The heavy construction industry is on a path from automation toward autonomy
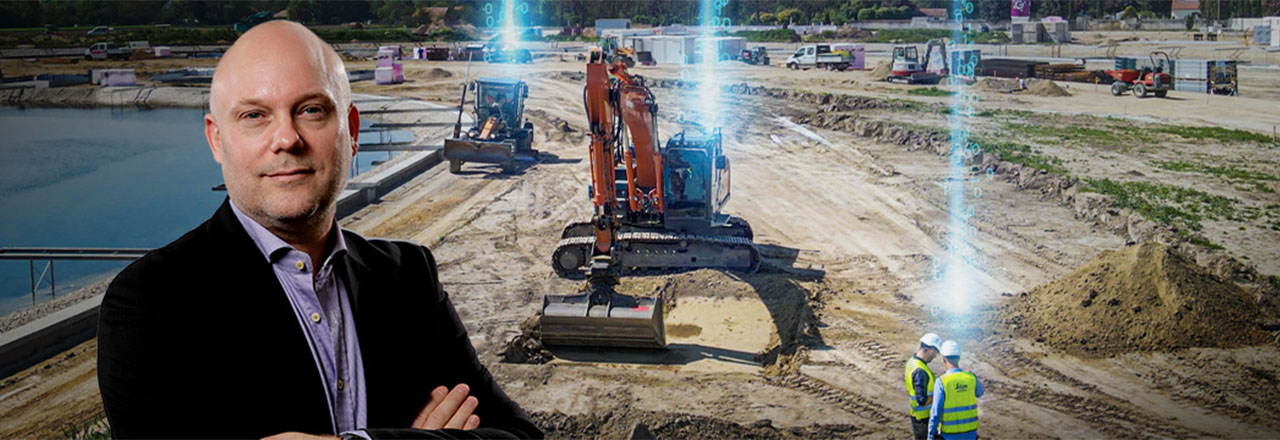
Magnus Thibblin, President Machine Control, Hexagon’s Geosystems division
Embracing technology-enabled solutions on the jobsite becomes a must in this digital era to improve efficiency, profitability, quality, and safety, and attract talent while reducing schedule, cost, and environmental impacts.
Nowadays, we are all aware of the advantages of using machine control and automation technology in heavy construction. But what is next?
The era of autonomy is just around the corner. To enable contractors to be prepared for that greater level of autonomy, we need to reimagine construction solutions with what our customers can confidently start their transformation journey on the path towards autonomy.
Machine control: from guidance to automation
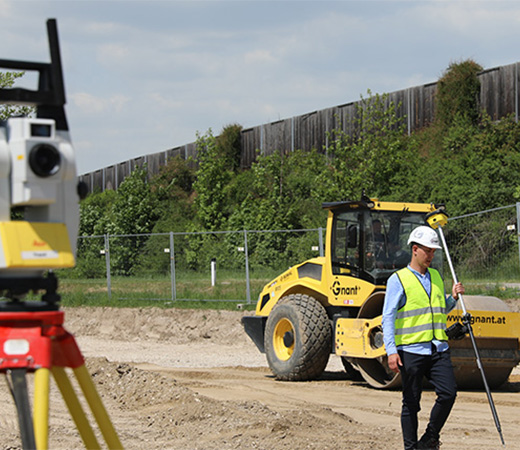
Machine control solutions use data from sources such as 3D-engineered models to guide construction equipment, with enhanced location referencing to provide accurate horizontal and vertical positioning for precise grading, milling, or paving. Machine control technology references the position of the cutting edges or pavement molds using GPS satellites, robotic total stations, lasers, or combinations of these methods.
Machine control is a subtle, often invisible way of automation, that sheds new light on the autonomy the heavy construction industry aims for.
For instance, semi-automation and automation are already in place, encompassing everything from the site machines to the data moving from the machines to the office.
Semi-automation: one step toward autonomy
Recently, we released the semi-automated excavator solution, which guides operators to the perfect target depth smoothly and quickly. As semi-automated solutions require fewer people on-site, they help address the shortage of skilled labour. We expect the application to become even faster, more accurate and easier to use in the next step. We are also working on solutions that facilitate data checking and validation, which will help speed up processes and make them less error-prone.
Enhanced safety: an inevitable step toward autonomous applications
Besides productivity and profitability, safety is another core concern in the industry. Autonomy would imply an unacceptable safety risk without sensors supporting operators and protecting people working around heavy machinery. Thus, we put a lot of effort into enhancing driver awareness and helping operators see things around them.
For instance, our modular safety awareness solutions, the Leica iCON PA10 and PA80 connect people and soft vehicles to the system. We create on-site awareness and use alert signals that indicate when operators are close to a car or a truck. This solution can save lives. Ultimately, we want to integrate the machines into an ecosystem of safety awareness — which is conceivable considering that we are already connecting entire sites.
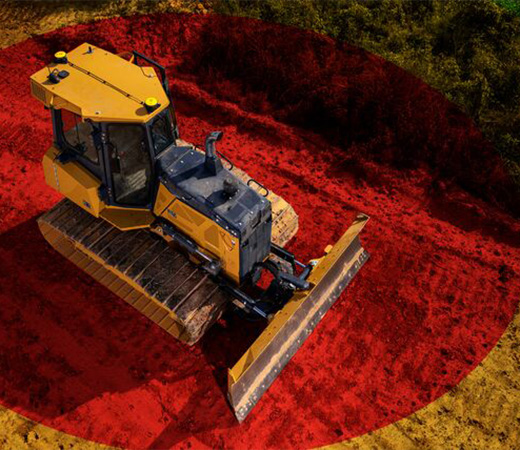
Autonomous solutions to reduce environmental footprint
Sustainability is another industry concern that Hexagon seeks to address by leveraging technology that is impactful on the jobsite and in the office to increase productivity, efficiency and quality at scale. The result: less input and less waste.
For instance, using 3D machine control for paving applications to govern material thickness, which helps save costly hot asphalt mix and energy from producing and transporting it.
Choosing an impactful, holistic solution translates into getting the job done right with fewer hours – moving the right dirt, at the right time, in the right place, with better quality, and accuracy to avoid costly rework. And the potential impacts are massive.
The construction industry represents 13% of worldwide GDP. The amount of CO₂ emitted and resources consumed are astronomical. A 1% improvement in CO₂ reduction thru fuel efficiency, transportation and other means has a direct reduction of 0.12 gigatons of CO₂ per year.
As an example, there are over 4 million miles of road in the US alone. If we can make a 1% improvement in recycling existing asphalt thru new reconditioning methods, such as precise milling or 3D machine control when laying asphalt to reduce wasting unnecessary hot asphalt mix.
1% in our industry has massive impacts and it’s urgent.
Data is the new gold
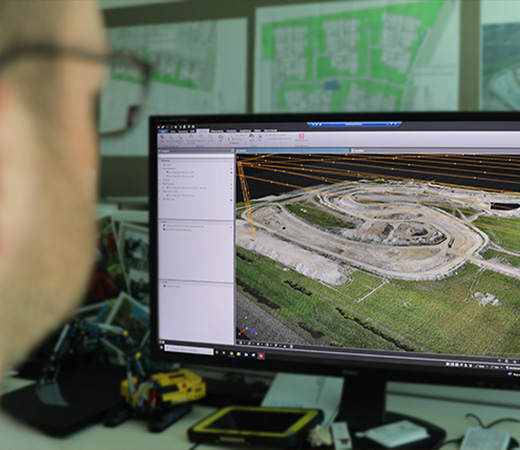
On the data front, there is no autonomy without real-time access to data and instantly generated insights that fuel the decision-making process.
Thus, we are equipping our machines with more sensors and adding additional calculation possibilities. Cameras, GPS and smart software will enable project managers, site foremen and operators to make quicker and better decisions. We are also creating a more effective data path from the field to the office and vice versa so everyone can access the right data at the right time.
Although generating more data points with the use of various sensors is tremendously valuable, being able to extract the right information from it will be essential. We facilitate the data flow by connecting all the field units and transferring the data to the cloud. We will need straightforward ways to make relevant data available in the proper format depending on the role and function of the target persona, be it a surveyor, a foreman or a project manager.
Workflows need to be easy to adopt and use
The future of construction processes and autonomy does not mean that workflows will be complex or solutions will have a huge learning curve. Just the opposite. We have many different customers with vastly different workflows. Our solutions must be adaptable enough to facilitate the adoption of our technology across all functions, from the field to the office. Ease of use is a priority.
The technology requirements, as well as the levels of acceptance and adoption, vary from company to company. Our solutions must be flexible enough to respond to a wide range of needs. We aim to find ways to make systems easier to use and data easier to utilise. This will help our customers deal with the skill shortage, increase efficiency and avoid costly mistakes.
Technology adoption starts from the factory
“If you want to walk far, walk together,” said Ratan Tata. And this philosophy cannot be even more on point when moving the entire industry forward on the autonomous path.
Original Equipment Manufacturers (OEMs) play a crucial role in technology adoption. And we believe in the power of collaboration. More and more machines are factory-fitted with 2D and 3D sensors due to our working relationship with them as well as the pull from the market.
Also the market demand helps with the technological development of autonomous solutions. It ensures that OEMs consider such solutions during the development process. When an OEM develops a new model of a machine, we can help the manufacturers deploy suitable technology for the customers’ needs.
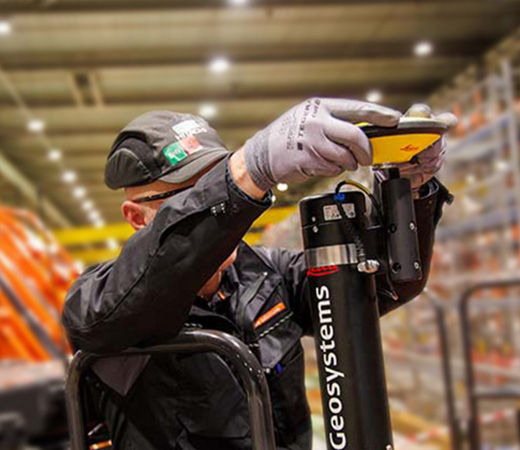
One step at a time
Autonomy does not happen in a day. Our technology is paving the way toward a more autonomous and connected ecosystem.
Today, 2D and 3D sensors already enable semi-automated or automated processes. The move into more autonomous cycles will happen in steps, with each step gaining increased acceptance and approval. Today, we are on steps two and three of the seven to eight steps it will likely take to reach fully autonomous operations. Getting to the last step of autonomy may take a while, but the industry is taking leaps forward every year, and it may come quicker than we think.
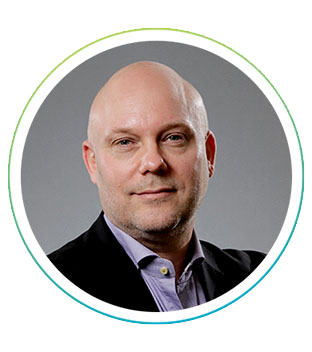