Découvrir les secrets de la fabrication des locomotives à vapeur
Unique en son genre, la technologie laser tracker Hexagon a joué un rôle clé dans la reconstruction d’une vieille locomotive classique britannique, en intervenant dans des applications comme le scanning direct ou le palpage de points cachés, en extérieur.
Contact

Un train à vapeur disparu depuis les années 1960, revoit le jour grâce au travail d’un groupe d’adeptes de l’ingénierie, assisté par des experts en métrologie du centre de recherche en fabrication avancée de l’université de Sheffield (AMRC). Avec l’aide de la technologie avancée industrielle du laser tracker d’Hexagon, l’équipe a pu prendre la mesure d’une mystérieuse divergence, entre les dessins originaux et la locomotive réelle.
Le groupe de Standard Steam Locomotive Company s'est fixé lui-même l'objectif ambitieux de reconstruire, d'exploiter et d'entretenir un train à vapeur britannique de la classe Standard 6 (Clan) de British Railways, en s'appuyant sur les plans de conception originaux des années 1950 et sur l'ingénierie du 21e siècle. Le but est d'intégrer des techniques de conception et de fabrication modernes et des technologies avancées dans la construction.
L'AT402 était idéal pour mesurer les extensions de cadre placées dans le hangar, en évitant de rechercher une salle d'inspection adaptée.Les fonctionnalités de scanning direct du Leica Absolute Tracker ATS600 se sont révélées très utiles dans la phase d'assemblage du projet. Elles ont permis à l'équipe de gagner beaucoup de temps dans l'analyse des pièces fournies et leur ajustement avant le montage final. A un stade anticipé du projet, les spécialistes ont utilisé un Leica Absolute Tracker AT402 pour mesurer des pièces par palpage dans un environnement extérieur exigeant, en vue de leur comparaison avec la documentation.
En effet, après avoir constaté qu'il manquait beaucoup de documentation sur la construction de certaines pièces clés relatives aux cadres de la locomotive, le relevé des mesures d'alignement a été mis en place par le centre AMRC.
Le Dr Phil Yates est ingénieur expert et travaille au centre AMRC sur le développement régional et l’activité de PME dans l’unité Factory 2050 du centre. Il est aussi membre du groupe de bénévoles Standard Steam. Il explique que les lacunes dans la documentation de certaines pièces proviennent de l’absence de contacts entre les dessinateurs et l’atelier de fabrication, il y a 80 ans. La locomotive a en effet été conçue et construite sur des sites distants d’environ 80 kilomètres.
"La Standard Class était conçue dans le bureau de dessinateur de Derby Works, alors que les locomotives étaient construites dans l'usine Crewe Works de British Railways entre 1951 et 1954. Ce bureau était donc loin du lieu de fabrication de la locomotive et, à l'époque, on se basait plutôt sur ses propres connaissances que sur des plans pour fabriquer des éléments. Il ne faut pas oublier que le plan ne montre pas comment une pièce est fabriquée. D'où ces erreurs. Elles révèlent la déconnexion entre le bureau de dessinateur et l'atelier de fabrication."
D’autres doutes sur la fonctionnalité des pièces ont été soulevés lorsque les dessins originaux de British Rail des années 1950 ont été convertis et transformés en modèles de conception assistée par ordinateur (CAO). “L’un des principaux éléments qui a suscité de sérieuses inquiétudes était les extensions du cadre”, explique le Dr Yates. “La CAO avait été produite après que la pièce ait été fabriquée et avant la fabrication des plaques du cadre principal.
La façon dont les modèles de trous de fixation avaient été datés sur le cadre et les extensions du cadre n’était pas identique, donc lorsque les pièces étaient alignées dans la CAO, les trous de fixation ne s’alignaient pas. L’erreur maximale sur les composants CAO était de 1,6 millimètres. L’erreur était due au fait que les deux dessins originaux ne correspondaient pas. La personne qui a fait le dessin du cadre et celle qui a fait le dessin des extensions du cadre sont deux personnes différentes ce qui en résulte qu’il n’y a pas un alignement correct.”
Le manque d'aptitudes au dessin et la non-compréhension de méthodes de fabrication peuvent conduire à des erreurs d'interprétation de plans. Ce problème est toujours actuel. Il est essentiel de comprendre les méthodes de production pour réaliser des plans clairs. Comme les entreprises qui usinaient les cadres et les extensions étaient différentes de celle qui a établi le plan original, on a supposé que ces erreurs étaient reproduites dans les pièces. Pour évaluer l'étendue de l'erreur, il a fallu mesurer les cadres et leurs extensions stockés sur des sites différents.
Pour relever les extensions, placées dans l'usine ferroviaire d'East Lancashire Railway à Bury, le Dr Yates et Tom Hodgson, responsable de l'inspection et de l'IA au sein de l'équipe Factory 2050, ont utilisé un laser tracker Leica Absolute Tracker AT402 avec un Leica B-Probe. Cette machine à mesurer tridimensionnelle portable provient de la division Manufacturing Intelligence de Hexagon, un partenaire de recherche privilégié de l'AMRC.
Elle fournit une précision extrême sur de grandes distances, et son palpeur portable B-Probe était l'instrument idéal pour relever les extensions de cadre de 4 mètres d'une locomotive à vapeur.
Il a permis d'effectuer des mesures bien plus rapides qu'un équipement classique, et des ajustements en temps réel pendant l'exécution du levé."Tom Hodgson et moi-même avons mesuré les extensions de cadre", explique le Dr Yates. "Nous devions prendre en compte que ces pièces étaient stockées dans un hangar glacial. Les matériaux peuvent rétrécir et se dilater lorsque les températures changent. Ce phénomène est pris en compte par des calculs mathématiques complexes, et nous avons essayé de le compenser le mieux possible en mesurant les mouvements du matériau dans une tranche de variation de température de 10°C Selon Geoff Turner, le directeur de l'ingénierie du groupe, la disponibilité des compétences de l'AMRC et de l'équipement avancé Hexagon, a permis une collecte de données rapide et précise, de même qu'une élimination rapide des erreurs. “L’AT402 était l’instrument idéal pour mesurer les extensions de cadre sur place, en évitant de rechercher une salle d’inspection adaptée et en fournissant des données précises sur les trois plans. Cela nous a permis d’identifier les erreurs et de les corriger”, ajoute Geoff Turner.
"Comme nous le savions avant l'assemblage, nous avons pu élaborer une stratégie pour refaire les orifices et réaliser des éléments de fixation légèrement surdimensionnés pour les trous mal placés", poursuit le Dr Yates.
La locomotive est assemblée sur le site de l'entreprise d'ingénierie CTL Seal Ltd, à Sheffield, qui est en même temps le siège du groupe de bénévoles Standard Steam depuis que CTL Seal a généreusement laissé à cette équipe une partie de l'atelier de fabrication pour construire la locomotive disparue.
Le cadre de la locomotive comprend des plaques principales, séparées par des écarteurs fabriqués et coulés en acier, ainsi que par des espaceurs horizontaux pressés en acier. Comme tous ces composants étaient fabriqués par différents fournisseurs, l'équipe de projet avait besoin d'obtenir une confirmation des dimensions de l'assemblage du cadre pour garantir la fabrication de toutes les pièces avec la même précision dimensionnelle.
À cet effet, le Dr Yates et le groupe de bénévoles de Standard Steam se sont adressés à Hexagon, partenaire du centre AMRC, et ont cette fois essayé un nouveau type de laser tracker, le Leica Absolute Tracker ATS600, qui assure un scanning direct, sans cible (par exemple réflecteur ou palpeur portable). Sa fonctionnalité de scanning convenait parfaitement à la tâche, selon le Dr Yates, et Hexagon a prêté un modèle à l'équipe de projet, qui bénéficiait aussi de l'assistance des ingénieurs d'application Tim Gears et Barry Dimelow.
"Hexagon assiste le centre AMRC depuis le début de notre partenariat en 2013", indique Tim Gears. "Nous avons participé à de nombreux projets, mais le plus intéressant était le scanning d'une locomotive à vapeur datant des années 1950. Grâce à la polyvalence de l'ATS600 et à la flexibilité du scanning sans réflecteur, c'était un équipement de mesure idéal pour cette tâche."
L'ATS600 est un scanner de niveau métrologique pour de grands volumes, qui réalise un scanning de surface direct et des mesures de points individuels sur réflecteur. Avec une portée de scanning direct jusqu'à 60 mètres, il peut effectuer des scans à une vitesse jusqu'à 10 secondes par mètre carré. Il est aussi compatible avec les flux de travail métrologiques bien établis, grâce à son interfaçage avec des logiciels de métrologie leaders, comme SpatialAnalyzer et Inspire. Cela permet de traiter les données de nuage de points de l'ATS600 directement dans un logiciel d'application et d'obtenir ainsi un retour immédiat, une fonctionnalité très utile pour les applications de construction et d'inspection.
La surface scannée était définie par la sélection de zones précises du cadre CAO, puis par le réglage de l'espacement de points nécessaire. Des caractéristiques clés comme les guides du klaxon, orifices et logements de référence ont été mesurées avec un système de palpage et un rétroréflecteur.Le système n'a pas manqué d'impressionner l'équipe Standard Steam. Les mesures du premier scan, soit 2 788 points, ont juste prix deux minutes et ont révélé une courbure importante du cadre. Des examens plus poussés ont fait apparaître que cette déformation avait été provoquée par un élément d'emballage resté en place. Celui-ci avait été monté pour permettre le retrait et le remplacement de l'un des espaceurs de cadre en vue de l'usinage.
"La déflexion maximale causée par cette pièce était de 8,9 millimètres", note le Dr Yates. "La surface scannée était définie par la sélection de zones précises du cadre CAO, puis par le réglage de l'espacement de points nécessaire. Des éléments clés comme les guides du klaxon et logements de référence ont été mesurés par palpage avec un rétroréflecteur."
En utilisant les données de scan et de palpage combinées, il a été possible de déterminer la relation de rotation des cadres. "Ces données ont montré que les cadres tournaient autour d'un point entre la deuxième et la troisième roue motrice", indique le Dr Yates. "Le point sur le croisillon d'échappement de vapeur avait une hauteur de 3,02 millimètres. Les ingénieurs de fabrication ont pu visualiser sous forme graphique la relation entre les deux cadres.
"Après le détachement et le réalignement des cadres, on a réalisé un deuxième scan, qui a confirmé l'alignement des cadres, et cela a permis d'effectuer le vissage final. Comme la position et la relation entre les guides du klaxon et les points de fixation de cylindre ont également été enregistrées, une section de palpage et de référencement a pu être réalisée pendant la phase d'usinage final. Cela a permis de gagner du temps sur la machine."
Le scanning laser a fourni une autre aide précieuse dans le cadre de ce projet, selon Geoff Turner. Il a permis d'effectuer des mesures bien plus rapides qu'un équipement classique, et des ajustements en temps réel pendant l'exécution du levé."
Le groupe de Standard Steam Locomotive Company s'est fixé lui-même l'objectif ambitieux de reconstruire, d'exploiter et d'entretenir un train à vapeur britannique de la classe Standard 6 (Clan) de British Railways, en s'appuyant sur les plans de conception originaux des années 1950 et sur l'ingénierie du 21e siècle. Le but est d'intégrer des techniques de conception et de fabrication modernes et des technologies avancées dans la construction.
L'AT402 était idéal pour mesurer les extensions de cadre placées dans le hangar, en évitant de rechercher une salle d'inspection adaptée.Les fonctionnalités de scanning direct du Leica Absolute Tracker ATS600 se sont révélées très utiles dans la phase d'assemblage du projet. Elles ont permis à l'équipe de gagner beaucoup de temps dans l'analyse des pièces fournies et leur ajustement avant le montage final. A un stade anticipé du projet, les spécialistes ont utilisé un Leica Absolute Tracker AT402 pour mesurer des pièces par palpage dans un environnement extérieur exigeant, en vue de leur comparaison avec la documentation.
En effet, après avoir constaté qu'il manquait beaucoup de documentation sur la construction de certaines pièces clés relatives aux cadres de la locomotive, le relevé des mesures d'alignement a été mis en place par le centre AMRC.
Le Dr Phil Yates est ingénieur expert et travaille au centre AMRC sur le développement régional et l’activité de PME dans l’unité Factory 2050 du centre. Il est aussi membre du groupe de bénévoles Standard Steam. Il explique que les lacunes dans la documentation de certaines pièces proviennent de l’absence de contacts entre les dessinateurs et l’atelier de fabrication, il y a 80 ans. La locomotive a en effet été conçue et construite sur des sites distants d’environ 80 kilomètres.
"La Standard Class était conçue dans le bureau de dessinateur de Derby Works, alors que les locomotives étaient construites dans l'usine Crewe Works de British Railways entre 1951 et 1954. Ce bureau était donc loin du lieu de fabrication de la locomotive et, à l'époque, on se basait plutôt sur ses propres connaissances que sur des plans pour fabriquer des éléments. Il ne faut pas oublier que le plan ne montre pas comment une pièce est fabriquée. D'où ces erreurs. Elles révèlent la déconnexion entre le bureau de dessinateur et l'atelier de fabrication."
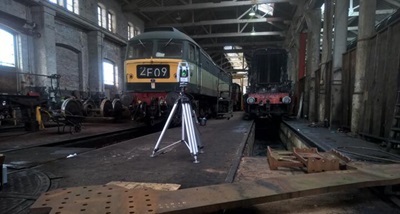
La façon dont les modèles de trous de fixation avaient été datés sur le cadre et les extensions du cadre n’était pas identique, donc lorsque les pièces étaient alignées dans la CAO, les trous de fixation ne s’alignaient pas. L’erreur maximale sur les composants CAO était de 1,6 millimètres. L’erreur était due au fait que les deux dessins originaux ne correspondaient pas. La personne qui a fait le dessin du cadre et celle qui a fait le dessin des extensions du cadre sont deux personnes différentes ce qui en résulte qu’il n’y a pas un alignement correct.”
Le manque d'aptitudes au dessin et la non-compréhension de méthodes de fabrication peuvent conduire à des erreurs d'interprétation de plans. Ce problème est toujours actuel. Il est essentiel de comprendre les méthodes de production pour réaliser des plans clairs. Comme les entreprises qui usinaient les cadres et les extensions étaient différentes de celle qui a établi le plan original, on a supposé que ces erreurs étaient reproduites dans les pièces. Pour évaluer l'étendue de l'erreur, il a fallu mesurer les cadres et leurs extensions stockés sur des sites différents.
Pour relever les extensions, placées dans l'usine ferroviaire d'East Lancashire Railway à Bury, le Dr Yates et Tom Hodgson, responsable de l'inspection et de l'IA au sein de l'équipe Factory 2050, ont utilisé un laser tracker Leica Absolute Tracker AT402 avec un Leica B-Probe. Cette machine à mesurer tridimensionnelle portable provient de la division Manufacturing Intelligence de Hexagon, un partenaire de recherche privilégié de l'AMRC.
Elle fournit une précision extrême sur de grandes distances, et son palpeur portable B-Probe était l'instrument idéal pour relever les extensions de cadre de 4 mètres d'une locomotive à vapeur.
Il a permis d'effectuer des mesures bien plus rapides qu'un équipement classique, et des ajustements en temps réel pendant l'exécution du levé."Tom Hodgson et moi-même avons mesuré les extensions de cadre", explique le Dr Yates. "Nous devions prendre en compte que ces pièces étaient stockées dans un hangar glacial. Les matériaux peuvent rétrécir et se dilater lorsque les températures changent. Ce phénomène est pris en compte par des calculs mathématiques complexes, et nous avons essayé de le compenser le mieux possible en mesurant les mouvements du matériau dans une tranche de variation de température de 10°C Selon Geoff Turner, le directeur de l'ingénierie du groupe, la disponibilité des compétences de l'AMRC et de l'équipement avancé Hexagon, a permis une collecte de données rapide et précise, de même qu'une élimination rapide des erreurs. “L’AT402 était l’instrument idéal pour mesurer les extensions de cadre sur place, en évitant de rechercher une salle d’inspection adaptée et en fournissant des données précises sur les trois plans. Cela nous a permis d’identifier les erreurs et de les corriger”, ajoute Geoff Turner.
"Comme nous le savions avant l'assemblage, nous avons pu élaborer une stratégie pour refaire les orifices et réaliser des éléments de fixation légèrement surdimensionnés pour les trous mal placés", poursuit le Dr Yates.
La locomotive est assemblée sur le site de l'entreprise d'ingénierie CTL Seal Ltd, à Sheffield, qui est en même temps le siège du groupe de bénévoles Standard Steam depuis que CTL Seal a généreusement laissé à cette équipe une partie de l'atelier de fabrication pour construire la locomotive disparue.
Le cadre de la locomotive comprend des plaques principales, séparées par des écarteurs fabriqués et coulés en acier, ainsi que par des espaceurs horizontaux pressés en acier. Comme tous ces composants étaient fabriqués par différents fournisseurs, l'équipe de projet avait besoin d'obtenir une confirmation des dimensions de l'assemblage du cadre pour garantir la fabrication de toutes les pièces avec la même précision dimensionnelle.
À cet effet, le Dr Yates et le groupe de bénévoles de Standard Steam se sont adressés à Hexagon, partenaire du centre AMRC, et ont cette fois essayé un nouveau type de laser tracker, le Leica Absolute Tracker ATS600, qui assure un scanning direct, sans cible (par exemple réflecteur ou palpeur portable). Sa fonctionnalité de scanning convenait parfaitement à la tâche, selon le Dr Yates, et Hexagon a prêté un modèle à l'équipe de projet, qui bénéficiait aussi de l'assistance des ingénieurs d'application Tim Gears et Barry Dimelow.
"Hexagon assiste le centre AMRC depuis le début de notre partenariat en 2013", indique Tim Gears. "Nous avons participé à de nombreux projets, mais le plus intéressant était le scanning d'une locomotive à vapeur datant des années 1950. Grâce à la polyvalence de l'ATS600 et à la flexibilité du scanning sans réflecteur, c'était un équipement de mesure idéal pour cette tâche."
L'ATS600 est un scanner de niveau métrologique pour de grands volumes, qui réalise un scanning de surface direct et des mesures de points individuels sur réflecteur. Avec une portée de scanning direct jusqu'à 60 mètres, il peut effectuer des scans à une vitesse jusqu'à 10 secondes par mètre carré. Il est aussi compatible avec les flux de travail métrologiques bien établis, grâce à son interfaçage avec des logiciels de métrologie leaders, comme SpatialAnalyzer et Inspire. Cela permet de traiter les données de nuage de points de l'ATS600 directement dans un logiciel d'application et d'obtenir ainsi un retour immédiat, une fonctionnalité très utile pour les applications de construction et d'inspection.
La surface scannée était définie par la sélection de zones précises du cadre CAO, puis par le réglage de l'espacement de points nécessaire. Des caractéristiques clés comme les guides du klaxon, orifices et logements de référence ont été mesurées avec un système de palpage et un rétroréflecteur.Le système n'a pas manqué d'impressionner l'équipe Standard Steam. Les mesures du premier scan, soit 2 788 points, ont juste prix deux minutes et ont révélé une courbure importante du cadre. Des examens plus poussés ont fait apparaître que cette déformation avait été provoquée par un élément d'emballage resté en place. Celui-ci avait été monté pour permettre le retrait et le remplacement de l'un des espaceurs de cadre en vue de l'usinage.
"La déflexion maximale causée par cette pièce était de 8,9 millimètres", note le Dr Yates. "La surface scannée était définie par la sélection de zones précises du cadre CAO, puis par le réglage de l'espacement de points nécessaire. Des éléments clés comme les guides du klaxon et logements de référence ont été mesurés par palpage avec un rétroréflecteur."
En utilisant les données de scan et de palpage combinées, il a été possible de déterminer la relation de rotation des cadres. "Ces données ont montré que les cadres tournaient autour d'un point entre la deuxième et la troisième roue motrice", indique le Dr Yates. "Le point sur le croisillon d'échappement de vapeur avait une hauteur de 3,02 millimètres. Les ingénieurs de fabrication ont pu visualiser sous forme graphique la relation entre les deux cadres.
"Après le détachement et le réalignement des cadres, on a réalisé un deuxième scan, qui a confirmé l'alignement des cadres, et cela a permis d'effectuer le vissage final. Comme la position et la relation entre les guides du klaxon et les points de fixation de cylindre ont également été enregistrées, une section de palpage et de référencement a pu être réalisée pendant la phase d'usinage final. Cela a permis de gagner du temps sur la machine."
Le scanning laser a fourni une autre aide précieuse dans le cadre de ce projet, selon Geoff Turner. Il a permis d'effectuer des mesures bien plus rapides qu'un équipement classique, et des ajustements en temps réel pendant l'exécution du levé."