Measuring milling and eroding accuracy
Contact us

Measuring parts in machining centres is state-of-the-art. m&h software and measuring probes also enable an immediate target/ performance comparison on eroding machines. Here, Engesser Formenbau tells us about its positive experiences and considerable time savings thanks to a harmonious production process.
It is often claimed that measuring in the tool setter is simply unproductive time, but Geisingen-based Engesser Formenbau always finds the opposite.
Parts are not only checked on two machining centres, but also on two vertical eroding machines with measuring probes before their tension is released. Parts are measured both in HSC machining centres and in the vertical eroding machine in the interlinked Zimmer & Kreim production cell using m&h measuring probes and software. “We check every part before it comes out of the machine,” explains Holger Gassenschmidt, Head of Mould Making at Engesser. “The tension on a part is only released when it has been rated as ‘OK’.” This ensures reliability in production and also measuring protocols for every component without any time-consuming diversion to the measuring machine.
At Engesser, 25 employees currently manufacture around 70-80 moulds per year. These moulds can be signed off in their own research facilities. Pilot series are also often made for customers before they take over the mould and process. Its injection moulding machines produce up to 275t of clamping force and handle shot weights of up to 400g. In total, around 70 employees work on the production of prefinished series parts at Engesser, including pre-mounted assemblies and components for a range of different industry sectors.
Alongside injection moulds, Engesser also produces moulds for processing silicone and rubber as well as overmoulding stored parts. Moulds are only part of in-house production. A much larger proportion is dedicated to contract production for other customers. Engesser is also a contractor for milling, turning, eroding, deep drilling and grinding (surface grinding, circular grinding, profile grinding and coordinate grinding). The majority of operations consist of updating existing moulds or reworking moulds that were originally made in third-party countries. This is a multifaceted environment that requires a high degree of both flexibility and accuracy. The quantity of moulds and mould inserts at Engesser is typically only one per order. The required tolerance ranges often vary by around 10μm.
In order to ensure this level of accuracy, m&h Hexagon measuring probes and software have been used for more than eight years. The measuring probes have infrared data transmission with HDR technology, which has proven to be extremely reliable, even under difficult conditions both in machining centres and in eroding machines.
m&h Hexagon 3D Form Inspect software makes it easy to create measuring programmes on the computer in the workshop. The software converts workshop CAD data into a surface model and the part is displayed with its target values. A few clicks of the mouse is all it takes for the operator to set the points, surfaces or geometries to be measured and allocate them the desired measuring capabilities. In the background, 3D Form Inspect writes the corresponding positioning programme for the measuring probe. Where possible, the exact counterpoints for the measurement are independently determined by the software, which excludes the possibility of erroneous measurements due to operator inaccuracy. The software knows the dimensions of all m&h measuring probes and carries out the calculations in the background while the measuring capabilities and the required positioning are automatically determined. An on-screen simulation displays the movements of the measuring probe and an automatic collision check is carried out with the part. Probing points that would result in a collision between parts of the measuring probe and the part are automatically excluded and displayed. This on-screen simulation results in a machine programme being automatically written into the software in accordance with the relevant post processor. This software process ensures maximum operational safety with extremely simple, fast programming.
Probing the measuring points in the machine generates a new programme, which is transmitted back to the operator’s computer. This contains the measured values, which are immediately integrated into the on-screen image of the part. The machine operator then immediately knows whether the part in any way deviates from its target values and the software can show him/her whether it remains within the tolerance range or not by means of colour coding. As the part is still subject to tension, the operator can react immediately and, if necessary, improve or rework sections of the part through tool correction or another processing method.
We work faster and more accurately and we also always have a measuring protocol,With every measurement, 3D Form Inspect automatically generates a measurement protocol, which is then printed and/or saved. “Only when a part is rated ‘OK’ is the tension released,” explains Holger Gassenschmidt about the process at Engesser. All grinding surfaces have been set to zero for some time. Contour points, fittings and free-form surfaces are generally measured at Engesser. Partitions worked into the mould are checked and only then is the tension released. Machine operators at Engesser are operators and programmers rolled into one. They also create measuring programmes with help from 3D Form Inspect. This means that all responsibility for the part lies with the person on the machine and he/she can decide whether contours must be reset. At the same time, he/she can verify the resulting accuracy at any time by means of a measuring protocol.
“This hugely reduces the effort required. The measuring flexibility has enabled us to considerably reduce our lead times. ,” exclaims Holger Gassenschmidt, adding that the tension used to be released from the parts before measuring, whereby the tension had to be restored before any changes could be made. This resulted in a loss of both time and precision. There was also often a bottleneck when it came to the measuring process. Holger Gassenschmidt continues: “Our assembly times have been hugely reduced. Parts are now truly assembly-ready. Grinding times are down too. Parts are put together, spotted and correct. We have to do a lot less reworking now.”
Machine operators confirm the ease of use of m&h 3D Form Inspect software and praise the good technology training they received recently at the m&h Hexagon Technology Centre to refresh their knowledge. They were pleased to discover that it was not a typical promotional event; it really did involve technology and operator training.
“We can no longer imagine working without 3D Form Inspect,” says Gassenschmidt. It only takes a few minutes to measure a part in the machine now, whereas parts often used to come back from the assembly needing urgent reworking. The machine wasn’t often free, which meant that other work had to be interrupted or postponed. “The measuring time in the machine doesn’t make us unproductive,” adds Holger Gassenschmidt. “This time is recovered and then some in assembly and grinding. Our throughput is much more harmonious now. We work faster and more accurately and we also always have a measuring protocol. And that doesn’t just apply to our machining centres, but for our eroding machines too.”
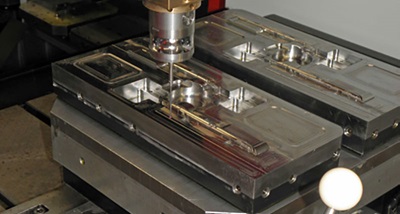
Parts are not only checked on two machining centres, but also on two vertical eroding machines with measuring probes before their tension is released. Parts are measured both in HSC machining centres and in the vertical eroding machine in the interlinked Zimmer & Kreim production cell using m&h measuring probes and software. “We check every part before it comes out of the machine,” explains Holger Gassenschmidt, Head of Mould Making at Engesser. “The tension on a part is only released when it has been rated as ‘OK’.” This ensures reliability in production and also measuring protocols for every component without any time-consuming diversion to the measuring machine.
At Engesser, 25 employees currently manufacture around 70-80 moulds per year. These moulds can be signed off in their own research facilities. Pilot series are also often made for customers before they take over the mould and process. Its injection moulding machines produce up to 275t of clamping force and handle shot weights of up to 400g. In total, around 70 employees work on the production of prefinished series parts at Engesser, including pre-mounted assemblies and components for a range of different industry sectors.

In order to ensure this level of accuracy, m&h Hexagon measuring probes and software have been used for more than eight years. The measuring probes have infrared data transmission with HDR technology, which has proven to be extremely reliable, even under difficult conditions both in machining centres and in eroding machines.

Probing the measuring points in the machine generates a new programme, which is transmitted back to the operator’s computer. This contains the measured values, which are immediately integrated into the on-screen image of the part. The machine operator then immediately knows whether the part in any way deviates from its target values and the software can show him/her whether it remains within the tolerance range or not by means of colour coding. As the part is still subject to tension, the operator can react immediately and, if necessary, improve or rework sections of the part through tool correction or another processing method.
We work faster and more accurately and we also always have a measuring protocol,With every measurement, 3D Form Inspect automatically generates a measurement protocol, which is then printed and/or saved. “Only when a part is rated ‘OK’ is the tension released,” explains Holger Gassenschmidt about the process at Engesser. All grinding surfaces have been set to zero for some time. Contour points, fittings and free-form surfaces are generally measured at Engesser. Partitions worked into the mould are checked and only then is the tension released. Machine operators at Engesser are operators and programmers rolled into one. They also create measuring programmes with help from 3D Form Inspect. This means that all responsibility for the part lies with the person on the machine and he/she can decide whether contours must be reset. At the same time, he/she can verify the resulting accuracy at any time by means of a measuring protocol.

Machine operators confirm the ease of use of m&h 3D Form Inspect software and praise the good technology training they received recently at the m&h Hexagon Technology Centre to refresh their knowledge. They were pleased to discover that it was not a typical promotional event; it really did involve technology and operator training.
“We can no longer imagine working without 3D Form Inspect,” says Gassenschmidt. It only takes a few minutes to measure a part in the machine now, whereas parts often used to come back from the assembly needing urgent reworking. The machine wasn’t often free, which meant that other work had to be interrupted or postponed. “The measuring time in the machine doesn’t make us unproductive,” adds Holger Gassenschmidt. “This time is recovered and then some in assembly and grinding. Our throughput is much more harmonious now. We work faster and more accurately and we also always have a measuring protocol. And that doesn’t just apply to our machining centres, but for our eroding machines too.”