Misurare per generare ordini!
Contattateci

Grazie alla misura e alla preparazione del protocollo dei pezzi mentre sono ancora staffati nella macchina la ZSM di Gummersbach ha conquistato nuovi clienti. L’azienda sta utilizzando questa tecnica per misurare, elaborare e protocollare i dati dei carrelli anteriori dell’Airbus A320.
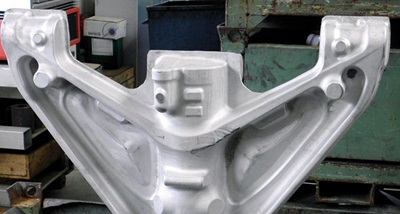
La ZSM Zertz + Scheid Maschinenbau- und Handels GmbH è nata da una società d’ingegneria attiva in svariati settori e si occupa della lavorazionedi pezzi molto complessi da materiali speciali. “È davvero molto che non lavoro l’acciaio normale” commenta Klaus Mands, il direttore dell’azienda, parlando del suo lavoro. L’azienda produce i più svariati componenti per l’areonautica e pezzi per i sistemi di difesa e la tecnologia offshore o la meccanica in genere.
L’azienda ha sede in un nuovo edificio in una zona industriale altrettanto nuova alla periferia di Gummersbach, il suo lavoro consiste nel fornire servizi di lavorazione per macchine multiasse nel reparto di tornitura e fresatura.
I clienti richiedono sempre più spesso qualità e protocollo di collaudo integrati con la lavorazione in ogni singolo pezzo. L’azienda ha quindi deciso di effettuare le misure sempre di più direttamente a bordo macchina e ha acquistato i tastatori e il software 3D Form Inspect di m&h. Il fatto che spesso si debbano lavorare materie prime molto dispendiose, che in caso di errore hanno come conseguenza uno scarto costoso e difficilmente recuperabile, ha spinto l’azienda ad acquistare e impiegare la nuova tecnica in tempi molto rapidi. La possibilità di garantire la qualità del processo produttivo e registrarne i dati effettuando misure in qualsiasi momento tra una lavorazione e l’altra ha consentito alla ZSM di acquisire commesse altrimenti inacessibili.
Sin dal primo giorno la misura, anche di superfici complesse e geometrie inclinate nello spazio, si è dimostrata uno strumento ideale nella sgrossatura del carrello anteriore dell’Airbus A320. Il pezzo grezzo forgiato viene staffato orizzontal- mente e ne viene rilevata la posizione nella macchina mediante il modulo Best Fit del Software 3D Form Inspect. In una seconda operazione di misura vengono confermati i valori in altri punti del contorno e viene eseguito un altro Best Fit. Nel macchina CNC questi valori vengono in seguito utilizzati per correggere gli offset e adeguare la posizione del programma di lavorazione alla posizione effettiva del pezzo staffato. Il secondo Best Fit garantisce l’esattezza della centratura sul lato anteriore e sui fianchi del forgiato.
“La Otto Fuchs KG di Meinerzhagen è un’azienda ottima che esegue forgiature di precisione, ma comunque ogni forgiato è un caso a sé. Nonostante questo ora siamo in grado di garantire che alla fine tutti i pezzi siano uguali”, com- menta soddisfatto Klaus Mands.
Poiché ora la posizione del pezzo è nota è possibile eseguire la lavorazione in modo mirato, senza doversi avvicinare lentamente alla sagoma del forgiato con il tastatore. Così il processo di lavorazione risulta non solo più sicuro e preciso, ma anche più produttivo.
Tra le altre cose i clienti richiedono che vengano rilevati e documentati in modo affidabile i valori di azzeramento di ogni singolo pezzo per poterli elaborare successivamente. I valori vengono inseriti in una tabella predisposta dal cliente che diventa parte integrante della documentazione finale dei componenti dell’aereo. Klaus Mands spiega così questo cambiamento: “Prima le misure venivano rilevate in gran parte manualmente e i valori venivano calcolati con delle formule. E questo poteva sempre essere una fonte di errore. Ora questo problema è stato risolto”. “Non si verificano più errori durante il trasferimento manuale dei valori perché questi vengono trasferiti automaticamente dal protocollo di misura di m&h in quello dell’utente.”
Con 3D Form Inspect il pezzo viene controllato con il tastatore sulla base di punti della superfice prestabiliti e viene confrontato con i dati della matematica CAD.
I punti possono essere definiti prima o direttamente al PC dall’operatore con pochi clic del mouse. Il software 3D Form Inspect non solo programma i movimenti ma esegue anche il controllo di collisione con i contorni del pezzo. 3D Form Inspect svolge queste funzioni sia per le macchine a 5 assi che per quelle a 3 assi. L’operatore può contare sulla massima sicurezza e su un controllo costante del lavoro della macchina. I valori rilevati sono visibili direttamente sulla rappresentazione a video della superficie del pezzo oppure possono essere richiamati come protocollo di misura. Essendo disponibili in formati diversi i file di protocollo possono essere trasferiti anche ad altri processi.
Per noi il vantaggio principale della misura a bordo macchina è avere la garanzia che non si verifichino errori e scarti che sarebbero molto costosi.“La lavorazione e la misura del pezzo a bordo macchina ha consentito a ZSM un tangibile risparmio di tempo. La misura manuale, con i suoi tempi lunghi e il rischio di errori, è stata abbandonata. Ora il pezzo può essere misurato rapidamente tra una fase di lavorazione e l’altra lungo punti di contorno selezionabili ed eventualmente rilavorato con lo stesso staffaggio. Tutti i pezzi escono dalla macchina già completi di protocollo di misura.
Alla ZSM i pezzi vengono staffati anche in un secondo dispositivo verticale nel quale vengono rimisurati con il modulo Best Fit. Quindi vengono rilevati altri punti richiesti
dal cliente finale e non accessibili in posizione orizzontale. Nel giro di pochi minuti si ottiene un protocollo con più di 64 punti di controllo che consentono una lavorazione precisa e corretta del carrello. “Per noi il vantaggio principale della misura a bordo macchina è avere la garanzia che non si verifichino errori e scarti che sarebbero molto costosi. Senza m&h non avremmo proprio ottenuto questo incarico”, dice soddisfatto Klaus Mands a proposito del suo successo.
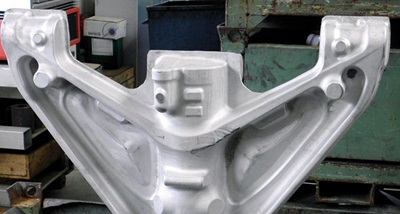
La ZSM Zertz + Scheid Maschinenbau- und Handels GmbH è nata da una società d’ingegneria attiva in svariati settori e si occupa della lavorazionedi pezzi molto complessi da materiali speciali. “È davvero molto che non lavoro l’acciaio normale” commenta Klaus Mands, il direttore dell’azienda, parlando del suo lavoro. L’azienda produce i più svariati componenti per l’areonautica e pezzi per i sistemi di difesa e la tecnologia offshore o la meccanica in genere.
L’azienda ha sede in un nuovo edificio in una zona industriale altrettanto nuova alla periferia di Gummersbach, il suo lavoro consiste nel fornire servizi di lavorazione per macchine multiasse nel reparto di tornitura e fresatura.

Sin dal primo giorno la misura, anche di superfici complesse e geometrie inclinate nello spazio, si è dimostrata uno strumento ideale nella sgrossatura del carrello anteriore dell’Airbus A320. Il pezzo grezzo forgiato viene staffato orizzontal- mente e ne viene rilevata la posizione nella macchina mediante il modulo Best Fit del Software 3D Form Inspect. In una seconda operazione di misura vengono confermati i valori in altri punti del contorno e viene eseguito un altro Best Fit. Nel macchina CNC questi valori vengono in seguito utilizzati per correggere gli offset e adeguare la posizione del programma di lavorazione alla posizione effettiva del pezzo staffato. Il secondo Best Fit garantisce l’esattezza della centratura sul lato anteriore e sui fianchi del forgiato.
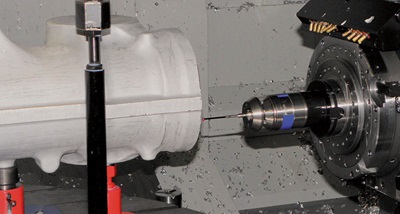
Poiché ora la posizione del pezzo è nota è possibile eseguire la lavorazione in modo mirato, senza doversi avvicinare lentamente alla sagoma del forgiato con il tastatore. Così il processo di lavorazione risulta non solo più sicuro e preciso, ma anche più produttivo.
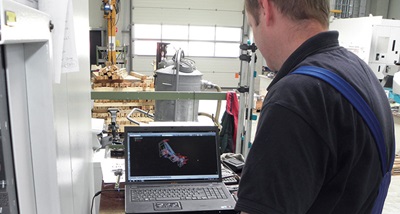
Con 3D Form Inspect il pezzo viene controllato con il tastatore sulla base di punti della superfice prestabiliti e viene confrontato con i dati della matematica CAD.
I punti possono essere definiti prima o direttamente al PC dall’operatore con pochi clic del mouse. Il software 3D Form Inspect non solo programma i movimenti ma esegue anche il controllo di collisione con i contorni del pezzo. 3D Form Inspect svolge queste funzioni sia per le macchine a 5 assi che per quelle a 3 assi. L’operatore può contare sulla massima sicurezza e su un controllo costante del lavoro della macchina. I valori rilevati sono visibili direttamente sulla rappresentazione a video della superficie del pezzo oppure possono essere richiamati come protocollo di misura. Essendo disponibili in formati diversi i file di protocollo possono essere trasferiti anche ad altri processi.
Per noi il vantaggio principale della misura a bordo macchina è avere la garanzia che non si verifichino errori e scarti che sarebbero molto costosi.“La lavorazione e la misura del pezzo a bordo macchina ha consentito a ZSM un tangibile risparmio di tempo. La misura manuale, con i suoi tempi lunghi e il rischio di errori, è stata abbandonata. Ora il pezzo può essere misurato rapidamente tra una fase di lavorazione e l’altra lungo punti di contorno selezionabili ed eventualmente rilavorato con lo stesso staffaggio. Tutti i pezzi escono dalla macchina già completi di protocollo di misura.
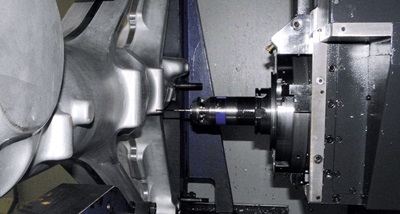