Metrological assets for precision machining
MPEB - France
Contact us
MPEB case study
MPEB is part of the LLEDO Industries Group and has specialised in the precision machining of mechanical parts and equipment since 1989, notably in the aeronautics, nuclear, optical, medical and microelectronics industries.
Ever since it was founded, the group has consciously decided to develop its industrial operations in the mechanics and machining sector. Starting with conventional machines, the company has now become a benchmark for tooling in the Provence-Alpes-Côte d’Azur.
The LLEDO Industries Group has reinforced this expertise by progressively integrating new technological knowledge as client demand developed. The growing need for control reports, especially for shapes with progressive radii, necessitated the purchase of a higher-performance, highprecision metrological instrument.
The Managing Director of the MPEB factory, Daniel Campanella, explains: “We started by making moulds and then moved on to aeronautical qualifications, critical parts and prototypes. Three-dimensional measuring machines provided us with extremely precise measurements, but they could not be moved.”
“The ideal way to avoid errors is to have a mobile, precise, easy-to-use measuring method”, adds Carole Parmentier, Head of the Quality Department at MPEB. This is why the company, which already had a Hexagon Manufacturing Intelligence TESA Micro-Hite, acquired a ROMER Multi Gage and then a ROMER Absolute Arm Compact.
“The ROMER Absolute Arm is great because it combines the three criteria above (mobility, precision and ease of use) and it works alongside other measuring machines”, adds Parmentier.
“If we were to have to buy another measuring instrument, it would be a ROMER Absolute Arm, as the operators are already familiar with the technology and this results in increased ease of operation and flexibility between operators. They are then able to work on all machines, which means increased productivity for us. After all, ‘technology drives productivity’. With the Hexagon measuring arm, it’s easy to collect information in real time, scan it and digitalise a part. It’s a real all-in-one tool”, concludes Campanella. Easy to use and ultra-mobile, the arm delivers extremely fast results.
Ever since it was founded, the group has consciously decided to develop its industrial operations in the mechanics and machining sector. Starting with conventional machines, the company has now become a benchmark for tooling in the Provence-Alpes-Côte d’Azur.
The LLEDO Industries Group has reinforced this expertise by progressively integrating new technological knowledge as client demand developed. The growing need for control reports, especially for shapes with progressive radii, necessitated the purchase of a higher-performance, highprecision metrological instrument.
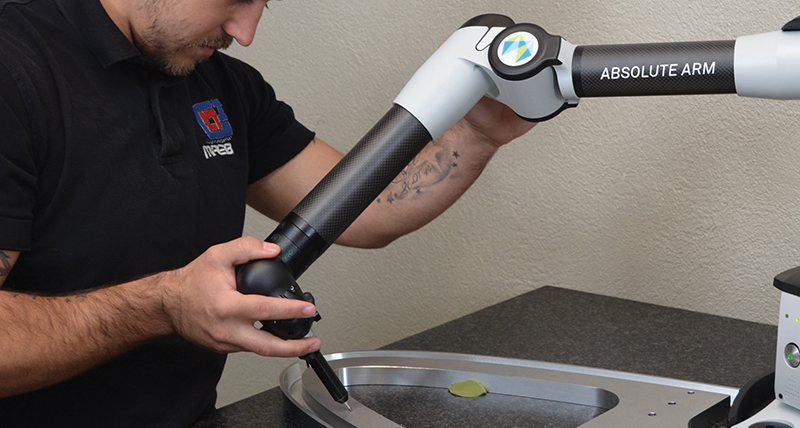
“The ideal way to avoid errors is to have a mobile, precise, easy-to-use measuring method”, adds Carole Parmentier, Head of the Quality Department at MPEB. This is why the company, which already had a Hexagon Manufacturing Intelligence TESA Micro-Hite, acquired a ROMER Multi Gage and then a ROMER Absolute Arm Compact.
“The ROMER Absolute Arm is great because it combines the three criteria above (mobility, precision and ease of use) and it works alongside other measuring machines”, adds Parmentier.
“If we were to have to buy another measuring instrument, it would be a ROMER Absolute Arm, as the operators are already familiar with the technology and this results in increased ease of operation and flexibility between operators. They are then able to work on all machines, which means increased productivity for us. After all, ‘technology drives productivity’. With the Hexagon measuring arm, it’s easy to collect information in real time, scan it and digitalise a part. It’s a real all-in-one tool”, concludes Campanella. Easy to use and ultra-mobile, the arm delivers extremely fast results.