Prototype design in 3D for customized sports cars
Contact us

TechArt Automobildesign GmbH is a successful German car design company, specialized in the design development and manufacturing of individually customized cars.
The broad creative design spectrum, which is based on Porsche sport cars, stretches from the complete vehicle body to the interior fittings all the way to customized engine tuning. The prototypes of the car body parts are handmade using glass fiber; for the subsequent serial production, the high resolution digitization technology of an AICON StereoScan is called into action.
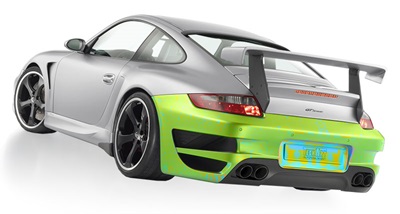
High resolution and accuracy even for demanding measuring objects
The object to be measured is the handshaped prototype of a TechArt GTStreet rear bumper.
The model of the rear bumper is made of glass fibre. The creation of the necessary tooling and molds for the serial production of the final product made of plastic composite is based on a 3D surface model of the rear bumper. As it is not possible to create a perfectly symmetrical model of the complete rear bumper by hand, initially only one half of the fibre glass model is produced which is digitized and subsequently completed into one coherent piece: In the computer aided post-processing phase, the mirror image of the first digitized half-shape model is generated by aid of a special software; both 3D parts are then virtually joined together resulting in a perfectly symmetrical complete object.
The project consists of two main phases: In a first step, the half bumper is captured three-dimensionally with the aid of the AICON StereoScan. In the second step, a surface model is generated using the reverse engineering software Rapidform XOR 2. This high precision 3D surface model is then available as the finished product, ready to serve as basis for further processing or production.
Due to the object involved, this scanning project is extremely demanding with regard to resolution and accuracy standards. A further crucial requirement is flexibility: Even object areas which are difficult to access must be captured at prime level of precision and reliability. Using the three triangulation angles provided with the AICON high-performance measuring system AICON StereoScan combined with the photogrammetry system AICON MoveInspect DPA, all these requirements are met consistently and reliably at the requested high-precision standard.
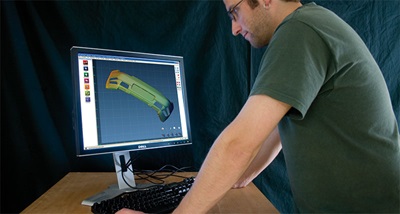
Team of two measuring systems
In a first step, the rear bumper is measured with the aid of an AICON photogrammetry system and coded index markers. Subsequently, once all reference markers have been captured, the AICON StereoScan is called into action to run a series of individual scans of the rear bumper; supported by a special software, these are then automatically aligned in compliance with the reference points of the photogrammetry data. This combined measuring method guarantees optimum quality and accuracy of the three-dimensional representation of the original measuring object.
Finally, having merged the individual scan images to a completed scan model, a surface model is generated with the aid of the parametrical reverse engineering software Rapidform XOR2 and exported as standard surface format IGES or STEP.
Top quality, individual vehicle components
Even involving vast data volumes, an efficient and reliable workflow is guaranteed for each scanning project. The measuring results are instantly available for further processing, enabling a special software to generate the mirror image model of the rear bumper immediately following the digitization of the first half of the rear bumper model. Both digital halves of the rear bumper are then virtually joined together, resulting in a perfectly symmetrical complete object.
In this particular project, the AICON StereoScan delivers a surface file in the IGES standard surface format. Based on these data sets, TechArt is able to carry out necessary shape adjustments in the subsequent stages of the design process.
In the final phase, the tooling for the mass production of the rear bumper is manufactured in cooperation with the Maucher Formenbau GmbH & Co. KG, a specialist provider in the tools and molds industry.
Furthermore, the surface model can be compared against the scan data set. This ensures that both data accuracy and reproduction precision have not been compromised in the course of the reverse engineering process. For all processes involved, AICON’s measuring system promptly and reliably provides the required 3D data at prime level of accuracy. As a result, both the efficient material usage in the tooling manufacturing phase as well as the production of top quality customized rear bumpers, and any other types of vehicle components, are ensured consistently and reliably at all times.
We give thanks to all participating parties for the cooperation in creating this report.