Uncovering the hidden past of steam locomotive manufacturing
From direct scanning to outdoor hidden point probing, Hexagon’s unique laser tracker technology played a key role in rebuilding a lost classic of British railway design.
Contact us

A steam train not seen since the 1960s is being rebuilt by a group of engineering enthusiasts, assisted by the metrology experts at the University of Sheffield Advanced Manufacturing Research Centre (AMRC). With a little extra help from Hexagon’s advanced industrial laser tracker technology, the team got the measure of a mysterious discrepancy between the original drawings and the actual locomotive.
The Standard Steam Locomotive Company group has set itself the ambitious challenge to recreate, operate and maintain a lost class of British steam train – a British Railways’ Standard Class 6 ‘Clan’ – using a combination of the original 1950s design drawings and 21st century engineering. The plan is to incorporate modern design and manufacturing techniques and technologies into the build.
The AT402 was ideal for measuring the frame extensions in situ in the engine shed, negating the need to find a dedicated inspection room.The direct scanning capabilities of the Leica Absolute Tracker ATS600 proved to be incredibly useful at the project’s assembly stage, delivering significant time savings to the team in both assessing the delivered parts and aligning them before final fixing. In addition, a Leica Absolute Tracker AT402 was used at an earlier stage of the project when probing functionality was demanded in a challenging outdoor storage environment to measure parts for comparison against documentation.
This came about when the AMRC was involved in a major frame alignment measuring exercise for the project after a review of the build inventory showed critical gaps in documentation for some of the key parts relating to the locomotive’s frames.
Dr Phil Yates is a chartered engineer at the AMRC working on regional and SME development within the centre’s Factory 2050 facility, as well as a member of the Standard Steam volunteer group. He said these gaps in the documentation for some of the parts are thought to be due to the fact that, 80 years ago, there was no direct link between the drawing office and shop floor as the locomotive was designed and constructed in separate locations some 50 miles apart.
“The Standard Class was designed at the drawing office of the Derby Works while the locomotives were constructed at British Railways’ Crewe Works between 1951 and 1954. So the drawing office was nowhere near where they made the locomotive and back then people made stuff based on what they knew rather than what was in the drawing. You have to bear in mind the drawing does not show how a part is manufactured. That’s what these errors are – they show the disconnect between the drawing office and the shop floor.”
Further doubts about the functionality of the parts were raised when the original 1950s British Rail drawings were converted and turned into computer-aided design (CAD) models. “One of the main components that caused serious concern were the frame extensions,” explained Dr Yates. “The CAD had been produced after the part had been previously manufactured prior to the manufacture of the mainframe plates. The way the fastener hole patterns had been datumed on the frame and the frame extensions was not identical, so when the parts were aligned in CAD, the fastener holes did not align. The maximum error on the CAD components was 1.6 millimetres. The error was because the two original drawings didn’t match. The person who did the drawing of the frame and the person who did the drawing of the frame extensions, one of them got something wrong or different, so they didn’t align.”
Poor draughtsmanship and not understanding manufacturing methods can lead to misinterpretation of drawings; a problem then as it is in today’s world. Understanding manufacturing methods is essential in dimensioning drawings with clarity. As both the frames and their extensions had been laser profiled by separate companies to the one that produced the original drawing, it was assumed that these errors existed in the parts. To ascertain the size of the error, the frames and frame extensions – which were stored in separate locations – had to be measured.
To measure the frame extensions, which were being stored at East Lancashire Railway works, Dr Yates and Factory 2050’s team lead for inspection and AI, Tom Hodgson, used a Leica Absolute Tracker AT402 laser tracker combined with a Leica B-Probe. The portable coordinate measuring machine is produced by the Manufacturing Intelligence division of Hexagon, a tier one research partner of the AMRC. It enables extreme accuracy over large distances, and its B-Probe handheld probing sensor was the ideal measurement tool for assessing the 4-metre long frame extensions of a steam locomotive.
“Tom Hodgson and I did the measurement work on the frame extensions,” said Dr Yates. “They were being stored in a freezing cold shed and that was something we had to consider because temperature can affect measurement work. Materials can shrink and grow with changes in temperature. To account for that involves some tricky maths and we’ve compensated for it best we can by gauging how much the material would move by a ten degrees difference in temperature.”
According to Geoff Turner, the group’s engineering director, access to the AMRC’s expertise and Hexagon’s advanced equipment allowed for fast, accurate data to be collected and for the errors to be remedied quickly.
It saved so much time compared with using traditional measuring equipment and, crucially, it meant that real-time adjustments could be made as the survey was in progress. “The AT402 was ideal for measuring the frame extensions in situ in the engine shed, negating the need to find a dedicated inspection room and giving us accurate data in the three planes identifying the errors which we were able to correct,” said Turner.
“Because we knew this before assembly, we could work out a strategy for re-doing the holes and make slightly oversized fasteners for where the holes were wrong,” added Dr Yates.
Assembly for the locomotive is being done at specialist Sheffield engineering firm CTL Seal Ltd, which also doubles as the Standard Steam volunteer group’s headquarters after CTL Seal generously allocated part of its shop floor to give the group a dedicated space in which to build the lost locomotive.
The locomotive’s frame comprises main frame plates held apart by fabricated steel frame stretchers, cast steel frame stretchers and pressed steel horizontal frame stretchers. All these components were manufactured by different suppliers so to ensure the different components were all manufactured to the same dimensional accuracy, the project team needed confirmation of the frame assembly dimensions.
To do this, Yates and the Standard Steam volunteer group enlisted further help from AMRC partner Hexagon, this time trialling a new type of direct scanning laser tracker that operates without the need for a target such as a reflector or handheld probe – the Leica Absolute Tracker ATS600. Its scanning ability was ideally suited to the task, said Yates, and Hexagon loaned one to the project along with the expertise of its application engineers, Tim Gears and Barry Dimelow.
“Hexagon has been supporting AMRC through our tier one partnership since 2013,” said Gears. “We’ve been involved in many projects, but not one as interesting as scanning a 1950s steam locomotive. The versatility of our ATS600, and the flexibility that reflectorless scanning gave us, made it the perfect measurement tool for the job.”
The ATS600 is a metrology-grade large-volume scanner that seamlessly combines direct surface scanning with single-point reflector measurement. With a direct scanning range of up to 60 metres, it can scan at speeds of up to 10 seconds per square metre. It’s also compatible with established metrology workflows thanks to its integration with leading metrology software such as SpatialAnalyzer and Inspire. This allows point cloud data from the ATS600 to be available directly within application software for immediate feedback – incredibly useful for build and inspect applications.
The scan area was defined by selecting the regions of interest from the frame in CAD and then setting the point spacing required. Key features such as the horn guides and datum holes and reference nests were measured by probing with a retroreflector.The system didn’t fail to impress the Standard Steam team. Measurements from the first scan, which consisted of 2788 points, took just two minutes and showed a significant bow in the frame. Further investigation revealed the bow had been caused by a packing piece being left in place, which had been fitted to allow the removal and replacement of one of the frame stretchers for machining.
“The maximum deflection caused by this packing piece was 8.9 millimetres,” said Yates. “The scan area was defined by selecting the regions of interest from the frame in CAD and then setting the point spacing required. Key features such as the horn guides and datum holes and reference nests were measured by probing with a retroreflector.”
By using the combined scan and probing data, the rotational relationship of the frames could be determined. “This showed that the frames were rotating around a point between the second and third driving wheel,” said Yates. “The point at the exhaust steam spider was 3.02 millimetres high. The manufacturing engineers were shown graphically the relationship between the two frames.
“With the frames loosened and then re-aligned, a second scan was completed and that showed that the frames were aligned and they could progress to final bolting. The position and relationship between the horn guides and the cylinder mounting points was also recorded so that in the final machining procedure a probing and datuming section could be completed, thus saving time on the machine.”
The laser scanning survey proved to be another huge help to the project according to Turner. “It saved so much time compared with using traditional measuring equipment and, crucially, it meant that real-time adjustments could be made as the survey was in progress.”
The Standard Steam Locomotive Company group has set itself the ambitious challenge to recreate, operate and maintain a lost class of British steam train – a British Railways’ Standard Class 6 ‘Clan’ – using a combination of the original 1950s design drawings and 21st century engineering. The plan is to incorporate modern design and manufacturing techniques and technologies into the build.
The AT402 was ideal for measuring the frame extensions in situ in the engine shed, negating the need to find a dedicated inspection room.The direct scanning capabilities of the Leica Absolute Tracker ATS600 proved to be incredibly useful at the project’s assembly stage, delivering significant time savings to the team in both assessing the delivered parts and aligning them before final fixing. In addition, a Leica Absolute Tracker AT402 was used at an earlier stage of the project when probing functionality was demanded in a challenging outdoor storage environment to measure parts for comparison against documentation.
This came about when the AMRC was involved in a major frame alignment measuring exercise for the project after a review of the build inventory showed critical gaps in documentation for some of the key parts relating to the locomotive’s frames.
Dr Phil Yates is a chartered engineer at the AMRC working on regional and SME development within the centre’s Factory 2050 facility, as well as a member of the Standard Steam volunteer group. He said these gaps in the documentation for some of the parts are thought to be due to the fact that, 80 years ago, there was no direct link between the drawing office and shop floor as the locomotive was designed and constructed in separate locations some 50 miles apart.
“The Standard Class was designed at the drawing office of the Derby Works while the locomotives were constructed at British Railways’ Crewe Works between 1951 and 1954. So the drawing office was nowhere near where they made the locomotive and back then people made stuff based on what they knew rather than what was in the drawing. You have to bear in mind the drawing does not show how a part is manufactured. That’s what these errors are – they show the disconnect between the drawing office and the shop floor.”
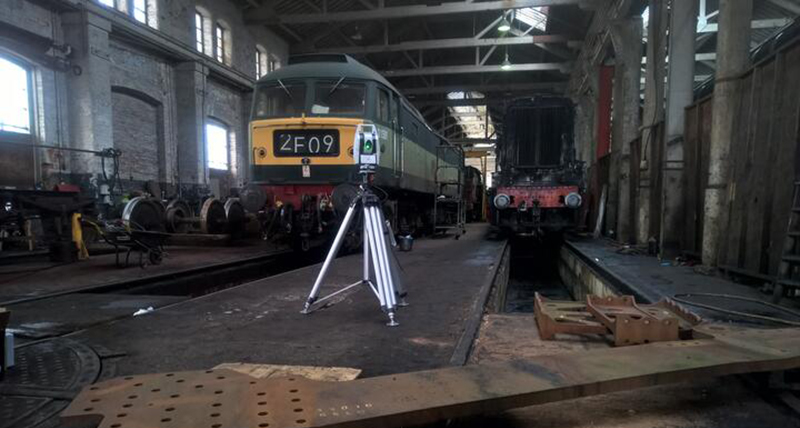
Poor draughtsmanship and not understanding manufacturing methods can lead to misinterpretation of drawings; a problem then as it is in today’s world. Understanding manufacturing methods is essential in dimensioning drawings with clarity. As both the frames and their extensions had been laser profiled by separate companies to the one that produced the original drawing, it was assumed that these errors existed in the parts. To ascertain the size of the error, the frames and frame extensions – which were stored in separate locations – had to be measured.
To measure the frame extensions, which were being stored at East Lancashire Railway works, Dr Yates and Factory 2050’s team lead for inspection and AI, Tom Hodgson, used a Leica Absolute Tracker AT402 laser tracker combined with a Leica B-Probe. The portable coordinate measuring machine is produced by the Manufacturing Intelligence division of Hexagon, a tier one research partner of the AMRC. It enables extreme accuracy over large distances, and its B-Probe handheld probing sensor was the ideal measurement tool for assessing the 4-metre long frame extensions of a steam locomotive.
“Tom Hodgson and I did the measurement work on the frame extensions,” said Dr Yates. “They were being stored in a freezing cold shed and that was something we had to consider because temperature can affect measurement work. Materials can shrink and grow with changes in temperature. To account for that involves some tricky maths and we’ve compensated for it best we can by gauging how much the material would move by a ten degrees difference in temperature.”
According to Geoff Turner, the group’s engineering director, access to the AMRC’s expertise and Hexagon’s advanced equipment allowed for fast, accurate data to be collected and for the errors to be remedied quickly.
It saved so much time compared with using traditional measuring equipment and, crucially, it meant that real-time adjustments could be made as the survey was in progress. “The AT402 was ideal for measuring the frame extensions in situ in the engine shed, negating the need to find a dedicated inspection room and giving us accurate data in the three planes identifying the errors which we were able to correct,” said Turner.
“Because we knew this before assembly, we could work out a strategy for re-doing the holes and make slightly oversized fasteners for where the holes were wrong,” added Dr Yates.
Assembly for the locomotive is being done at specialist Sheffield engineering firm CTL Seal Ltd, which also doubles as the Standard Steam volunteer group’s headquarters after CTL Seal generously allocated part of its shop floor to give the group a dedicated space in which to build the lost locomotive.
The locomotive’s frame comprises main frame plates held apart by fabricated steel frame stretchers, cast steel frame stretchers and pressed steel horizontal frame stretchers. All these components were manufactured by different suppliers so to ensure the different components were all manufactured to the same dimensional accuracy, the project team needed confirmation of the frame assembly dimensions.
To do this, Yates and the Standard Steam volunteer group enlisted further help from AMRC partner Hexagon, this time trialling a new type of direct scanning laser tracker that operates without the need for a target such as a reflector or handheld probe – the Leica Absolute Tracker ATS600. Its scanning ability was ideally suited to the task, said Yates, and Hexagon loaned one to the project along with the expertise of its application engineers, Tim Gears and Barry Dimelow.
“Hexagon has been supporting AMRC through our tier one partnership since 2013,” said Gears. “We’ve been involved in many projects, but not one as interesting as scanning a 1950s steam locomotive. The versatility of our ATS600, and the flexibility that reflectorless scanning gave us, made it the perfect measurement tool for the job.”
The ATS600 is a metrology-grade large-volume scanner that seamlessly combines direct surface scanning with single-point reflector measurement. With a direct scanning range of up to 60 metres, it can scan at speeds of up to 10 seconds per square metre. It’s also compatible with established metrology workflows thanks to its integration with leading metrology software such as SpatialAnalyzer and Inspire. This allows point cloud data from the ATS600 to be available directly within application software for immediate feedback – incredibly useful for build and inspect applications.
The scan area was defined by selecting the regions of interest from the frame in CAD and then setting the point spacing required. Key features such as the horn guides and datum holes and reference nests were measured by probing with a retroreflector.The system didn’t fail to impress the Standard Steam team. Measurements from the first scan, which consisted of 2788 points, took just two minutes and showed a significant bow in the frame. Further investigation revealed the bow had been caused by a packing piece being left in place, which had been fitted to allow the removal and replacement of one of the frame stretchers for machining.
“The maximum deflection caused by this packing piece was 8.9 millimetres,” said Yates. “The scan area was defined by selecting the regions of interest from the frame in CAD and then setting the point spacing required. Key features such as the horn guides and datum holes and reference nests were measured by probing with a retroreflector.”
By using the combined scan and probing data, the rotational relationship of the frames could be determined. “This showed that the frames were rotating around a point between the second and third driving wheel,” said Yates. “The point at the exhaust steam spider was 3.02 millimetres high. The manufacturing engineers were shown graphically the relationship between the two frames.
“With the frames loosened and then re-aligned, a second scan was completed and that showed that the frames were aligned and they could progress to final bolting. The position and relationship between the horn guides and the cylinder mounting points was also recorded so that in the final machining procedure a probing and datuming section could be completed, thus saving time on the machine.”
The laser scanning survey proved to be another huge help to the project according to Turner. “It saved so much time compared with using traditional measuring equipment and, crucially, it meant that real-time adjustments could be made as the survey was in progress.”