Messen spart viel zeit
Kontakt

Kein neues Paradoxon sondern Realität ist bei
Laro, einem Lohnfertiger das Messen zu einem
wichtigen Mittel zum genaueren Arbeiten und zur
Zeitersparnis geworden. Mit Messtastern und der
3D Form Inspect Software werden viele Stunden
gespart und Rüstzeiten deutlich verkürzt.
Die Firma LARO NC-Technik GmbH ist seit 2001 ein selbstständiges Unternehmen innerhalb der Langer-Group und beschäftigt sich mit dem Bau von Formen und Werkzeugen, Prototypteilen, Kleinserien und Lohnaufträgen.
Besondere Stärken hat man sich im Fräsen erarbeitet und kann Werkstücke klein bis groß bearbeiten. Groß heißt in diesem Fall bis zu 6 Metern Länge und bis zu 2,2 m in der Z-Achse. Ein entsprechend großes Spektrum unterschiedlicher Werkstücke hat der Betrieb tagtäglich zu bewältigen. Neben Aluminium und Werkzeugstahl werden auch Materialien wie Duplex-Stahl, hochlegierte Stähle, gelegentlich Titan und Kunststoffe wie Uriol, Lauramid, CFK und GFK bearbeitet. Genauso vielfältig verhält es sich mit den Stückzahlen, die von 1 Stück bis zu Serien von 5.000 Stück reichen. Entsprechend vielseitig ist auch der Maschinenpark von LARO. Von der großen Henri Linée über Handtmann, FPT Mikron HPM 1000 mit 7 Paletten, HSM 800 bis zu DMU 100T, 70 Evo und 64V reicht das Spektrum der Bearbeitungszentren, die wegen der generell hohen Genauigkeitsanforderungen in klimatisierten Hallen arbeiten.
Begonnen hat die Erfolgsgeschichte der m&h Taster und
Software bei LARO mit der Anschaffung einer Handtmann-
Maschine, die mit einem Messtaster von m&h ausgerüstet
war. Die Software 3D Form Inspect erlaubt, das Werkstück
noch in der Aufspannung zu prüfen und gegebenenfalls
notwendige Nacharbeiten sofort und ohne zusätzlich
Ungenauigkeit durch erneutes Spannen zu erledigen. “Das
spart uns viel Zeit,” sagt Geschäftsführer Elmar Müller. “Wir
brauchen keinen Messraum mehr für die Produktion und
niemand muss das Werkstück ein zweites Mal in die Hand
nehmen,” schildert er seine Vorteile. Doch schon Beim Rüsten
der Werkstücke hat Elmar Müller wesentliche Vorteile mit
den Messtastern gegenüber der vorherigen Vorgehensweise
ausgemacht. Das Werkstück wird ungefähr auf die
gewünschte Position gespannt und dann mit dem Messtaster
eingemessen. Anschließend werden die Abweichungen von
der Sollposition lediglich in der Steuerung korrigiert, ohne
langwierige, manuelle Korrektur der Aufspannung des Teiles.
Die Bearbeitungsprogramme werden mit der tatsächlichen
Lage des Werkstücke in Deckung gebracht, was die Rüstzeiten
drastisch senkt, vor allem bei Werkstücken bis 2,80 m
Länge. Besondere Vorteile bietet diese Vorgehensweise beim Einmessen von Rohgussteilen. Gussteile dieser
Größenordnung weisen meist stark unterschiedliche
Verzüge auf.
Mit der Software 3D Form Inspect von m&h können die Werkstücke anhand der kritischen Stellen Ihrer Kontur eingemessen werden, was sicherstellt, dass Teil und Bearbeitungsprogramm optimal in Deckung gebracht werden. Das schaltet Fehler aus und sorgt für gleichbleibend genaue Teile und höchste Prozesssicherheit.
Auf Basis der CAD-Daten des Werkstückes legt der
Maschinenbediener per Mausklick an einem Computer
die Punkte und Bereiche fest, die er messen will.
3D Form Inspect erstellt nicht nur automatisch das
erforderliche Maschinenprogramm, sondern ergänzt es
gleichzeitig automatisch mit einem Kalibriervorgang,
um die thermischen Veränderungen der Achsen in der
Maschine zu erfassen und automatisch zu kompensieren.
Dieses Verfahren ist für m&h patentiert. Nur so sind aber
verlässliche und wiederholgenaue Messwerte möglich, die
auch einem Vergleich mit der Messmaschine standhalten.
Diese Messwerte können unmittelbar nach dem Antasten
auf der Maschine am Bildschirm des Computers angezeigt
und als Protokoll ausgedruckt werden. Der Bediener
sieht an diesem Soll-Ist-Vergleich genau, wie die Maße
des Werkstückes in der Maschine wirklich sind und kann
gegebenenfalls sofort reagieren und korrigieren.
Elmar Müller betont, wie einfach diese Software zu bedienen ist und wie unproblematisch die Einführung in den Betrieb vonstatten ging. “Die Schulung fand mit der Installation in unserem Hause statt und ging innerhalb von 2 Tagen ohne Probleme und anhand unserer eigenen Werkstücke vonstatten,” schildert er. “Der abgestellte Mann war anschließend nicht nur in der Lage damit zu arbeiten, sondern konnte sein Wissen gleich weitergeben. Optimal.” Entsprechend schnell hat sich die Arbeitsweise im Haus Laro geändert. “Heute fragen wir uns, wie wir nur vorher klar gekommen sind.” Während man früher die Werkstücke in den Messraum geben musste und auf die Ergebnisse gewartet hat, wird nun das Werkstück unmittelbar nach der Bearbeitung noch in der Maschine gemessen und kritische Merkmale geprüft. Mit den neuen Möglichkeiten konnte man auch die Bearbeitungsstrategie wesentlich verbessern, was in der Regel kürzere Bearbeitungszeiten bedeutet. So werden bei Laro heute Taschen und kritische Konturen, wie Trennebenen oder ähnliches mit 5 Hundertstel Aufmaß programmiert und vorbearbeitet. Dann wird gemessen, wo die Geometrie genau steht, um dann genau auf Solldimension zu schlichten. Der Einfachheit halber wird dies über die Werkzeugkorrekturfunktion der Steuerung gemacht. Das gibt hohe Prozesssicherheit und minimiert die Fehlerquelle Mensch. Gleichzeitig erleichtert es den Bedienern die Arbeit und gibt Ihnen bisher ungewohnte Sicherheit. Ein wesentlicher Faktor bei Toleranzen im Hunderstelbereich.
Da muss man nicht lange überlegen. Die Sache hat sich in jedem Fall bezahlt gemacht. Mit dem Modul Best Fit verschafft die Software 3D Form Inspect dem Betrieb auch im Bereich der Serienfertigung als Zulieferer deutliche Vorteile und enorme Zeitersparnis. Besonders bei der Fertigung von Leitschaufeln für Turbinen zeigte sich das bei LARO sehr eindrucksvoll. So wurde nicht nur die Bedeutung der Spannvorrichtung wesentlich geringer, sondern es fällt sogar das langwierige manuelle Einmessen des Werkstückes weg. Es wird einfach durch Antasten der Kontur die jeweilige, tatsächliche Position jedes Werkstückes in der Maschine ermittelt und durch Drehen und Verschieben der Nullpunkte und Koordinatenkreuze in der Steuerung das Bearbeitungsprogramm in Deckung mit der tatsächlichen Lage gebracht. Das dauert zwar einige Minuten, “spart uns aber Minimum 1 Stunde Rüstzeit pro Teil,” bestätigt Elmar Müller seine Erfahrung. “Wir nehmen einfach die kritischen Stellen, wie beispielsweise die Dichtoder Abschlussflächen der Schaufeln als Ausrichtpunkte und tasten die genauen Positionen ab. So haben wir keinerlei Messfehler und keine Übertragungsfehler mehr.”
“Der Kostenrahmen ist relativ gering,” resümiert Elmar Müller seine Erfahrungen “Da muss man nicht lange überlegen. Die Sache hat sich in jedem Fall bezahlt gemacht.” Geht man beispielhaft von einer Gesamtbearbeitungszeit von etwa 20 Stunden je Werkstück aus, bedeutet die Verkürzung von ca. 1 Stunde schon eine Einsparung von ca. 5 % je Teil, was eine erhebliche Produktivitätssteigerung darstellt. Dabei wird prozesssicher und gleichbleibend bessere Qualität gefertigt. Nicht nur für ein Unternehmen wie LARO, das sogar für die Fertigung von Luftfahrtteilen gesondert zertifiziert ist, sind derart aufgewertete und motivierte Mitarbeiter ein unschätzbarer Vorteil.
Die Firma LARO NC-Technik GmbH ist seit 2001 ein selbstständiges Unternehmen innerhalb der Langer-Group und beschäftigt sich mit dem Bau von Formen und Werkzeugen, Prototypteilen, Kleinserien und Lohnaufträgen.
Besondere Stärken hat man sich im Fräsen erarbeitet und kann Werkstücke klein bis groß bearbeiten. Groß heißt in diesem Fall bis zu 6 Metern Länge und bis zu 2,2 m in der Z-Achse. Ein entsprechend großes Spektrum unterschiedlicher Werkstücke hat der Betrieb tagtäglich zu bewältigen. Neben Aluminium und Werkzeugstahl werden auch Materialien wie Duplex-Stahl, hochlegierte Stähle, gelegentlich Titan und Kunststoffe wie Uriol, Lauramid, CFK und GFK bearbeitet. Genauso vielfältig verhält es sich mit den Stückzahlen, die von 1 Stück bis zu Serien von 5.000 Stück reichen. Entsprechend vielseitig ist auch der Maschinenpark von LARO. Von der großen Henri Linée über Handtmann, FPT Mikron HPM 1000 mit 7 Paletten, HSM 800 bis zu DMU 100T, 70 Evo und 64V reicht das Spektrum der Bearbeitungszentren, die wegen der generell hohen Genauigkeitsanforderungen in klimatisierten Hallen arbeiten.
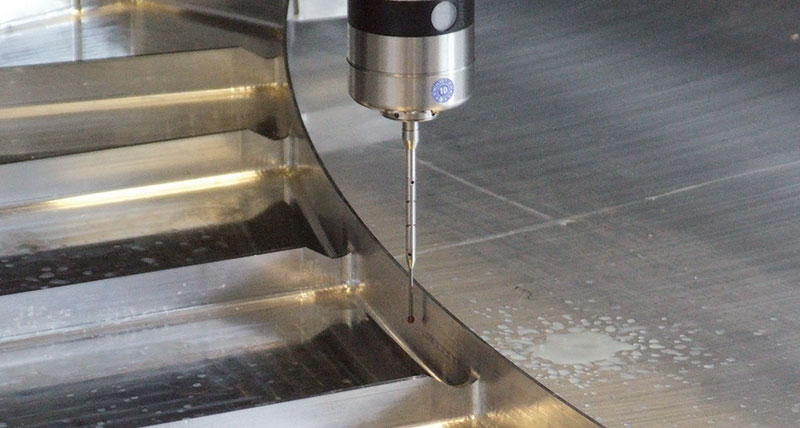
Mit der Software 3D Form Inspect von m&h können die Werkstücke anhand der kritischen Stellen Ihrer Kontur eingemessen werden, was sicherstellt, dass Teil und Bearbeitungsprogramm optimal in Deckung gebracht werden. Das schaltet Fehler aus und sorgt für gleichbleibend genaue Teile und höchste Prozesssicherheit.
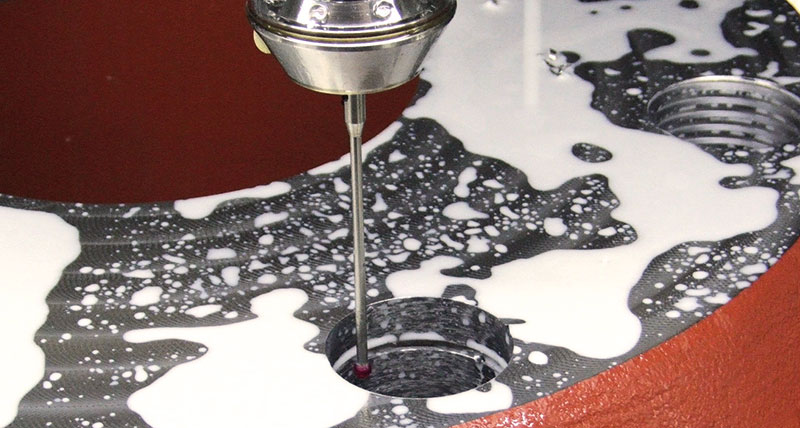
Elmar Müller betont, wie einfach diese Software zu bedienen ist und wie unproblematisch die Einführung in den Betrieb vonstatten ging. “Die Schulung fand mit der Installation in unserem Hause statt und ging innerhalb von 2 Tagen ohne Probleme und anhand unserer eigenen Werkstücke vonstatten,” schildert er. “Der abgestellte Mann war anschließend nicht nur in der Lage damit zu arbeiten, sondern konnte sein Wissen gleich weitergeben. Optimal.” Entsprechend schnell hat sich die Arbeitsweise im Haus Laro geändert. “Heute fragen wir uns, wie wir nur vorher klar gekommen sind.” Während man früher die Werkstücke in den Messraum geben musste und auf die Ergebnisse gewartet hat, wird nun das Werkstück unmittelbar nach der Bearbeitung noch in der Maschine gemessen und kritische Merkmale geprüft. Mit den neuen Möglichkeiten konnte man auch die Bearbeitungsstrategie wesentlich verbessern, was in der Regel kürzere Bearbeitungszeiten bedeutet. So werden bei Laro heute Taschen und kritische Konturen, wie Trennebenen oder ähnliches mit 5 Hundertstel Aufmaß programmiert und vorbearbeitet. Dann wird gemessen, wo die Geometrie genau steht, um dann genau auf Solldimension zu schlichten. Der Einfachheit halber wird dies über die Werkzeugkorrekturfunktion der Steuerung gemacht. Das gibt hohe Prozesssicherheit und minimiert die Fehlerquelle Mensch. Gleichzeitig erleichtert es den Bedienern die Arbeit und gibt Ihnen bisher ungewohnte Sicherheit. Ein wesentlicher Faktor bei Toleranzen im Hunderstelbereich.
Da muss man nicht lange überlegen. Die Sache hat sich in jedem Fall bezahlt gemacht. Mit dem Modul Best Fit verschafft die Software 3D Form Inspect dem Betrieb auch im Bereich der Serienfertigung als Zulieferer deutliche Vorteile und enorme Zeitersparnis. Besonders bei der Fertigung von Leitschaufeln für Turbinen zeigte sich das bei LARO sehr eindrucksvoll. So wurde nicht nur die Bedeutung der Spannvorrichtung wesentlich geringer, sondern es fällt sogar das langwierige manuelle Einmessen des Werkstückes weg. Es wird einfach durch Antasten der Kontur die jeweilige, tatsächliche Position jedes Werkstückes in der Maschine ermittelt und durch Drehen und Verschieben der Nullpunkte und Koordinatenkreuze in der Steuerung das Bearbeitungsprogramm in Deckung mit der tatsächlichen Lage gebracht. Das dauert zwar einige Minuten, “spart uns aber Minimum 1 Stunde Rüstzeit pro Teil,” bestätigt Elmar Müller seine Erfahrung. “Wir nehmen einfach die kritischen Stellen, wie beispielsweise die Dichtoder Abschlussflächen der Schaufeln als Ausrichtpunkte und tasten die genauen Positionen ab. So haben wir keinerlei Messfehler und keine Übertragungsfehler mehr.”
“Der Kostenrahmen ist relativ gering,” resümiert Elmar Müller seine Erfahrungen “Da muss man nicht lange überlegen. Die Sache hat sich in jedem Fall bezahlt gemacht.” Geht man beispielhaft von einer Gesamtbearbeitungszeit von etwa 20 Stunden je Werkstück aus, bedeutet die Verkürzung von ca. 1 Stunde schon eine Einsparung von ca. 5 % je Teil, was eine erhebliche Produktivitätssteigerung darstellt. Dabei wird prozesssicher und gleichbleibend bessere Qualität gefertigt. Nicht nur für ein Unternehmen wie LARO, das sogar für die Fertigung von Luftfahrtteilen gesondert zertifiziert ist, sind derart aufgewertete und motivierte Mitarbeiter ein unschätzbarer Vorteil.