Straightforwardly measure and report on 5 axes
Contact us

By measuring its milled workpieces using touch probes and the software 3D Form Inspect from m&h, the fixture manufacturer Dörr has not only removed a production bottleneck, but also a source of errors. His customers value the quick delivery of workpieces with a measuring report based on measurements made directly on the machine.
Curved and arbitrarily shaped milled parts are the daily business of the gauge and fixture manufacturer Dörr GmbH in the Rhineland town of St. Augustin. The third-generation family business was founded more than 60 years ago as a model-maker and can look back on a successful history.
The models for foundries, manufactured using the so-called hand forming method, have long since faded into the background. Demanding gauges, fixtures and the contract manufacture of single parts and very small production runs for the automotive industry, machine tool manufacturers and motor sport are today the most important business activities of Dörr.
A common feature of almost all workpieces is free-form surfaces and curved geometries. To manufacture these parts a whole series of machining centres, predominantly with 5 axes, are available. C40 machining centres from Hermle operate alongside DMU 635V, DMU 835V, DMU 1035V and a new DMU 200P. For very large workpieces there is also a machining centre of type Zimmermann FZ40.
For some years Dörr has had good experience with touch probes from m&h, which were purchased for the first time with a Hermle C40U. However, the measuring cycles in the control software proved to be increasingly inadequate, because more and more surfaces and geometries needed to be measured and logged in the compartment. Although Dörr has 6 measuring machines, they are time consuming to use and the tedious clamping and removal processes are also time consuming. The available capacity also caused delays time and again. Also at Dörr the high quality gauges are mostly assembled and completed on the measuring machines to ensure the highest accuracy. However it is then not possible to remove a workpiece from the measuring machine to measure a milled part. Finally it was decided to purchase the m&h software 3D Form Inspect.
Using this software the nominal data from the CAD design are compared with the actual values on the workpiece directly on the machine and logged. For this purpose the CAD data are loaded into a computer in the workshop; the software from m&h then generates a surface model from the data and displays the model on the monitor. As the majority of the designs, not just the gauges, are developed in-house at Dörr using Catia, there are always CAD models available. The points to be measured are then defined on these surface models and measuring functions such as angles, widths, diameters and many others, assigned. At Dörr the supervisor and machine operator jointly define which points and areas are to be measured on the related workpiece.
With 3D Form Inspect we have become more flexible and significant faster. The software 3D Form Inspect automatically writes, in the background, the related movement program for the touch probe on the machines. During this pro- cess a collision check with the workpiece contours is also performed, which provides additional safety in daily use. A short calibration is included before the movement program, in this way the actual thermal and static errors on the machine are measured. These errors are included in the evaluation, an aspect that guarantees reliable, comparable values on measuring machines. On the 5-axis machines the calibration is undertaken at the angles at which the touch probe is then also used for measuring. The evaluation then automatically compensates for the rotational errors on the 4th and 5th axes. These calibration methods are patented by m&h. The measured values are available both on the surface model on the computer monitor, and as a file for further processing, storage or for printing reports in various formats. “Our customers require measuring reports more and more, even for relatively simple milled parts, but especially for 3D contours”, explains Roland Tillmann, head of fixture making, precision mechanics, contract manufacture and inspection gauges at Dörr. “Our orders are often quick jobs”, explains Roland Tillmann. “Often we manufacture the individual parts in only 2 to 3 days.” This situation is made easier by the fact that the majority of workpieces are made of aluminium and only rarely from steels or model-making plastics. Very practically, with only one software licence 3D Form Inspect can be used alternately on several machines, also of varying type and manufacturer. As a consequence Dörr can also work very flexibly without the need to release workpieces from their clamping arrangements.
“With 3D Form Inspect we are have become more flexible and significantly faster”, Mr. Tillmann is pleased to state. “We save setting up on the measuring machine and the task of moving to it. The investment has definitely already paid for itself. And we are still only at the start.” Up to now only the final measurement of the workpieces was undertaken at Dörr using 3D Form Inspect. Step-by-step more and more measurements are to be undertaken between machining steps. Also faster set-up with the aid of the software module Best Fit is to be addressed in the near future.
During these processes the ease of use of the software 3D Form Inspect is a great help; the software was specifically developed for usage in the workshop. With scroll menus and icons it permits almost intuitive operation. If a function is selected at a point on the work-piece, the software automatically searches for the exactly corresponding counterpoint, a feature that makes the measurement absolutely reliable and error-free. Prior to the approval of the program on the machine, a simulation of the program is run that, in case of doubt, shows if a selected function cannot be run. Training on the system is provided on-site during installation. “After just the first day we had already measured the first workpiece on the machine without having to wait for the measuring machine”, Roland Tillmann is pleased to state. “In addition we have gained certainty” he adds. “In the past we measured manually and only hit the required points approximately. Today we move exactly to the points using the touch probe. And there are no longer any reading errors on the dial gauge.” The certainty and the time gained, despite the short time needed for the measurements, make the system valuable for the business. “The short time needed for the measurements is not an issue on our individual parts. It would be much worse if the parts did not fit subsequently and the customers were not satisfied”, emphasises Roland Tillmann.
Curved and arbitrarily shaped milled parts are the daily business of the gauge and fixture manufacturer Dörr GmbH in the Rhineland town of St. Augustin. The third-generation family business was founded more than 60 years ago as a model-maker and can look back on a successful history.
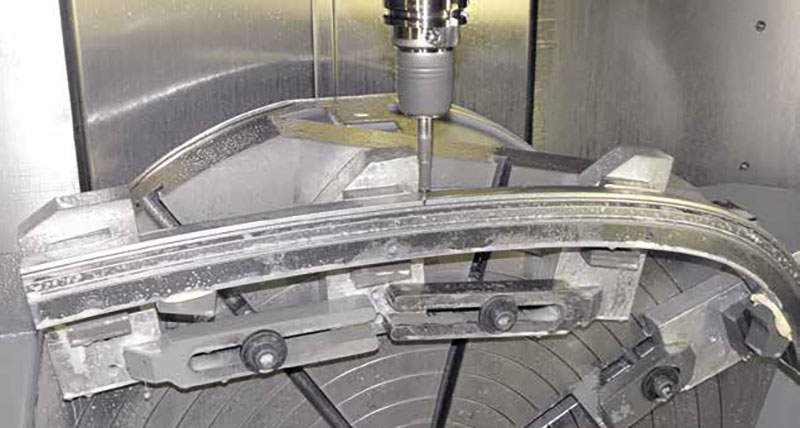
A common feature of almost all workpieces is free-form surfaces and curved geometries. To manufacture these parts a whole series of machining centres, predominantly with 5 axes, are available. C40 machining centres from Hermle operate alongside DMU 635V, DMU 835V, DMU 1035V and a new DMU 200P. For very large workpieces there is also a machining centre of type Zimmermann FZ40.
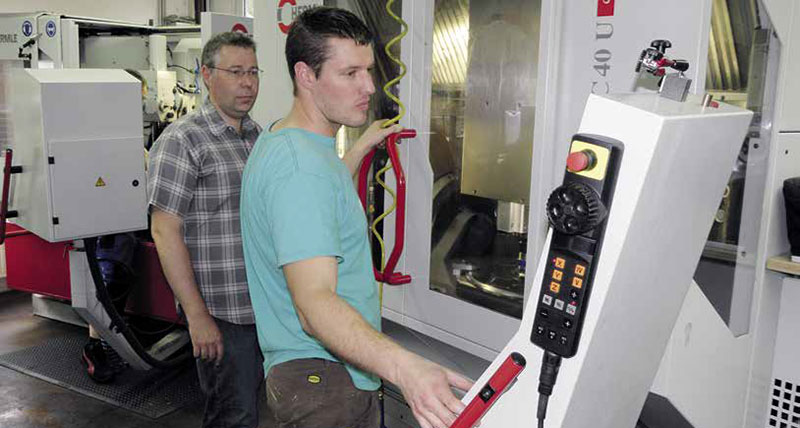
Using this software the nominal data from the CAD design are compared with the actual values on the workpiece directly on the machine and logged. For this purpose the CAD data are loaded into a computer in the workshop; the software from m&h then generates a surface model from the data and displays the model on the monitor. As the majority of the designs, not just the gauges, are developed in-house at Dörr using Catia, there are always CAD models available. The points to be measured are then defined on these surface models and measuring functions such as angles, widths, diameters and many others, assigned. At Dörr the supervisor and machine operator jointly define which points and areas are to be measured on the related workpiece.
With 3D Form Inspect we have become more flexible and significant faster. The software 3D Form Inspect automatically writes, in the background, the related movement program for the touch probe on the machines. During this pro- cess a collision check with the workpiece contours is also performed, which provides additional safety in daily use. A short calibration is included before the movement program, in this way the actual thermal and static errors on the machine are measured. These errors are included in the evaluation, an aspect that guarantees reliable, comparable values on measuring machines. On the 5-axis machines the calibration is undertaken at the angles at which the touch probe is then also used for measuring. The evaluation then automatically compensates for the rotational errors on the 4th and 5th axes. These calibration methods are patented by m&h. The measured values are available both on the surface model on the computer monitor, and as a file for further processing, storage or for printing reports in various formats. “Our customers require measuring reports more and more, even for relatively simple milled parts, but especially for 3D contours”, explains Roland Tillmann, head of fixture making, precision mechanics, contract manufacture and inspection gauges at Dörr. “Our orders are often quick jobs”, explains Roland Tillmann. “Often we manufacture the individual parts in only 2 to 3 days.” This situation is made easier by the fact that the majority of workpieces are made of aluminium and only rarely from steels or model-making plastics. Very practically, with only one software licence 3D Form Inspect can be used alternately on several machines, also of varying type and manufacturer. As a consequence Dörr can also work very flexibly without the need to release workpieces from their clamping arrangements.
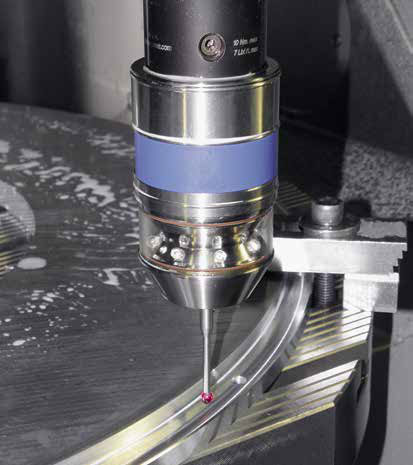
During these processes the ease of use of the software 3D Form Inspect is a great help; the software was specifically developed for usage in the workshop. With scroll menus and icons it permits almost intuitive operation. If a function is selected at a point on the work-piece, the software automatically searches for the exactly corresponding counterpoint, a feature that makes the measurement absolutely reliable and error-free. Prior to the approval of the program on the machine, a simulation of the program is run that, in case of doubt, shows if a selected function cannot be run. Training on the system is provided on-site during installation. “After just the first day we had already measured the first workpiece on the machine without having to wait for the measuring machine”, Roland Tillmann is pleased to state. “In addition we have gained certainty” he adds. “In the past we measured manually and only hit the required points approximately. Today we move exactly to the points using the touch probe. And there are no longer any reading errors on the dial gauge.” The certainty and the time gained, despite the short time needed for the measurements, make the system valuable for the business. “The short time needed for the measurements is not an issue on our individual parts. It would be much worse if the parts did not fit subsequently and the customers were not satisfied”, emphasises Roland Tillmann.