Descubriendo el pasado oculto de la fabricación de locomotoras de vapor
Desde el escaneo directo hasta el palpado de puntos inaccesibles en exteriores, la exclusiva tecnología láser de Hexagon jugó un papel determinante en la reconstrucción de un clásico perdido de un diseño ferroviario británico.
Contacto

Un tren de vapor que no se había visto desde la década de 1960 se está reconstruyendo por un grupo de entusiastas ingenieros, ayudados por los expertos en metrología en el University of Sheffield Advanced Manufacturing Research Centre (AMRC). Con un poco de ayuda adicional de la avanzada tecnología láser tracker industrial de Hexagon, el equipo logró medir una misteriosa discrepancia entre los planos originales y la locomotora actual.
El grupo de la Standard Steam Locomotive Company se ha propuesto el ambicioso reto de recrear, poner en funcionamiento y conservar una clase perdida de locomotora de vapor británica –una Clase estándar 6 o ’Clase Clan’ de los ferrocarriles británicos – usando una combinación de los planos originales de la década de 1950s e ingeniería del siglo XXI. El plan consiste en incorporar el diseño moderno y técnicas de fabricación con tecnologías en su construcción.
El AT402 resultó idea para medir las extensiones de la estructura in situ en el cobertizo del motor, eliminando la necesidad de buscar un lugar especializado para la inspección.Las capacidades de escaneo directo del Leica Absolute Tracker ATS600 demostraron ser de gran utilidad en la etapa de ensamblado del proyecto, ofreciendo ahorros de tiempo considerables al equipo tanto en la evaluación de las piezas entregadas como en su alineación antes de la fijación final. Además, se usó un Leica Absolute Tracker AT402 en una etapa previa del proyecto cuando se requirió la funcionalidad de palpado en un entorno desafiante de almacenamiento en exteriores para medir piezas para su comparación con la documentación.
Esto ocurrió cuando el AMRC participó en un ejercicio de medición de alineación de una estructura principal para el proyecto después de que una revisión del inventario de construcción mostró faltas considerables en la documentación de algunas de las piezas principales con relación a las estructuras de la locomotora.
El Dr Phil Yates es un ingeniero colegiado en el AMRC que trabaja en el desarrollo regional y de las PYME en las instalaciones de Factory 2050, además de ser miembro del grupo de voluntarios de Standard Steam. Explicó que estas faltas en la documentación para algunas de las piezas se deben quizás a que hace 80 años, no existía un vínculo directo entre la oficina de diseño y el taller, ya que la locomotora fue diseñada y construida en ubicaciones diferentes a una distancia de 80 km entre si.
“La Clase estándar fue diseñada en la oficina de diseño de Derby Works y las locomotoras se construyeron en Crewe Works de British Railways entre 1951 y 1954. Por lo tanto, la oficina de diseño no se encontraba cerca del lugar de fabricación de la locomotora y las personas en ese entonces hacían las cosas basándose en lo que sabían más que en lo que había en los planos. Es necesario tomar en cuenta que los planos no muestran cómo se fabrica una pieza. Ahí es donde se encuentran estos errores – muestran la falta de conexión entre la oficina de diseño y el taller.”
Surgieron más dudas acerca de la funcionalidad de las piezas cuando los planos originales de la década de 1950 de British Rail se digitalizaron y se convirtieron a modelos de diseño asistido por computadora (CAD). “Uno de los principales componentes que provocó serias dudas fueron las extensiones de la estructura,” explicó el Dr Yates. “El modelo CAD había sido generado después de que la pieza había sido fabricada antes de la producción de las placas de la estructura. La forma como los patrones de los agujeros para sujeción habían sido referenciados sobre la estructura y las extensiones de la estructura no eran iguales, por lo que cuando las piezas fueron alineadas en CAD los agujeros para sujeción no coincidían. El error máximo en los componentes CAD era de 1.6 milímetros. El error surgió debido a que los dos planos originales no coincidían. Quien elaboró el plano de la estructura o quien generó el plano de las extensiones de la estructura cometió algún error o hizo algo diferente, lo cual explica que no coincidieran.”
Una escasa habilidad como delineante y la falta de comprensión de los métodos de fabricación puede provocar una mala interpretación de los planos, un problema en aquel momento y que sigue siendo actual. La comprensión de los métodos de fabricación resulta esencial al dimensionar los planos con claridad. Ya que las estructuras y sus extensiones habían sido perfiladas con láser por empresas diferentes a las que generó los planos originales, se asumió que estos errores existían ya en las piezas. Para establecer la dimensión del error, las estructuras y las extensiones de la estructura – que se guardaron en lugares diferentes – debían ser medidos.
Para medir las extensiones de la estructura, que se guardaron en los trabajos de East Lancashire Railway, el Dr Yates y el equipo de Factory 2050 efectuaron una inspección con IA, Tom Hodgson, usó un láser tracker Leica Absolute Tracker AT402 combinado con un Leica B-Probe. La máquina de medición por coordenadas portátil fue fabricada por la división de Manufacturing Intelligence de Hexagon, socio de investigación de primer nivel de AMRC. Permite la obtención de gran precisión en grandes distancias y su sensor de palpado portátil B-Probe resultó ser la herramienta ideal de medición para evaluar las extensiones de 4 metros de largo de la estructura de una locomotora de vapor.
“Tom Hodgson y yo efectuamos el trabajo de medición en las extensiones de la estructura,” comentó el Dr Yates. “Habían sido guardadas en un cobertizo helado y teníamos que tomar en cuenta ese detalle ya que la temperatura puede afectar el trabajo de medición. Los materiales se pueden encoger y dilatar con los cambios de temperatura. Tomar esto en cuenta implica algunos cálculos matemáticos por lo que lo compensamos lo mejor posible calculando cuánto se movería el material con una diferencia de 10 grados de temperatura.”
Según Geoff Turner, director del grupo de ingenieros, el acceso a la experiencia de AMRC y el avanzado equipo de Hexagon permitió la obtención rápida y precisa de datos y la pronta corrección de los errores. “El AT402 resultó ideal para la medición de las extensiones de la estructura in situ en el cobertizo del motor, anulando la necesidad de encontrar un área especializada de inspección y ofreciéndonos datos precisos en tres planos al identificar los errores que fue posible corregir,” explicó Turner.
Ahorramos mucho tiempo comparado con el uso de equipo de medición tradicional y, forma crucial, fue posible efectuar ajustes en tiempo real durante el levantamiento mismo. “Ya que contábamos con esta información antes del ensamblado, fue posible delinear una estrategia para rehacer los huecos y elaborar cierres ligeramente más grandes para usarlos con los huecos incorrectos,” agregó el Dr Yates.
El ensamblado de la locomotora se lleva a cabo en una empresa de ingeniería especialista de Sheffield, CTL Seal Ltd, que también funciona como la sede de grupo de voluntarios de Standard Steam después de que CTL Seal generosamente asignó parte de su taller para ofrecer al grupo un espacio especializado para la fabricación de la locomotora perdida.
La estructura de la locomotora incluye placas para la estructura principal que se mantienen separadas por tensores de estructura de acero, tensores de estructura de acero fundido y tensores de estructura horizontal de acero prensado. Todos estos componentes fueron fabricados por diferentes proveedores por lo que para garantizar que los diversos componentes fueran fabricados con la misma precisión dimensional, el equipo del proyecto requería la confirmación de las dimensiones del ensamblado de la estructura.
Para lograrlo, Yates y el grupo de voluntarios de Standard Steam consiguió apoyo de Hexagon, socio de AMRC, esta vez para probar un nuevo tipo de láser tracker de escaneo directo que funciona sin necesidad de una señal de puntería como un reflector o un palpador portátil – el Leica Absolute Tracker ATS600. Su capacidad de escaneo resultó ideal para la tarea, explicó Yates, y Hexagon prestó uno para el proyecto junto con la experiencia de sus ingenieros de aplicación, Tim Gears y Barry Dimelow.
“Hexagon ha apoyado a AMRC a través de su sociedad de nivel avanzado desde 2013,” comentó Gears. Hemos trabajado en diversos proyectos, pero ninguno tan interesante como el escaneo de una locomotora de vapor de la década de 1950. La versatilidad de nuestro ATS600, y la flexibilidad que nos ofreció el escaneo sin reflector, lo convirtió en la herramienta perfecta de medición para el trabajo.”
El ATS600 es un escáner de grado metrológico de gran volumen que combina fácilmente el escaneo directo de la superficie con la medición de reflector de punto individual. Con un escaneo directo con alcance de hasta 60 metros, puede escanear a velocidades de hasta 10 segundos por metro cuadrado. También es compatible con flujos de trabajo de metrología establecidos gracias a su incorporación con software líder de metrología como SpatialAnalyzer e Inspire. Esto permite tener disponibles los datos de la nube de puntos del ATS600 directamente en el software de aplicación para una realimentación inmediata – extremadamente útil para aplicaciones de construcción e inspección.
El área de escaneo se definió al seleccionar las regiones de interés de la estructura en el modelo CAD y definiendo la separación entre puntos necesaria. Los elementos principales como las guías de la bocina y los nidos de los orificios de referencia fueron medidos con el palpado con un retrorreflector.El sistema dejó una impresión muy positiva en el equipo de Standard Steam. Las mediciones desde el primer escaneo, que consistió de 2788 puntos, solo demoró dos minutos y mostró una inclinación considerable en la estructura. Otra investigación reveló que la inclinación había sido provocada por una pieza de embalaje que se dejó en el lugar y que se había colocado para permitir el retiro y la colocación de uno de los tensores de la estructura para el mecanizado.
“La deflexión máxima provocada por esta pieza de embalaje era de 8.9 milímetros,” explicó Yates. “El área de escaneo se definió al seleccionar las regiones de interés de la estructura en el modelo CAD y definiendo la separación entre puntos necesaria. Los elementos principales como las guías de la bocina y los nidos de los orificios de referencia fueron medidos con el palpado con un retrorreflector.”
Al usar los datos combinados de escaneo y palpado, fue posible determinar la relación de rotación de las estructuras. “Esto demostró que las estructuras giraban alrededor de un punto entre la segunda y la tercera rueda de accionamiento,” explicó Yates. “El punto en la araña de la válvula de escape tenía una altura de 3.02 milimetros. A los ingenieros de fabricación se les mostró gráficamente la relación entre ambas estructuras.
“Después de aflojar y realinear las estructuras, se completó un segundo escaneo que mostró que las estructuras estaban alineadas y era posible proceder con la fijación final. También se registró la posición y la relación entre las guías de la bocina y los puntos de instalación del cilindro para poder completar el procedimiento final de mecanizado y la sección de referenciación, ahorrando tiempo en la máquina.”
Según Tuner, el levantamiento con escaneo láser demostró ser de gran utilidad para el proyecto. “Ahorró un tiempo considerable comparado con el uso de equipo de medición tradicional y, de forma crucial, permitió efectuar ajustes en tiempo real durante el levantamiento mismo.”
El grupo de la Standard Steam Locomotive Company se ha propuesto el ambicioso reto de recrear, poner en funcionamiento y conservar una clase perdida de locomotora de vapor británica –una Clase estándar 6 o ’Clase Clan’ de los ferrocarriles británicos – usando una combinación de los planos originales de la década de 1950s e ingeniería del siglo XXI. El plan consiste en incorporar el diseño moderno y técnicas de fabricación con tecnologías en su construcción.
El AT402 resultó idea para medir las extensiones de la estructura in situ en el cobertizo del motor, eliminando la necesidad de buscar un lugar especializado para la inspección.Las capacidades de escaneo directo del Leica Absolute Tracker ATS600 demostraron ser de gran utilidad en la etapa de ensamblado del proyecto, ofreciendo ahorros de tiempo considerables al equipo tanto en la evaluación de las piezas entregadas como en su alineación antes de la fijación final. Además, se usó un Leica Absolute Tracker AT402 en una etapa previa del proyecto cuando se requirió la funcionalidad de palpado en un entorno desafiante de almacenamiento en exteriores para medir piezas para su comparación con la documentación.
Esto ocurrió cuando el AMRC participó en un ejercicio de medición de alineación de una estructura principal para el proyecto después de que una revisión del inventario de construcción mostró faltas considerables en la documentación de algunas de las piezas principales con relación a las estructuras de la locomotora.
El Dr Phil Yates es un ingeniero colegiado en el AMRC que trabaja en el desarrollo regional y de las PYME en las instalaciones de Factory 2050, además de ser miembro del grupo de voluntarios de Standard Steam. Explicó que estas faltas en la documentación para algunas de las piezas se deben quizás a que hace 80 años, no existía un vínculo directo entre la oficina de diseño y el taller, ya que la locomotora fue diseñada y construida en ubicaciones diferentes a una distancia de 80 km entre si.
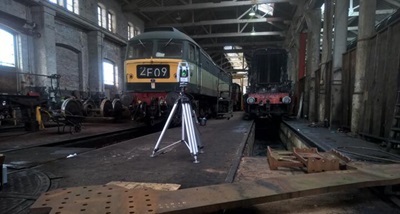
Surgieron más dudas acerca de la funcionalidad de las piezas cuando los planos originales de la década de 1950 de British Rail se digitalizaron y se convirtieron a modelos de diseño asistido por computadora (CAD). “Uno de los principales componentes que provocó serias dudas fueron las extensiones de la estructura,” explicó el Dr Yates. “El modelo CAD había sido generado después de que la pieza había sido fabricada antes de la producción de las placas de la estructura. La forma como los patrones de los agujeros para sujeción habían sido referenciados sobre la estructura y las extensiones de la estructura no eran iguales, por lo que cuando las piezas fueron alineadas en CAD los agujeros para sujeción no coincidían. El error máximo en los componentes CAD era de 1.6 milímetros. El error surgió debido a que los dos planos originales no coincidían. Quien elaboró el plano de la estructura o quien generó el plano de las extensiones de la estructura cometió algún error o hizo algo diferente, lo cual explica que no coincidieran.”
Una escasa habilidad como delineante y la falta de comprensión de los métodos de fabricación puede provocar una mala interpretación de los planos, un problema en aquel momento y que sigue siendo actual. La comprensión de los métodos de fabricación resulta esencial al dimensionar los planos con claridad. Ya que las estructuras y sus extensiones habían sido perfiladas con láser por empresas diferentes a las que generó los planos originales, se asumió que estos errores existían ya en las piezas. Para establecer la dimensión del error, las estructuras y las extensiones de la estructura – que se guardaron en lugares diferentes – debían ser medidos.
Para medir las extensiones de la estructura, que se guardaron en los trabajos de East Lancashire Railway, el Dr Yates y el equipo de Factory 2050 efectuaron una inspección con IA, Tom Hodgson, usó un láser tracker Leica Absolute Tracker AT402 combinado con un Leica B-Probe. La máquina de medición por coordenadas portátil fue fabricada por la división de Manufacturing Intelligence de Hexagon, socio de investigación de primer nivel de AMRC. Permite la obtención de gran precisión en grandes distancias y su sensor de palpado portátil B-Probe resultó ser la herramienta ideal de medición para evaluar las extensiones de 4 metros de largo de la estructura de una locomotora de vapor.
“Tom Hodgson y yo efectuamos el trabajo de medición en las extensiones de la estructura,” comentó el Dr Yates. “Habían sido guardadas en un cobertizo helado y teníamos que tomar en cuenta ese detalle ya que la temperatura puede afectar el trabajo de medición. Los materiales se pueden encoger y dilatar con los cambios de temperatura. Tomar esto en cuenta implica algunos cálculos matemáticos por lo que lo compensamos lo mejor posible calculando cuánto se movería el material con una diferencia de 10 grados de temperatura.”
Según Geoff Turner, director del grupo de ingenieros, el acceso a la experiencia de AMRC y el avanzado equipo de Hexagon permitió la obtención rápida y precisa de datos y la pronta corrección de los errores. “El AT402 resultó ideal para la medición de las extensiones de la estructura in situ en el cobertizo del motor, anulando la necesidad de encontrar un área especializada de inspección y ofreciéndonos datos precisos en tres planos al identificar los errores que fue posible corregir,” explicó Turner.
Ahorramos mucho tiempo comparado con el uso de equipo de medición tradicional y, forma crucial, fue posible efectuar ajustes en tiempo real durante el levantamiento mismo. “Ya que contábamos con esta información antes del ensamblado, fue posible delinear una estrategia para rehacer los huecos y elaborar cierres ligeramente más grandes para usarlos con los huecos incorrectos,” agregó el Dr Yates.
El ensamblado de la locomotora se lleva a cabo en una empresa de ingeniería especialista de Sheffield, CTL Seal Ltd, que también funciona como la sede de grupo de voluntarios de Standard Steam después de que CTL Seal generosamente asignó parte de su taller para ofrecer al grupo un espacio especializado para la fabricación de la locomotora perdida.
La estructura de la locomotora incluye placas para la estructura principal que se mantienen separadas por tensores de estructura de acero, tensores de estructura de acero fundido y tensores de estructura horizontal de acero prensado. Todos estos componentes fueron fabricados por diferentes proveedores por lo que para garantizar que los diversos componentes fueran fabricados con la misma precisión dimensional, el equipo del proyecto requería la confirmación de las dimensiones del ensamblado de la estructura.
Para lograrlo, Yates y el grupo de voluntarios de Standard Steam consiguió apoyo de Hexagon, socio de AMRC, esta vez para probar un nuevo tipo de láser tracker de escaneo directo que funciona sin necesidad de una señal de puntería como un reflector o un palpador portátil – el Leica Absolute Tracker ATS600. Su capacidad de escaneo resultó ideal para la tarea, explicó Yates, y Hexagon prestó uno para el proyecto junto con la experiencia de sus ingenieros de aplicación, Tim Gears y Barry Dimelow.
“Hexagon ha apoyado a AMRC a través de su sociedad de nivel avanzado desde 2013,” comentó Gears. Hemos trabajado en diversos proyectos, pero ninguno tan interesante como el escaneo de una locomotora de vapor de la década de 1950. La versatilidad de nuestro ATS600, y la flexibilidad que nos ofreció el escaneo sin reflector, lo convirtió en la herramienta perfecta de medición para el trabajo.”
El ATS600 es un escáner de grado metrológico de gran volumen que combina fácilmente el escaneo directo de la superficie con la medición de reflector de punto individual. Con un escaneo directo con alcance de hasta 60 metros, puede escanear a velocidades de hasta 10 segundos por metro cuadrado. También es compatible con flujos de trabajo de metrología establecidos gracias a su incorporación con software líder de metrología como SpatialAnalyzer e Inspire. Esto permite tener disponibles los datos de la nube de puntos del ATS600 directamente en el software de aplicación para una realimentación inmediata – extremadamente útil para aplicaciones de construcción e inspección.
El área de escaneo se definió al seleccionar las regiones de interés de la estructura en el modelo CAD y definiendo la separación entre puntos necesaria. Los elementos principales como las guías de la bocina y los nidos de los orificios de referencia fueron medidos con el palpado con un retrorreflector.El sistema dejó una impresión muy positiva en el equipo de Standard Steam. Las mediciones desde el primer escaneo, que consistió de 2788 puntos, solo demoró dos minutos y mostró una inclinación considerable en la estructura. Otra investigación reveló que la inclinación había sido provocada por una pieza de embalaje que se dejó en el lugar y que se había colocado para permitir el retiro y la colocación de uno de los tensores de la estructura para el mecanizado.
“La deflexión máxima provocada por esta pieza de embalaje era de 8.9 milímetros,” explicó Yates. “El área de escaneo se definió al seleccionar las regiones de interés de la estructura en el modelo CAD y definiendo la separación entre puntos necesaria. Los elementos principales como las guías de la bocina y los nidos de los orificios de referencia fueron medidos con el palpado con un retrorreflector.”
Al usar los datos combinados de escaneo y palpado, fue posible determinar la relación de rotación de las estructuras. “Esto demostró que las estructuras giraban alrededor de un punto entre la segunda y la tercera rueda de accionamiento,” explicó Yates. “El punto en la araña de la válvula de escape tenía una altura de 3.02 milimetros. A los ingenieros de fabricación se les mostró gráficamente la relación entre ambas estructuras.
“Después de aflojar y realinear las estructuras, se completó un segundo escaneo que mostró que las estructuras estaban alineadas y era posible proceder con la fijación final. También se registró la posición y la relación entre las guías de la bocina y los puntos de instalación del cilindro para poder completar el procedimiento final de mecanizado y la sección de referenciación, ahorrando tiempo en la máquina.”
Según Tuner, el levantamiento con escaneo láser demostró ser de gran utilidad para el proyecto. “Ahorró un tiempo considerable comparado con el uso de equipo de medición tradicional y, de forma crucial, permitió efectuar ajustes en tiempo real durante el levantamiento mismo.”