Misurazione della precisione di fresatura ed erosione
Contattateci

La misurazione dei pezzi nel centro di lavorazione
oggi è allo stato della tecnica. Con i software e
i tastatori di misura di m&h è possibile eseguire un
confronto valore nominale-effettivo immediato
anche nelle macchine per elettroerosione. La ditta
produttrice di stampi Engesser ha riferito delle
ottime esperienze e un notevole risparmio di tempo
con un procedimento di produzione armonizzata.
Spesso si afferma che la misurazione nelle macchine
utensili è soltanto tempo sprecato, non produttivo. Presso
la ditta produttrice di stampi Engesser a Geisingen esiste
la controprova.
Qui i pezzi non solo vengono controllati in due centri di lavorazione, ma anche in due macchine per elettroerosione con tastatori di misura, prima che vengano staccati dal serraggio. I pezzi vengono misurati sia nella cella di produzione a catena di Zimmer & Kreim, sia nel centro di lavorazione HSC, sia nella macchina per elettroerosione con tastatori di misura e software di m&h. “Controlliamo ogni pezzo prima che arrivi dalla macchina” spiega Holger Gassenschmidt, capo responsabile nella produzione di stampi di Engesser. “Un componente viene allentato soltanto se è “OK”.” Ciò infonde sicurezza alla produzione e, come effetto secondario, al protocollo di misura di ogni componente, senza i lunghi tragitti alla macchina di misura.
Nella produzione di stampi di Engesser i 25 collaboratori producono al momento da 70 a 80 stampi all’anno. Questi stampi possono essere realizzati come modello con la propria tecnica. Spesso per i clienti vengono realizzate anche delle serie pilota, prima di passare ai clienti lo stampo e il processo. Le macchine di stampaggio a iniezione interne arrivano fino a 275 t di forza di chiusura e lavorano delle quantità fino a 400 g. In totale presso Engesser vengono occupati circa 70 collaboratori nella produzione dei componenti di serie pronti al montaggio, inclusi i gruppi costruttivi prefabbricati e i componenti per i differenti rami industriali.
Nella produzione di stampi Engesser, oltre agli stampi a iniezione vengono prodotti anche stampi per la lavorazione di silicone o caucciù, oltre che per l’iniezione di componenti innestati. Gli stampi servono solo in parte per la produzione interna. La maggior parte viene realizzata su richiesta per altri clienti. Inoltre, Engesser offre anche, su compenso, operazioni nei settori di fresatura, rotazione, erosione ma anche perforatura di profondità e molatura (molatura piatta, rotonda, profilata e con coordinate). La maggior parte dei lavori sono dei servizi di modifica di stampi già esistenti o una ripassatura di stampi che in origine erano stati prodotti in altri Paesi. Quindi un campo lavorativo versatile che richiede elevate flessibilità e precisione. Normalmente, il numero di pezzi degli stampi e di impieghi degli stampi presso Engesser è di solo uno per ordine. I campi di tolleranza richiesti spesso oscillano di circa 10 μm.
Per assicurare questa precisione, vengono impiegati già da oltre otto anni i tastatori di misura e i software di m&h-Hexagon. I tastatori di misura sono dotati di una trasmissione dati a infrarossi con tecnologia HDR (High-Data-Rate), che si è dimostrata altamente sicura per i processi, anche nelle condizioni ambientali più estreme, sia nei centri di lavorazione, sia nelle macchine per elettroerosione.
Per l’esecuzione semplice dei programmi di misura sul computer in officina è utile il software 3D Form Inspect di m&h Hexagon. In questo software i dati CAD dei pezzi vengono convertiti in un modello di superficie e il pezzo viene rappresentato con i suoi valori nominali. Con pochi clic del mouse l’operatore della macchina è in grado di determinare i punti, le superfici o le geometrie da misurare e assegnare a
questi ultimi le funzioni di misura desiderate. Il programma 3D
Form Inspect scrive in background il programma di processo
corrispondente per il tastatore di misura. A tale proposito
i contropunti precisi per la misurazione vengono rilevati
autonomamente dal software in modo preciso, dove possibile,
escludendo così delle misurazioni errate dovute alla precisione
di comando. Il software riconosce le dimensioni di tutti i
tastatori di m&h e calcola automaticamente in background,
durante la determinazione delle funzioni di misura, i processi
necessari. Durante una simulazione sullo schermo vengono
rappresentati i movimenti dei tastatori e viene eseguito un
controllo della collisione automatico con il pezzo. Le scansioni
che causerebbero una collisione di componenti del tastatore
con il pezzo vengono escluse automaticamente e indicate
in modo adeguato. Soltanto durante questa simulazione
sullo schermo nel software viene scritto automaticamente
il programma della macchina reale, in base al relativo postprocessor.
La modalità di lavoro del software garantisce la
massima sicurezza di esercizio con una programmazione molto
più semplice e rapida.
Durante la scansione dei punti di misura nella macchina, questa genera un nuovo programma che viene trasmesso di nuovo al computer dell’operatore. Questo contiene i valori misurati, che vengono immediatamente visualizzati nella raffigurazione dei pezzi sullo schermo. L’operatore della macchina riconosce subito se nel pezzo ci sono degli scostamenti dai valori nominali e il software è in grado di indicare con dei colori se i valori rientrano nei rispettivi intervalli di tolleranza o meno. Poiché il pezzo è sotto carico come in precedenza, l’operatore può reagire immediatamente ed eventualmente migliorare o modificare la lavorazione di aree parziali del pezzo con una correzione dell’utensile o altre modalità di lavorazione.
In generale lavoriamo più rapidamente, con maggiore precisione e abbiamo sempre anche un protocollo di misura, Con ogni misurazione, 3D Form Inspect genera automaticamente un protocollo di misura che viene stampato o memorizzato. “Soltanto se un pezzo è “OK”, viene messo sotto carico”, spiega Holger Gassenschmidt sul metodo di lavorazione presso Engesser. Qui già da lungo tempo tutte le superfici da ritoccare vengono fresate a “zero”. Per principio, presso Engesser i punti caratteristici della sagoma, gli aggiustaggi e le superfici senza matrice vengono misurati. Le separazioni inserite nello stampo vengono verificate e soltanto allora vengono allentate. Gli operatori delle macchine presso Engesser sono sia operai sia programmatori. Realizzano anche i programmi di misura con l’aiuto di 3D Form Inspect. In questo modo l’intera responsabilità del pezzo ricade sull’addetto alla macchina ed egli può decidere autonomamente se ritoccare le sagome. Allo stesso tempo, in ogni momento può dimostrare la precisione del prodotto finito con un protocollo di misura.
“Per noi questo è un gran risparmio di fatica. Grazie alla flessibilità nella misurazione abbiamo ridotto significativamente i tempi di risposta. ”, racconta Holger Gassenschmidt e spiega che in passato si doveva allentare il pezzo, eseguire la misurazione e poi di nuovo tensionare e continuare con la lavorazione. Ciò significava una perdita di tempo e precisione. Inoltre spesso la misurazione era difficile. Holger Gassenschmidt continua: “Anche i nostri tempi di montaggio si sono sensibilmente ridotti. I pezzi ora sono davvero pronti per il montaggio. I tempi di ritocco sono più brevi. Si esegue l’assemblaggio, il ritocco e basta. Le modifiche sono ormai molto rare.”
Gli operatori della macchina confermano la semplicità d’uso del software m&h - 3D Form Inspect e lodano l’ottimo corso di formazione sulla tecnologia che hanno completato recentemente nel centro tecnologico m&h - Hexagon, per ripassare le loro conoscenze. Questi ultimi hanno scoperto con piacere che non si tratta, come spesso accade, di un evento pubblicitario, ma davvero di un corso di addestramento sulla tecnologia e l’utilizzo.
“Non riusciamo più a immaginare come sarebbe lavorare senza 3D Form Inspect”, racconta Gassenschmidt. Addirittura adesso avanzano pochi minuti, nei quali si esegue la misurazione nella macchina, in passato spesso i pezzi, a causa della fretta, ritornavano indietro dal montaggio per essere modificati. In seguito di solito la macchina non era più libera e le altre operazioni dovevano essere interrotte o rimandate. “Il tempo impiegato per la misurazione non è del tutto improduttivo”, afferma Holger Gassenschmidt. “Questo tempo si moltiplica durante il montaggio e il ritocco. Il nostro procedimento oggi è molto più armonico. In generale lavoriamo più rapidamente, con maggiore precisione e abbiamo sempre anche un protocollo di misura. E questo non solo nei centri di lavorazione, ma anche sulle nostre macchine per elettroerosione.”
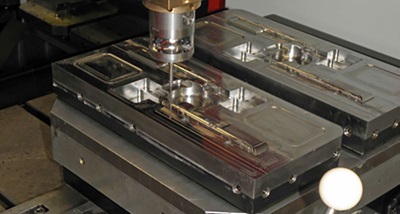
Qui i pezzi non solo vengono controllati in due centri di lavorazione, ma anche in due macchine per elettroerosione con tastatori di misura, prima che vengano staccati dal serraggio. I pezzi vengono misurati sia nella cella di produzione a catena di Zimmer & Kreim, sia nel centro di lavorazione HSC, sia nella macchina per elettroerosione con tastatori di misura e software di m&h. “Controlliamo ogni pezzo prima che arrivi dalla macchina” spiega Holger Gassenschmidt, capo responsabile nella produzione di stampi di Engesser. “Un componente viene allentato soltanto se è “OK”.” Ciò infonde sicurezza alla produzione e, come effetto secondario, al protocollo di misura di ogni componente, senza i lunghi tragitti alla macchina di misura.
Nella produzione di stampi di Engesser i 25 collaboratori producono al momento da 70 a 80 stampi all’anno. Questi stampi possono essere realizzati come modello con la propria tecnica. Spesso per i clienti vengono realizzate anche delle serie pilota, prima di passare ai clienti lo stampo e il processo. Le macchine di stampaggio a iniezione interne arrivano fino a 275 t di forza di chiusura e lavorano delle quantità fino a 400 g. In totale presso Engesser vengono occupati circa 70 collaboratori nella produzione dei componenti di serie pronti al montaggio, inclusi i gruppi costruttivi prefabbricati e i componenti per i differenti rami industriali.
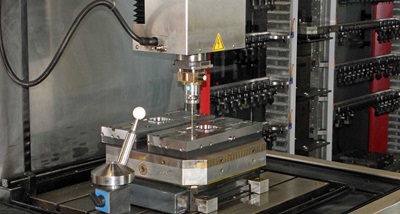
Per assicurare questa precisione, vengono impiegati già da oltre otto anni i tastatori di misura e i software di m&h-Hexagon. I tastatori di misura sono dotati di una trasmissione dati a infrarossi con tecnologia HDR (High-Data-Rate), che si è dimostrata altamente sicura per i processi, anche nelle condizioni ambientali più estreme, sia nei centri di lavorazione, sia nelle macchine per elettroerosione.
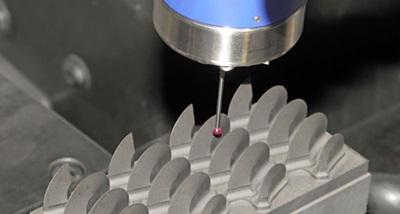
Durante la scansione dei punti di misura nella macchina, questa genera un nuovo programma che viene trasmesso di nuovo al computer dell’operatore. Questo contiene i valori misurati, che vengono immediatamente visualizzati nella raffigurazione dei pezzi sullo schermo. L’operatore della macchina riconosce subito se nel pezzo ci sono degli scostamenti dai valori nominali e il software è in grado di indicare con dei colori se i valori rientrano nei rispettivi intervalli di tolleranza o meno. Poiché il pezzo è sotto carico come in precedenza, l’operatore può reagire immediatamente ed eventualmente migliorare o modificare la lavorazione di aree parziali del pezzo con una correzione dell’utensile o altre modalità di lavorazione.
In generale lavoriamo più rapidamente, con maggiore precisione e abbiamo sempre anche un protocollo di misura, Con ogni misurazione, 3D Form Inspect genera automaticamente un protocollo di misura che viene stampato o memorizzato. “Soltanto se un pezzo è “OK”, viene messo sotto carico”, spiega Holger Gassenschmidt sul metodo di lavorazione presso Engesser. Qui già da lungo tempo tutte le superfici da ritoccare vengono fresate a “zero”. Per principio, presso Engesser i punti caratteristici della sagoma, gli aggiustaggi e le superfici senza matrice vengono misurati. Le separazioni inserite nello stampo vengono verificate e soltanto allora vengono allentate. Gli operatori delle macchine presso Engesser sono sia operai sia programmatori. Realizzano anche i programmi di misura con l’aiuto di 3D Form Inspect. In questo modo l’intera responsabilità del pezzo ricade sull’addetto alla macchina ed egli può decidere autonomamente se ritoccare le sagome. Allo stesso tempo, in ogni momento può dimostrare la precisione del prodotto finito con un protocollo di misura.
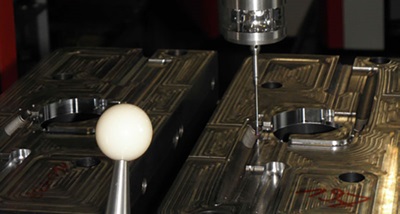
Gli operatori della macchina confermano la semplicità d’uso del software m&h - 3D Form Inspect e lodano l’ottimo corso di formazione sulla tecnologia che hanno completato recentemente nel centro tecnologico m&h - Hexagon, per ripassare le loro conoscenze. Questi ultimi hanno scoperto con piacere che non si tratta, come spesso accade, di un evento pubblicitario, ma davvero di un corso di addestramento sulla tecnologia e l’utilizzo.
“Non riusciamo più a immaginare come sarebbe lavorare senza 3D Form Inspect”, racconta Gassenschmidt. Addirittura adesso avanzano pochi minuti, nei quali si esegue la misurazione nella macchina, in passato spesso i pezzi, a causa della fretta, ritornavano indietro dal montaggio per essere modificati. In seguito di solito la macchina non era più libera e le altre operazioni dovevano essere interrotte o rimandate. “Il tempo impiegato per la misurazione non è del tutto improduttivo”, afferma Holger Gassenschmidt. “Questo tempo si moltiplica durante il montaggio e il ritocco. Il nostro procedimento oggi è molto più armonico. In generale lavoriamo più rapidamente, con maggiore precisione e abbiamo sempre anche un protocollo di misura. E questo non solo nei centri di lavorazione, ma anche sulle nostre macchine per elettroerosione.”