Simply reliable
Contact us

Large turning/milling centres with a large number of machine components are the metier of Weingärtner Maschinenbau. Radio-wave touch probes from m&h check the accuracy of the machining operations.
Founded in 1966, the family-run business on the edge of the Austrian Salzkammergut can look back a long tradition in the manufacturing of large machines and turning/ milling centres and for machining and turning screws and rotors for compressors and extruders of widely varying type, as well as tubes and rollers, along with drive screws for boring heads and other special workpieces.
In the meantime approx. 200 employees not only build the machines, they also provide comprehensive service to the customer, starting from planning, through installation, to the maintenance of the machines at the customer. Everything that has a thread or screw-like contours appears predestined for machining on the machines from Weingärtner Maschinenbau.
It is not only the customer’s workpieces that are big, the machines from Weingärtner are large specimens, they are mostly very long and it is not unusual for them to be unique. The quality of the machining and the accuracy that can be achieved during the machining operations are correspondingly important. After all, in case of scrap, new parts are not only expensive, they also mostly involve a significant delay. So functional, reliable monitoring of the machining accuracy and ensuring correct positions and fits are all the more important.
For this reason at an early stage Weingärtner sought touch probes that were not only able to withstand the harsh environment in the turning/milling centre, but that also provide dependably exact measurement results, even at large distances and inside workpieces with recesses. During trials it soon became clear that the touch probes from m&h represent the best solution for Weingärtner. The sensing behaviour of the probes was predestined for the machine tool and the so-called trigger values were significantly more consistent than on competitor products.
Then as m&h became the first manufacturer to place a touch probe with RF data transmission on the market, the decision for this product was almost inevitable. At these large distances in the machines direct optical contact, as required for the more economical infrared data transmission, is often not ensured. Furthermore, the machines of modular design from Weingärtner are, depending on the application, equipped with a very wide range of machining components, ranging from tailstocks and steadies to the swivel unit; these components also represent obstacles for infrared data transmission, however they are of no consequence for RF data transmission. Even measuring inside the workpiece is possible, because the radio waves travel out of the workpieces to the receiver without delay. Right from the start m&h has used the protected industrial waveband at 433 MHz on which 64 channels are available. Highly developed and continuously improved electronics ensure high reception and transmission performance so that reliable data transmission is safeguarded even under extreme conditions, and so that unnecessary machine downtimes due to inadequate signals or the like are avoided.
Reliable RF signals ensure precision in large machines.The receiver installed outside the machine is connected to the control via a cable and contains all the necessary electrical devices and interfaces in its small housing, which in general is mounted on the machine’s enclosure. The entire time the machine is switched on it monitors all channels for interference and recommends to the fitter or machine operator which channel to use. The channel can be selected at the simple press of button. Channels on which significant interference is received are automatically inhibited to prevent malfunctions. This simple method without time-consuming synchronisation is particularly highly valued by the electrical department at Weingärtner, because the installation of the touch probe is very straightforward and correspondingly quick.
The good function of the probes is also confirmed by the organisation’s customers: since Weingärtner started supplying m&h touch probes as standard also to its customers abroad, there has not been any negative feedback from the customers according to the organisation.
The receiver is connected to an antenna, which as a rule protrudes into the machine’s working area above the headstock. However, as the antenna is subject to coolants, vapours and flying chips in this position, m&h has designed the antenna (optional) in stainless steel. The same applies to the body of the touch probe. Sealing to the IP68 standard also makes the probe insensitive to the harsh ambient conditions inside the machine tool. After all the touch probe must reliably and accurately transfer its data to the control without delay on every request.
Weingärtner can confirm from its own experience that the probe does just that. The same touch probes are used on a large number of machine tools in the organisation’s own factory with around 90% vertical integration. RF data transmission is also necessary on these machines with machining lengths of up to 15 metres. Weingärtner can therefore confirm that no spurious signals that could cause interference are emitted by the touch probes even on adjacent machines.
Weingärtner has also willingly taken on board the continuous further developments from m&h. For instance today’s probes have significantly lower power consumption than many years ago at the start. The straightforward battery change is no longer an issue these days, as it is only necessary on rare occasions. Depending on the probe type, the battery compartment can be opened with a few actions without the need for tools and the commercially available battery replaced in a few seconds. The indicators on the receiver indicate the current status of the probe to the operator at any time and signal that a battery change is necessary before the battery is completely exhausted.
Another product feature on the newer touch probes from m&h praised by Weingärtner is the measuring mechanism that can be unscrewed and the modular design of the probe. Rod-shaped extensions with a diameter of 25 mm are available in various lengths; these are screwed into the body of the probe instead of the measuring mechanism. They can also be screwed to each other as required and the measuring mechanism screwed to the end. The extensions screwed together in this manner retain their stiffness due to the matching contact faces between the modules. These extensions are also manufactured in stainless steel. At the same time internal contacts, which are gold-plated, ensure a reliable electrical contact and as a result reliable signal transmission. As the measuring mechanism is fitted to the end of the extensions, it is closer to the measuring point and ensures the same sampling behaviour and the same accuracy, independent of the projection required. In this way a very slender probe can be inserted deep in the workpiece with familiar accuracy and almost without risk of collision, or it is possible to measure significantly closer to side walls than was the case in the past.
Founded in 1966, the family-run business on the edge of the Austrian Salzkammergut can look back a long tradition in the manufacturing of large machines and turning/ milling centres and for machining and turning screws and rotors for compressors and extruders of widely varying type, as well as tubes and rollers, along with drive screws for boring heads and other special workpieces.
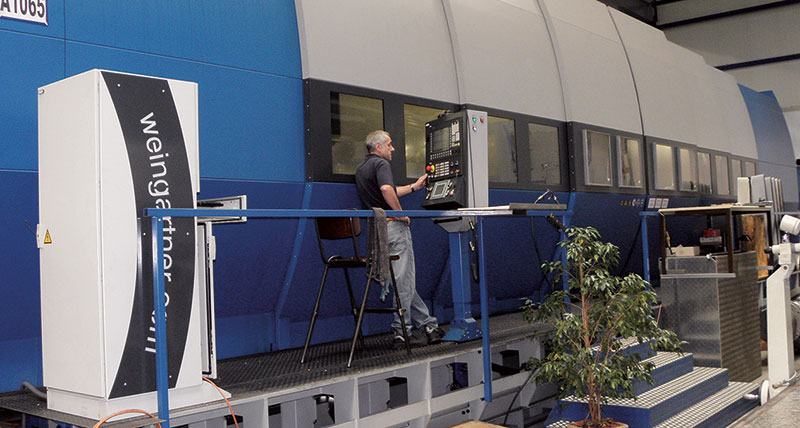
It is not only the customer’s workpieces that are big, the machines from Weingärtner are large specimens, they are mostly very long and it is not unusual for them to be unique. The quality of the machining and the accuracy that can be achieved during the machining operations are correspondingly important. After all, in case of scrap, new parts are not only expensive, they also mostly involve a significant delay. So functional, reliable monitoring of the machining accuracy and ensuring correct positions and fits are all the more important.
For this reason at an early stage Weingärtner sought touch probes that were not only able to withstand the harsh environment in the turning/milling centre, but that also provide dependably exact measurement results, even at large distances and inside workpieces with recesses. During trials it soon became clear that the touch probes from m&h represent the best solution for Weingärtner. The sensing behaviour of the probes was predestined for the machine tool and the so-called trigger values were significantly more consistent than on competitor products.
Then as m&h became the first manufacturer to place a touch probe with RF data transmission on the market, the decision for this product was almost inevitable. At these large distances in the machines direct optical contact, as required for the more economical infrared data transmission, is often not ensured. Furthermore, the machines of modular design from Weingärtner are, depending on the application, equipped with a very wide range of machining components, ranging from tailstocks and steadies to the swivel unit; these components also represent obstacles for infrared data transmission, however they are of no consequence for RF data transmission. Even measuring inside the workpiece is possible, because the radio waves travel out of the workpieces to the receiver without delay. Right from the start m&h has used the protected industrial waveband at 433 MHz on which 64 channels are available. Highly developed and continuously improved electronics ensure high reception and transmission performance so that reliable data transmission is safeguarded even under extreme conditions, and so that unnecessary machine downtimes due to inadequate signals or the like are avoided.
Reliable RF signals ensure precision in large machines.The receiver installed outside the machine is connected to the control via a cable and contains all the necessary electrical devices and interfaces in its small housing, which in general is mounted on the machine’s enclosure. The entire time the machine is switched on it monitors all channels for interference and recommends to the fitter or machine operator which channel to use. The channel can be selected at the simple press of button. Channels on which significant interference is received are automatically inhibited to prevent malfunctions. This simple method without time-consuming synchronisation is particularly highly valued by the electrical department at Weingärtner, because the installation of the touch probe is very straightforward and correspondingly quick.
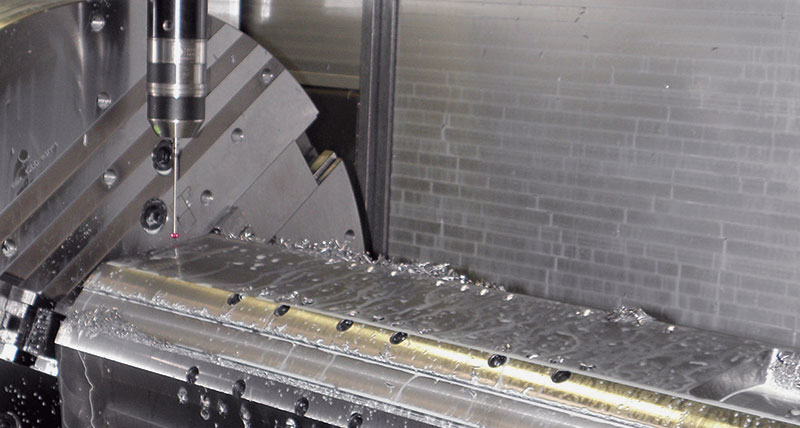
The receiver is connected to an antenna, which as a rule protrudes into the machine’s working area above the headstock. However, as the antenna is subject to coolants, vapours and flying chips in this position, m&h has designed the antenna (optional) in stainless steel. The same applies to the body of the touch probe. Sealing to the IP68 standard also makes the probe insensitive to the harsh ambient conditions inside the machine tool. After all the touch probe must reliably and accurately transfer its data to the control without delay on every request.
Weingärtner can confirm from its own experience that the probe does just that. The same touch probes are used on a large number of machine tools in the organisation’s own factory with around 90% vertical integration. RF data transmission is also necessary on these machines with machining lengths of up to 15 metres. Weingärtner can therefore confirm that no spurious signals that could cause interference are emitted by the touch probes even on adjacent machines.
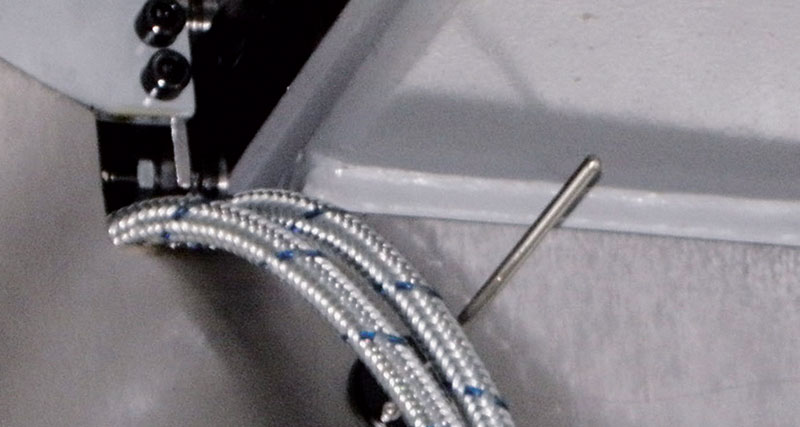
Another product feature on the newer touch probes from m&h praised by Weingärtner is the measuring mechanism that can be unscrewed and the modular design of the probe. Rod-shaped extensions with a diameter of 25 mm are available in various lengths; these are screwed into the body of the probe instead of the measuring mechanism. They can also be screwed to each other as required and the measuring mechanism screwed to the end. The extensions screwed together in this manner retain their stiffness due to the matching contact faces between the modules. These extensions are also manufactured in stainless steel. At the same time internal contacts, which are gold-plated, ensure a reliable electrical contact and as a result reliable signal transmission. As the measuring mechanism is fitted to the end of the extensions, it is closer to the measuring point and ensures the same sampling behaviour and the same accuracy, independent of the projection required. In this way a very slender probe can be inserted deep in the workpiece with familiar accuracy and almost without risk of collision, or it is possible to measure significantly closer to side walls than was the case in the past.