La misurazione fa risparmiare molto tempo
Contattateci

La misurazione è una risorsa importante per
ottenere un lavoro più preciso e risparmiare
tempo – non un lusso ma una necessità presso
Laro, costruttore su commessa. Con i tastatori
m&h ed il software 3D Form Inspect si risparmiano
molte ore ed i tempi di azzeramento si
riducono notevolmente.
Dal 2001, LARO NC-Technik GmbH è un’azienda
giuridicamente indipendente all’interno del Gruppo
Langer e fabbrica stampi plastica e stampi di im-butitura,
prototipi, piccoli lotti e soprattutto lavora su commessa.
Risorse sono state sviluppate nel settore della fresa- tura,
dove vengono lavorati pezzi di grandi e piccole dimensioni.
Presso Laro, grande significa lunghezze che arrivano a
6 metri e 2,2 m sull’asse Z. Affrontare una vasta gamma di
pezzi differenti è l’attività quotidiana dell’azienda. Accanto
ad alluminio e acciaio, Laro fresa anche materiali come
acciai prodotti con il processo duplex e acciai ad alto tenore
di legante, più occasionalmente titanio e resine come ureol,
lauramit, CRP e GRP. I materiali sono tanto vari quanto le
dimensioni dei lotti, spaziando dal singolo pezzo a volumi
di 5.000 pezzi. Il parco macchine di Laro è egualmente
versatile. La gamma di centri di lavoro spazia dai grandi
Henri Linée a Handtmann, FPT, Mikron HPM 1000 con
7 pallet, HSM 800, DMU 100T, 70 Evo, e 64 V. Per la grande
precisione richiesta, questi centri di lavoro sono installati
in un’ officina provvista di aria condizionata.
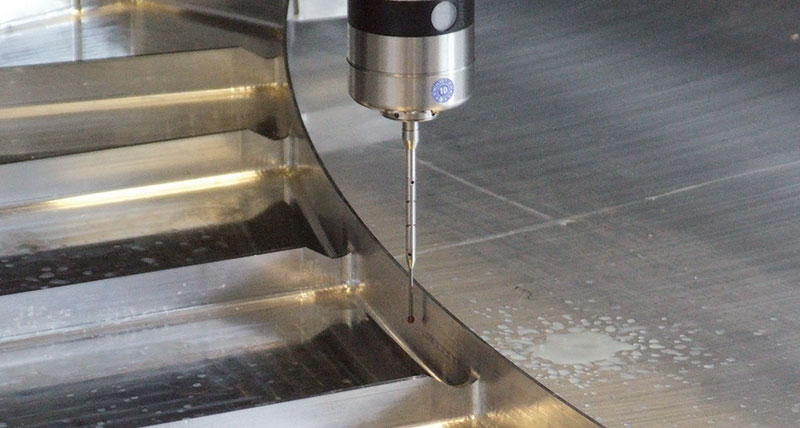
La storia dei
tastatori e del software m&h presso Laro è iniziata con
l’acquisto di una macchina equipaggiata con un tastatore
m&h e software di misura. Il software 3D Form Inspect
di m&h consente di verificare il pezzo quando è ancora
staffato e ogni rilavorazione necessaria può essere fatta
immediatamente e senza quelle imprecisioni causate dal
ri-staffaggio del pezzo. “Questo ci fa risparmiare molto
tempo,” riferisce l’amministratore delegato Elmar Müller.
“Non c’è bisogno di avere una sala metrologica per la
produzione e nessuno deve movimentare un pezzo due
volte,” spiega. Nell’esecuzione dell’azzeramento pezzo, Elmar Müller
ha potuto vedere gli indiscutibili vantaggi ottenuti con
i tastatori rispetto all’approccio precedente. Il pezzo è
staffato in posizione e poi allineato dal tastatore. Questo
significa che gli scostamenti dalla posizione richiesta
sono corrette automaticamente nel controllo senza la
correzione manuale dello staffaggio, che richiede tempo.
I programmi di lavorazione sono allineati con la posizione reale del pezzo, riducendo drasticamente i tempi di
azzeramento, in particolare per i pezzi con una lunghezza
fino a 2,80 m. Questa procedura offre particolari vantaggi in
fase di azzeramento di fusioni grezze. Le fusioni di queste
dimensioni mostrano diverse deformazioni di forma.
Con il
3D Form Inspect, i pezzi possono essere centrati rispetto ai
punti critici di una superficie, assicurando l’allinea- mento
ottimale del pezzo e del programma di lavorazione. Questo
riduce le fonti di errore e assicura di conseguenza pezzi
precisi e grande affidabilità di processo.
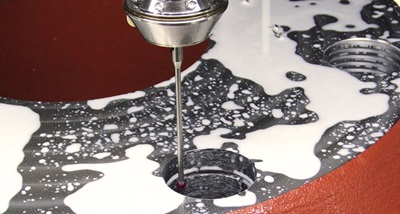
L’operatore macchina determina i punti e le aree che
devono essere misurati su un computer cliccando con il
mouse in base ai dati CAD del pezzo. Il 3D Form Inspect
genera automaticamente il programma di misura richiesto
e crea anche un programma di calibrazione per tenere
conto dei cambiamenti termici degli assi della macchina
e compensarli. Questa procedura è brevettata da m&h.
Questo è l’unico modo per ottenere valori misurati
affidabili e ripetibili che possono essere paragonati a
quelli di una macchina di misura. I valori misurati possono
essere visualizzati immediatamente sullo schermo del
computer dopo la rilevazione e possono essere stampati
come protocollo. Sulla base di questa analisi, l’operatore
determina le dimensioni reali del pezzo in macchina e,
se necessario, può intervenire e fare subito le correzioni.
Elmar Müller enfatizza il facile utilizzo di questo software e
come sia stato esente da problemi l’inserimento in azienda.
“L’addestramento è stato fatto contemporaneamente
all’installazione del tastatore presso i nostri stabilimenti
ed è terminato in due giorni senza problemi ed utilizzando i
nostri pezzi,” riferisce. “In seguito, la persona incaricata non
solo è stata in grado di lavorare con questo software ma è
stata anche in grado di trasmet- tere le sue conoscenze ad altri. Perfetto.” Di conseguenza, in Laro i metodi di lavoro sono cambiati
molto rapidamente. “Oggi ci chiediamo come abbiamo
potuto fare a meno di questo software in precedenza.” In
passato si dovevano portare i pezzi nella sala metrologica
e aspettare i risultati mentre ora il pezzo è misurato ed i
punti critici sono controllati mentre è ancora staffato in
macchina subito dopo la lavorazione. Le nuove possibilità
danno anche come risultato un notevole miglioramento della
nostra strategia di lavora-zione, dando luogo generalmente
a tempi di lavorazione ridotti. Oggi in Laro, tasche e
superfici critiche, quali piani di chiusura o simili, sono
programmate e pre-lavorate utilizzando una tolleranza di
5 centesimi. Successivamente si misura l’esatta geometria
per rifinire con precisione le dimensioni richieste. Per
semplicità, questo viene fatto attraverso la funzione di
correttore utensile nel controllo. Questo fornisce una
grande affida bilità di processo e minimizza l’errore umano.
Inoltre semplifica il lavoro agli operatori e garantisce loro
una sicu-rezza prima sconosciuta. Questo è un fattore
importante quando si ha a che fare con tolleranze dell’ordine
di centesimi.
Il budget
necessario è
relativamente
basso
Con il modulo Best Fit, il software 3D Form
Inspect garantisce vantaggi significativi e fa risparmiare
molto tempo a Laro, anche nella produzione in serie. Questo
è stato molto evidente in Laro nel caso della produzione di
palette del distributore per turbine. Non solo lo staffaggio
è diventato molto meno importante ma l’azzeramento ed
il centraggio dei pezzi, dispendioso in termini di tempo, è
risultato obsoleto. La posizione reale di ogni pezzo sulla
macchina è determinata rilevando la sua superficie e
il programma di lavorazione è allineato alla posizione
reale ruotando e spostando i punti di zero e i piani delle
coordinate. Anche se questo ci richiede pochi minuti, “ci fa risparmiare almeno un’ ora di tempo per l’azzeramento
per pezzo,” Elmar Müller conferma così la sua esperienza.
“Semplicemente prendiamo i punti critici, come ad esempio
le superfici di tenuta o finali delle pale come punti di
allineamento e rileviamo le esatte posizioni. Il risultato
è che non commettiamo più errori di misurazione o di
trasmissione.” “Il budget necessario è relativamente basso ”
riassume Elmar Müller. “Non c’è bisogno di pensarci troppo,
questa attrezzatura si ripaga sicuramente.”
Presupponendo un tempo di lavorazione medio totale
di 20 ore per pezzo, una riduzione di un’ora significa
risparmiare circa il 5% per parte. Questo dà origine ad
un notevole miglioramento di produttività e capacità. Si
tratta di una produzione dal processo affidabile con una
qualità notevolmente migliore. Questo è perfetto per Laro,
certificate per la produzione di parti aeronautiche.
E’ anche un vantaggio per i loro dipendenti, che vengono
incentivati e motivati, altro incalcolabile vantaggio.