Mesure de la précision de fraisage et d’usinage
Contact

Le centre d’usinage dispose d’une technologie de
pointe en matière de mesure des pièces. Grâce à
l’utilisation de logiciels et de palpeurs de mesure de
m&h, il est possible de comparer immédiatement
l’état prévu et l’état final de la pièce dans la
machine. Le fabricant de moules Engesser présente
son expérience positive, ainsi que le gain de
temps permis grâce un processus de fabrication
harmonisé.
Les mesures prises dans la machine-outil sont souvent
considérées comme une perte de temps. Le fabricant de
moules Engesser, situé à Geisingen, réfute sans cesse
cette affirmation.
Les pièces y sont contrôlées non seulement à deux centres d’usinage, mais également sur deux machines d’électroérosion par enfonçage équipées de palpeurs de mesure, avant d’être relâchées par l’outil de serrage. Les pièces sont mesurées à l’aide de palpeurs et de logiciels de m&h dans les centres d’usinage HSC, ainsi que dans la machine d’électroérosion par enfonçage, et ce même dans la cellule d’usinage Zimmer & Kreim. « Nous vérifions chaque pièce avant qu’elle sorte de la machine », explique Holger Gassenschmidt, contremaître responsable de la fabrication de moule chez Engesser. « Une pièce n’est relâchée que lorsqu’elle est considérée comme conforme ». Cela permet de sécuriser l’usinage et d’établir des protocoles de mesure pour chaque élément, tout en évitant une perte de temps dû à un passage dans une machine de mesure.
Actuellement, 25 collaborateurs usinent environ 70 à 80 moules par an chez Engesser. Ces derniers peuvent être échantillonnés au sein du centre technique. Des lots pilotes sont souvent fabriqués avant que les moules et les processus ne soient transférés au client. Les machines de moulage à injection fournissent une force de verrouillage allant jusqu’à 275 t et peuvent traiter des poids injectables jusqu’à 400 g. Chez Engesser, environ 70 collaborateurs travaillent dans l’usinage de pièces fabriquées en série prêtes à l’emploi, y compris les assemblages et les composants prémontés pour différents secteurs industriels.
Outre les moulages par injection, Engesser fabrique également des moules destinés au traitement du silicone ou du caoutchouc, ainsi que pour le surmoulage des pièces stockées. Les moules ne servent que partiellement à l’usinage en interne. La majorité est fabriquée pour d’autres clients. De plus, Engesser propose également des travaux à façon dans les domaines du fraisage, du tournage et de l’usinage, mais également dans le perçage profond et la rectification (plane, cylindrique, de profilés et de coordonnées). La majeure partie de ces travaux consiste en des services de modification de moulages existants ou de remaniement de moules fabriqués à l’origine dans des pays tiers. Ainsi, la société offre un large panel d’activités, ce qui exige une haute précision et une importante flexibilité. Habituellement, les demandes reçues par Engesser ne concernent qu’un seul exemplaire de moulage ou d’empreinte rapportée. Les plages de tolérances exigées sont souvent de l’ordre d’environ 10 μm.
Afin de garantir cette précision, nous utilisons depuis plus de huit ans des palpeurs de mesure et des logiciels de m&h Hexagon. Les palpeurs disposent d’une fonctionnalité de transmission de données par infrarouge avec technologie HDR (High-Data-Rate), qui s’est révélée très sécurisée, même sous des conditions difficiles, aussi bien dans les centres d’usinage que les machines d’usinage.
Le logiciel 3D Form Inspect de m&h Hexagon permet d’établir simplement un programme de mesure depuis les ordinateurs de l’atelier. Il convertit les données de CAO des pièces en un
modèle de surface et représente la pièce avec ses valeurs de
consigne. Les utilisateurs définissent les points, les surfaces
ou les formes à mesurer en quelques clics et leur attribuent
les fonctionnalités de mesure souhaitées. Le logiciel 3D Form
Inspect écrit ensuite en arrière-plan le programme correspond
pour le palpeur de mesure. Le logiciel définit ensuite les points
opposés pour la mesure, si possible, de manière autonome,
ce qui permet d’éviter des mesures erronées en raison
d’imprécisions. Le logiciel connaît toutes les mesures prises
par les palpeurs de mesure et calcule automatiquement en
arrière-plan les parcours nécessaires pendant la définition
de la fonction de mesure. Les mouvements des palpeurs de
mesure sont représentés grâce à une simulation sur écran
et un contrôle automatique des collisions est effectué. Les
palpages entraînant une collision des pièces des palpeurs
avec la pièce sont automatiquement exclus et affichés
en conséquence. Le programme réel de la machine est
écrit automatiquement à partir de cette simulation, en
fonction du post-processeur concerné. Ce mode de travail
du logiciel garantit une haute sécurité de travail lorsque la
programmation est simple et rapide.
Lors du palpage des points de mesure dans la machine, le programme en génère un nouveau, qui est transféré à l’ordinateur de l’utilisateur. Ce nouveau programme contient les valeurs mesurées, qui s’affichent immédiatement à l’écran sur la représentation de la pièce. Ainsi, l’utilisateur détecte immédiatement les différences entre les valeurs de consigne et les valeurs obtenues. Le logiciel peut également afficher des couleurs qui indiquent si les plages de tolérances sont respectées ou non. Du fait que la pièce est encore serrée, l’utilisateur peut réagir immédiatement et améliorer ou modifier, le cas échéant, certaines parties de la pièce grâce à la correction ou d’autres modes de traitement.
De manière générale, nous travaillons plus rapidement, plus précisément, et nous disposons toujours d’un protocole de mesure, Le logiciel 3D Form Inspect génère automatiquement un protocole à chaque mesure, qui est ensuite imprimé et enregistré. « La pièce n’est relâchée que lorsqu’elle est considérée comme correcte », explique Holger Gassenschmidt. Chez Engesser, les surfaces de dressage sont depuis longtemps fraisées sur « zéro ». Les points de contour, les ajustements et les surfaces de dépouille sont mesurés chez Engesser. Les séparations du moulage sont vérifiées avant le relâchement de la pièce. Chez Engesser, les opérateurs des machines sont à la fois des ouvriers et des programmeurs. Ils créent également les programmes de mesure à l’aide du logiciel 3D Form Inspect. Ainsi, l’opérateur de la machine a entre ses mains l’entière responsabilité de la pièce et il est en mesure de décider seul, si les contours doivent être regravés ou non. Dans un même temps, il peut justifier la précision de la pièce à l’aide d’un protocole de mesure.
« C’est un véritable gain de temps. La flexibilité des mesures nous a permis de réduire considérablement les temps d’usinage », se réjouit Holger Gassenschmidt. Il explique qu’auparavant, les pièces étaient relâchées, puis envoyées en mesure, avant d’être à nouveau fixées et modifiées. Cela engendrait des pertes de temps et de précision. De plus, les mesures étaient souvent compliquées. Il ajoute : « Même nos temps de montage ont été sensiblement réduits. Les pièces sont désormais prêtes au montage. Les temps de dressage sont plus courts. Elles sont montées, dressées et nivelées. Il est de moins en moins nécessaire de procéder à des modifications. »
Les opérateurs des machines sont unanimes quant à la simplicité d’utilisation du logiciel 3D Form Inspect de m&h et font l’éloge de la formation technique qu’ils ont dû suivre au préalable au centre technologique de m&h Hexagon afin d’actualiser leurs connaissances. Ils ont particulièrement apprécié le fait qu’il ne s’agisse pas d’une formation commerciale qui a pour but de vendre, comme c’est souvent le cas, mais bien d’une formation technique visant à prendre en main le logiciel.
« Nous ne pouvons plus nous passer du logiciel 3D Form Inspect »,déclare Holger Gassenschmidt. Quelques minutes se sont certes rajoutées en raison des mesures prises sur la machine, mais auparavant, les pièces revenaient souvent du montage, car elles devaient être modifiées, et ce sous contrainte de temps. La machine était alors généralement occupée et il fallait interrompre d’autres travaux ou les décaler afin de pouvoir terminer la pièce. « Le temps de mesure sur la machine n’est pas vraiment une perte de temps », explique Holger Gassenschmidt. « Il permet de gagner du temps ensuite au niveau du montage et du dressage. Notre processus est beaucoup plus harmonisé aujourd’hui. De manière générale, nous travaillons plus rapidement, plus précisément, et nous disposons toujours d’un protocole de mesure, non seulement sur les centres d’usinage, mais également sur nos machines d’usinage. »
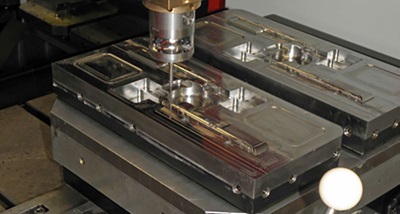
Les pièces y sont contrôlées non seulement à deux centres d’usinage, mais également sur deux machines d’électroérosion par enfonçage équipées de palpeurs de mesure, avant d’être relâchées par l’outil de serrage. Les pièces sont mesurées à l’aide de palpeurs et de logiciels de m&h dans les centres d’usinage HSC, ainsi que dans la machine d’électroérosion par enfonçage, et ce même dans la cellule d’usinage Zimmer & Kreim. « Nous vérifions chaque pièce avant qu’elle sorte de la machine », explique Holger Gassenschmidt, contremaître responsable de la fabrication de moule chez Engesser. « Une pièce n’est relâchée que lorsqu’elle est considérée comme conforme ». Cela permet de sécuriser l’usinage et d’établir des protocoles de mesure pour chaque élément, tout en évitant une perte de temps dû à un passage dans une machine de mesure.
Actuellement, 25 collaborateurs usinent environ 70 à 80 moules par an chez Engesser. Ces derniers peuvent être échantillonnés au sein du centre technique. Des lots pilotes sont souvent fabriqués avant que les moules et les processus ne soient transférés au client. Les machines de moulage à injection fournissent une force de verrouillage allant jusqu’à 275 t et peuvent traiter des poids injectables jusqu’à 400 g. Chez Engesser, environ 70 collaborateurs travaillent dans l’usinage de pièces fabriquées en série prêtes à l’emploi, y compris les assemblages et les composants prémontés pour différents secteurs industriels.
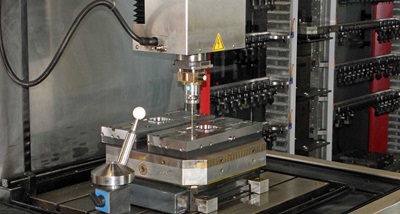
Afin de garantir cette précision, nous utilisons depuis plus de huit ans des palpeurs de mesure et des logiciels de m&h Hexagon. Les palpeurs disposent d’une fonctionnalité de transmission de données par infrarouge avec technologie HDR (High-Data-Rate), qui s’est révélée très sécurisée, même sous des conditions difficiles, aussi bien dans les centres d’usinage que les machines d’usinage.
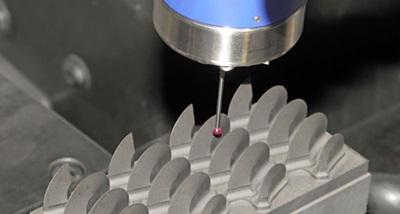
Lors du palpage des points de mesure dans la machine, le programme en génère un nouveau, qui est transféré à l’ordinateur de l’utilisateur. Ce nouveau programme contient les valeurs mesurées, qui s’affichent immédiatement à l’écran sur la représentation de la pièce. Ainsi, l’utilisateur détecte immédiatement les différences entre les valeurs de consigne et les valeurs obtenues. Le logiciel peut également afficher des couleurs qui indiquent si les plages de tolérances sont respectées ou non. Du fait que la pièce est encore serrée, l’utilisateur peut réagir immédiatement et améliorer ou modifier, le cas échéant, certaines parties de la pièce grâce à la correction ou d’autres modes de traitement.
De manière générale, nous travaillons plus rapidement, plus précisément, et nous disposons toujours d’un protocole de mesure, Le logiciel 3D Form Inspect génère automatiquement un protocole à chaque mesure, qui est ensuite imprimé et enregistré. « La pièce n’est relâchée que lorsqu’elle est considérée comme correcte », explique Holger Gassenschmidt. Chez Engesser, les surfaces de dressage sont depuis longtemps fraisées sur « zéro ». Les points de contour, les ajustements et les surfaces de dépouille sont mesurés chez Engesser. Les séparations du moulage sont vérifiées avant le relâchement de la pièce. Chez Engesser, les opérateurs des machines sont à la fois des ouvriers et des programmeurs. Ils créent également les programmes de mesure à l’aide du logiciel 3D Form Inspect. Ainsi, l’opérateur de la machine a entre ses mains l’entière responsabilité de la pièce et il est en mesure de décider seul, si les contours doivent être regravés ou non. Dans un même temps, il peut justifier la précision de la pièce à l’aide d’un protocole de mesure.
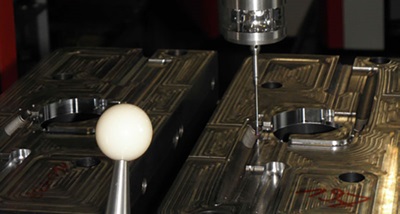
Les opérateurs des machines sont unanimes quant à la simplicité d’utilisation du logiciel 3D Form Inspect de m&h et font l’éloge de la formation technique qu’ils ont dû suivre au préalable au centre technologique de m&h Hexagon afin d’actualiser leurs connaissances. Ils ont particulièrement apprécié le fait qu’il ne s’agisse pas d’une formation commerciale qui a pour but de vendre, comme c’est souvent le cas, mais bien d’une formation technique visant à prendre en main le logiciel.
« Nous ne pouvons plus nous passer du logiciel 3D Form Inspect »,déclare Holger Gassenschmidt. Quelques minutes se sont certes rajoutées en raison des mesures prises sur la machine, mais auparavant, les pièces revenaient souvent du montage, car elles devaient être modifiées, et ce sous contrainte de temps. La machine était alors généralement occupée et il fallait interrompre d’autres travaux ou les décaler afin de pouvoir terminer la pièce. « Le temps de mesure sur la machine n’est pas vraiment une perte de temps », explique Holger Gassenschmidt. « Il permet de gagner du temps ensuite au niveau du montage et du dressage. Notre processus est beaucoup plus harmonisé aujourd’hui. De manière générale, nous travaillons plus rapidement, plus précisément, et nous disposons toujours d’un protocole de mesure, non seulement sur les centres d’usinage, mais également sur nos machines d’usinage. »