More efficient and timesaving, with a higher guarantee of success
Modern structured light scanning for new standards in quality management for lifestyle goods.
Contact us
Flexible 3D scanning at the highest precision
For more than 270 years, the name Villeroy & Boch has stood for high-quality ceramic products in the bathroom and wellness as well as dining and lifestyle segments. Founded in 1748, the company is headquartered in an old abbey in Mettlach, Germany, and has 13 production sites in Europe and Asia. Around 7100 employees are responsible for the production, marketing and sales of high-quality ceramic goods ranging from classic tableware and products for the sanitary area to fittings, furniture and decorative items.
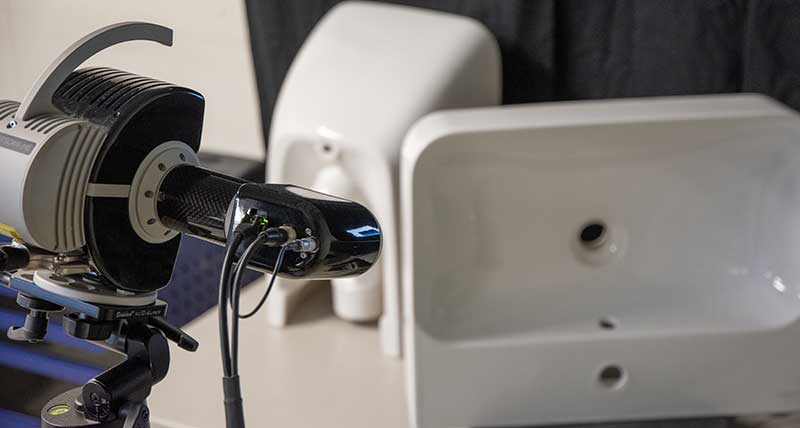
As one component of the internal "Digital Validation" project, Villeroy & Boch acquired the Hexagon structured light scanner system SmartScan at the end of 2018. "Most 3D scanners require targets to refer the single scans to each other. Attaching and then removing the targets is very time-consuming. With the SmartScan, this is not necessary," says Miguel Ramalhosa from Total Quality Management at Villeroy & Boch in Mettlach. "In addition, the turntable for automated scanning of the components is very useful. Other decisive points were the mobility and the speed of the SmartScan."
Digital validation
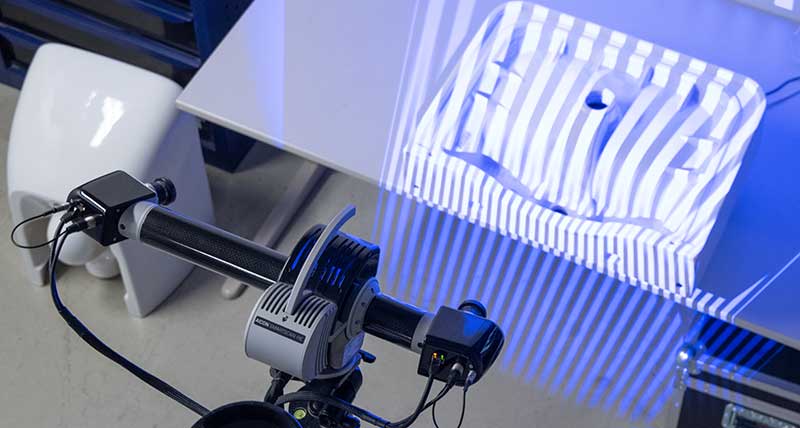
In order to check the approximately 50 dimensions that each checklist contains, series of measurements are repeatedly carried out with the new products during the validation process. For this purpose, the components to be inspected are placed on a turntable and scanned automatically with the SmartScan. An STL model created from the scans is then used to compare against the preset checklist dimensions in the PolyWorks inspection software. If all dimensions are within the tolerance and the product meets all target specifications, the production of this model is validated.
In the digital world, it is very clearly defined where the measurement has to be taken. I see that as a big advantage.Before the SmartScan was purchased, this task was still performed completely by hand with a ruler, compass, inside caliper and angle. The dimensions measured in this way were then noted by hand in a printed checklist. But using these methods, especially with complicated or very gently shaped components, exact measurement was just not possible.
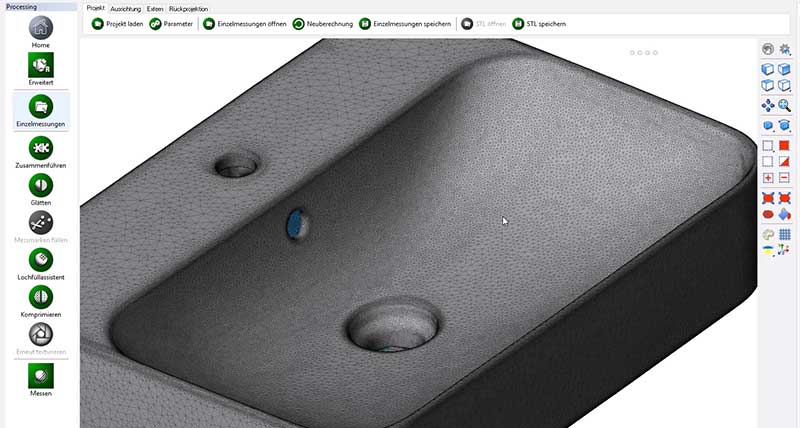
Ramalhosa also sees great potential for the use of structured light scanning in the elimination of problems that arise. "Especially with models where it is important, for example, that the frame is exactly straight, the information that I have a deformation of one millimetre is still of no use to me. I need to know where the deformation is. With the scan data provided by the SmartScan, I can see in colour in which area the dent or ding is and rework accordingly. This allows me to tackle the problem more efficiently and in less time, with an even greater guarantee of success."
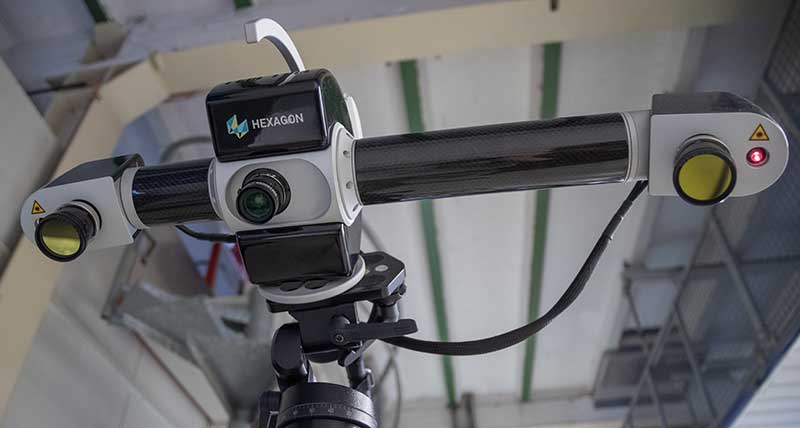
Efficiently into the future
Since its acquisition, the SmartScan has been fully integrated into the validation process, with any technical questions answered quickly by Hexagon support. "In the beginning, it was a learning process to determine how to get the most appropriate measurements. But over time we have solved all the problem cases we had. We are very satisfied with it," says Ramalhosa.
"It would be really efficient if we also used the scanner in continuous monitoring," says Ramalhosa, as he is already thinking about further areas of application for the scanning technology in the future. In the quality control of serial production, only an abstracted checklist with the most necessary dimensions can be checked so far. A complete check would be too costly and time-consuming with today's measuring equipment. With the use of the SmartScan at this point, the complete checklist could also be applied here and statistical monitoring could be carried out.