Die Wiederentdeckung der Dampflokomotiven-Produktion
Vom direkten Scanning bis zur Erfassung verdeckter Punkte im Freien – Hexagons bahnbrechende Laser-Tracker-Technologie spielte beim Nachbau eines fast vergessenen Klassikers des britischen Schienenfahrzeugdesigns eine Schlüsselrolle.
Kontakt

Ein seit den 1960er Jahren nicht mehr gesehener Dampfzug wird von einer Gruppe von Technikbegeisterten mit Unterstützung der Messtechnik-Experten des Forschungszentrums für moderne Fertigung (AMRC) der Universität Sheffield wieder aufgebaut. Mithilfe der modernen Industrie-Laser-Tracker von Hexagon konnte das Team eine rätselhafte Maßabweichung zwischen den Originalzeichnungen und der realen Lokomotive aufklären.
Die Standard Steam Locomotive Company verfolgt ein ehrgeiziges Ziel: den Nachbau, Betrieb und die Erhaltung einer fast vergessenen britischen Dampfzugklasse – einer British Railways Standard Class 6 ‘Clan’. Dafür kommen sowohl die originalen Konstruktionszeichnungen von 1950 als auch die Technik des 21. Jahrhundert zum Einsatz. Der Plan ist, moderne Konstruktions- und Fertigungstechniken sowie fortschrittliche Technologien beim Nachbau zu nutzen.
Der AT402 eignete sich ideal für die Vermessung der Rahmenverlängerungen direkt im Lokschuppen, sodass kein spezieller Messraum gefunden werden musste.Die direkte Scanningfunktion des Leica Absolute Trackers ATS600 erwies sich in der Montagephase des Projekts als äußerst nützlich. Sowohl beim Überprüfen der gelieferten Teile als auch bei ihrer Ausrichtung vor der endgültigen Montage erzielte das Team damit erhebliche Zeitersparnisse. Darüber hinaus kamen zu Beginn des Projekts die Probingfunktionen eines Leica Absolute Tracker AT402 zum Einsatz, als das AMRC für einen Abgleich mit der vorliegenden Dokumentation umfangreiche Teilemessungen im anspruchsvollen Umfeld einer offenen Lagerfläche durchführte.
Diese Messungen zur Ausrichtung der Rahmen waren notwendig geworden, nachdem sich bei einer Überprüfung des Teilebestandes kritische Dokumentationslücken für einige Schlüsselteile der Lokomotivenrahmen zeigten.
Der staatlich geprüfte Ingenieur Dr. Phil Yates, der sich mit Regionalentwicklung sowie der Weiterentwicklung von KMU an der Einrichtung ‚Factory 2050‘ des AMRC beschäftigt, ist zugleich Mitglied der ehrenamtlich arbeitenden Gruppe Standard Steam. Er nimmt an, dass diese Dokumentationslücken für einige der Teile der vor 80 Jahren vorherrschenden Arbeitsweise geschuldet sind. Damals gab es keine unmittelbare Verbindung zwischen dem Konstruktionsbüro und der Produktion, denn Konstruktion und Herstellung fanden an zwei unterschiedlichen, über 50 Meilen voneinander entfernten Standorten statt.
„Die Standard Class wurde in einem Konstruktionsbüro des Werks in Derby entworfen. Die Herstellung der Lokomotiven fand zwischen 1951 und 1954 jedoch im Eisenbahnwerk der British Railways in Crewe statt. Das Konstruktionsbüro lag also weit von der Produktionsstätte der Lokomotiven entfernt. Zudem arbeiteten die Beschäftigten damals eher anhand ihrer Erfahrungen als auf der strikten Grundlage von Zeichnungen. Darüber hinaus gilt es zu bedenken, dass die Zeichnung keine Angaben zur Herstellungsweise der Teile enthält. Das sind die Gründe für diese Fehler – und sie verdeutlichen uns klar die Trennung zwischen Konstruktionsbüro und Produktion.“
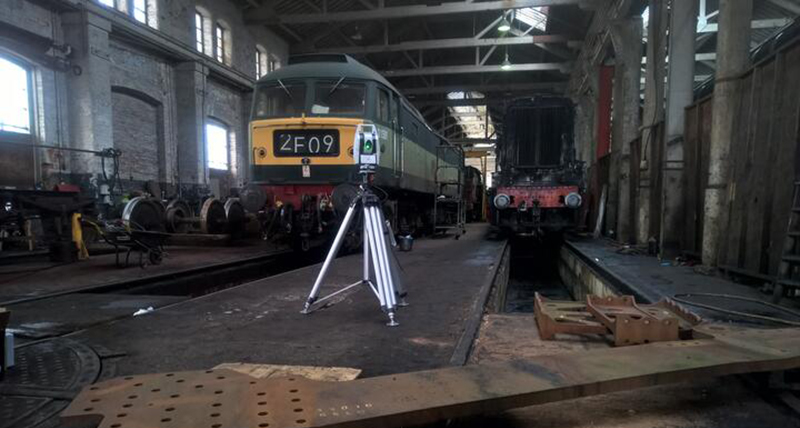
Sowohl mangelnde zeichnerische Präzision als auch die Unkenntnis der Fertigungsmethoden kann zu Fehlinterpretationen von Zeichnungen führen. Das ist heute wie damals ein Problem. Ein tiefgreifendes Verständnis der Fertigungsmethoden ist für die eindeutige Bemaßung von Zeichnungen unerlässlich. Die Rahmen und ihre Verlängerungen fertigten andere Betriebe als das Unternehmen, das die Originalzeichnungen erstellte. Das führte zu der Annahme, die Teile seien fehlerhaft. Zum Ermitteln der Fehlergröße galt es, die Rahmen und Rahmenverlängerungen – die an unterschiedlichen Orten gelagert wurden – zu messen.
Für die Messung der Rahmenverlängerungen, die im Eisenbahnwerk in East Lancashire lagerten, nutzten Dr. Yates und Tom Hodgson (Teamleiter Prüfungen und KI der Factory 2050) einen Leica Absolute Tracker AT402 in Kombination mit einer Leica B-Probe. Das mobile Koordinatenmessgerät ist ein Produkt der Hexagon-Sparte Manufacturing Intelligence, einem Hauptpartner des AMRC. Der Laser Tracker bietet höchste Präzision über große Entfernungen hinweg – und der handgeführte Messsensor B-Probe ist das ideale Messinstrument für die 4 Meter langen Rahmenverlängerungen einer Dampflokomotive.
„Tom Hodgson und ich führten die Messungen der Rahmenverlängerungen durch“, so Dr. Yates. „Dass sie in einem eiskalten Schuppen lagerten, war ein zu berücksichtigender Faktor, da sich die Temperatur auf die Messungen auswirkt. Bei Temperaturschwankungen ziehen sich Werkstoffe zusammen oder dehnen sich aus. Um dem Rechnung zu tragen, bedarf es einiger kniffliger Berechnungen. Durch Messen der Materialveränderungen bei einem Temperaturunterschied von 10 Grad konnten wir diese Schwankungen bestmöglich kompensieren.”
Im Vergleich zu unserer herkömmlichen Messausrüstung sparten wir enorm viel Zeit ein. Darüber hinaus war entscheidend, dass sich bereits während der Vermessung Echtzeit-Anpassungen vornehmen ließen.Laut Geoff Turner, dem technischen Direktor der Gruppe, sorgte sowohl das Fachwissen des AMRC als auch die hochmoderne Ausrüstung von Hexagon für das schnelle Erfassen präziser Daten sowie ein zügiges Abstellen der Fehler. „Der AT402 eignete sich ideal für die Vermessung der Rahmenverlängerungen direkt im Lokschuppen. So musste kein spezieller Messraum gefunden werden. Des Weiteren erhielten wir präzise Daten aus drei Ebenen, mithilfe derer wir die Fehler identifizieren und korrigieren konnten“, sagt Turner.
„Da wir dies bereits vor der Montage wussten, konnten wir eine Strategie für die Nachbearbeitung der Bohrungen entwickeln sowie etwas überdimensionierte Befestigungen für diejenigen Stellen herstellen, an denen die Bohrungen nicht passten“, fügt Dr. Yates hinzu.
Die Montage der Lokomotive übernimmt eine spezialisiertes Ingenieurbüro aus Sheffield, CTL Seal Ltd. Nachdem CTL Seal der ehrenamtlich arbeitenden Standard-Steam-Gruppe großzügigerweise einen Teil seiner Produktionshalle für den Nachbau der verloren geglaubten Lokomotive zu Verfügung stellte, fungiert das Unternehmen nun gleichzeitig als Hauptquartier des Teams.
Der Rahmen der Lokomotive besteht aus Hauptrahmenplatten, die von speziell angefertigten und gegossenen Rahmenverbindern aus Stahl sowie horizontalen Rahmenverbindern aus Pressstahl auseinander gehalten werden. Unterschiedliche Lieferanten stellten eine Vielzahl verschiedenster Komponenten her. Um ihre Maßhaltigkeit zu gewährleisten, benötigte das Projektteam eine Bestätigung der Abmaße der Rahmenbaugruppe.
Hierfür holten sich Yates und die Standard-Steam-Gruppe weitere Unterstützung beim AMRC-Partner Hexagon. Diesesmal testeten sie den Leica Absolute Tracker ATS600. Der neuartige direkt scannende Laser Tracker erfordert weder Messmarken wie einen Reflektor noch einen handgeführten Messtaster. Seine Scanningfunktionen seien ideal für diese Aufgabe geeignet, so Yates, und Hexagon stellte dem Projekt eines der Geräte sowie zwei erfahrene Anwendungstechniker – Tim Gears und Barry Dimelow – zur Verfügung.
„Hexagon unterstützt das AMRC über unsere Partnerschaft bereits seit 2013“, sagt Gears. „Wir haben schon an vielen Projekten mitgewirkt, aber bisher war keines so interessant wie das Scannen einer Dampflokomotive aus den 1950er Jahren. Dank seiner Vielseitigkeit und der Flexibilität, die wir durch das Scannen ohne Reflektoren erhielten, war unser ATS600 das ideale Messinstrument für diese Aufgabe.“
Der ATS600 ist ein messtechnisch hochwertiger Scanner für große Messvolumen, der das direkte Oberflächenscanning nahtlos mit Einzelpunkt-Reflektormessungen kombiniert. Mit einer Reichweite von bis zu 60 Metern für das direkte Scanning, scannt er mit Geschwindigkeiten von bis zu 10 Sekunden pro Quadratmeter. Dank seiner Integration in führende Messsoftwareprogramme wie SpatialAnalyzer und Inspire ist er zudem mit etablierten Metrologie-Workflows kompatibel. Damit stehen die Punktwolkendaten des ATS600 direkt in der Anwendungssoftware für ein sofortiges Feedback zur Verfügung. Das ist bei Montageund Prüfanwendungen unglaublich nützlich.
Das Festlegen des Scanbereichs erfolgte durch Auswählen der betreffenden Rahmenbereiche im CAD und anschließendes Einstellen der notwendigen Punkteabstände. Schlüsselmerkmale wie Führungen und Bezugsbohrungen sowie die Referenznester wurden mittels Antasten mit Retroreflektor vermessen.Das System beeindruckte das Team von Standard Steam. Messergebnisse aus dem ersten Scanningdurchlauf mit 2.788 Punkten nahmen lediglich zwei Minuten in Anspruch und zeigten eine signifikante Verbiegung des Rahmens. Weitere Erkundungen ergaben, dass eine vergessene Unterlage die Biegung verursachte. Zweck dieser Unterlage war, einen der Rahmenverbinder zur maschinellen Bearbeitung entnehmen und später wieder montieren zu können.
„Die Unterlage verursachte eine maximale Durchbiegung von 8,9 Millimetern“, sagt Yates. „Das Festlegen des Scanbereichs erfolgte durch Auswählen der betreffenden Rahmenbereiche im CAD und anschließendes Einstellen der notwendigen Punkteabstände. Schlüsselmerkmale wie Führungen und Bezugsbohrungen sowie die Referenznester wurden mittels Probing mit Retroreflektor vermessen.”
Mithilfe der kombinierten Scanning- und Probingdaten ließ sich das Rotationsverhältnis der Rahmen feststellen. „Es zeigte sich, dass die Rahmen um einen Punkt zwischen dem zweiten und dritten Antriebsrad rotierten“, erläutert Yates. „Der Punkt am Dampfausströmrohr war 3,02 Millimeter hoch. Den Fertigungsingenieuren wurde das Verhältnis der beiden Rahmen zueinander grafisch angezeigt.
„Nach dem Lockern und neuen Positionieren der Rahmen bestätigte ein neuer Scan die exakte Ausrichtung der Rahmen und sie konnten vernietet werden. Sowohl die Position als auch das Verhältnis der Führungen sowie der Befestigungspunkte des Zylinders zueinander wurde ebenfalls dokumentiert. So ließ sich im abschließenden Bearbeitungvorgang ein Antast- und Kalibrierabschnitt beenden und damit Zeit an der Maschine einsparen.”
Die Vermessung mit dem Laserscanner erwies sich laut Turner ebenso als außerordentlich hilfreich für das Projekt. „Im Vergleich zu unserer herkömmlichen Messausrüstung sparten wir enorm viel Zeit ein. Darüber hinaus war entscheidend, dass sich bereits während der Vermessung Echtzeit-Anpassungen vornehmen ließen.”