectés dans le corps de support. On comprend
alors qu‘on ait souvent besoin de la technique du Laser Cusing
pour fabriquer des conduits de refroidissement correspondants.
Dans le même temps, les moulages composites
en particulier exigent une précision extrême pour les cavités
du moule.
A l‘époque, tout à commencé par la fabrication d‘électrodes qui sont réalisées chez FKT dans une cellule de production automatisée. C‘était le point de départ de la mesure en machine APO (assistée par ordinateur) avec m&h. Le centre d‘usinage Röders qui est dans la cellule de production est équipée de palpeurs de mesure de m&h et du logiciel Inspect de Röders, basé sur le logiciel Form Inspect de m&h.
Très vite, d‘autres centres d‘usinage furent équipés des
palpeurs et du logiciel de m&h. Entre-temps, nous travaillons
avec 6 licences de logiciels pour Form Inspect m&h sur
10 centres d‘usinage de différente tailles et de fabricants
(Röders, DMG Makino, etc.).
Au lieu de décharger la pièce du poste d‘usinage pour la placer sur une machine de mesure puis la remonter ensuite, le palpeur mesure directement la pièce dans le système de serrage de la machine-outil. Un ordinateur installé dans l‘atelier collecte les données CAD de la pièce usinée et la représente en 3D. Avec la souris ou des données fixées dans le dessin, vous pouvez définir des points et contours que vous affectez alors à une fonction de mesure sur simple clic. Le logiciel 3D Form Inspect calcule automatiquement les courses requises par le palpeur de mesure, et rédige un programme de mesure en tâche de fond pour la machine sur laquelle la mesure doit être prise. Le programme peut ensuite être appelé comme un programme d‘usinage normal. La machine insère le palpeur de mesure et un calibrage rapide automatique recense le décalage thermique actuel des axes de machine. Les valeurs de correction ainsi déterminées sont ensuite intégrées dans l‘évaluation des données de mesure. Ce procédé breveté pour m&h permet d‘obtenir à tout moment des résultats de mesure fiables et répétitibles qui correspondent à la machine de mesure. Les résultats s‘affichent ensuite sur l‘ordinateur et peuvent être imprimés en rapport sous divers formats ou transférés en blocs de données. La procédure complète ne dure que quelques minutes. L‘opérateur voit d‘un seul coup d’oeil si ses pièces respectent les tolérances ou non. En cas de doute, il peut immédiatement et sur le même serrage, corriger la pièce avec la machine.
Les critiques initiales des opérateurs de machines à qui on ajoutait les prises de mesure se sont rapidement transformées à l‘inverse. „Maintenant, chacun peut lui-même contrôler sa pièce et consigner qu‘elle est bonne“ décrit l‘assistant au service d‘innovations Maik Spangenberg. „On peut rapidement mesurer des surfaces et points importants dans l‘espace, et les confirmer.“ La manipulation du logiciel est simple et l‘initiation s‘est déroulé sans problème. Entre-temps, la prise de mesure avec Form Inspect de m&h est devenue une évidence et une amélioration des conditions de travail quotidiennes pour chaque collaborateur de l‘entreprise. „Cela nous confère une sécurité dans toute l‘entreprise“ souligne Klaus Dietsch.
Interrogé sur les minutes de mesure sur la machine, Klaus
Dietsch décrit son expérience: „Plus important encore que
le temps de fabrication d‘une pièce, c‘est la sécurité et la
stabilité de la production“, explique-t-il. „Si la pièce n‘est
pas bonne, cela demande beaucoup plus de travail par la
suite et surtout on perd beaucoup de temps“ présentetil
les conséquences. Chaque fois qu‘il faut remettre une
pièce en place, on perd du temps et de la précision. Il faut
souvent refaire la pièce entièrement. Dorénavant chez
FKT, on s‘évite en grande partie ces post-usinages.
Certes, Klaus Dietsch ne peut ou ne veut pas exprimer en
chiffres le gain grâce à la prise de mesure sur machine, mais le bénéfice est indiscutable pour le procédé de
fabrication. Maintenant, on voit dès le départ que les
pièces ont la précision requise et qu‘elles s‘ajusteront
donc parfaitement aux procédés suivants. Ce sont des
aspects importants, et pas seulement pour les cavités
multiples, les coulisseaux et moulages composites.
Les moules sont de plus en plus complexes et possèdent
des niveaux de jonction dans les trois dimensions de
l‘espace. Aujourd‘hui, ils sont fraisés et directement
réalisés aux dimensions finales, ce qui n‘était souvent
garanti que par la mesure avant la finition. Avant,
recommencer une pièce signifiait toujours chambouler
l‘emploi du temps des autres produits. „Il y a nettement
moins de post-usinage“ confirme Klaus Dietsch, „et le
déroulement du procédé est beaucoup plus posé.“ Il est
évident que, outre la qualité et la longévité du produit,
le respect des délais est un facteur important pour
les clients.
Technologie innovante, déroulement fiable de la production ainsi que précision et respect des délais apportent le succès dans le moulage „made in Germany“ au sein de la concurrence mondiale. C‘est ce qui fait la réputation de FKT à Triptis située dans la région de La Thüringe.
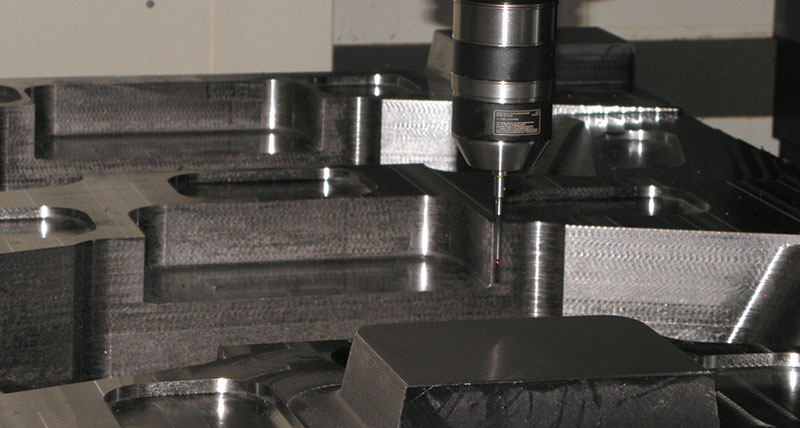
Le Lasercusing signifie que des matériaux en métal, un peu comme le „Rapid-Prototyping“, sont posés par couches successives fondues ensemble par laser. Cette technique permet d‘introduire des contours internes aux formes libres qu‘il est impossible de réaliser autrement. On utilise ces contours internes dans des moulages par injection et par pression comme canaux de climatisation semblables au contour, ce qui permet d‘atteindre des cycles de production rapides, y compris pour de gros volumes d‘injection.
Avec la technique MuCell, le plastique est moussé physiquement en forme. La température et la pression permettent de contrôler le moussage, ce qui serait difficile à réaliser ainsi avec des produits moussants. Cela permet de fabriquer des pièces internes légères et stables, généralement combinées par la suite à d‘autres plastiques ou sous-groupes dans l‘objectif de conserver les propriétés de surface souhaitées.
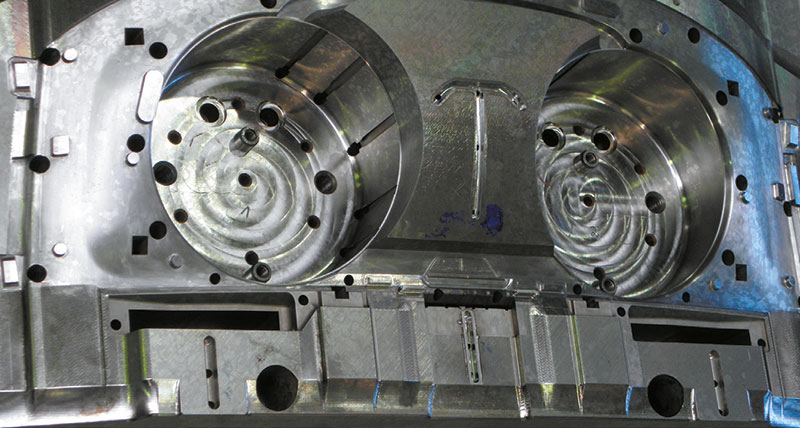
A l‘époque, tout à commencé par la fabrication d‘électrodes qui sont réalisées chez FKT dans une cellule de production automatisée. C‘était le point de départ de la mesure en machine APO (assistée par ordinateur) avec m&h. Le centre d‘usinage Röders qui est dans la cellule de production est équipée de palpeurs de mesure de m&h et du logiciel Inspect de Röders, basé sur le logiciel Form Inspect de m&h.
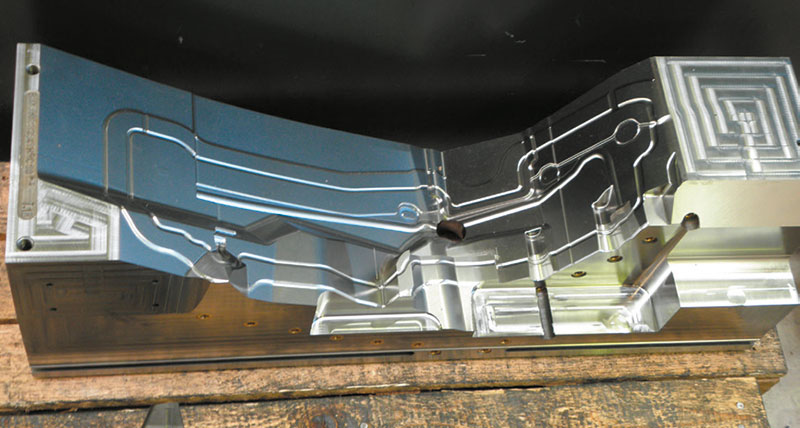
Au lieu de décharger la pièce du poste d‘usinage pour la placer sur une machine de mesure puis la remonter ensuite, le palpeur mesure directement la pièce dans le système de serrage de la machine-outil. Un ordinateur installé dans l‘atelier collecte les données CAD de la pièce usinée et la représente en 3D. Avec la souris ou des données fixées dans le dessin, vous pouvez définir des points et contours que vous affectez alors à une fonction de mesure sur simple clic. Le logiciel 3D Form Inspect calcule automatiquement les courses requises par le palpeur de mesure, et rédige un programme de mesure en tâche de fond pour la machine sur laquelle la mesure doit être prise. Le programme peut ensuite être appelé comme un programme d‘usinage normal. La machine insère le palpeur de mesure et un calibrage rapide automatique recense le décalage thermique actuel des axes de machine. Les valeurs de correction ainsi déterminées sont ensuite intégrées dans l‘évaluation des données de mesure. Ce procédé breveté pour m&h permet d‘obtenir à tout moment des résultats de mesure fiables et répétitibles qui correspondent à la machine de mesure. Les résultats s‘affichent ensuite sur l‘ordinateur et peuvent être imprimés en rapport sous divers formats ou transférés en blocs de données. La procédure complète ne dure que quelques minutes. L‘opérateur voit d‘un seul coup d’oeil si ses pièces respectent les tolérances ou non. En cas de doute, il peut immédiatement et sur le même serrage, corriger la pièce avec la machine.
"On peut vraiment le dire: cet investissement est rentable."
Les critiques initiales des opérateurs de machines à qui on ajoutait les prises de mesure se sont rapidement transformées à l‘inverse. „Maintenant, chacun peut lui-même contrôler sa pièce et consigner qu‘elle est bonne“ décrit l‘assistant au service d‘innovations Maik Spangenberg. „On peut rapidement mesurer des surfaces et points importants dans l‘espace, et les confirmer.“ La manipulation du logiciel est simple et l‘initiation s‘est déroulé sans problème. Entre-temps, la prise de mesure avec Form Inspect de m&h est devenue une évidence et une amélioration des conditions de travail quotidiennes pour chaque collaborateur de l‘entreprise. „Cela nous confère une sécurité dans toute l‘entreprise“ souligne Klaus Dietsch.
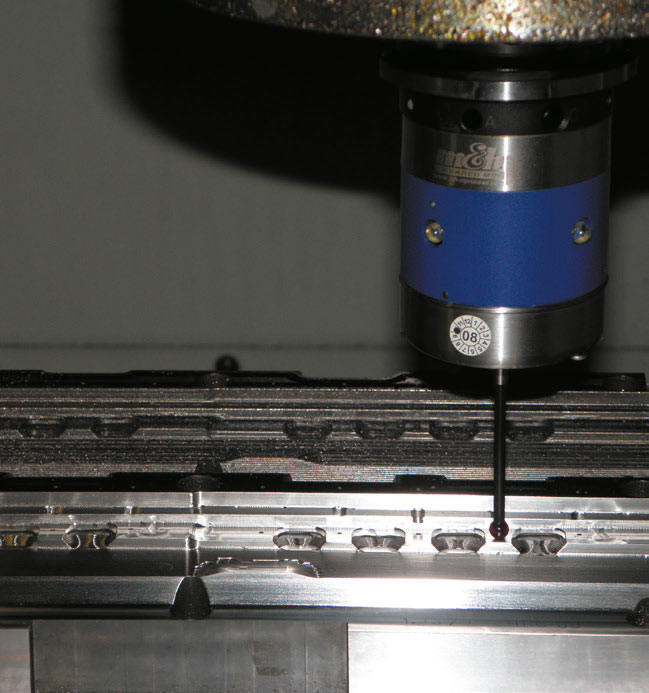