Portability and flexibility for maximum time savings
The perfect combination of CMM and measuring arm meets increasingly tight tolerances of larger and larger components.
Contact us

Construction Mécanique Badimon (CMB) is a family business specialised for over 30 years in the precision machining of mechanical parts of all sizes. Located in the southwest of France in Lavelanet, CMB employs about thirty people. Proudly certified to ISO 9001/EN 9100, the company has the means and the ability to produce high-quality outputs including tools, prototype parts, parts under pre-production and parts in small, medium and large series. The structure of the business supports activities across research, realisation, assembly and control.
Milling, turning, flat grinding, fitting, reaming, throughput, welding, tool storage and raw material storage are the main services offered today by CMB. These applications are applied across the wide range of sectors with which CMB has been involved throughout its development, such as aerospace, railways, petrochemicals, machining, medical and agriculture. Customers in these industries come to CMB from the four corners of France as well as from overseas.
There is great variety in the pieces produced at CMB. Parts regularly exceed one metre in size and can weigh in at several tons. The company processes all types of materials, from aluminium and steel to alloys and plastics, but also super alloys such as Inconel or titanium. CMB is proud of its technology toolkit, which is not only an integral part of its day-to-day work, but also enables it to respond to new constraints related to the use of new materials.
As the orders processed by the company are very specific – CMB often delivers very small series or even single units – margins of error are very small, especially for parts that initially have a high market value. It is therefore necessary for the company to be as precise as possible in the manufacture of its parts.
The experience, patience and tenacity of our Hexagon contact were decisive in our contacting him again. At the same time, customer demand has increased in recent years, particularly with regard to quality control, and the majority of requests go in the same direction. “Our main client asks more and more for us to perform control of form. In fact, they do not ask us for any coordinates of points with “GO – NO GO”, but instead now work with only colour cartographies,” says CMB Quality Manager Thierry Bizet. “The client wants to see ‘green’ everywhere on the piece and no areas that come out of tolerance. It’s a lot more than merely taking aligned points now.”
At the end of 2015, CMB acquired a Hexagon coordinate measuring machine (CMM) in order to meet the finer tolerances increasingly required by their clients. Already the owner of a measuring arm, the increasing dimensions of the parts to be controlled created the need for a larger instrument that includes scanner technology. This would allow for the collection of point-cloud data and offer significant time savings compared to point-by-point measurements. CMB quickly turned to Hexagon for an Absolute Arm with integrated scanner in early January 2018.
The arm perfectly meets the quality control needs of the company, and in doing so shapes the impact of their measurement processes. “This technology saves considerable time – in the order of 50 percent of working time,” says Bizet. “On an engraving, for example, the measurement time is reduced from 30 to only 15 minutes.”
The company benefits from a department dedicated to quality control. This team defines sampling procedures and, depending on the type of part to be controlled, they will adapt the means to be used. As the dimensions and weight of the manufactured parts become more complex, the Absolute Arm will regularly have to be moved directly to the machines on the production floor to take measurements. It is for this reason that the portability of the measuring arm and its adaptability to different environments represents a real benefit for the company.
In the future, CMB intends to make more use of the Absolute Arm system’s integrated scanner: “With all the possibilities that the scanner offers, we will be able to develop our services and better respond to certain customer requests, especially in terms of reverse engineering,” says the quality manager.
The company also expects to increase the size of the parts it can process as it continues to reach further to meet the growing demands of its customers, “The evolution of CMB will really be based on the high-tech tools that drive our technological development,” says Bizet.
Today, the arm is sufficient in terms of tolerances, and the scan technology is not yet applied in all its capabilities. But one thing is certain; in a few years, CMB intends to invest in a second arm from Hexagon.


As the orders processed by the company are very specific – CMB often delivers very small series or even single units – margins of error are very small, especially for parts that initially have a high market value. It is therefore necessary for the company to be as precise as possible in the manufacture of its parts.
The experience, patience and tenacity of our Hexagon contact were decisive in our contacting him again. At the same time, customer demand has increased in recent years, particularly with regard to quality control, and the majority of requests go in the same direction. “Our main client asks more and more for us to perform control of form. In fact, they do not ask us for any coordinates of points with “GO – NO GO”, but instead now work with only colour cartographies,” says CMB Quality Manager Thierry Bizet. “The client wants to see ‘green’ everywhere on the piece and no areas that come out of tolerance. It’s a lot more than merely taking aligned points now.”
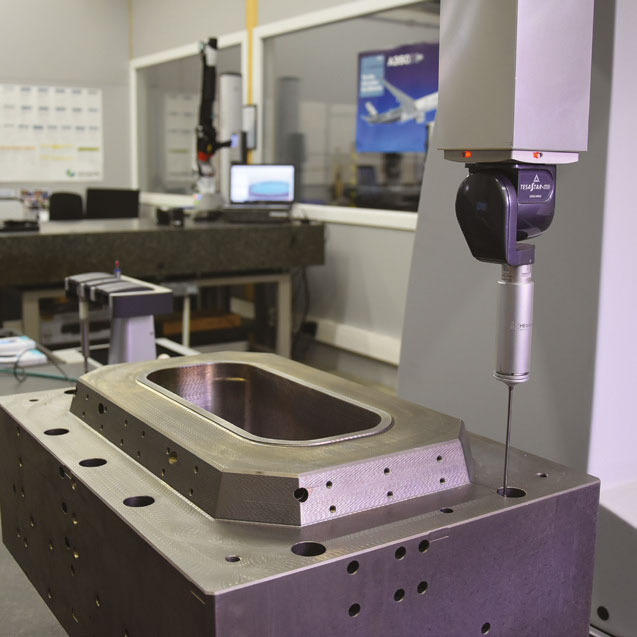
Time savings estimated at 50 percent
At the end of 2015, CMB acquired a Hexagon coordinate measuring machine (CMM) in order to meet the finer tolerances increasingly required by their clients. Already the owner of a measuring arm, the increasing dimensions of the parts to be controlled created the need for a larger instrument that includes scanner technology. This would allow for the collection of point-cloud data and offer significant time savings compared to point-by-point measurements. CMB quickly turned to Hexagon for an Absolute Arm with integrated scanner in early January 2018.The arm perfectly meets the quality control needs of the company, and in doing so shapes the impact of their measurement processes. “This technology saves considerable time – in the order of 50 percent of working time,” says Bizet. “On an engraving, for example, the measurement time is reduced from 30 to only 15 minutes.”
The company benefits from a department dedicated to quality control. This team defines sampling procedures and, depending on the type of part to be controlled, they will adapt the means to be used. As the dimensions and weight of the manufactured parts become more complex, the Absolute Arm will regularly have to be moved directly to the machines on the production floor to take measurements. It is for this reason that the portability of the measuring arm and its adaptability to different environments represents a real benefit for the company.

A future of quality
In the future, CMB intends to make more use of the Absolute Arm system’s integrated scanner: “With all the possibilities that the scanner offers, we will be able to develop our services and better respond to certain customer requests, especially in terms of reverse engineering,” says the quality manager.The company also expects to increase the size of the parts it can process as it continues to reach further to meet the growing demands of its customers, “The evolution of CMB will really be based on the high-tech tools that drive our technological development,” says Bizet.
Today, the arm is sufficient in terms of tolerances, and the scan technology is not yet applied in all its capabilities. But one thing is certain; in a few years, CMB intends to invest in a second arm from Hexagon.