The Rohde Schwarz factory at Teisnach opts for one software for all 3D measuring devices
Rohde & Schwarz - Germany
Contact us
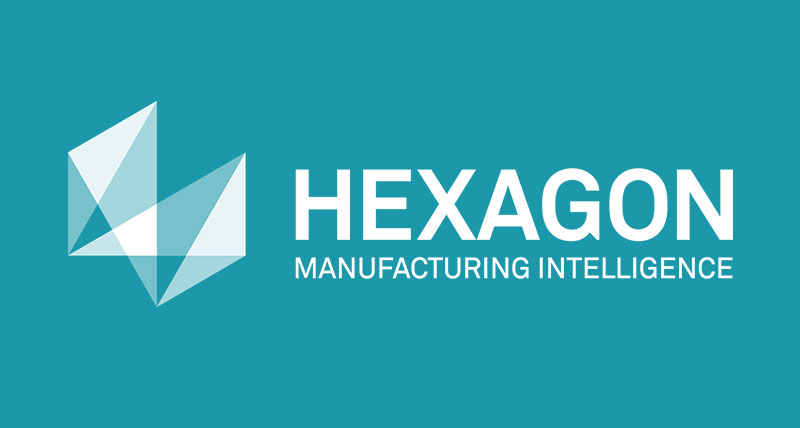
At their factory in Teisnach, Rohde & Schwarz carry out cutting and non-cutting processes, surface treatment, printed circuit production, tool making and other processes. The company is able to meet customers’ requirements quickly and flexibly on the basis of this extensive production depth. Hexagon Metrology’s 3D coordinate metrology is essential for the release of initial samples, for optimising processes in ongoing quality assurance during production and for the final approval of products.
These instruments can be found in the measuring rooms at Rohde & Schwarz: Optiv Performance, an optical system for printed circuit board production, Optiv Reference, a multi-sensory device used in precision manufacture, and tactile coordinate measuring instruments such as DEA GLOBAL or Leitz PMM-C. The Teisnach factory even boasts a portable ROMER measuring arm to ensure that products reach as close to perfection as possible.
All these devices are handled by the PC-DMIS software, which is used to compare the effective measured data from all Hexagon Metrology measuring devices with the CAD model. Not only does this save training expenses, but it also stops these machines from becoming bottlenecks: when work piles up, users can simply switch to another measuring device. “We were very clear on our objective. We wanted to deal with just one software environment. At that point in time, only Hexagon Metrology was in the position to meet this requirement”, confirms Gerhard Kokott, Head of Decentralised Quality Management.
With the help of the additional offline function, the metrology engineers can start producing their programs as soon as the production of the first development parts commences. Since then, it has been possible to reduce the throughput time of parts by up to 30 percent. “We can now use CAD data right from the beginning and work with measuring programs throughout the entire CAD/ CAM chain”, says Karl-Heinz Stieglbauer of Decentralised Quality Control.
In order to cope with all their measuring requirements, the company makes good use of PC-DMIS with its user-friendly operating features. The metrology engineers are professionals in this specialist field and work out their measuring programs and clamping plans. The measuring itself is then mostly carried out by the shopfloor workers. In future it is intended to introduce a simplified user interface which should make the process even more intuitive for the workers on the shop-floor.
It is not by chance that Rohde & Schwarz have such a variety of measuring devices at their factory in Teisnach. Kokott: “Our flexibility in production also requires us to be flexible in our quality assurance processes. The only way we can measure the high-frequency structure of our circuit boards is with optical devices. On the other hand, we produce parts in precision manufacturing which need to be measured with tactile and non-contact methods. ”This can be achieved with a high degree of accuracy with multi-sensor systems in one clamping process. The tolerances are not more than a few microns.
Stationary coordinate measuring machines with tactile measuring heads can be used for larger steel sheet and milled structures which are used as frames for various radio and transmitter systems. And talking about size: at its factory in Teisnach, Rohde & Schwarz uses a portable ROMER measuring arm to check aerial radomes with dimensions of up to two meters. In this instance, the accuracy lies within the functional range.
Finally, all these devices for optical, tactile, multi-sensory, stationary and portable measuring are all brought together by the PC-DMIS measuring software. And that will not change in the future as Rohde & Schwarz plans to integrate new systems into the PC-DMIS landscape in Teisnach.
These instruments can be found in the measuring rooms at Rohde & Schwarz: Optiv Performance, an optical system for printed circuit board production, Optiv Reference, a multi-sensory device used in precision manufacture, and tactile coordinate measuring instruments such as DEA GLOBAL or Leitz PMM-C. The Teisnach factory even boasts a portable ROMER measuring arm to ensure that products reach as close to perfection as possible.
PC-DMIS: common denominator
All these devices are handled by the PC-DMIS software, which is used to compare the effective measured data from all Hexagon Metrology measuring devices with the CAD model. Not only does this save training expenses, but it also stops these machines from becoming bottlenecks: when work piles up, users can simply switch to another measuring device. “We were very clear on our objective. We wanted to deal with just one software environment. At that point in time, only Hexagon Metrology was in the position to meet this requirement”, confirms Gerhard Kokott, Head of Decentralised Quality Management. With the help of the additional offline function, the metrology engineers can start producing their programs as soon as the production of the first development parts commences. Since then, it has been possible to reduce the throughput time of parts by up to 30 percent. “We can now use CAD data right from the beginning and work with measuring programs throughout the entire CAD/ CAM chain”, says Karl-Heinz Stieglbauer of Decentralised Quality Control.
In order to cope with all their measuring requirements, the company makes good use of PC-DMIS with its user-friendly operating features. The metrology engineers are professionals in this specialist field and work out their measuring programs and clamping plans. The measuring itself is then mostly carried out by the shopfloor workers. In future it is intended to introduce a simplified user interface which should make the process even more intuitive for the workers on the shop-floor.
The whole range of measuring devices
It is not by chance that Rohde & Schwarz have such a variety of measuring devices at their factory in Teisnach. Kokott: “Our flexibility in production also requires us to be flexible in our quality assurance processes. The only way we can measure the high-frequency structure of our circuit boards is with optical devices. On the other hand, we produce parts in precision manufacturing which need to be measured with tactile and non-contact methods. ”This can be achieved with a high degree of accuracy with multi-sensor systems in one clamping process. The tolerances are not more than a few microns.Stationary coordinate measuring machines with tactile measuring heads can be used for larger steel sheet and milled structures which are used as frames for various radio and transmitter systems. And talking about size: at its factory in Teisnach, Rohde & Schwarz uses a portable ROMER measuring arm to check aerial radomes with dimensions of up to two meters. In this instance, the accuracy lies within the functional range.
Finally, all these devices for optical, tactile, multi-sensory, stationary and portable measuring are all brought together by the PC-DMIS measuring software. And that will not change in the future as Rohde & Schwarz plans to integrate new systems into the PC-DMIS landscape in Teisnach.