Measuring to generate orders
Contact us

Measuring and logging of workpieces, while still clamped on the machine, has enabled ZSM of Gummersbach to win new customers. They perform measuring, machining and logging of nose gear for the Airbus A320 using this technology.
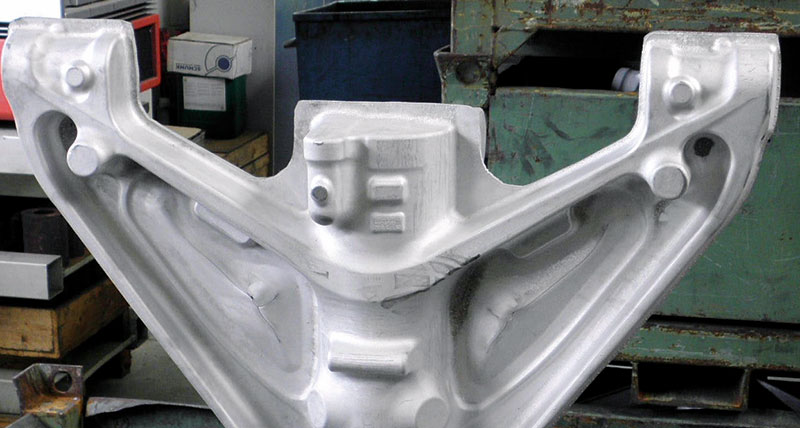
ZSM Zertz + Scheid Maschinenbau-und Handels GmbH has evolved from an engineering company covering a wide range of activities into one cutting high demand special material workpieces. “I haven’t machined normal steel for a long time now,” says production manager Klaus Mands as he describes the current situation.
Here they manufacture a variety of parts for defence and offshore technologies and practice mechanical engineering in the very broadest sense.
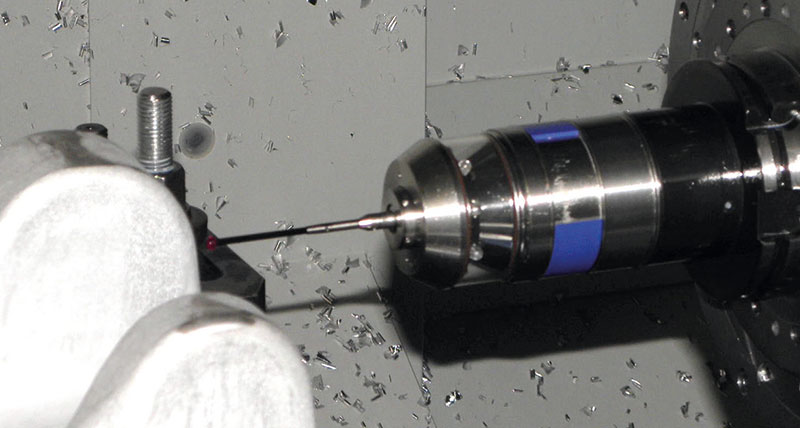
Measuring of free-form surfaces and inclined spatial geometries during pre-machining of the Airbus A320 nose gear proved its worth from the first day onwards. Initially the forged blank is clamped horizontally and the workpiece position is determined using the Best Fit module included in 3D Form Inspect software. In a second measuring operation, the values of additional contour points are confirmed and another Best Fit operation is performed. These values then serve as zero points and the machining program in the control is manipulated to the actual position of the clamped workpiece.
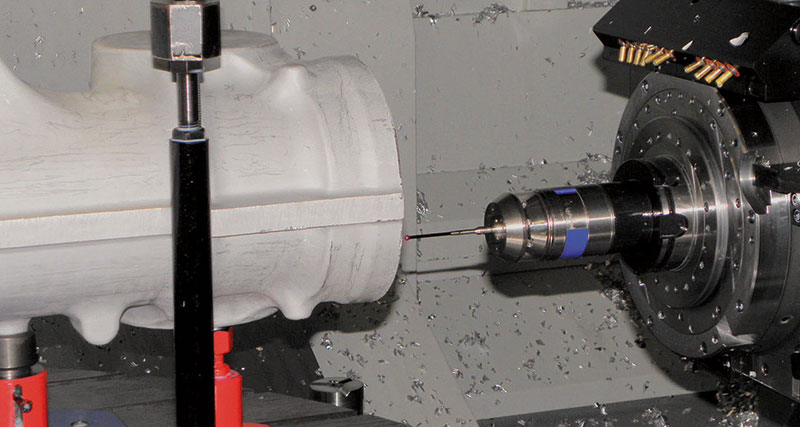
Once the position of the workpiece is determined, precise machining is possible as there is no need to manually “knife and fork” setting to suit the contours of the forged blank. This makes the machining process much faster and precise and also enhances productivity.
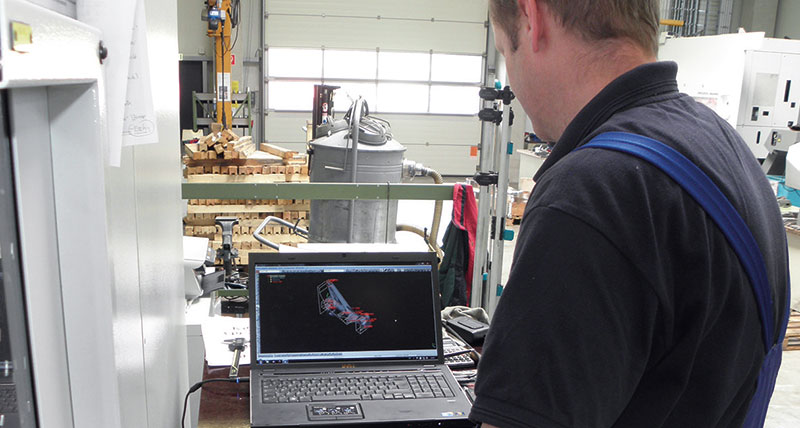
Using 3D Form Inspect, the workpiece is checked using the touch probe at contour points previously determined and compared with the specifications of CAD engineering.
The points can be determined by the operator with just a few mouse clicks on his workshop computer. 3D Form Inspect software automatically programs the axis paths and performs collision control with the workpiece contours. This function is available for both 3 and 5-axis machines. The operator benefits from increased safety and can check the job on his machine at any time. The measured values are immediately visible in the graphic representation on the screen and can be called as a measuring protocol. They can also be transferred to other processes as files in different formats.
For us, the main effect of measuring on the machine is avoiding errors and expensive rejects.“The software is easy to handle,” says machine operator Michael Förster. “We are enthusiastic about m&h and their probes”. They praise the robustness of the touch probes that are ideally suited for the harsh environment inside the machine with coolant and chips. This is thanks to the stainless steel body and glass cover protecting the transmitting diodes. They also appreciate the easy to change monobloc battery. Even more important is the quick response from m&h in case of emergencies such as the touch probe being damaged. “We received an exchange unit within one day and were able to continue working,” praises Klaus Mands.
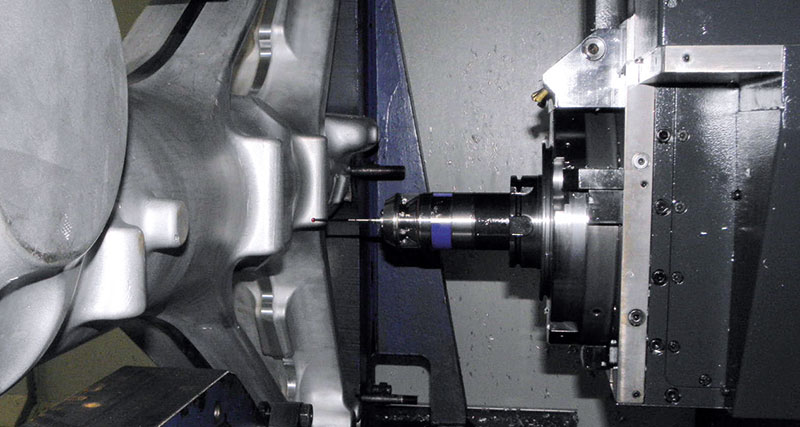