Mal eben 5-achsig messen und protokollieren
Kontakt

Mit dem Messen der Fräswerkstücke mit
Messtastern und Software 3D Form Inspect von
m&h hat der Vorrichtungsbauer Dörr nicht nur
einen Engpass beseitigt, sondern Fehlerquellen
beseitigt. Seine Kunden schätzen die schnelle
Lieferung der Werkstücke mit Messprotokoll
direkt von der Maschine.
Vielseitig gekrümmte und frei geformte Frästeile sind das tägliche Geschäft des Lehren- und Vorrichtungsbaus Dörr GmbH im rheinischen St. Augustin. Das in dritter Generation familiengeführte Unternehmen wurde vor mehr als 60 Jahren als Modellbau gegründet und blickt auf eine erfolgreiche Geschichte zurück.
Längst
sind die Modelle für Gießereien mit dem sogenannten
Handformverfahren eher in den Hintergrund gerückt.
Anspruchsvolle Lehren, Vorrichtungen und die Lohnfertigung von Einzelteilen und Kleinstserien für die
Automobilindustrie, den Maschinenbau und den Rennsport
sind heute die wichtigsten Tätigkeitsfelder des Hauses Dörr.
Fast allen Werkstücken gemein sind Freiformflächen und gekrümmte Geometrien. Für deren Fertigung steht eine ganze Reihe von Bearbeitungszentren, vornehmlich mit 5 Achsen, zur Verfügung. Bearbeitungszentren C40 von Hermle arbeiten neben DMU 635V, DMU 835V, DMU 1035V und einer neuen DMU 200P. Für die ganz großen Brocken gibt es noch ein Bearbeitungszentrum vom Typ Zimmermann FZ40.
Schon seit Jahren hat die Firma Dörr gute Erfahrungen
mit den Messtastern von m&h gesammelt, die seinerzeit
erstmals mit einer Hermle C40U angeschafft wurden.
Die Messzyklen der Steuerungs-software erwiesen sich
jedoch zunehmend als unzureichend, weil mehr und
mehr Flächen und Geometrien im Raum gemessen und
protokolliert werden mussten. Zwar verfügt die Firma Dörr
sogar über 6 Messmaschinen, aber der Zeitaufwand und
das lästige Ab- und Aufspannen erwiesen sich ebenso als
zeitraubend. Auch die verfügbare Kapazität führte immer
wieder zu Verzögerungen. Schließlich werden bei Dörr
die hochwertigen Lehren meist auf den Messmaschinen
zusammengebaut und komplettiert, um höchste
Genauigkeit zu gewährleisten. Da kann nicht eben mal ein
Werkstück von der Messmaschine genommen werden, nur
um ein Frästeil zu messen.
Letztlich entschloss man sich zum Kauf der m&h- Software
3D Form Inspect.
Mit dieser Software werden die Solldaten der CAD-Konstruktion mit den tatsächlichen Werten des Werkstückes direkt auf der Maschine verglichen und protokolliert. Dazu werden die CAD-Daten in einen Computer in der Werkstatt geladen, auf dem die Software von m&h daraus ein Flächenmodell formt und am Bildschirm darstellt. Weil die meisten Konstruktionen, nicht nur der Lehren, im Haus Dörr selbst auf Catia entwickelt werden, sind immer CAD-Modelle vorhanden. An diesen Flächenmodellen werden dann die zu messenden Punkte festgelegt und Messfunktionen, wie Winkel, Breite, Durchmesser u.a.m. zugewiesen. Im Hause Dörr legen Meister und Maschinenbediener gemeinsam fest, welche Punkte und Bereiche am jeweiligen Werkstück gemessen werden sollen.
Mit 3D Form Inspect sind wir flexibler und wesentlich schneller geworden, Die Software 3D Form Inspect schreibt im Hintergrund automatisch das entsprechende Verfahrprogramm für den Messtaster auf den Maschinen. Dabei wird auch eine Kollisionsprüfung mit den Werkstückkonturen durchgeführt, was zusätzliche Sicherheit im täglichen Einsatz schafft. Dem Verfahrprogramm wird eine kurze Kalibrierung voran gestellt, wodurch die aktuellen thermischen und statischen Abweichungen der Maschine erfasst werden. Diese werden in der Auswertung mitberechnet, was vergleichbar zuverlässige Werte wie auf Messmaschinen garantiert. Bei den 5-achsigen Maschinen erfolgt die Kalibrierung in den Anstellwinkeln des Messtasters, in denen dann auch gemessen wird. So ergibt sich mit der Auswertung eine automatische Kompensation der Schwenkfehler der 4. und 5. Achsen. Diese Kalibrierverfahren sind für m&h patentiert. Die Messwerte stehen sowohl auf dem Flächenmodell am Computerbildschirm, als auch als Datei zur Weitergabe, Speicherung oder zum Protokollaus- druck in verschiedenen Formaten zur Verfügung. “Unsere Kunden verlangen mehr und mehr nach Messprotokollen, auch bei relativ einfachen Frästeilen, aber insbesondere bei den 3D Konturen”, erklärt Roland Tillmann, zuständiger Leiter des Vorrichtungsbaus, Feinmechanik, Lohnfertigung und Prüflehren bei Dörr. “Bei unseren Aufträgen handelt es sich oft um schnelle Geschäfte”, erläutert Roland Tillmann. “Oft fertigen wir die Einzelteile innerhalb von nur 2 bis 3 Tagen.” Das wird dadurch erleichtert, dass die Werkstücke meist aus Aluminium und seltener aus Stählen oder aus Modellbaukunststoffen gefertigt werden. Praktischer Weise kann 3D Form Inspect mit nur einer Softwarelizenz wechselweise an mehreren Maschinen, auch unterschiedlicher Art und Hersteller, eingesetzt werden. Dadurch wird auch Dörr sehr flexibel, ohne die Werkstücke aus deren Aufspannung lösen zu müssen.
“Mit 3D Form Inspect sind wir flexibler und wesentlich
schneller geworden”, freut sich Herr Tillmann. “Wir sparen
uns das Rüsten auf der Messmaschine und den Weg dorthin.
Die Investition hat sich in jedem Fall bereits gelohnt. Dabei
stehen wir noch am Anfang.” Bisher wird bei Dörr erst die
abschließende Messung der Werkstücke mit 3D Form
Inspect durchgeführt. Schrittweise soll mehr und mehr auch
zwischen den Bearbeitungsschritten gemessen werden.
Auch das schnellere Rüsten mit Hilfe des Softwaremoduls
Best Fit soll demnächst angegangen werden.
Dabei hilft die leichte Bedienbarkeit der Software 3D Form Inspect, die gezielt für den Einsatz in der Werkstatt entwickelt wurde. Mit Scroll-Menüs und Icons erlaubt sie eine nahezu intuitive Bedienung. Wenn zu einem Punkt auf dem Werkstück eine Funktion gewählt wird, sucht sich die Software automatisch den genau entsprechenden Gegenpunkt, was die Messung absolut zuverlässig und fehlerfrei macht. Vor der Freigabe des Programmes an die Maschine durchläuft das Programm eine Simulation, die im Zweifelsfall darstellt, wenn eine gewählte Funktion nicht ausgeführt werden kann. Geschult wurde das System bei der Installation vor Ort. “Bereits nach dem ersten Tag hatten wir das erste Werkstück auf der Maschine gemessen, ohne auf die Messmaschine warten zu müssen”, freut sich Roland Tillmann. “Zudem haben wir Sicherheit gewonnen” ergänzt er. “Früher haben wir manuell gemessen und die gewünschten Punkte nur ungefähr getroffen. Heute fahren wir die Punkte mit dem Messtaster genau an. Und Ablesefehler auf der Messuhr gibt es nicht mehr.” Die gewonnene Sicherheit und die gewonnene Zeit, trotz kurzem Zeitaufwand für das Messen, machen das System wertvoll für den Betrieb. “Die kurze Zeit für das Messen darf bei unseren Einzelteilen nicht zählen. Viel schlimmer wäre, wenn die Teile nachher nicht passen und die Kunden nicht zufrieden wären”, bekräftigt Roland Tillmann.
Vielseitig gekrümmte und frei geformte Frästeile sind das tägliche Geschäft des Lehren- und Vorrichtungsbaus Dörr GmbH im rheinischen St. Augustin. Das in dritter Generation familiengeführte Unternehmen wurde vor mehr als 60 Jahren als Modellbau gegründet und blickt auf eine erfolgreiche Geschichte zurück.
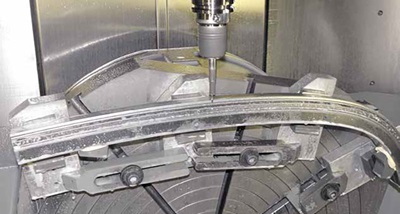
Fast allen Werkstücken gemein sind Freiformflächen und gekrümmte Geometrien. Für deren Fertigung steht eine ganze Reihe von Bearbeitungszentren, vornehmlich mit 5 Achsen, zur Verfügung. Bearbeitungszentren C40 von Hermle arbeiten neben DMU 635V, DMU 835V, DMU 1035V und einer neuen DMU 200P. Für die ganz großen Brocken gibt es noch ein Bearbeitungszentrum vom Typ Zimmermann FZ40.
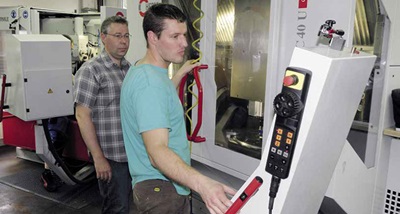
Mit dieser Software werden die Solldaten der CAD-Konstruktion mit den tatsächlichen Werten des Werkstückes direkt auf der Maschine verglichen und protokolliert. Dazu werden die CAD-Daten in einen Computer in der Werkstatt geladen, auf dem die Software von m&h daraus ein Flächenmodell formt und am Bildschirm darstellt. Weil die meisten Konstruktionen, nicht nur der Lehren, im Haus Dörr selbst auf Catia entwickelt werden, sind immer CAD-Modelle vorhanden. An diesen Flächenmodellen werden dann die zu messenden Punkte festgelegt und Messfunktionen, wie Winkel, Breite, Durchmesser u.a.m. zugewiesen. Im Hause Dörr legen Meister und Maschinenbediener gemeinsam fest, welche Punkte und Bereiche am jeweiligen Werkstück gemessen werden sollen.
Mit 3D Form Inspect sind wir flexibler und wesentlich schneller geworden, Die Software 3D Form Inspect schreibt im Hintergrund automatisch das entsprechende Verfahrprogramm für den Messtaster auf den Maschinen. Dabei wird auch eine Kollisionsprüfung mit den Werkstückkonturen durchgeführt, was zusätzliche Sicherheit im täglichen Einsatz schafft. Dem Verfahrprogramm wird eine kurze Kalibrierung voran gestellt, wodurch die aktuellen thermischen und statischen Abweichungen der Maschine erfasst werden. Diese werden in der Auswertung mitberechnet, was vergleichbar zuverlässige Werte wie auf Messmaschinen garantiert. Bei den 5-achsigen Maschinen erfolgt die Kalibrierung in den Anstellwinkeln des Messtasters, in denen dann auch gemessen wird. So ergibt sich mit der Auswertung eine automatische Kompensation der Schwenkfehler der 4. und 5. Achsen. Diese Kalibrierverfahren sind für m&h patentiert. Die Messwerte stehen sowohl auf dem Flächenmodell am Computerbildschirm, als auch als Datei zur Weitergabe, Speicherung oder zum Protokollaus- druck in verschiedenen Formaten zur Verfügung. “Unsere Kunden verlangen mehr und mehr nach Messprotokollen, auch bei relativ einfachen Frästeilen, aber insbesondere bei den 3D Konturen”, erklärt Roland Tillmann, zuständiger Leiter des Vorrichtungsbaus, Feinmechanik, Lohnfertigung und Prüflehren bei Dörr. “Bei unseren Aufträgen handelt es sich oft um schnelle Geschäfte”, erläutert Roland Tillmann. “Oft fertigen wir die Einzelteile innerhalb von nur 2 bis 3 Tagen.” Das wird dadurch erleichtert, dass die Werkstücke meist aus Aluminium und seltener aus Stählen oder aus Modellbaukunststoffen gefertigt werden. Praktischer Weise kann 3D Form Inspect mit nur einer Softwarelizenz wechselweise an mehreren Maschinen, auch unterschiedlicher Art und Hersteller, eingesetzt werden. Dadurch wird auch Dörr sehr flexibel, ohne die Werkstücke aus deren Aufspannung lösen zu müssen.
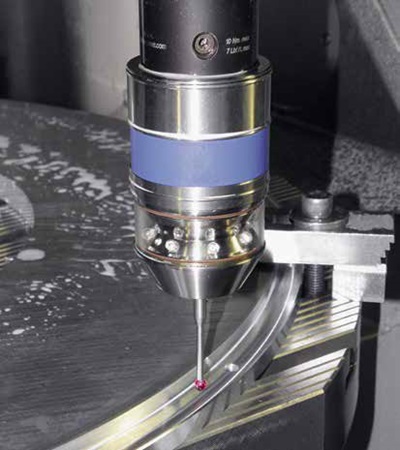
Dabei hilft die leichte Bedienbarkeit der Software 3D Form Inspect, die gezielt für den Einsatz in der Werkstatt entwickelt wurde. Mit Scroll-Menüs und Icons erlaubt sie eine nahezu intuitive Bedienung. Wenn zu einem Punkt auf dem Werkstück eine Funktion gewählt wird, sucht sich die Software automatisch den genau entsprechenden Gegenpunkt, was die Messung absolut zuverlässig und fehlerfrei macht. Vor der Freigabe des Programmes an die Maschine durchläuft das Programm eine Simulation, die im Zweifelsfall darstellt, wenn eine gewählte Funktion nicht ausgeführt werden kann. Geschult wurde das System bei der Installation vor Ort. “Bereits nach dem ersten Tag hatten wir das erste Werkstück auf der Maschine gemessen, ohne auf die Messmaschine warten zu müssen”, freut sich Roland Tillmann. “Zudem haben wir Sicherheit gewonnen” ergänzt er. “Früher haben wir manuell gemessen und die gewünschten Punkte nur ungefähr getroffen. Heute fahren wir die Punkte mit dem Messtaster genau an. Und Ablesefehler auf der Messuhr gibt es nicht mehr.” Die gewonnene Sicherheit und die gewonnene Zeit, trotz kurzem Zeitaufwand für das Messen, machen das System wertvoll für den Betrieb. “Die kurze Zeit für das Messen darf bei unseren Einzelteilen nicht zählen. Viel schlimmer wäre, wenn die Teile nachher nicht passen und die Kunden nicht zufrieden wären”, bekräftigt Roland Tillmann.