PC-DMIS Preset & Measure suite
You produce - we measure. Increase the productivity of your machine tools.

Ready to get started?
Can be used on a manual measuring device up to the automated cell in connection with the PC-DMIS software.
To ensure the quality of the workpieces, various manufacturing steps must be monitored using measurement technology. If this is done on the milling or eroding machine, the processing machine is not available for the production process during this time.
Furthermore, inaccurate measurement results cannot be ruled out during the critical warm-up time of the processing machine.
Therefore, the measurement on a coordinate measuring machine pays off from the first eroding machine:
- Shorter set-up times
- Longer machine runtimes (availability)
- Reduction of lead times
- Fast availability and more precise offset data directly in the processing machine
- In addition to generating offset data, quality data is also available
In total, the degree of utilization of the processing machine is significantly increased, which increases overall productivity.
Fully automated eroding and / or milling cell with Hexagon CMM & PC-DMIS Preset & Measure Supervisor
In the case of a fully automatic solution, the coordinate measuring machine, the milling and / or eroding machine and other components are integrated into the production cell. A job manager coordinates the robot loading and tooling as well as the interaction of the processing and measuring machine.
This enables maximum productivity & machine efficiency combined with accuracy and process stability with 24/7 use in production.
The PC-DMIS Preset & Measure Suite includes the following software solutions:
3 modules enable the software to be optimally adapted to customer requirements
Preset & Measure
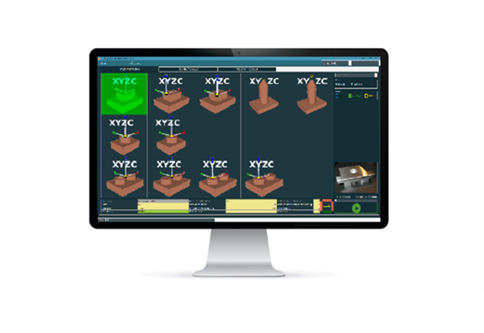
- Calibration of probes
- Calibration of chucks
- Offset data determination for electrodes and workpieces for the chucks
- Quality measurement on electrode contours and / or workpieces
- Plausibility checks are integrated and prevent operator errors
In addition, the measurement data are managed and can be exported to any output format. Fully parameterized post processors are available for this, which can be added by the customer and adapted to the existing processing machines.
Measurement data can be output in various protocol formats and Q-DAS ASCII transfer format.
Preset & Measure Inspection Planner
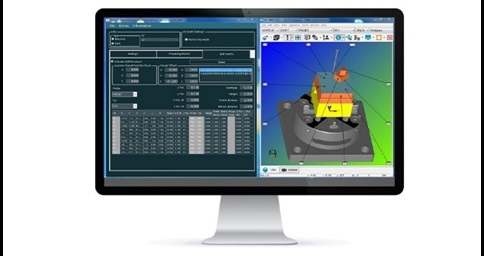
The buttons and secondary information to be used (such as probing parameters and spark gap) are defined here. The data file can then be automatically converted into a measuring routine in Preset & Measure on the coordinate measuring machine.
Preset & Measure Supervisor
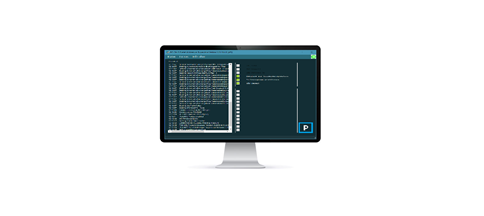
- Zimmer & Kreim: JOBmod CMM
- GF Machining Solutions (System 3R): WSM – WorkShopManager
- Röders: RMSMain
-
Features & benefits
-
Downloads
-
Applications