Glen Dimplex Thermal Solutions (GDTS)
Glen Dimplex Thermal Solutions achieves greater efficiency and accuracy with RADAN automatic nesting, labeling, and MRP Essentials
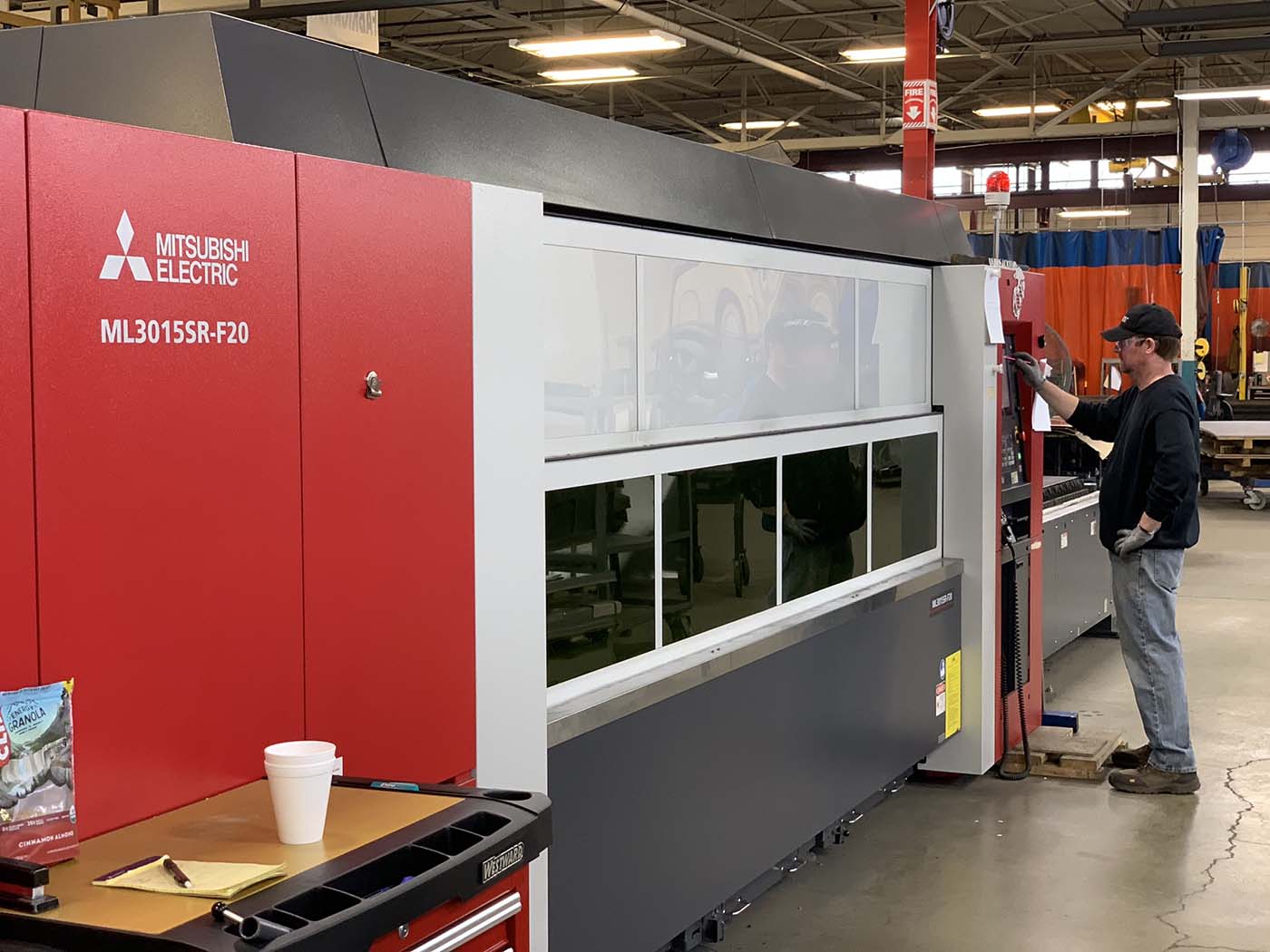
"There’s a really delicate balance and a really tight link between the laser and the software. So much of the potential of the expensive piece of machinery is dependent upon on how well you use the software."
Cooling systems specialist Glen Dimplex Thermal Solutions (GDTS) maintains its reputation for quality by consistently upgrading production technologies while remaining dedicated to customer service.
“The company is proud of its name, and we’ve been around long enough that we have brand recognition and brand loyalty,” says Manufacturing Engineer Zachary Reinke. “Beyond that, we really strive for quality and are proud of the stability of the product.”

GDTS opened its doors more than 60 years ago with its Koolant Koolers brand chiller and has consistently expanded its capabilities to serve a widening array of industries around the world. Today, the company, which employs about 200 staff, produces custom chillers for the aerospace, automotive, food and beverage processing and packaging, medical imaging, and machine tooling industries — and even counts a microbrewery or two among its clients.
The company, which offers extensive design services, produces its own line of products and utilizes the talents of an in-house research and development team to assist clients and break new ground. “We’re proud to be able to put products out there in more complex and more demanding markets. We are in a state of constant upgrade, including new technologies that keep us competitive.”
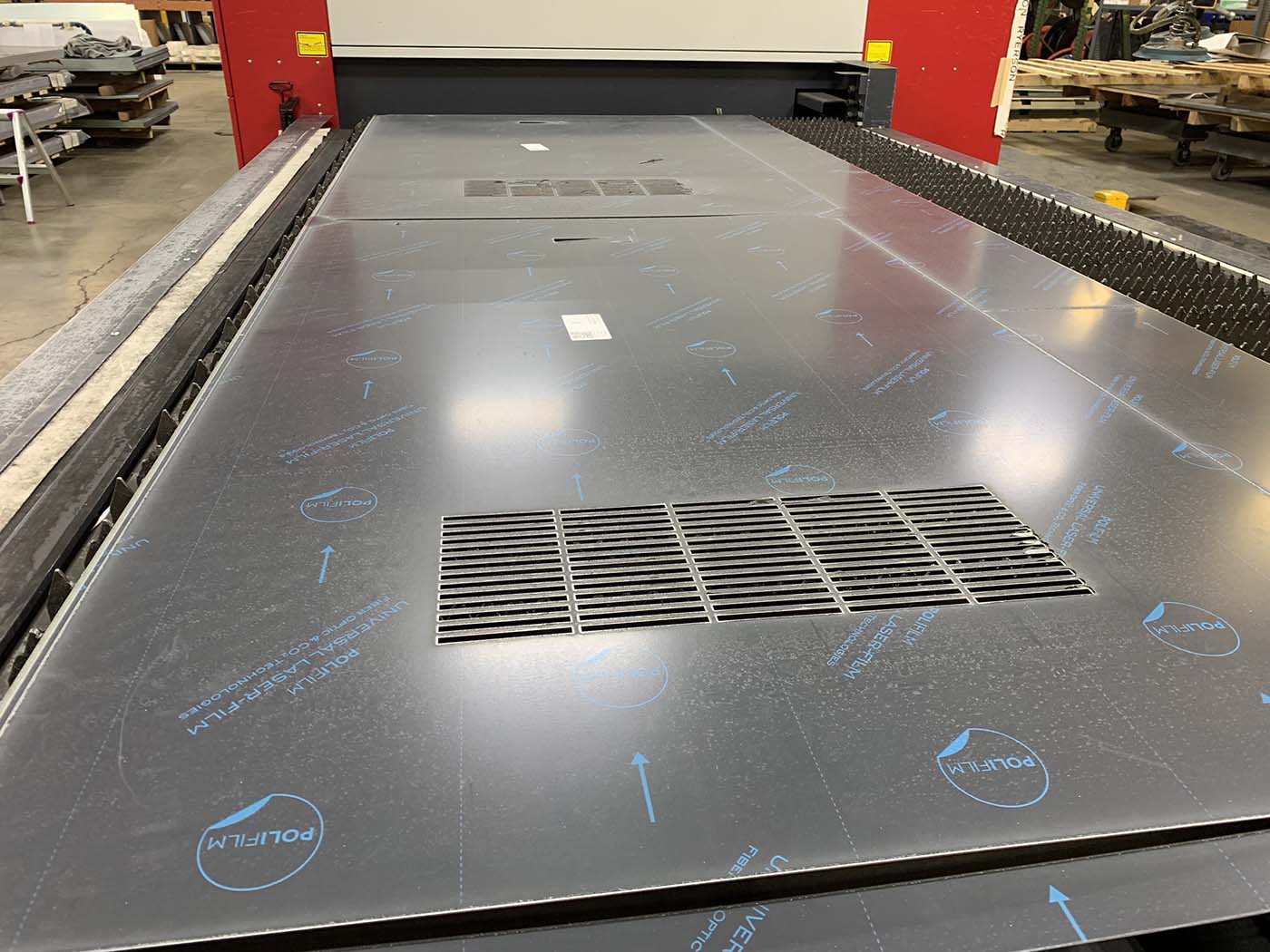
Among those technologies is the RADAN solution for sheet metal, a computer-aided-manufacturing (CAM) system that was implemented at GDTS in 2017 specifically to program the company’s new fiber laser. Reinke was hired following the implementation of the fiber laser and software, and was tasked with optimizing production.

“They purchased a fiber laser to update fabrication capabilities, and part of my job has been to get the laser and software up to production quality,” Reinke says. “There’s a really delicate balance and a really tight link between the laser and the software. So much of the potential of the expensive piece of machinery is dependent upon on how well you use the software.”
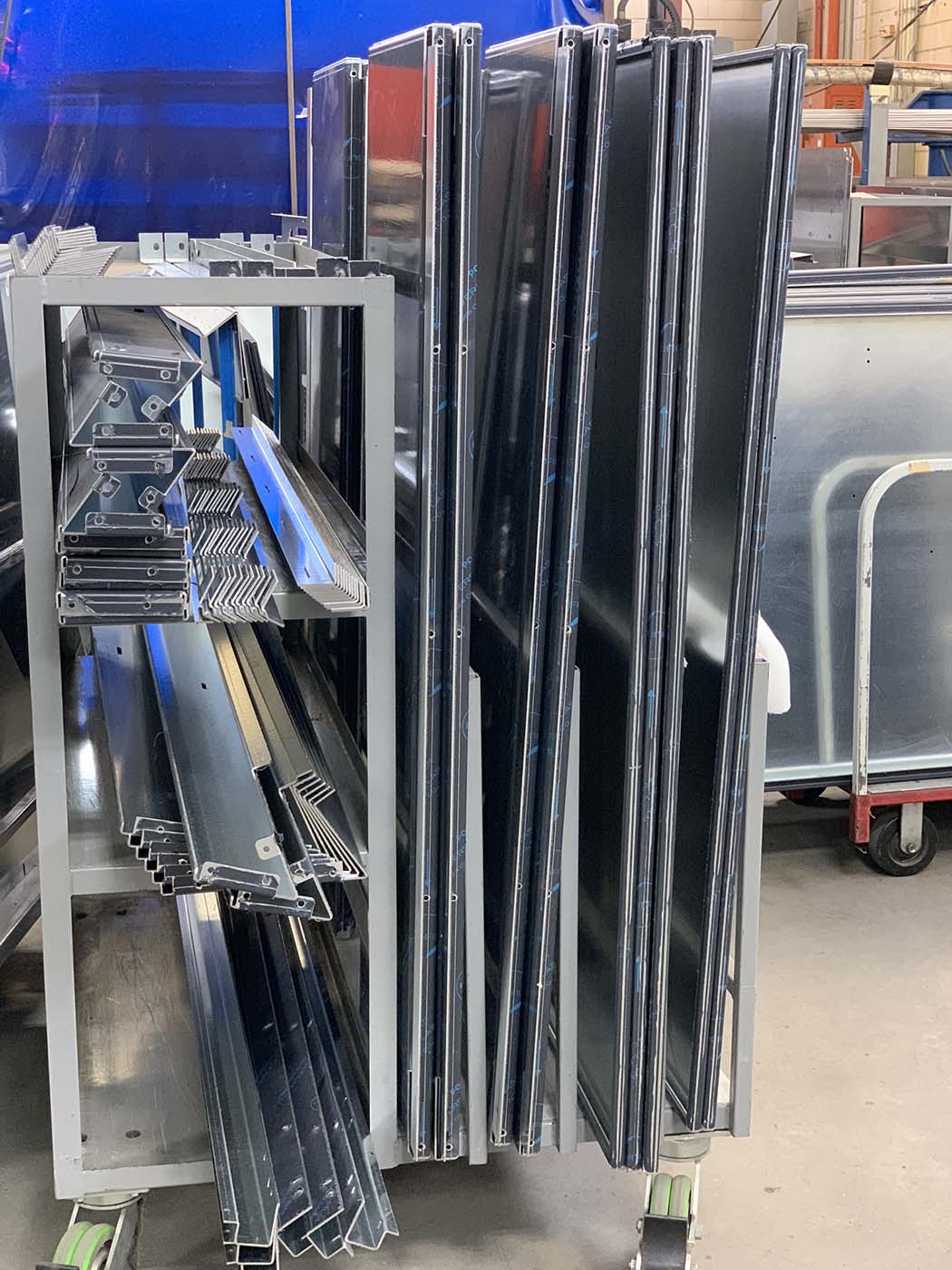
GDTS takes advantage of RADAN’s powerful automatic nesting capabilities, which it uses to automatically generate efficient nests that can be manually edited if desired.
“There is a lot of flexibility for fine tuning things when it comes to nesting,” Reinke says “Almost all of what we do is customized in a lot of small ways, so the benefit for us is in the automatic nesting.”
To optimize production, automatic nesting at GDTS works in conjunction with RADAN MRP Essentials, an MRP integration utility that enables nested projects to be automatically generated from a production-schedule file.
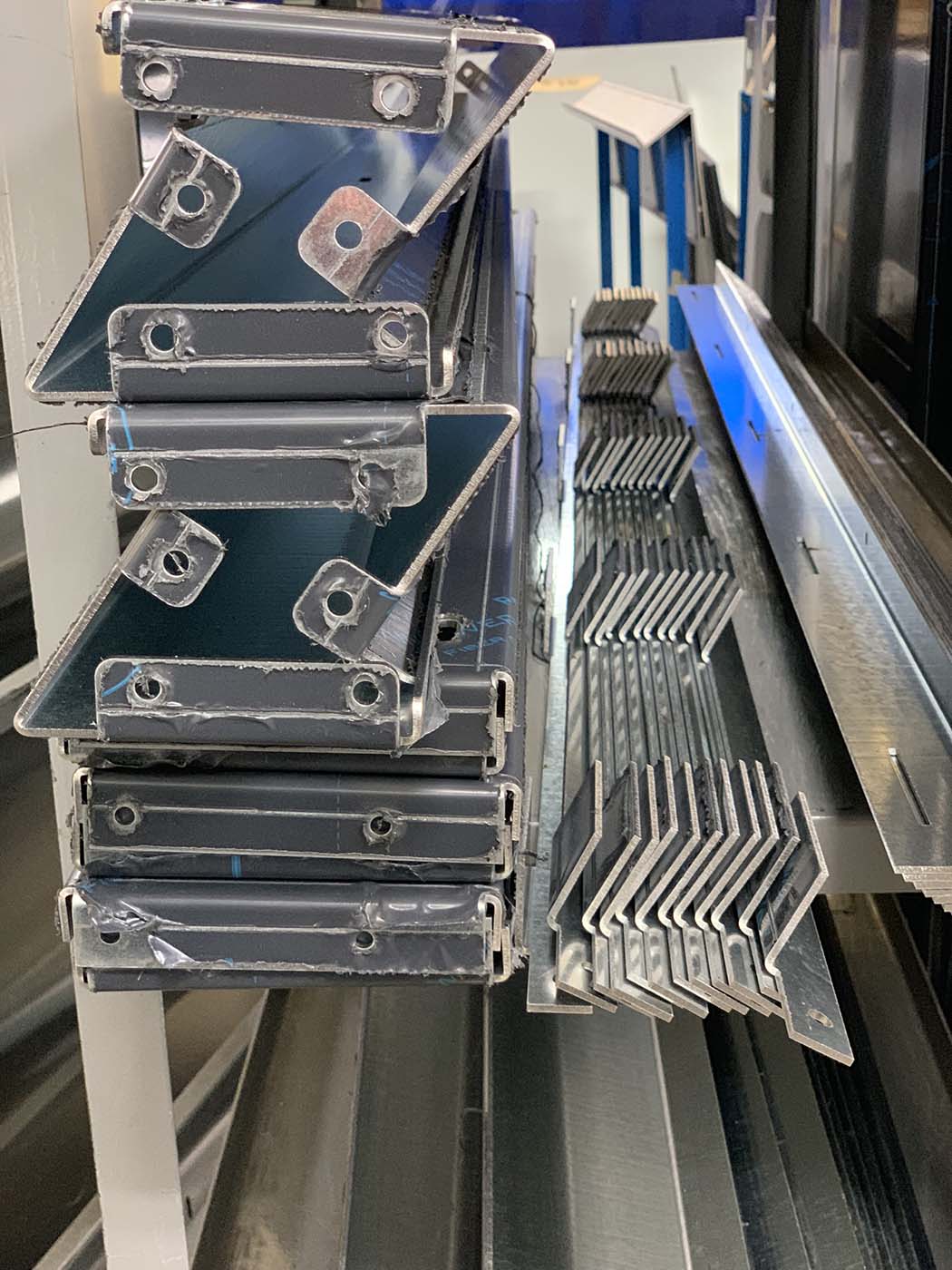
GDTS utilizes an ERP system for production control that tracks parts and generates bills of materials. That system produces text files that MRP Essentials uses to initiate the creation of data files, and RADAN uses that data to load parts and part quantities, as well as to generate batches of nests for each project.
“When a unit has been sold, we’ll see that and automatically generate a list of parts in our ERP system, and a data file that we can use with RADAN will also be generated,” Reinke says. “This helps to eliminate the need to manually input information, which saves time and reduces error.
We just push a few buttons and RADAN does all the heavy lifting. There may be 18 nests for one project and, in a matter of 10 minutes, we can have 18 programs ready to send to the machine to cut out on a laser.”
Included in Reinke’s overarching mission for greater optimization at GDTS is the reduction or elimination of manual input wherever possible. As such, he is currently in the process of creating an automated system to replace the manual labeling of parts that have been cut on the laser. “We may have 10 nests for a single project, and they’re using a marker to write a part number when it comes off the laser,” Reinke explains. “The manual writing isn’t efficient and can be prone to error.”
The GDTS team is using RADAN’s ability to generate project reports to create stickers that will eventually replace the need for manual labeling.
“When RADAN nests everything, I can go in on the project level and create a sticker layout that can be used to label each part. These can have an image of the part, the part number, a QR code, a serial number — whatever other information that you want — to create sticker for each part for the project. Some of that capability reflects what we’ve done as a company to customize RADAN, but the software is very flexible in allowing us to tailor it to suit our needs.”
The ability to accurately label parts as they come off the laser is vital, as GDTS nests several projects, with numerous different serial numbers, together across multiple sheets. “Trying to cut out several different models at once is the challenge, but we can nest several of our machines at once. Because of the stickers, we can tag each part and there is a ton of information that is automatically generated. It’s definitely going to be faster to apply a sticker, and it will have a lot more information on it that what we have now.”
In addition to reducing error, the new labeling process will make it easier for the company to increase the size of its nested batches. “This all adds up to better sheet utilization and laser-time utilization,” explains Reinke, who estimates that material savings, once the labeling process is at full force, will be five to 10 sheets per week.
Reinke is pleased with the progress GDTS has made in optimizing the fiber laser, and is confident that ongoing gains will be made.
“When you invest significantly in machinery, there is a lot riding on that piece of equipment in terms of seeing a return on your investment,” he says. “If you use it correctly, and have the software that you need to make sure you’re getting the most out of it that you can, the benefits of having that machinery are very clear.”
Reinke adds that RADAN technical support was consistent and responsive throughout the implementation process, and continues to be supportive as GDTS improves capabilities and tailors processes. “I’ve just called out of the blue and they always make time to talk to me,” he says. “Everyone on the team has been really helpful, and that can make a big difference.”

About the company
Name: Glen Dimplex Thermal Solutions (GDTS)
Business: Custom chiller manufacturer
Web: www.dimplexthermal.com
Benefits Achieved
- Greater production speed and control with the ability to quickly and efficiently generate and customize nests
- Use of an MRP integration utility enables nested projects to be automatically generated from a production-schedule file
- Reduction or elimination of manual input, which reduces error