Messen um Bestellungen zu generieren!
Kontakt

Mit dem Messen und Protokollieren von Werkstücken noch in der Maschine hat sich ZSM in Gummersbach neue Kunden erschlossen. Mit dieser Technik werden dort Bugfahrwerke für den Airbus A320 eingemessen, bearbeitet und protokolliert.
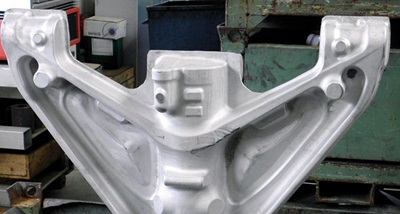
Die Firma ZSM Zertz + Scheid Maschinenbau- und Handels GmbH ist aus einer breit tätigen Ingenieursgesellschaft entstanden und beschäftigt sich mit der Zerspanung sehr anspruchsvoller Werkstücke aus ebenso besonderen Werkstoffen. “Normalen Stahl habe ich lange nicht mehr bearbeitet”, schildert Betriebsleiter Klaus Mands seine Situation.
Unterschiedlichste Luftfahrtteile und Werkstücke für die Verteidigungstechnik sowie für die Offshore-Technik oder den Maschinenbau im weitesten Sinne werden hier gefertigt.
Untergebracht in einem Neubau in einem ebenso neuen Industriegebiet am Rande von Gummersbach gilt es die Mehrachsmaschinen in Dreherei und Fräserei mit passenden Bearbeitungsaufgaben zu füllen. Vermehrt fragen die Kunden nach integrierter Qualitätssicherung und Protokollierung der Bearbeitungsergebnisse, Werkstück für Werkstück. Deshalb hat man sich entschlossen, fortan vermehrt auf den Maschinen zu messen. Dazu wurden Messtaster und Software 3D Form Inspect von m&h angeschafft. Die Tatsache dass man oft sehr teure Werkstoffe zu bearbeiten hat, die im Zweifelsfall teuren und schwer wieder zu beschaffenden Ausschuss bedeuten, verhalf zu zügiger Beschaffung und schnellem Einsatz der neuen Technik. Die Möglichkeit, den Fertigungsprozess durch Messungen jederzeit zwischen einzelnen Bearbeitungen zu sichern und zu protokollieren, verhalf recht bald zu Aufträgen, die anderenfalls nicht erteilt worden wären.
Vom ersten Tag an bewährt sich das Messen, auch von Freiformflächen und schräg im Raum liegenden Geometrien, bei der Vorbearbeitung des Bugfahrwerkes für den Airbus A320. Dazu wird das geschmiedete Rohteil zunächst waagerecht aufgespannt und in der Maschine mit Hilfe des Best Fit Moduls der Software 3D Form Inspect die Lage des Werkstückes ermittelt. In einem zweiten Messvorgang werden dann die Werte an weiteren Konturpunkten bestätigt und ein weiteres Best Fit durchgeführt. In der Maschinensteuerung dienen diese Werte dann zur Nullpunktverschiebung und Anpassung der Lage des Bearbeitungsprogrammes an die tatsächliche Lage des
Werkstückes in seiner Spannung. Das zweite Best Fit führt zur sicheren Zentrierung an der Frontseite und den Flanken des Schmiederohlings. “Zwar ist die Otto Fuchs KG in Meinerzhagen eine wirklich gute Präzisionsschmiede, aber dennoch ist jeder Schmiederohling anders. Trotzdem schaffen wir es jetzt, dass später jedes Bauteil gleich ist”, freut sich Klaus Mands.
Weil nun die Lage des Werkstückes bekannt ist, kann die Bearbeitung auch entsprechend gezielt erfolgen, da man sich nicht erst langsam an die Kontur des Schmiederohlings herantasten muss. Das macht den Bearbeitungsprozess nicht nur sicherer und genauer, sondern auch produktiver.
Zu den Anforderungen des Kunden gehört auch das verlässliche Ermitteln und Dokumentieren der Einrichtewerte jedes einzelnen Werkstückes für die spätere Weiterbearbeitung. Diese Werte müssen in eine vom Kunden vorgegebene Tabelle übertragen werden, die auch Bestandteil der späteren Teiledokumentation des Flugzeuges wird. “Früher konnten wir das Meiste nur manuell messen und haben die Werte oft mit Formeln errechnet. Das war immer eine mögliche Fehlerquelle. Nun sind die Fehlerquellen eliminiert”, erläutert Klaus Mands den Wandel. “Es gibt keine manuellen Übertragungsfehler mehr, weil wir die Werte aus dem m&h Messprotokoll ohne manuelle Arbeit in das Protokoll des Kunden übertragen können.”
Mit 3D Form Inspect wird das Werkstück mit dem Messtaster an vorher festgelegten Konturpunkten geprüft und mit den Vorgaben der CAD-Konstruktion verglichen. Die Festlegung der Punkte kann sowohl vorab, als auch mit wenigen Mausklicks durch den Bediener an seinem Computer in der Werkstatt erfolgen.
Die Programmierung der Verfahrwege übernimmt die Software 3D Form Inspect ebenso, wie die Kollisionskontrolle mit den Werkstückkonturen. Im Falle von 3D Form Inspect gilt das für 5-Achsmaschinen ebenso wie für dreiachsige. Der Maschinenbediener gewinnt hohe Sicherheit und kann die Arbeit seiner Maschine immer kontrollieren. Die ermittelten Werte sind sowohl direkt in der Flächendarstellung des Werkstücks am Bildschirm sichtbar, als auch als Messprotokoll abrufbar. Als Dateien verschiedener Formate lassen sich die Werte auch an weitere Prozesse transferieren.
Der Haupteffekt des Messens in der Maschine liegt für uns sicher in der Fehlervermeidung und der Vermeidung von teurem Ausschuss.““Die Software ist einfach zu bedienen”, ergänzt der Maschinenführer Michael Förster. “Überhaupt sind wir von m&h und den Tastern begeistert.” Gelobt wird die Robustheit der Messtaster, die mit Ihren Edelstahlgehäuse und der Glasabdeckung der Übertragungsdioden für die raue Umgebung der Maschine mit Kühlmitteln und Spänen geschaffen sind. Auch die einfach austauschbare Blockbatterie wird gelobt. Wichtiger aber ist die Reaktionszeit von m&h im Ernstfall, wenn am Taster etwas beschädigt wurde. “Innerhalb von einem Tag war ein Tauschgerät da und wir konnten weiterarbeiten”, lobt auch Klaus Mands.
Bei ZSM bringt das kombinierte Zerspanen und Messen auf der Maschine einen echten Zeitgewinn. Das zeitraubende manuelle Messen mit seinen möglichen Fehlerquellen entfällt. Das Teil kann zwischen den Bearbeitungsgängen immer mal kurz an beliebigen Konturpunkten gemessen werden. Sollte es notwendig sein, kann noch in gleicher Aufspannung maschinell nachgearbeitet werden. Die Werkstücke kommen direkt mit Messprotokoll von der Maschine. Im Fall ZSM werden die Werkstücke noch in eine zweite, vertikale Vorrichtung gespannt. Dort werden
Sie wieder mit Best Fit eingemessen und anschließend weitere Punkte gemessen, die vom Endkunden gefordert sind, aber in der horizontalen Lage nicht erreichbar sind. So wird in wenigen Minuten ein Protokoll über 64 Prüfpunkte erstellt, die eine maßgenaue Weiterbearbeitung des teuren Fahrwerkbeins gewährleisten. “Der Haupteffekt des Messens in der Maschine liegt für uns sicher in der Fehlervermeidung und der Vermeidung von teurem Ausschuss.” Ohne m&h hätten wir nicht nur diesen Auftrag gar nicht erst bekommen”, freut sich Klaus Mands über seine Erfolgsstory.
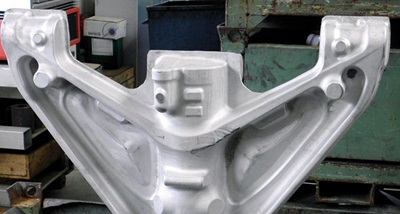
Die Firma ZSM Zertz + Scheid Maschinenbau- und Handels GmbH ist aus einer breit tätigen Ingenieursgesellschaft entstanden und beschäftigt sich mit der Zerspanung sehr anspruchsvoller Werkstücke aus ebenso besonderen Werkstoffen. “Normalen Stahl habe ich lange nicht mehr bearbeitet”, schildert Betriebsleiter Klaus Mands seine Situation.
Unterschiedlichste Luftfahrtteile und Werkstücke für die Verteidigungstechnik sowie für die Offshore-Technik oder den Maschinenbau im weitesten Sinne werden hier gefertigt.

Vom ersten Tag an bewährt sich das Messen, auch von Freiformflächen und schräg im Raum liegenden Geometrien, bei der Vorbearbeitung des Bugfahrwerkes für den Airbus A320. Dazu wird das geschmiedete Rohteil zunächst waagerecht aufgespannt und in der Maschine mit Hilfe des Best Fit Moduls der Software 3D Form Inspect die Lage des Werkstückes ermittelt. In einem zweiten Messvorgang werden dann die Werte an weiteren Konturpunkten bestätigt und ein weiteres Best Fit durchgeführt. In der Maschinensteuerung dienen diese Werte dann zur Nullpunktverschiebung und Anpassung der Lage des Bearbeitungsprogrammes an die tatsächliche Lage des
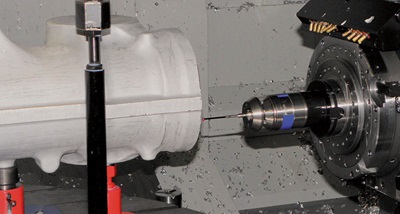
Weil nun die Lage des Werkstückes bekannt ist, kann die Bearbeitung auch entsprechend gezielt erfolgen, da man sich nicht erst langsam an die Kontur des Schmiederohlings herantasten muss. Das macht den Bearbeitungsprozess nicht nur sicherer und genauer, sondern auch produktiver.
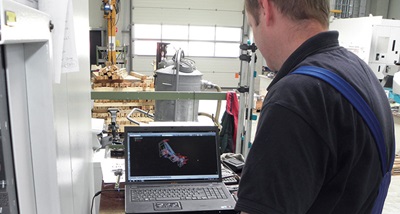
Mit 3D Form Inspect wird das Werkstück mit dem Messtaster an vorher festgelegten Konturpunkten geprüft und mit den Vorgaben der CAD-Konstruktion verglichen. Die Festlegung der Punkte kann sowohl vorab, als auch mit wenigen Mausklicks durch den Bediener an seinem Computer in der Werkstatt erfolgen.
Die Programmierung der Verfahrwege übernimmt die Software 3D Form Inspect ebenso, wie die Kollisionskontrolle mit den Werkstückkonturen. Im Falle von 3D Form Inspect gilt das für 5-Achsmaschinen ebenso wie für dreiachsige. Der Maschinenbediener gewinnt hohe Sicherheit und kann die Arbeit seiner Maschine immer kontrollieren. Die ermittelten Werte sind sowohl direkt in der Flächendarstellung des Werkstücks am Bildschirm sichtbar, als auch als Messprotokoll abrufbar. Als Dateien verschiedener Formate lassen sich die Werte auch an weitere Prozesse transferieren.
Der Haupteffekt des Messens in der Maschine liegt für uns sicher in der Fehlervermeidung und der Vermeidung von teurem Ausschuss.““Die Software ist einfach zu bedienen”, ergänzt der Maschinenführer Michael Förster. “Überhaupt sind wir von m&h und den Tastern begeistert.” Gelobt wird die Robustheit der Messtaster, die mit Ihren Edelstahlgehäuse und der Glasabdeckung der Übertragungsdioden für die raue Umgebung der Maschine mit Kühlmitteln und Spänen geschaffen sind. Auch die einfach austauschbare Blockbatterie wird gelobt. Wichtiger aber ist die Reaktionszeit von m&h im Ernstfall, wenn am Taster etwas beschädigt wurde. “Innerhalb von einem Tag war ein Tauschgerät da und wir konnten weiterarbeiten”, lobt auch Klaus Mands.
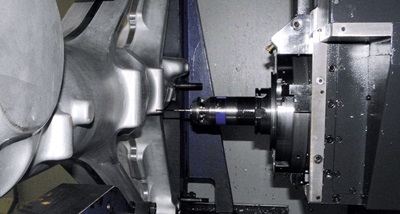