Retro but fit
Thöni Manufacturing GmbH - Germany
Contact us

The company specialises in processing high precision, medium-sized cubic parts in small or medium production batches. Parts weighing up to five tonnes dominate the production line. From these unfinished cast parts, the company creates housings for wind turbines, tractor frames, axles for forestry vehicles, working tables for processing machines and other large-format components for the machine-making, wind energy and automotive industries.
Fully integrated measuring machines
At the heart of the production facility is the pallet transport system, which moves the parts from one processing centre to the next, stringing together a series of horizontal and vertical processing centres, jig-boring machines, grinding machines and manual work stations. Metrology is also fully integrated into the process.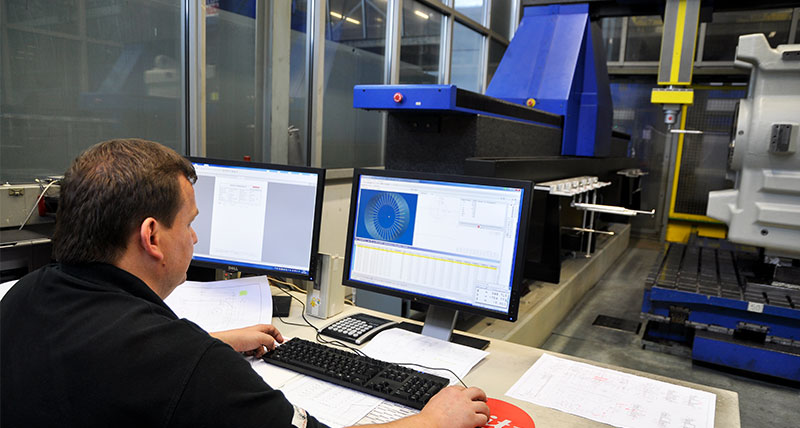
A Leitz PMM with a measuring range of 4000 x 2000 x 1600 mm in a further climatised room is connected to the pallet transport system. This separate capsule ensures a more stable temperature and keeps the measuring machine clean. The parts are transported directly to the measuring machine and measured during series production. Some orders require 100% inspection, others rely on random sampling. Flawless documentation is mandatory for all orders.
Spare parts assured
And the company is growing. In less than one year the workforce has doubled. And the order books are correspondingly full. The 19-year-old measuring machine has had to follow suit. We had no problems with the accuracy of this machine, says Michael Warta, Managing Director of Thöni Manufacturing. The measurement accuracy of the Leitz PMM is between 3 to 5 microns. All features with tolerances of less than 20 microns are measured with the Leitz PMM. However, one very obvious problem was the supply of spare parts, which was no longer 100% assured. A retrofit from Hexagon Metrology provided the remedy.
What remains of the old machine is limited to the basic mechanics. All the wiring, the control cabinet, measuring software, PC and probe head had to give way to 21st century technology. With the new controls, the efficient LSP-S2 probe head from Hexagon Metrology and the new version of QUINDOS 7 software, Thöni is well equipped for the future.
Core components now up-to-date
With the new probe head we can use totally different methods and work much faster. It is also more stable than its predecessor, says Warta. The LSP-S2 probe head can accept horizontal stylus extensions up to 800 mm long and stylus assemblies weighing up to 1000 g. The right choice for Thöni: in order to reach all the features on some large parts, the metrology technician needs long and heavy styli. The LSPS2 is compatible with all standard measurement procedures, such as single-point probing, self-centring tactile probes and continuous high-speed scanning for rapid and accurate measurement of shapes and profiles.
Distinct advantages arose from the software upgrade from QUINDOS 3 to QUINDOS 7. The evaluation and display options provided by the new software is of a completely new class. The software can do so much more and is a great improvement in its own right, says Hodzic, Metrology Technician at Thöni. For example with QUINDOS 7 the inspection records can be saved directly as a pdf file and sent to the customer. The results are graphical and the software easier to use.
Time and cost minimised
In addition to the shorter measuring and programming times gained from the new technology, Thöni was also impressed by the speed with which the upgrade was implemented. The changes were accomplished within four weeks. Bottlenecks in the measuring room are abolished by the modernisation. The delivery and installation of a new machine would have taken much more time. And last but not least there is the price-performance ratio. As a comparison: buying a new system would have burdened the books with a six-figure expenditure.
The potential of the modernised measuring system has yet to be fully exploited. The measuring machine technicians will be attending further QUINDOS training courses to make the most of the full range of functions of the latest software version. Now the old-style programming from the drawing is considered passé. The new software version will allow CAD models to make their début in the measuring room and make the programming even simpler.