Battery Modelling and Design Solutions
Optimize battery design with advanced simulation tools and reduce manufacturing costs, to deliver affordable and reliable products.
Ready to learn more?
Battery Modelling and Solutions Overview
Rechargeable Energy Storage Systems (RESS) Manufacturing
The rechargeable energy storage systems (RESS) manufacturing process involves several stages that require specialized knowledge and expertise. The design stage is critical to determine the specifications needed in the system. The next step involves manufacturing the individual cells that make up the battery, including assembling the electrodes, separator, and electrolyte into a sealed container. The cells are then assembled into modules that are enclosed in a protective casing. The modules are connected in series or parallel to achieve the desired voltage and capacity. Finally, the modules are assembled into a complete battery pack, which undergoes testing to ensure it meets the required specifications. Quality control is critical to ensure that the battery pack meets the required quality standards.
Hexagon solutions enable engineers to use simulation to virtually prove the production process considering the material, process, performance, cost, and quality.
Hexagon solutions
Battery Inspection and Development
One of the most expensive and safety-critical components in cars and other electrified vehicles (EV) is the battery. It has the highest influence on the vehicle range, and poor quality may lead to rapid degradation. Currently, lithium-ion batteries (LIBs) are the most common on the market. Their integrity must be guaranteed with maximum reliability using the latest battery inspection technologies. Consumer electronics require batteries with even higher energy densities. Incidents in the recent past have shown that the safety of these devices must be guaranteed, as well.
Besides the production of established designs, batteries are also a hot topic in research. Challenges in R&D span from battery design to microstructure characterization of the components. Scientists aim to optimize anode and cathode material of LIBs, as well as explore new concepts like solid-state batteries—where a fixed internal design has not yet been established.
Hexagon solutions
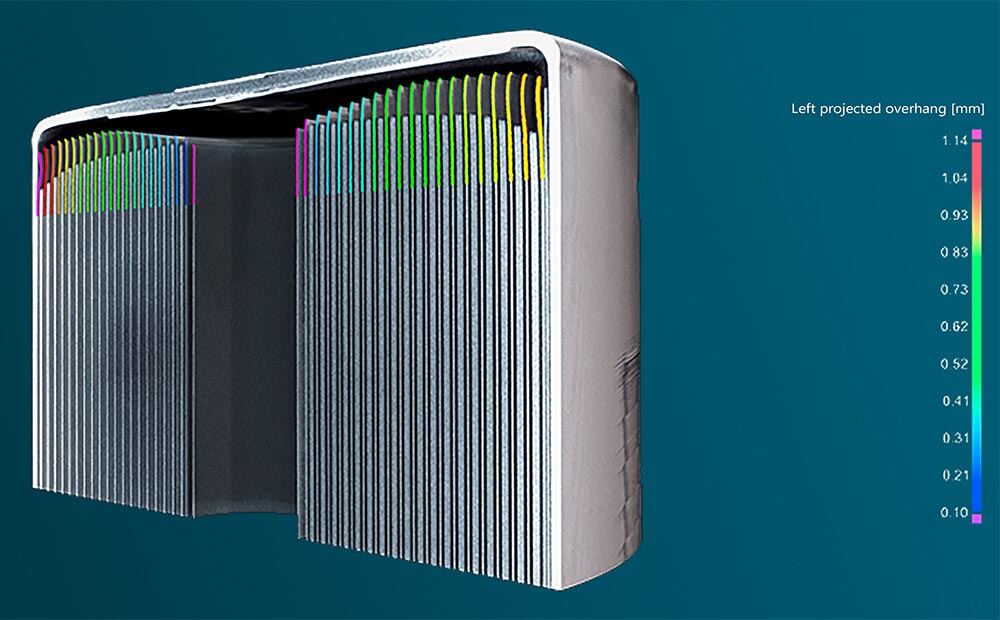
Computed tomography scan of a 18650 Li-Ion battery cell virtually cut open with analysis of the anode overhang region
Optimizing Battery Performance & Safety: Thermal Management
Battery thermal management is crucial for optimal electric vehicle performance and safety. Operating within the ideal temperature range of 20-30 °C ensures efficiency, power, and prevents degradation. High temperatures risk battery life and safety, causing thermal runaway and potential explosions. To design an effective thermal management system, engineers need multiphysics simulation tools like CFD and 1-D system modeling. These tools enable rapid evaluation of design options, operational scenarios, and confidence in the system's performance. Simulations are cost-effective, eliminating bad designs early and reducing reliance on physical prototypes. High-fidelity CFD methods and integrated electrochemistry models ensure accurate thermal propagation and cooling system evaluation. Simulations allow for system-level optimization, considering constraints like weight, without requiring specialized facilities or battery prototype destruction.
Hexagon solutions
- Cradle CFD: Thermo-fluid simulations with integrated cell electrochemistry
- Elements: 1D system modeling; coupling with 3D CFD via FMI/FMU
- CoSim: Multiphysics co-simulations
- MSC Nastran: general-purpose solution for structural thermal management
- Marc: general-purpose solution for advanced nonlinear structural thermal management

Battery Durability & Safety: Simulation for Excellence
Batteries are not only the source of power of the vehicle, but they are also the most expensive component. Furthermore, regulations around the globe require car manufacturers to protect the batteries with warranties that can go up to 10 years. These factors set battery durability under huge pressure as recall campaigns can be extremely expensive and may lead to loss of trust from potential customers for the entire vehicle range of the OEM, not only for the involved models. It is then of paramount importance to early discover potential design flaws by extensive use of simulations techniques. These techniques allow, well in advance of the availability of any real prototype, to expose batteries to the most severe vibrations and temperature levels; hotspots and weak connections can be immediately identified, and countermeasures taken before any real issue arises.
Early design explorations also allow guaranteeing safety of this critical component both in terms of mechanical abuse, e.g., impact from underneath, and thermal, e.g., optimizing the number and locations of the venting caps.
Hexagon solutions
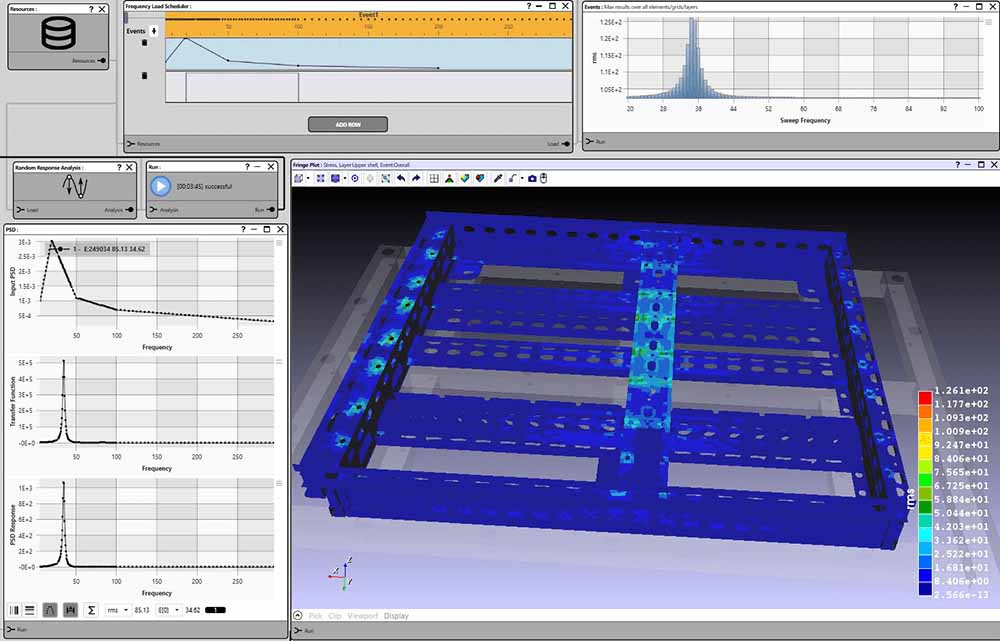
Integrated Design: Enhancing Performance & Efficiency
Batteries power complex systems like electric vehicles where system performance is dependent on multiple sub-systems and how they interact with each other. Systems level integration is key to making the right choices in early design to accelerate your development cycle. In Elements you can integrate batteries, electrical, controls, thermal, mechanics, hydraulics, and many more physical domains in a single model. These models can run entire drive cycles in seconds, enabling you to run multiple scenarios to find the right set of parameters to match your requirements. Once the components designs are fleshed out, you can integrate FMUs from Adams and Cradle CFD into Elements to validate your designs. Elements has your system integration needs covered on both ends of the development cycle.
Hexagon solutions
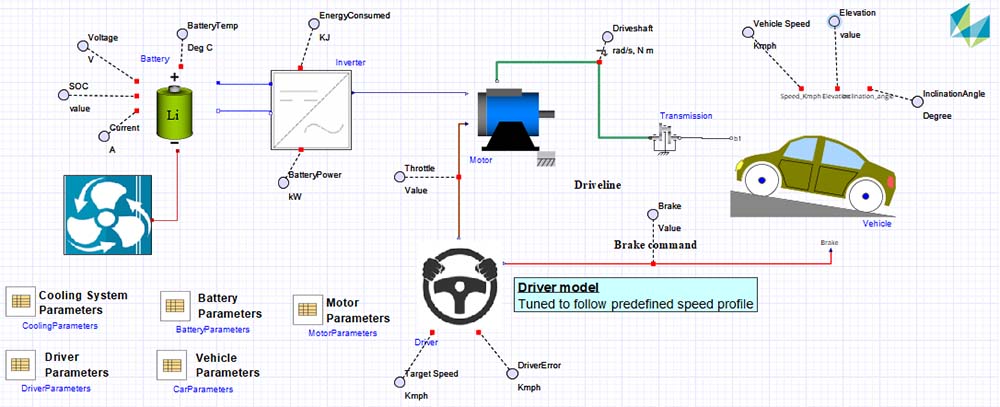