Measuring saves a lot of time
Contact us

Measuring is an important resource for more precise work and time saving – not a luxury but necessity at contract manufacturer Laro. With m&h touch probes and 3D Form Inspect software, many hours are saved and set-up times are reduced considerably.
Since 2001, LARO NC-Technik GmbH has been a legally independent company within the Langer Group and has been manufacturing moulds and tools, prototype parts, small batch volumes and specially commissioned orders. Strengths have been developed in the field of milling, where work-pieces from large to small sizes are machined.
At Laro, large means lengths up to 6 metres and 2.2m in the Z-axis. Dealing with a broad spectrum of different workpieces is the company’s daily business. As well as aluminium and (carbon) tool steel, Laro also cut materials such as duplex and high-alloyed steels plus occasionally titanium and plastics like uriol, lauramit, CRP and GRP. As varied as materials are batch sizes, ranging from one-offs to volumes of 5,000 parts. Laro’s machinery is similarly versatile. The range of machining centres varies from large Henri Linée to Handtmann, FPT Mikron HPM 1000 with 7 pallets, HSM 800, DMU 100T, 70 Evo, and 64V. Because of the high precision required these machining centres are located in an air-conditioned workshop.
The story of m&h touch probes and software at Laro began with the acquisition of a Handtmann machine equipped with an m&h touch probe and measuring software. 3D Form Inspect software from m&h allows checking of the workpiece while still clamped and any required rework can be done immediately and without inaccuracies caused by reclamping of the workpiece. “This saves us a lot of time,” reports managing director Elmar Müller. “There is no need to have a measuring room for production and nobody has to handle a workpiece twice,” he explains. When setting up the workpieces, Elmar Müller could see definite advantages with the touch probe compared to their previous approach. The workpiece is roughly clamped into position and then aligned by the touch probe. This means deviations from the required position are automatically corrected in the control without timecon-suming manual correction of clamping. Machining programs are aligned with the actual position of the workpiece, drastically reducing set-up times particularly for workpieces up to a length of 2.80m. This procedure offers special advantages when setting up unmachined castings.
Castings of this size show different distortions in shape. With 3D Form Inspect the workpieces can be aligned around critical points of a contour, ensuring optimum alignment of part and machining program. This reduces sources of error and gives consistently accurate parts and high process reliability.
The machine operator determines the points and areas to be measured on a computer using mouse clicks based on the CAD data of the workpiece. 3D Form Inspect automatically generates the required measuring program and also creates a calibration program to allow and compensate for thermal changes of the machine axes. This procedure is patented by m&h. This is the only way to achieve reliable and repeatable measured values that can be compared to a measuring machine. The measured values can be displayed on the computer screen immediately after probing and can be printed as a protocol. From this analysis, the operator determines actual workpiece dimensions on the machine and, if necessary, is able to react and make corrections immediately.
Elmar Müller emphasizes the easy use of this software and how problem-free the introduction to the facility was. “Training was made at the same time as the probe installation at our premises and was finished within two days without any problems and using our own workpieces,” he reports. “Afterwards, the assigned staff member was not only able to work with this software but could also pass on his knowledge to others. Perfect.” As a result, the working methods at Laro changed very quickly. “Today we ask ourselves how we ever managed without this software before.” In the past they had to take workpieces to the measu- ring room and wait for results, whereas the workpiece is now measured and critical points are checked while still clamped on the machine immediately after machining. The new possibilities also result in considerable enhancement of our machining strategy, normally resulting in reduced machining times. Today, pockets and critical contours like mould parting surfaces or similar, are programmed and pre-machined at Laro using 5 hundredths allowance. Subsequently, the exact geometry is measured in order to finish precisely to required dimensions. To simplify matters, this is done via the tool correction function in the control. This provides high process reliability and minimizes human error. Also, it simplifies work for the operators and offers them safety previously unknown. This is an important factor when dealing with tolerances in the range of hundredths.
No need for deep thinking, this equipment has definitely paid off.With the Best Fit module, 3D Form Inspect software gives significant advantages and considerable time savings for Laro, even in volume production. This became particularly apparent at Laro when manufacturing guide blades for turbines. Not only did the clamping become significantly less important but time-consuming manual setting of the workpieces became obsolete. The actual position of each workpiece on the machine is determined by probing its contour and the machining program is aligned to the actual position by rotating and shifting the zero points and coordinate planes. Although that takes us a few minutes, “it saves us at least one hour of set-up time per part,” Elmar Müller confirms his experience. “We simply take the critical points, such as sealing or end surfaces of the blades as aligning points and probe the exact positions. The result is that we do not have any measuring or transmission errors any more.”
“The budget needed is relatively low,” Elmar Müller sums up. “No need for deep thinking, this equipment has definitely paid off.” Assuming an average total machining time of 20 hours per workpiece, a one hour reduction means savings of around 5% per part. This results in a considerable enhancement of productivity and capacity. It is process-reliable manufacturing with consistently better quality. This is good for Laro who are certified for the manufacture of aviation parts. It is also a benefit for their staff who are enhanced in status and motivation, another invaluable advantage.
Since 2001, LARO NC-Technik GmbH has been a legally independent company within the Langer Group and has been manufacturing moulds and tools, prototype parts, small batch volumes and specially commissioned orders. Strengths have been developed in the field of milling, where work-pieces from large to small sizes are machined.
At Laro, large means lengths up to 6 metres and 2.2m in the Z-axis. Dealing with a broad spectrum of different workpieces is the company’s daily business. As well as aluminium and (carbon) tool steel, Laro also cut materials such as duplex and high-alloyed steels plus occasionally titanium and plastics like uriol, lauramit, CRP and GRP. As varied as materials are batch sizes, ranging from one-offs to volumes of 5,000 parts. Laro’s machinery is similarly versatile. The range of machining centres varies from large Henri Linée to Handtmann, FPT Mikron HPM 1000 with 7 pallets, HSM 800, DMU 100T, 70 Evo, and 64V. Because of the high precision required these machining centres are located in an air-conditioned workshop.
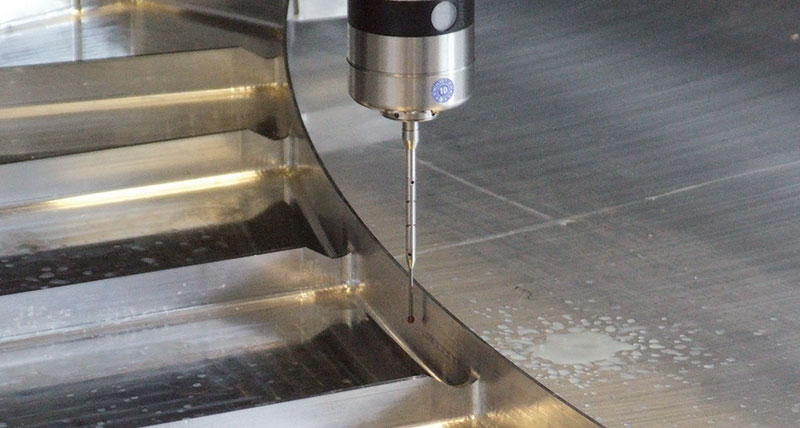
Castings of this size show different distortions in shape. With 3D Form Inspect the workpieces can be aligned around critical points of a contour, ensuring optimum alignment of part and machining program. This reduces sources of error and gives consistently accurate parts and high process reliability.
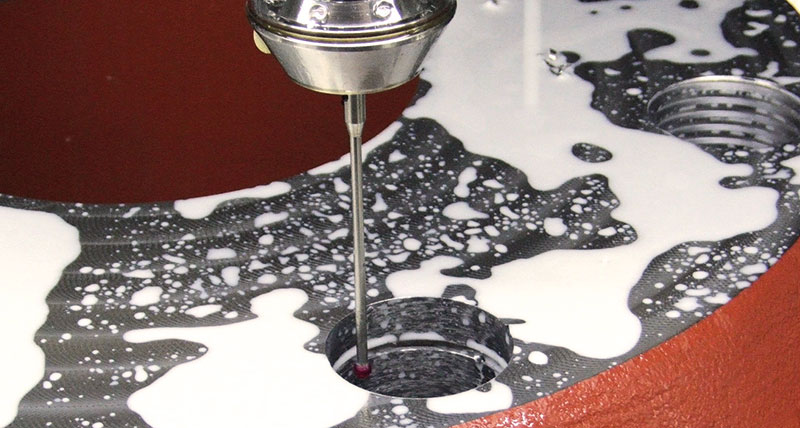
Elmar Müller emphasizes the easy use of this software and how problem-free the introduction to the facility was. “Training was made at the same time as the probe installation at our premises and was finished within two days without any problems and using our own workpieces,” he reports. “Afterwards, the assigned staff member was not only able to work with this software but could also pass on his knowledge to others. Perfect.” As a result, the working methods at Laro changed very quickly. “Today we ask ourselves how we ever managed without this software before.” In the past they had to take workpieces to the measu- ring room and wait for results, whereas the workpiece is now measured and critical points are checked while still clamped on the machine immediately after machining. The new possibilities also result in considerable enhancement of our machining strategy, normally resulting in reduced machining times. Today, pockets and critical contours like mould parting surfaces or similar, are programmed and pre-machined at Laro using 5 hundredths allowance. Subsequently, the exact geometry is measured in order to finish precisely to required dimensions. To simplify matters, this is done via the tool correction function in the control. This provides high process reliability and minimizes human error. Also, it simplifies work for the operators and offers them safety previously unknown. This is an important factor when dealing with tolerances in the range of hundredths.
No need for deep thinking, this equipment has definitely paid off.With the Best Fit module, 3D Form Inspect software gives significant advantages and considerable time savings for Laro, even in volume production. This became particularly apparent at Laro when manufacturing guide blades for turbines. Not only did the clamping become significantly less important but time-consuming manual setting of the workpieces became obsolete. The actual position of each workpiece on the machine is determined by probing its contour and the machining program is aligned to the actual position by rotating and shifting the zero points and coordinate planes. Although that takes us a few minutes, “it saves us at least one hour of set-up time per part,” Elmar Müller confirms his experience. “We simply take the critical points, such as sealing or end surfaces of the blades as aligning points and probe the exact positions. The result is that we do not have any measuring or transmission errors any more.”
“The budget needed is relatively low,” Elmar Müller sums up. “No need for deep thinking, this equipment has definitely paid off.” Assuming an average total machining time of 20 hours per workpiece, a one hour reduction means savings of around 5% per part. This results in a considerable enhancement of productivity and capacity. It is process-reliable manufacturing with consistently better quality. This is good for Laro who are certified for the manufacture of aviation parts. It is also a benefit for their staff who are enhanced in status and motivation, another invaluable advantage.