Medir y protocolizar con 5 ejes
Contacto

Con la medición de las piezas de fresado con
sondas de contacto y software 3D Form Inspect
de m&h, el fabricante de dispositivos Dörr no solo
ha eliminado un cuello de botella sino también
las fuentes de error. Sus clientes valoran la rápida
entrega de l as piezas de trabajo con protocolo de
medición directamente de la máquina.
Las piezas de fresado curvilíneas y de forma libre son el trabajo diario del fabricante de calibres y dispositivos Dörr GmbH en la población alemana de Sankt Augustin. Esta empresa familiar que ya va por la tercera generación fue fundada hace más de 60 años como fábrica de maquetas y tiene tras de sí toda una historia de éxito.
Hace tiempo
que los modelos para fundiciones con el denominado
procedimiento de moldeo manual fueron relegados a un
segundo plano. Los exigentes calibres y dispositivos y la fabricación por encargo de piezas individuales y series
pequeñas para la automoción, la ingeniería mecánica y el
deporte del motor son hoy en días los principales campos de
actividad de la empresa Dörr.
Casi todas las piezas de trabajo son superficies de forma libre y geo-metrías curvilíneas. Para su fabrica- ción, se dispone de una serie completa de centros de mecanizado, principalmente con 5 ejes. Los centros de mecanizado C40 de Hermle trabajan junto a DMU 635V, DMU 835V, DMU 1035V y un nuevo DMU 200P. Para las piezas muy grandes se dispone de un centro de mecanizado del tipo Zimmermann FZ40.
La empresa Dörr acumula desde hace años buenas
experiencias con las sondas de contacto de m&h, que
se adquirieron en su momento por primera vez con un
Hermle C40U. Pero los ciclos de medición del software de
control se mostraron insuficientes, ya que se debían medir
y protocolizar cada vez más superficies y geometrías. La
empresa Dörr dispone incluso de 6 máquinas de medición,
pero el consumo de tiempo y el fatigoso destensado y tensado
exigían también mucho tiempo. También la capacidad
disponible provocaba a menudo retrasos. En Dörr también
se montan y completan los calibres mayormente en las
máquinas de medición para garantizar la máxima precisión,
puesto que no es posible tomar una pieza de trabajo de la
máquina de medición solo para medir una parte fresada.
Finalmente, se decidió la compra del software
3D Form Inspect de m&h.
Con este software se comparan y protocolizan los datos nominales del diseño CAD con los valores reales de la pieza de trabajo directamente en la máquina. Para ello se cargan los datos CAD en un ordenador del taller en el que el software de m&h forma un modelo de superficies y lo representa en la pantalla. Puesto que la mayoría de diseños, no solo de los calibres, se han desarrollado en Dörr con Catia, se dispone siempre de modelos CAD. En estos modelos de superficie se determinan luego los puntos por medir y se asignan las funciones de medición, como ángulos, ancho, diámetro, etc. En Dörr, el maestro de taller y los operarios determinan conjuntamente qué puntos y áreas deben medirse en la herramienta correspondiente.
Con 3D Form Inspect somos más flexibles y considerablemente más rápidos, El software 3D Form Inspect registra en segundo plano automáticamente el programa correspondiente para las sondas de contacto en las máquinas. Para ello se realiza una comprobación de colisión con los contornos de herramienta, lo que aporta seguridad adicional en la aplicación diaria. Al programa se antepone una breve calibración mediante la cual se registran las divergencias estáticas y térmicas actuales de la máquina. Estas se incluyen en la evaluación, lo que garantiza valores fiables comparables a los de las máquinas de medición. En las máquinas de 5 ejes, la calibración se realiza en los ángulos de incidencia de la sonda de contacto, en los que también se mide. De este modo, se obtiene con la evaluación una compensación automática de los errores rotacionales de los ejes 4o y 5o. Estos procedimientos de calibración están patentados por m&h. Los valores de medición están a disposición tanto en el modelo de superficie en la pantalla del ordenador, como también como archivo para su repro-ducción, guardado o impresión de protocolos en distintos formatos. “Nuestros clientes exigen cada vez más protocolos de medición, incluso para piezas fresadas relativamente sencillas, pero especialmente cuando se trata de contornos 3D”, explica Roland Tillmann, jefe responsable de construcción de dispositivos, mecánica de precisión, fabricación por encargo y calibres en Dörr. “Nuestros encargos son a menudo de carácter urgente“, explica Roland Tillmann. “A menudo fabricamos las piezas en solo 2 ó 3 días”. Esto es posible, porque las piezas de trabajos son en su mayoría de aluminio y raramente de aceros o plásticos de modelado. Resulta muy práctico que 3D Form Inspect pueda utilizarse con solo una licencia de software en varias máquinas, también de distintos tipos y fabricantes. Además Dörr también es muy flexible, no requiere soltar las piezas de trabajo de su fijación.
“Con 3D Form Inspect somos más flexibles y
considerablemente más rápidos”, afirma el señor Tillmann.
“Nos ahorramos la preparación de la máquina de medición
y el traslado. La inversión realmente ha merecido la pena.
Pero todavía estamos al principio”. Hasta ahora, en Dörr se
realizaba solo la medición final de las piezas de trabajo con
3D Form Inspect. Poco a poco debe medirse cada vez más
también entre fases de mecanizado. También se iniciará
próximamente el ajuste más rápido con ayuda del módulo de
software Best Fit.
Servirá de ayuda la fácil manejabilidad del software 3D Form Inspect, que ha sido desarrollado específicamente para utilización en el taller. Con los menús desplegables y los iconos permite un manejo real- mente intuitivo. Cuando se selecciona una función en un punto de la pieza de trabajo, el software busca automáticamente el contrapunto preciso correspondiente que hace que la medición sea absolutamente fiable y sin errores. Antes de la autorización del programa en la máquina, este realiza una simulación que en caso de duda representa cuándo no puede ejecutarse una función seleccionada. El sistema fue programado durante la instalación in situ. “Después del primer día ya pudimos medir la primera pieza de trabajo en la máquina sin tener que esperar a la máquina de medición“, afirma contento Roland Tillmann. “Además, hemos ganado en seguridad“ añade. “Antes medíamos manualmente y los puntos deseados solo se lograban de modo aproximado. Ahora abordamos los puntos de modo preciso con la sonda de contacto. Y hemos acabado con los errores de lectura en la galga”. La seguridad adquirida y el tiempo ganado, a pesar del breve tiempo invertido para la medición, hacen que el sistema sea muy valioso para la empresa. “El breve tiempo para la medición no supone ningún handicap. Mucho peor sería que las piezas no fuesen correctas y que los clientes no estuvieran satisfechos” remarca Roland Tillmann.
Las piezas de fresado curvilíneas y de forma libre son el trabajo diario del fabricante de calibres y dispositivos Dörr GmbH en la población alemana de Sankt Augustin. Esta empresa familiar que ya va por la tercera generación fue fundada hace más de 60 años como fábrica de maquetas y tiene tras de sí toda una historia de éxito.
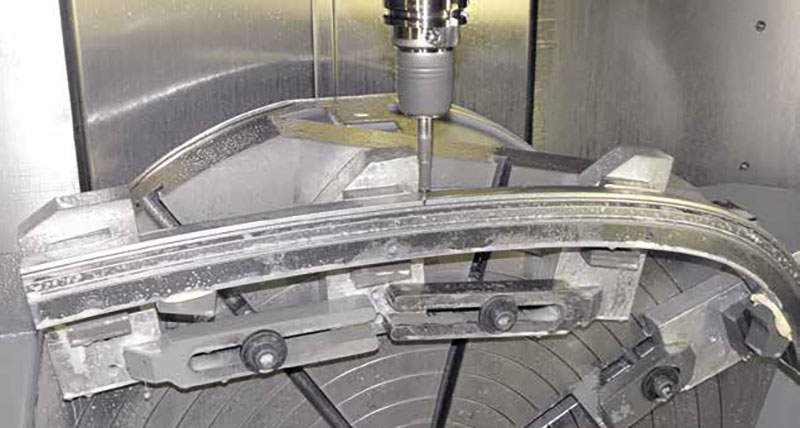
Casi todas las piezas de trabajo son superficies de forma libre y geo-metrías curvilíneas. Para su fabrica- ción, se dispone de una serie completa de centros de mecanizado, principalmente con 5 ejes. Los centros de mecanizado C40 de Hermle trabajan junto a DMU 635V, DMU 835V, DMU 1035V y un nuevo DMU 200P. Para las piezas muy grandes se dispone de un centro de mecanizado del tipo Zimmermann FZ40.
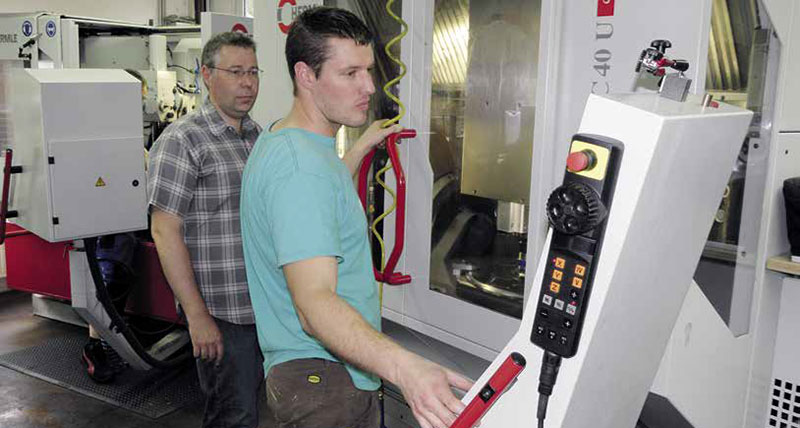
Con este software se comparan y protocolizan los datos nominales del diseño CAD con los valores reales de la pieza de trabajo directamente en la máquina. Para ello se cargan los datos CAD en un ordenador del taller en el que el software de m&h forma un modelo de superficies y lo representa en la pantalla. Puesto que la mayoría de diseños, no solo de los calibres, se han desarrollado en Dörr con Catia, se dispone siempre de modelos CAD. En estos modelos de superficie se determinan luego los puntos por medir y se asignan las funciones de medición, como ángulos, ancho, diámetro, etc. En Dörr, el maestro de taller y los operarios determinan conjuntamente qué puntos y áreas deben medirse en la herramienta correspondiente.
Con 3D Form Inspect somos más flexibles y considerablemente más rápidos, El software 3D Form Inspect registra en segundo plano automáticamente el programa correspondiente para las sondas de contacto en las máquinas. Para ello se realiza una comprobación de colisión con los contornos de herramienta, lo que aporta seguridad adicional en la aplicación diaria. Al programa se antepone una breve calibración mediante la cual se registran las divergencias estáticas y térmicas actuales de la máquina. Estas se incluyen en la evaluación, lo que garantiza valores fiables comparables a los de las máquinas de medición. En las máquinas de 5 ejes, la calibración se realiza en los ángulos de incidencia de la sonda de contacto, en los que también se mide. De este modo, se obtiene con la evaluación una compensación automática de los errores rotacionales de los ejes 4o y 5o. Estos procedimientos de calibración están patentados por m&h. Los valores de medición están a disposición tanto en el modelo de superficie en la pantalla del ordenador, como también como archivo para su repro-ducción, guardado o impresión de protocolos en distintos formatos. “Nuestros clientes exigen cada vez más protocolos de medición, incluso para piezas fresadas relativamente sencillas, pero especialmente cuando se trata de contornos 3D”, explica Roland Tillmann, jefe responsable de construcción de dispositivos, mecánica de precisión, fabricación por encargo y calibres en Dörr. “Nuestros encargos son a menudo de carácter urgente“, explica Roland Tillmann. “A menudo fabricamos las piezas en solo 2 ó 3 días”. Esto es posible, porque las piezas de trabajos son en su mayoría de aluminio y raramente de aceros o plásticos de modelado. Resulta muy práctico que 3D Form Inspect pueda utilizarse con solo una licencia de software en varias máquinas, también de distintos tipos y fabricantes. Además Dörr también es muy flexible, no requiere soltar las piezas de trabajo de su fijación.
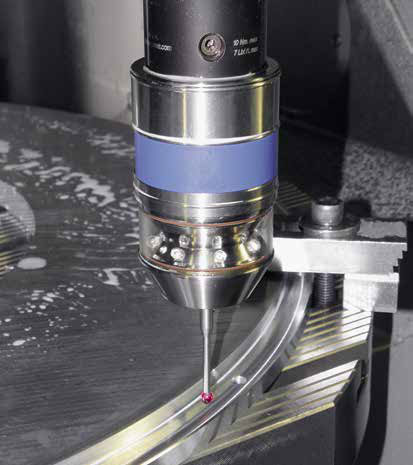
Servirá de ayuda la fácil manejabilidad del software 3D Form Inspect, que ha sido desarrollado específicamente para utilización en el taller. Con los menús desplegables y los iconos permite un manejo real- mente intuitivo. Cuando se selecciona una función en un punto de la pieza de trabajo, el software busca automáticamente el contrapunto preciso correspondiente que hace que la medición sea absolutamente fiable y sin errores. Antes de la autorización del programa en la máquina, este realiza una simulación que en caso de duda representa cuándo no puede ejecutarse una función seleccionada. El sistema fue programado durante la instalación in situ. “Después del primer día ya pudimos medir la primera pieza de trabajo en la máquina sin tener que esperar a la máquina de medición“, afirma contento Roland Tillmann. “Además, hemos ganado en seguridad“ añade. “Antes medíamos manualmente y los puntos deseados solo se lograban de modo aproximado. Ahora abordamos los puntos de modo preciso con la sonda de contacto. Y hemos acabado con los errores de lectura en la galga”. La seguridad adquirida y el tiempo ganado, a pesar del breve tiempo invertido para la medición, hacen que el sistema sea muy valioso para la empresa. “El breve tiempo para la medición no supone ningún handicap. Mucho peor sería que las piezas no fuesen correctas y que los clientes no estuvieran satisfechos” remarca Roland Tillmann.