Process reliability in short cycle time
Contact us

Being a typical supplier for the automotive, office machine and electrical engineering sectors, Berger in Memmingen manufactures a variety of different parts and ready-to-install components. With a workforce of around 1,600 employees, Berger is a worldwide business. About 600 staff produce precision parts in medium and large volumes on the boundaries of the Allgäu, using state-of-the-art machinery.
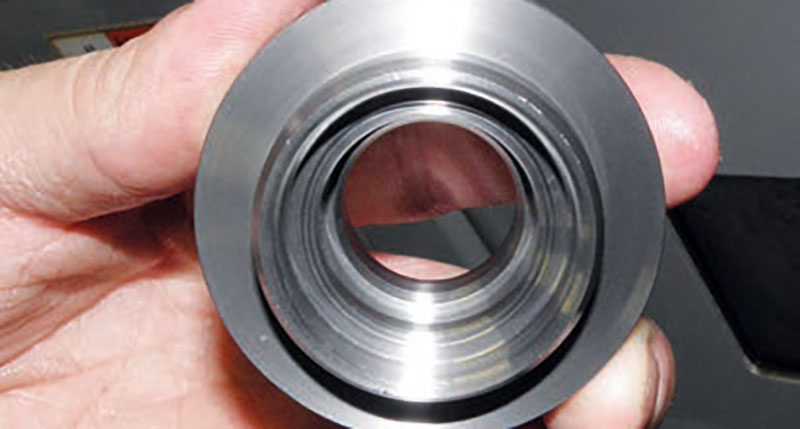
Trouble-free metal cutting with a consistent fitting accuracy is required within a close tolerance range of 25μm for a part length of around 10mm and 23μm for a diameter of 40mm. Occasionally, manufacturing errors occurred with the cause being diagnosed as false positioning when the workpiece was being automatically loaded into the chuck. Chips were sometimes getting between the chuck and the part which meant components were sitting incorrectly in the chuck with resultant manufacturing errors.
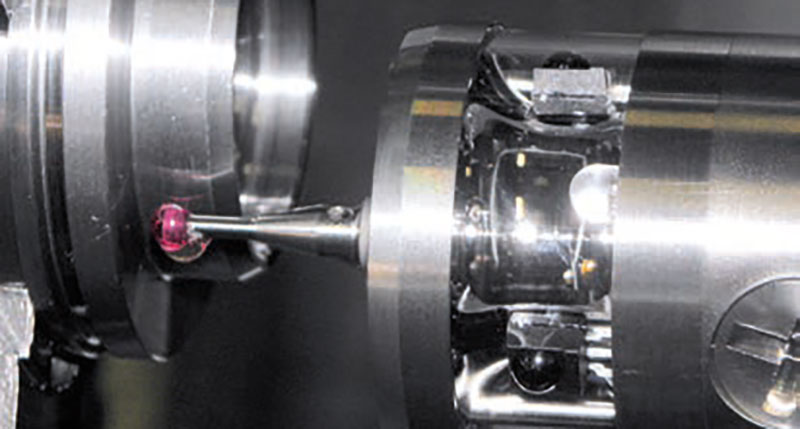
The adverse conditions do not affect the m&h IRP40.01 touch probe which has been specially designed for use on machine tools. With its body made of stainless steel, diode cover made of hardened natural glass and sealing in accordance to IP68 standard as well as the renowned m&h sturdy measuring design, it is perfectly suited for this environment, promising a long service life. Data transmission via the secure, high-performance HDR infrared technology not only ensures process-reliable signals but is also unaffected by environmental conditions in the lathe such as sticking chips, coolant film, oil mist and external light. These are absolute prerequisites for use in the turret of a lathe. Its slim diameter of only 40mm and length of 50mm avoid collision areas and allow installation in the small working areas of automatic lathes.
The touch probe is used every 45 seconds and measures six points on the workpiece.Equipped with a short stylus, this probe has been in use for some time in volume production at Berger. The probe is used every 45 seconds and switched on by encoded infrared signal. It touches in six positions on the flange and outer diameter and transmits these trigger positions to the control. To save energy, it is immediately switched off after measuring. Only if all 6 values are within the permissible range does the machining cycle continue. The inspection procedure takes just 5 seconds of the machining cycle Initially the machine was programmed so that the cutting process was stopped if measured values were found to be outside the predefined tolerance. However, this meant unscheduled machine downtime that limited achievable machine capacity. Each time an operator had to remove the part and start the procedure again. In order to save valuable production time, false measurement now results in automatic removal and ejection of the part. A new part is then automatically loaded and the cycle starts without requiring any outside intervention. This saves time and enhances the self-reliance of the automated machine. Both capacity and productivity of the machine, usually running on 3 shifts, is considerably enhanced.
Since errors in the machine can sometimes happen and because chips are the biggest problem in lathes, Berger bought a spare probe but there has been no need to use it so far. The touch probe always stays installed in the lathe turret without requiring special maintenance. Possible chip deposits on the touch probe do not impede its function. Chips and other things sticking onto the stylus ball are removed by the strong coolant spray and have not affected the measuring process so far.
Retrofitting of infrared receiver and touch probe at Berger was done by m&h service staff and an m&h Fanuc specialist. He was in charge of the initial programming on site plus any control changes made to the Takamaz. Proveout on the machine was done by m&h and since then the machine has been running without problems.
A comparably small investment gives great results in daily use as production is now running without any unscheduled downtime. Even in the case of false loading, the machine continues production. The few seconds required for measuring have paid off through error-free, reliable manufacturing. Measuring on the machine contributes to considerably enhanced process reliability and economic efficiency in volume production.