Become more sustainable with advanced reality capture technology

Ready to get started?
The Danish company R3DA was founded in 2019 by Peter Fisker and his partner Thomas Melsen to challenge the status quo of the registration phase in the construction business. Traditional methods cannot deliver the same accuracy to capture the surroundings, and the time needed to complete the task is much shorter with a 3D laser scanner and more sustainable. Being able to capture the entire building in one shot, only one trip is necessary, and no material is wasted as everything can be calculated more accurately.
They focus on heritage preservation to provide accurate data so future projects such as renovations can be better planned and executed. With over 800 historical sites in Denmark, there is a lot to preserve and not only them but their history too. That is only one part of their business; the other part is B2B projects for small and large-scale projects for various companies or private properties.
Scanning a building with the right solution
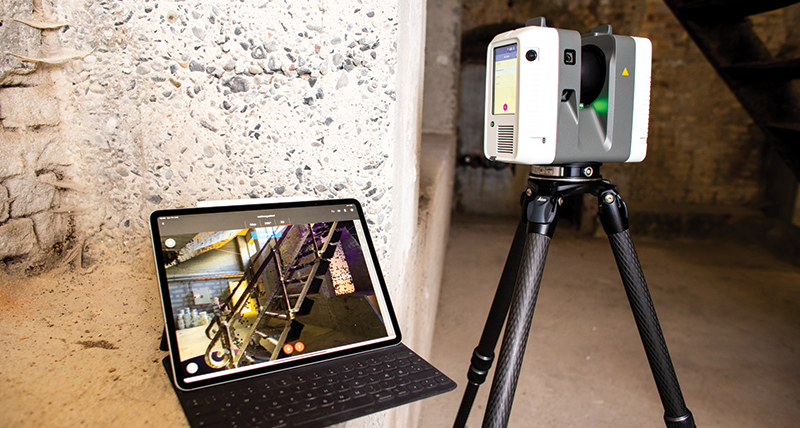
After using the Leica BLK360 G1 imaging laser scanner for several months to scan smaller spaces in the interior better, they expanded their product portfolio with the Leica RTC360 because of its extended range and higher resolution to get the best possible quality. The latest addition to their portfolio was the Leica BLK2FLY, the world’s first flying laser scanner to scan the exterior of a building in its entirety. With the new hardware, R3DA can overlap the scans from all three laser scanners and increase accuracy and efficiency to create 2D and 3D deliverables from the captured point clouds.
When they start on a new project, the first step is to get an overview of the building and its surroundings to define the most efficient path to scan the building. Once on-site, they usually start with the exterior of the building using the Leica RTC360 for ground scans and the Leica BLK2FLY for aerial scans. For the Leica BLK2FLY they create a flight path to have it autonomously complete the exterior scans. If some details were missed, they would manually navigate the BLK2FLY to that spot for a second scan.
The interior is captured with the Leica RTC360 and the BLK360 G1. Depending on the required accuracy, they switch between the laser scanners to fit their customers’ needs. A helpful part of the scanning process is the Leica Cyclone FIELD 360 app combined with the scanner Visual Inertial System (VIS technology). This VIS technology tracks the position of the scanners throughout the scanning process on site and lets you see if an area was missed or not scanned.
Using their reality capture hardware Peter Fisker, CIO at R3DA said: “Compared to how we did it in the past, using PDF drawings and modelling it up from there, now we have a digital twin from which we can create the deliverables much faster.”
Efficient processing of point clouds to create accurate deliverables
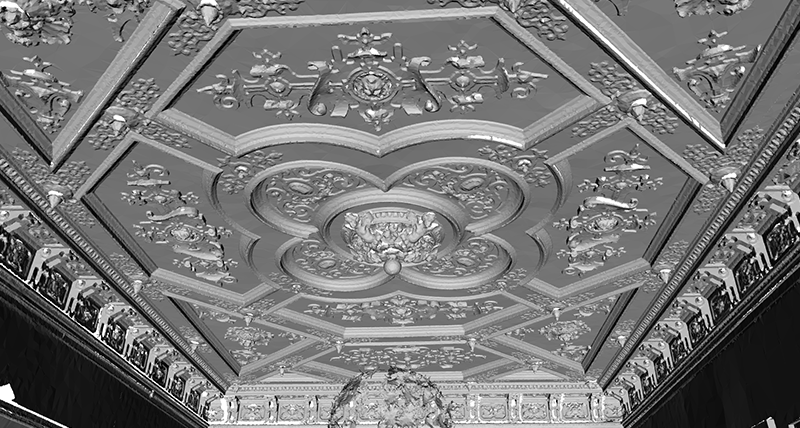
When R3DA scan a building, they return to their office and import the captured data into Leica Cyclone REGISTER 360 post-processing software. With that software solution, they combine the raw data of all scans and create a complete point cloud of the building. For the highest possible accuracy, R3DA combines all scans and manually reduces the tolerances of the point cloud to the absolute minimum. In the end, they export the file in a compatible format for the software used to process the data further and create 2D floorplans or 3D models.
When the point cloud is exported, the data can be used to visualise the building by creating 2D plans and 3D models. The accuracy of the deliverables helps the client to plan their tasks as efficiently as possible to save costs and time. But these are not the only benefits. Once the deliverables are created, they can be used for future projects, which in most cases, eliminates the need to drive to the site again and take measurements.
With a digital workflow the quality of the deliverables increases as Fisker explains: “With the point clouds we can create the deliverables and export all types of objects from the models. Combining the capabilities of 3D scanning and the Leica Cyclone FIELD 360 app, human errors are decreased significantly.”
Leica Geosystems reality capture in action

Egeskov Castle is one project that nicely demonstrates the possibilities of Leica Geosystems’ reality capture solutions. To get insurance for the castle, the owner Michael Ahlefeldt Laurvig-Bille needed to know the exact size of his property. Because the castle is surrounded by water it was not an easy task to scan it precisely with static 3D laser scanners. But the BLK2FLY did it with ease as they could create a flight path and let it scan the entire castle autonomously from the outside. The castle’s interior with every little hidden room and corner right to the very top of the towers was scanned with the BLK360 G1 and RTC360 to create a complete point cloud of the entire castle. R3DA completed the scans within three and a half days – with five floors and 4,500 m2 to scan – and then processed the data and created the required deliverables for their client in another days’ time.
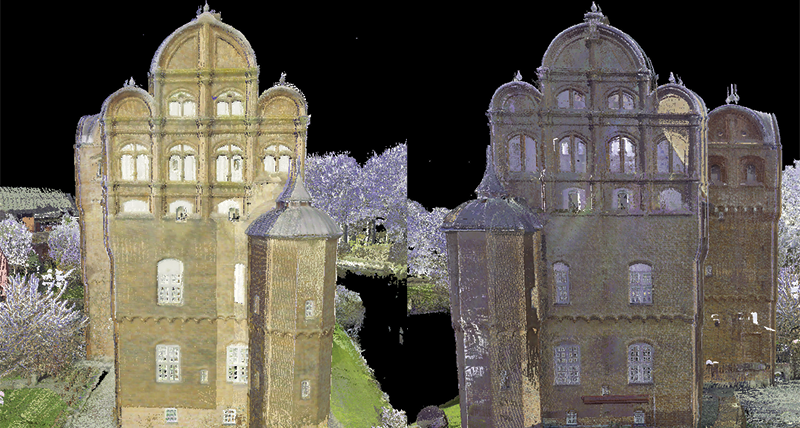
Another project is the Manor House Hesselagergaard that R3DA scanned to determine the required renovations for the façade gables. They used the RTC360 to create an accurate point cloud of the building’s exterior. That allowed them to precisely measure the cracks in the stones to calculate the amount of material needed for the renovations. In this case, it was essential to know the exact number of stones that had to be replaced because the renovation costs are very high. If it had not been for the RTC360 3D laser scanner, it would have been necessary to build a scaffolding to the Manor House which would have been more costly and not as precise when using tape to make the measurements.
Benefits of using reality capture solutions

Compared to traditional methods for measuring buildings, Leica Geosystems’ latest reality capture solutions deliver a more efficient and precise experience. They help to reduce the time needed to scan buildings by approximately 80%, ultimately saving clients costs. After scanning, you have all the required data, eliminating the need to drive back to the site as deliverables can be re-used for future projects. This saves a lot of time and CO2 as there is no need for hour-long round trips anymore. With the created deliverables it is easier to calculate precisely what materials are needed for the project. This does not only save materials but also money as some of the materials, especially for heritage preservation, can be very expensive. This project also showed Fisker that reality capture technology can help to become a more circular economy, as refurbishing an existing building has a positive impact on reducing its footprint.
Fisker mentioned some of the most significant benefits he sees: “The switch to using 3D laser scanners for the registration phase was an easy decision for us, as the accuracy, efficiency and even sustainability can be increased greatly compared to traditional methods. With the models created from the captured point clouds, the building owners, engineers and architects can communicate on the same platform and work on the same data set that was created from the scans.”